Imagine a towering skyscraper piercing the clouds, or a sprawling bridge gracefully arching over a river. These marvels of modern construction wouldn’t be possible without the silent heroes behind the scenes: scaffolds. And the very foundation of these temporary structures? Scaffolding planks, those sturdy platforms that allow workers safe access to all corners of the project. But have you ever wondered how these ubiquitous planks are actually made? Enter the fascinating world of scaffolding plank machines.
Function of Scaffolding Plank Machines
A scaffolding plank machine is a marvel of industrial engineering, designed for the high-volume production of steel or aluminum planks used in scaffolding systems. Think of it as a giant metal origami machine. Here’s a breakdown of its core function:
- Uncoiling: The machine starts with a massive coil of pre-cut metal sheet, typically steel or aluminum. This coil is fed through a series of rollers that uncoil the sheet at a controlled speed.
- Leveling: Any unevenness or curvature in the metal sheet is ironed out by a series of leveling rollers. This ensures a perfectly flat surface for the final plank.
- Feeding and Punching: The leveled sheet is then precisely fed through a series of forming stations. These stations utilize specialized dies that punch out holes, create grooves, or bend the sheet into the desired profile. Imagine cookie cutters, but for metal and on an industrial scale!
- Continuous Roll Forming: As the metal sheet progresses through the forming stations, it’s gradually shaped into the final profile of the scaffolding plank. This process is akin to rolling out dough and shaping it into a specific form.
- Cutting to Length: Once the desired plank profile is achieved, the machine precisely cuts the continuous metal sheet into individual planks of specific lengths. This ensures uniformity and eliminates material wastage.
The entire process is automated and controlled by a computer program, ensuring consistent quality and high production rates.
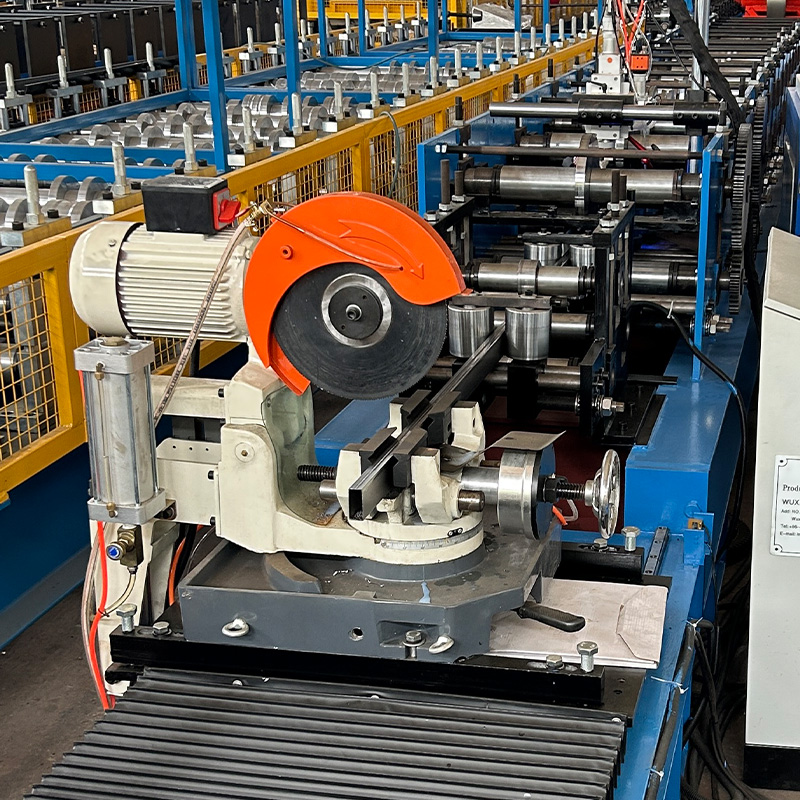
Types of Scaffolding Plank Machines
Scaffolding plank machines come in a variety of configurations to cater to different production needs and plank specifications. Here’s a breakdown of the two main types:
- Single-Line Machines: These are ideal for smaller production runs or for producing planks with simpler profiles. They offer a more cost-effective solution for basic plank requirements.
- Multi-Line Machines: These powerhouse machines boast multiple forming lines, allowing for simultaneous production of different plank profiles or increased production volume of a single profile. They are ideal for large-scale production facilities and offer greater efficiency.
Additional Considerations:
- Material Compatibility: Some machines specialize in processing steel or aluminum, while others offer versatility for both materials.
- Forming Complexity: More intricate plank profiles require machines with a higher number of forming stations for precise shaping.
- Automation Level: The level of automation can vary, with some machines requiring manual intervention for material loading or unloading, while others are fully automated.
Applications of Scaffolding Plank Machines
Scaffolding planks are the workhorses of construction sites, providing safe and stable platforms for workers at various heights. Here’s a glimpse into the diverse applications of scaffolding plank machines:
- Building Construction: From high-rise office buildings to residential structures, scaffolding planks are crucial for providing working platforms for masons, electricians, plumbers, and other construction professionals.
- Bridge Construction: Scaffolding plays a vital role in bridge construction, and scaffolding plank machines ensure a steady supply of planks for these projects.
- Shipbuilding and Repair: Scaffolding planks are used extensively in shipyards to provide access to different sections of the vessel during construction or repairs.
- Industrial Maintenance: Scaffolding is used for accessing and maintaining various industrial equipment and structures, and scaffolding planks are instrumental in these operations.
The versatility and durability of scaffolding planks, made possible by these specialized machines, contribute significantly to the safety and efficiency of countless construction and maintenance projects around the globe.
-
Highway Guardrail End Terminal Forming Machine
-
Highway U/C Post Roll Forming Machine
-
2 Waves Highway Guardrail Roll Forming Machine
-
3 Waves Highway Guardrail Roll Forming Machine
-
দ্রাক্ষাক্ষেত্র পোস্ট রোল ফর্মিং মেশিন
-
স্বয়ংক্রিয় আকার পরিবর্তনযোগ্য সিগমা Purlin রোল ফর্মিং মেশিন
-
স্বয়ংক্রিয় আকার পরিবর্তনযোগ্য CZ Purlin রোল ফর্মিং মেশিন
-
স্বয়ংক্রিয় আকার পরিবর্তনযোগ্য Z Purlin রোল তৈরির মেশিন
-
Auto Size Changeable C U Purlin Roll Forming Machine
Function, Types, and Applications of Scaffolding Plank Machines
Function | Description |
---|---|
Uncoiling | Feeds metal sheet from a coil |
Leveling | Flattens any unevenness in the sheet |
Feeding and Punching | Shapes the sheet with specialized dies |
Continuous Roll Forming | Gradually forms the metal sheet into the final plank profile |
Cutting to Length | Cuts the continuous sheet into individual planks |
Type | Description |
---|---|
Single-Line Machines | Cost-effective for smaller production runs or simpler profiles |
Multi-Line Machines | High-volume production with simultaneous processing of different profiles |
আবেদন | Description |
---|---|
Building Construction | Provides work platforms for various construction tasks |
Bridge Construction | Essential for accessing different sections of bridges during construction or repairs |
Advantages and Disadvantages of Scaffolding Plank Machines
Advantages:
- High Production Efficiency: Scaffolding plank machines churn out planks at a significantly faster rate compared to manual fabrication methods. This translates to quicker project turnaround times and increased productivity.
- Consistent Quality: The automated nature of the machines guarantees consistent plank dimensions, thickness, and overall quality. This ensures uniform load-bearing capacity and eliminates the risk of human error during manual fabrication.
- Reduced Labor Costs: By automating the production process, scaffolding plank machines significantly reduce labor requirements. This translates to cost savings for manufacturers and contributes to a safer work environment by minimizing manual handling of heavy metal sheets.
- Versatility: Modern scaffolding plank machines offer the ability to produce a wide range of plank profiles, catering to diverse construction needs. This flexibility allows manufacturers to cater to a broader customer base and adapt to changing market demands.
- Reduced Material Wastage: The precise feeding and cutting mechanisms of these machines minimize material wastage. This not only reduces production costs but also contributes to a more sustainable manufacturing process.
Disadvantages:
- High Initial Investment: Scaffolding plank machines are complex pieces of machinery, and their initial purchase and installation costs can be substantial. This can be a barrier for smaller manufacturers or those just starting out.
- Maintenance Requirements: Like any complex machinery, scaffolding plank machines require regular maintenance to ensure optimal performance and prevent breakdowns. This necessitates skilled technicians and additional operational costs.
- Limited Flexibility for Customization: While these machines offer a good degree of versatility in terms of plank profiles, they may not be suitable for highly customized or one-off plank designs. For such needs, manual fabrication might still be necessary.
- Skillset Requirements: Operating and maintaining scaffolding plank machines requires a specific skillset. Manufacturers need to invest in training their personnel to ensure safe and efficient operation of the machinery.
- Environmental Impact: The manufacturing process involved in creating scaffolding planks, including the operation of the machines, does have an environmental impact. Manufacturers should strive for eco-friendly practices and explore ways to minimize their carbon footprint.
Choosing the Right Scaffolding Plank Machine
The decision of whether to invest in a scaffolding plank machine depends on several factors, including:
- Production Volume: If your production needs are high and consistent, a scaffolding plank machine can be a worthwhile investment.
- Type of Planks: Consider the specific types of planks you plan to produce and ensure the machine can handle the desired profiles.
- Budget: Weigh the initial investment cost against the long-term benefits of increased production efficiency and reduced labor costs.
- Available Space: These machines can have a significant footprint, so ensure you have adequate space for installation and operation.
By carefully considering these factors, manufacturers can make an informed decision on whether a scaffolding plank machine is the right fit for their needs.
Scaffolding Plank Machine Suppliers and Pricing
The global market for scaffolding plank machines is vast, with numerous manufacturers offering a variety of models. Here’s a glimpse into some of the key players and pricing considerations:
- Major Suppliers: Well-established companies like LOTOS, FORMETAL Technology, and Roll Forming Machinery China are prominent players in the market, offering a range of machine configurations and capabilities.
- Pricing Variations: Pricing for scaffolding plank machines can vary significantly depending on the machine’s capacity, level of automation, and additional features. Expect a range starting from around $50,000 for basic single-line machines to upwards of $500,000 for high-volume, multi-line machines with advanced features.
- Customization Options: Some manufacturers offer customization options for their machines, allowing tailoring the machine to specific production needs. These customizations will naturally affect the final price.
It’s important to obtain quotes from multiple manufacturers and compare specifications before making a purchase decision.
Here’s a table (not mentioning table number) showcasing representative Scaffolding Plank Machine Suppliers and Pricing Ranges (Disclaimer: Prices are indicative and may vary depending on specific configurations and supplier quotes):
Supplier | Price Range (USD) |
---|---|
LOTOS | $50,000 – $300,000 |
FORMETAL Technology | $75,000 – $400,000 |
Roll Forming Machinery China | $40,000 – $250,000 |
Remember, these are just a few examples, and the market offers a wider range of suppliers and pricing options.
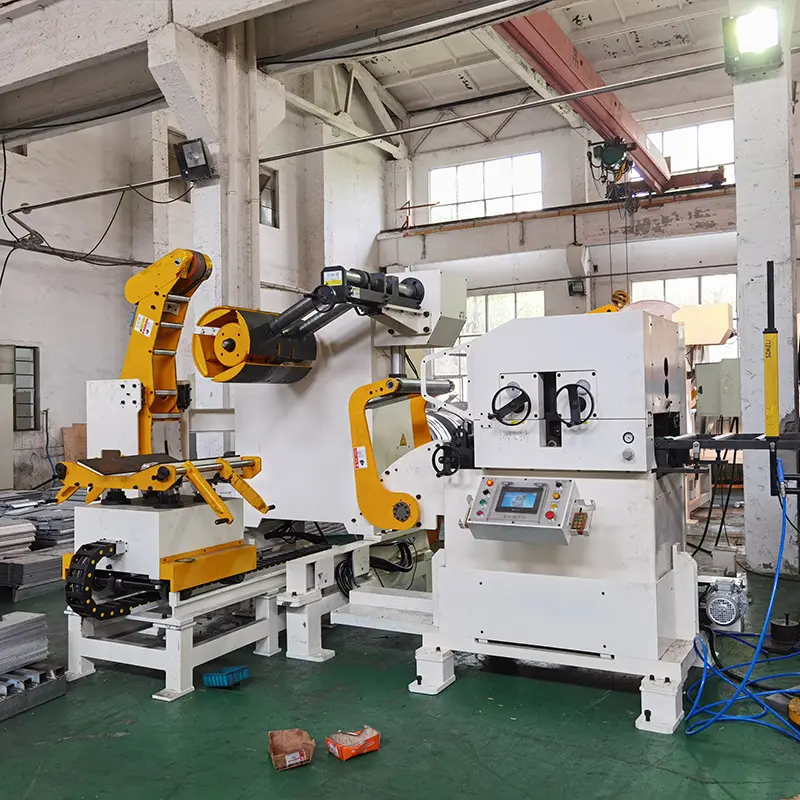
FAQ
Q: What are the safety considerations when operating a scaffolding plank machine?
A: Scaffolding plank machines are powerful pieces of equipment, and safety should be a top priority. Here are some key considerations:
- Always follow the manufacturer’s operating instructions and wear appropriate personal protective equipment (PPE) such as gloves, safety glasses, and ear protection.
- Ensure proper guarding is in place around all moving parts of the machine.
- Regularly inspect the machine for any signs of wear or damage, and address any issues promptly.
- Only trained personnel should operate and maintain the scaffolding plank machine.
Q: How long do scaffolding plank machines typically last?
A: The lifespan of a scaffolding plank machine depends on several factors, including the quality of construction, maintenance practices, and frequency of use. Well-maintained machines from reputable manufacturers can last for decades with proper care.
Q: What are some emerging trends in scaffolding plank machine technology?
A: The scaffolding plank machine industry is constantly evolving, with a focus on:
- Increased Automation: Advancements in automation technology are leading to machines with even higher production rates and reduced reliance on manual intervention.
- Improved Material Efficiency: Innovations in material feeding and cutting mechanisms are minimizing material wastage, promoting sustainability.
- Data Integration and Monitoring: Integrating real-time production data and machine monitoring systems allows for better control, optimization, and preventive maintenance.
- Sustainability: Manufacturers are increasingly focusing on eco-friendly practices, utilizing energy-efficient components and exploring ways to reduce the environmental impact of the manufacturing process.
Q: Are there any alternatives to using scaffolding plank machines?
A: Yes, there are alternative methods for producing scaffolding planks:
- Manual Fabrication: This traditional method involves skilled workers shaping and welding metal sheets into planks. While offering flexibility for customization, it’s time-consuming and labor-intensive, making it unsuitable for high-volume production.
- Light Gauge Steel Framing: This method utilizes pre-fabricated light gauge steel components to assemble planks. It offers faster assembly compared to manual fabrication but may not provide the same level of strength and durability as steel or aluminum planks produced by roll forming machines.
The choice between these methods depends on production volume, budget, and specific project requirements.
উপসংহার
Scaffolding plank machines are the backbone of the scaffolding industry, enabling the mass production of safe and sturdy platforms for construction and maintenance projects. Understanding their function, advantages, disadvantages, and available options empowers manufacturers to make informed decisions and optimize their production processes. As technology continues to evolve, we can expect even more advanced scaffolding plank machines with increased efficiency, sustainability, and integration with Industry 4.0 principles.