Imagine cruising down a highway, the wind whipping through your hair (or helmet, if you’re safety-conscious). Suddenly, a car swerves out of control. Your heart jumps into your throat, but then – a flash of metal. The car collides with a guardrail, the impact absorbed by a series of unassuming blocks. These, my friends, are the unsung heroes of road safety – highway guardrail spacer blocks.
Function of Highway Guardrail Spacer Block Machine
Think of a guardrail as a metal fence separating the road from danger zones. But a rigid fence can be just as dangerous in a collision. Enter the spacer block. These U-shaped or trapezoidal blocks fit between the guardrail post and the rail itself, creating a small gap. During an impact, the spacer block absorbs the force, allowing the guardrail to deform gradually, rather than snapping and becoming a potentially deadly projectile. The machine that manufactures these crucial components is the Highway Guardrail Spacer Block Machine.
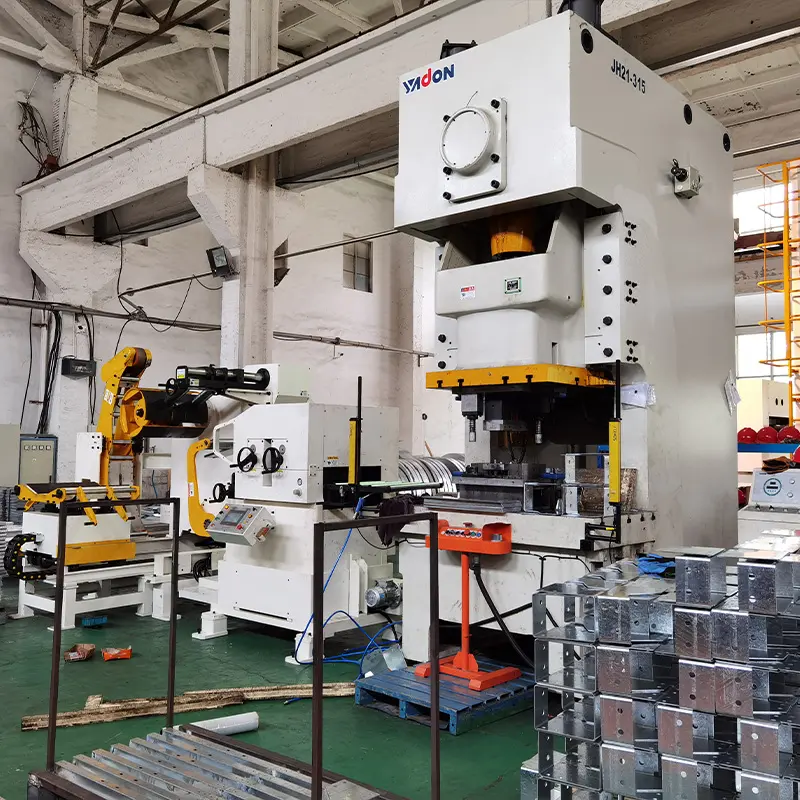
Types of Highway Guardrail Spacer Block Machines
Just like cars come in different makes and models, there’s a variety of Highway Guardrail Spacer Block Machines available. Here’s a breakdown of the two main types:
- Roll Forming Machines: Imagine a giant cookie cutter. This machine feeds coiled steel strip through a series of rollers that progressively bend and shape it into the desired spacer block profile. Think of it like Play-Doh being squeezed through a series of molds. It’s a continuous process, churning out a steady stream of spacer blocks.
- Punching and Bending Machines: This method utilizes pre-cut sheets of steel. A powerful press equipped with a specialized die punches out the basic shape of the block. Secondary bending machines then form the final profile. It’s a more manual approach compared to roll forming, but suitable for smaller production runs or complex spacer block designs.
Applications of Highway Guardrail Spacer Block Machines
The applications of Highway Guardrail Spacer Block Machines are clear – they’re used to manufacture essential components for guardrail systems. These systems find use in a wide range of environments:
- Highways and Expressways: The most common application. Guardrails separate traffic lanes, protect against roadside hazards and prevent vehicles from leaving the roadway.
- Bridges and Overpasses: Guardrails provide additional safety on bridges and overpasses, where a fall could be catastrophic.
- Construction Zones: Guardrails shield workers and equipment from passing traffic during construction projects.
- Parking Lots: Guardrails protect parked vehicles and pedestrians from collisions.
-
Highway Guardrail End Terminal Forming Machine
-
Highway U/C Post Roll Forming Machine
-
2 Waves Highway Guardrail Roll Forming Machine
-
3 Waves Highway Guardrail Roll Forming Machine
-
স্বয়ংক্রিয় আকার পরিবর্তনযোগ্য সিগমা Purlin রোল ফর্মিং মেশিন
-
স্বয়ংক্রিয় আকার পরিবর্তনযোগ্য CZ Purlin রোল ফর্মিং মেশিন
-
স্বয়ংক্রিয় আকার পরিবর্তনযোগ্য Z Purlin রোল তৈরির মেশিন
-
Auto Size Changeable C U Purlin Roll Forming Machine
-
বৈদ্যুতিক মন্ত্রিসভা ফ্রেম রোল গঠনের মেশিন
Advantages of Highway Guardrail Spacer Block Machines
There are several advantages to investing in a Highway Guardrail Spacer Block Machine:
- Increased Safety: By contributing to the effectiveness of guardrail systems, these machines play a vital role in keeping our roads safer.
- Reduced Costs: Manufacturing your own spacer blocks eliminates dependence on external suppliers, potentially leading to cost savings in the long run.
- Production Control: Having your own machine allows for greater control over production schedules and ensures a steady supply of spacer blocks to meet project demands.
- Customization Potential: Some machines can be adapted to produce spacer blocks in different sizes and profiles to meet specific project requirements.
Disadvantages of Highway Guardrail Spacer Block Machines
While beneficial, there are also some drawbacks to consider:
- High Initial Investment: These machines can be expensive, making them a significant upfront cost for smaller companies.
- Technical Expertise Required: Operating and maintaining these machines requires specialized knowledge and training.
- Storage Space Needs: The machines themselves can be quite large, requiring dedicated storage space.
- Production Volume Considerations: If your spacer block needs are minimal, the cost of the machine might not be justified.
Pricing Information
The cost of a Highway Guardrail Spacer Block Machine varies depending on the type (roll forming vs. punching and bending), capacity, features, and brand. Here’s a ballpark range to give you an idea:
- Roll Forming Machines: $50,000 – $200,000+
- Punching and Bending Machines: $20,000 – $100,000+
Choosing the Right Highway Guardrail Spacer Block Machine
So, you’ve decided a Highway Guardrail Spacer Block Machine might be a worthwhile investment. But with various options on the market, choosing the right one can feel like navigating a maze. Here’s a breakdown of some key factors to consider:
- Production Volume: This is crucial. If you only require a small number of spacer blocks for occasional projects, a less expensive punching and bending machine might suffice. However, for high-volume production, a roll forming machine’s efficiency and speed become more attractive. Consider your anticipated production needs over a realistic timeframe (e.g., next 5 years) to make an informed decision.
- Machine Features: Machines come with varying functionalities. Look for features that align with your needs. Do you require the ability to produce multiple spacer block profiles? Is automatic material feeding important? Think about the level of automation you desire and the features that would streamline your production process.
- Material Compatibility: Ensure the machine can handle the desired steel thickness and grade commonly used for spacer blocks. Some machines might offer flexibility to accommodate different material specifications.
- Ease of Operation and Maintenance: Operating a complex machine requires training and expertise. Evaluate the machine’s control system and ensure user-friendly interfaces and readily available training materials. Consider the availability of service technicians and spare parts in your region. Downtime due to maintenance issues can significantly impact your productivity.
- Reputation and Customer Service: Research the reputation of potential suppliers. Look for companies with a proven track record and positive customer reviews. Responsive and reliable customer service is essential for troubleshooting any technical challenges that might arise.
Beyond the Basics: Advanced Considerations
For those seeking an extra edge, here are some advanced considerations:
- Integration with Existing Equipment: Can the machine integrate seamlessly with your existing production line? Consider compatibility factors like material handling systems and control software.
- Automation Potential: Look for machines with features that minimize manual intervention, such as automatic material loading and unloading systems. This can improve efficiency and reduce labor costs.
- Data Acquisition and Monitoring: Some advanced machines offer data acquisition capabilities. This allows you to monitor production parameters, identify potential issues early on, and optimize machine performance.
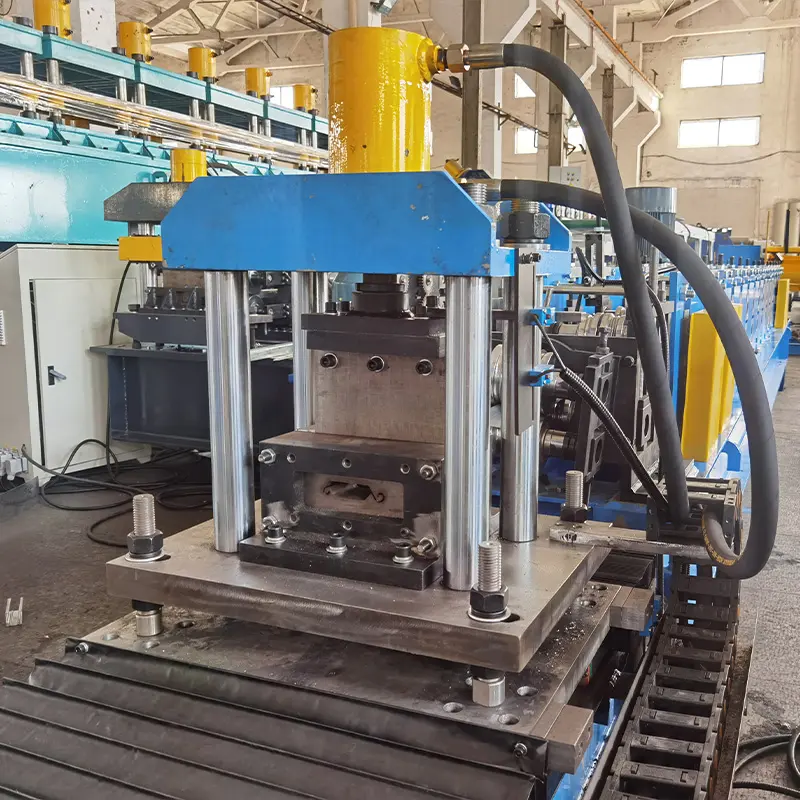
FAQ
Q: What are the typical sizes and profiles of highway guardrail spacer blocks?
A: The size and profile of spacer blocks vary depending on regional standards and guardrail system specifications. Common profiles include U-shaped and trapezoidal blocks. Dimensions typically range from 3-6 inches in width and 2-4 inches in height.
Q: What safety features are important in a Highway Guardrail Spacer Block Machine?
A: Safety should be paramount. Look for machines that comply with relevant safety regulations and include features like emergency stop buttons, proper guarding around moving parts, and lockout/tagout procedures.
Q: How long do Highway Guardrail Spacer Block Machines typically last?
A: With proper maintenance, a well-built Highway Guardrail Spacer Block Machine can last for 15-20 years or even longer. Regular maintenance ensures optimal performance and extends the machine’s lifespan.