দ্য সিগমা পুরলিন রোল তৈরির মেশিন plays a crucial role in the construction industry, shaping metal sheets into Sigma purlins, a vital component for roofs and walls in pre-engineered buildings. Imagine the skeleton of a building – the purlins act as the ribs, providing structural support for the roofing and cladding materials.
This guide delves into the world of Sigma purlin roll forming machines, exploring their components, functionalities, applications, and frequently asked questions.
Components of সিগমা পুরলিন রোল ফর্মিং মেশিন
A Sigma purlin roll forming machine is a marvel of mechanical engineering, orchestating a series of intricate steps to transform flat metal sheets into the desired Sigma purlin profile. Here’s a breakdown of its key components:
- Uncoiler: This motorized unit feeds the metal sheet into the machine, ensuring smooth and consistent feeding.
- Leveler: As the name suggests, the leveler straightens any irregularities in the sheet metal, guaranteeing a uniform profile for the purlin.
- Roll forming stations: The heart of the machine, these stations consist of a series of precisely shaped rollers that progressively bend the metal sheet into the Sigma purlin profile. Each station contributes to a specific stage of the shaping process.
- Punching unit (optional): This unit can be integrated to create holes in the purlin for easy installation and connection with other building components.
- Cutting unit: The cutting unit precisely shears the formed purlin to the desired length.
- Stacker (optional): This automated unit neatly stacks the finished purlins, enhancing production efficiency and reducing manual handling.
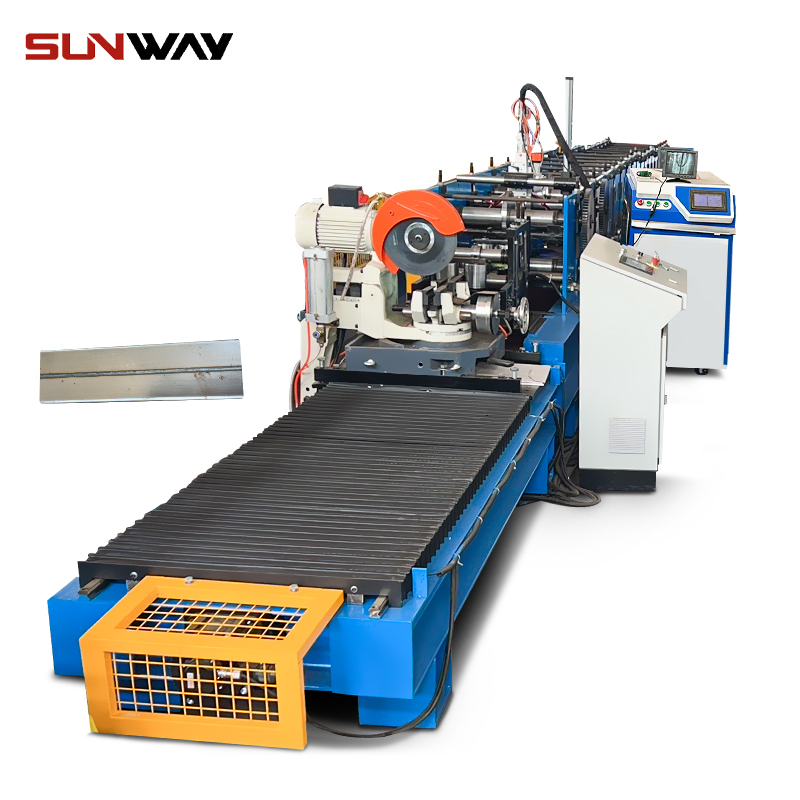
Industrial Applications of সিগমা পুরলিন রোল ফর্মিং মেশিন
The versatility of Sigma purlins translates into a wide range of applications across various industries:
- Construction: The primary application of Sigma purlins lies in pre-engineered buildings, including warehouses, factories, workshops, and agricultural structures. They provide a lightweight yet robust support system for roofs and walls.
- Cladding: Sigma purlins can be used as a substrate for cladding materials like metal sheets, sandwich panels, and composite panels, creating weather-resistant building envelopes.
- Suspended ceilings: In some cases, Sigma purlins can be employed to support suspended ceilings in industrial and commercial settings.
- Solar panel mounting: The structural integrity of Sigma purlins makes them suitable for supporting solar panels on rooftops, contributing to sustainable energy solutions.
Advantages of Using Sigma Purlin Roll Forming Machines
- Cost-effective: Compared to traditional construction methods using wood or steel beams, Sigma purlins offer a cost-efficient alternative due to their lightweight nature and ease of installation.
- Fast and efficient production: Sigma purlin roll forming machines enable rapid and continuous production of purlins, significantly expediting construction timelines.
- Consistent quality: The automated nature of the roll forming process ensures consistent quality and dimensional accuracy in the produced purlins.
- Lightweight: Sigma purlins contribute to the overall lighter weight of the building structure, reducing the load on foundations and potentially lowering construction costs.
- Durable: These purlins are manufactured from high-quality steel, offering excellent resistance to corrosion and harsh weather conditions, ensuring a long lifespan.
- Environmentally friendly: Sigma purlins can be formed from recycled steel, contributing to sustainable construction practices.
-
Highway Guardrail End Terminal Forming Machine
-
Highway U/C Post Roll Forming Machine
-
2 Waves Highway Guardrail Roll Forming Machine
-
3 Waves Highway Guardrail Roll Forming Machine
-
সি সেকশন ব্রেসিং ওমেগা স্টোরেজ র্যাক খাড়া পোস্ট রোল ফর্মিং মেশিন
-
স্টিল বক্স প্লেট মেকিং রোল ফর্মিং মেশিন
-
বক্স মরীচি স্টীল রোল শেল্ফ কলাম জন্য মেশিন গঠন
-
প্যালেট র্যাকিং স্টেপ বিম পি বিম রোল তৈরির মেশিন
-
গুদাম শেল্ফ খাড়া রোল গঠন মেশিন
Considerations When Choosing a সিগমা পুরলিন রোল ফর্মিং মেশিন
Investing in a Sigma purlin roll forming machine requires careful consideration of various factors:
- Production capacity: Evaluate your anticipated production volume and choose a machine with sufficient capacity to meet your needs.
- Purlin profile and size: Ensure the machine can produce the specific Sigma purlin profile and size required for your projects.
- Material thickness: The machine’s capabilities should accommodate the desired thickness of the metal sheet you plan to use.
- Automation level: Consider the level of automation you require, ranging from manual size changes to fully automated operations.
- Brand reputation and warranty: Opt for reputable brands offering reliable machines backed by comprehensive warranties.
choosing a Sigma purlin roll forming machine:
Selecting the ideal Sigma purlin roll forming machine goes beyond simply comparing features and specifications. Two often-overlooked factors play a crucial role in your long-term success: after-sales service and maintenance requirements. Let’s delve deeper into each of these aspects:
After-Sales Service: Your Safety Net
Imagine your machine encountering a technical hiccup. A reliable after-sales support system acts as your safety net, ensuring minimal downtime and a swift resolution to any challenges you may face. Here’s what to consider:
- Availability and responsiveness: Choose a manufacturer with readily available support channels, offering prompt assistance in case of issues.
- Technical expertise: Ensure the support team possesses the necessary knowledge and experience to address your specific machine and its complexities.
- Spare parts accessibility: Verify the manufacturer’s capacity to provide readily available spare parts to minimize downtime during repairs.
Maintenance Requirements: Understanding the Long-Term Commitment
Every machine, including a Sigma purlin roll forming machine, demands regular maintenance. Understanding these requirements upfront is crucial for several reasons:
- Cost considerations: Factor in the cost of maintenance, including parts, labor, and potential downtime, when comparing different machine options.
- Resource allocation: Assess your team’s capabilities and resources to ensure they can handle the required maintenance procedures effectively.
- Production efficiency: Regular maintenance directly impacts your production efficiency. Opting for a machine with simpler or less frequent maintenance needs can minimize disruptions to your workflow.
additional points
- User-friendliness: A user-friendly machine with intuitive controls can minimize training time and improve operator efficiency.
- Energy efficiency: Look for machines that incorporate energy-saving features to reduce operational costs and environmental impact.
- Scalability: If you anticipate future growth in your business, consider a machine that can be easily upgraded to accommodate increased production needs.
Table: Key features and considerations for Sigma purlin roll forming machines
Feature | Consideration |
---|---|
Production capacity | Choose a machine that meets your anticipated production volume. |
Purlin profile and size | Ensure the machine can produce the desired profile and size. |
Material thickness | Select a machine compatible with the desired metal sheet thickness. |
Automation level | Choose the level of automation that aligns with your needs and budget. |
Brand reputation and warranty | Opt for reputable brands with reliable machines and comprehensive warranties. |
After-sales service | Ensure access to reliable after-sales support for technical assistance. |
Maintenance requirements | Understand the complexity and frequency of maintenance procedures. |
User-friendliness | Choose a machine with intuitive controls for ease of operation. |
Energy efficiency | Look for machines with features that minimize energy consumption. |
Scalability | Consider future growth and choose a machine with upgrade potential. |
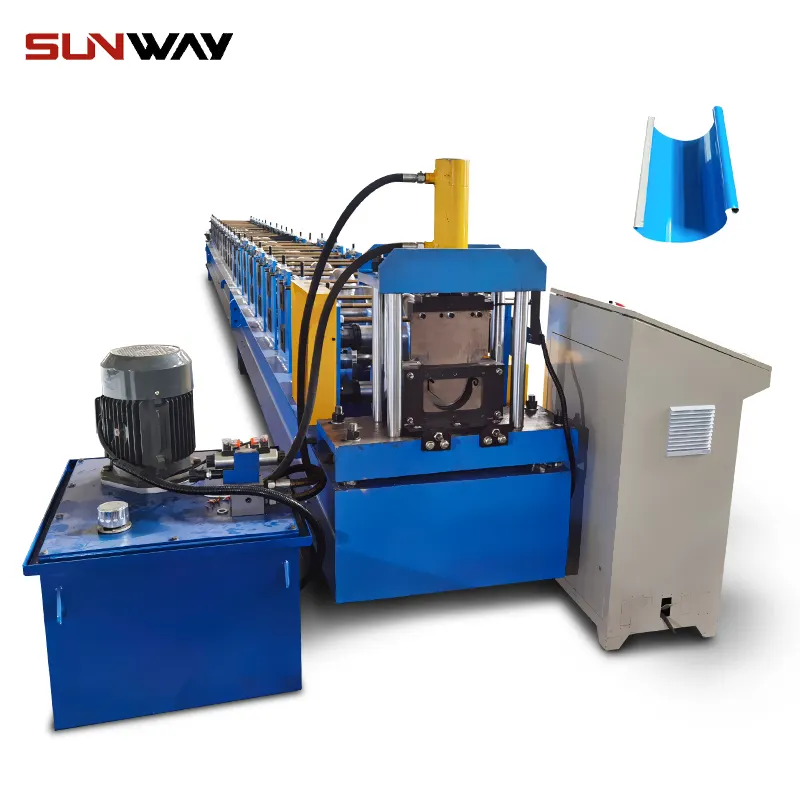
উপসংহার
Sigma purlin roll forming machines are a valuable asset for companies involved in pre-engineered building construction, cladding, and other applications requiring lightweight and robust support structures. By understanding the different components, functionalities, and considerations involved in choosing the right machine, you can make an informed decision that empowers your business to operate efficiently and productively.
FAQ
Q: What are the typical production speeds of Sigma purlin roll forming machines?
A: Production speeds can vary depending on the machine’s model, complexity of the purlin profile, and material thickness. Speeds typically range from 10 to 30 meters per minute.
Q: What are the safety considerations when operating a Sigma purlin roll forming machine?
A: Always follow the manufacturer’s safety instructions and wear appropriate personal protective equipment, including gloves, safety glasses, and ear protection.
Q: How much does a Sigma purlin roll forming machine cost?
A: The cost of a Sigma purlin roll forming machine can vary significantly depending on its features, capabilities, and brand. Prices can range from USD 20,000.