The construction industry thrives on innovation, constantly seeking materials and methods that offer superior strength, affordability, and ease of use. In this realm, barrel corrugated making machines stand tall as a testament to such ingenuity. These specialized machines take on the crucial task of transforming metal sheets into corrugated profiles, commonly known as barrel tiles or sheets, widely used in roofing and wall cladding applications.
Understanding Barrel Corrugated Sheets
Before delving into the world of barrel corrugated making machines, let’s establish a clear understanding of their output: barrel corrugated sheets. Imagine a flat sheet of metal, like steel or aluminum, transformed into a series of wavy ridges and valleys. These ridges, resembling the curved staves of a barrel (hence the name), enhance the sheet’s structural integrity and load-bearing capacity without adding significant weight. This unique profile makes barrel corrugated sheets a popular choice for:
- Roofs: They offer excellent weather resistance, durability, and lightweight construction, making them ideal for both residential and commercial buildings.
- Walls: Their aesthetic appeal and ease of installation contribute to their widespread use in industrial warehouses, agricultural buildings, and even temporary structures.
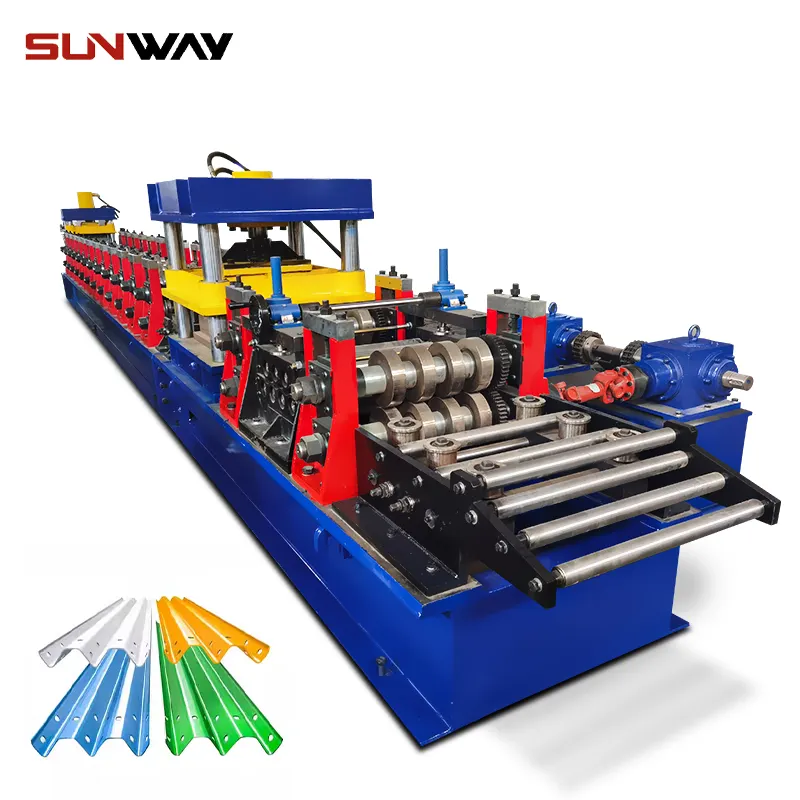
Unveiling the Barrel Corrugated Making Machine
Now that we appreciate the value of barrel corrugated sheets, let’s explore the machine that breathes life into them: the barrel corrugated making machine. Essentially, this machine functions as a metal forming marvel. Imagine feeding a flat sheet of metal into one end, and out pops a precisely shaped, corrugated sheet at the other end. But this seemingly simple process involves a fascinating interplay of mechanical components:
- Uncoiler: This is the starting point, where the metal coil is unwound and fed into the machine.
- Feeder: This unit precisely guides the sheet metal through the forming process.
- Forming Rolls: These are the heart of the machine, featuring a series of precisely designed rollers that progressively shape the metal sheet into the desired corrugated profile. The number and configuration of these rolls determine the specific profile of the final product.
- Cutter: Once formed, the sheet is cut to the desired length using a shearing mechanism.
- Stacker: The finished corrugated sheets are then automatically stacked for easy handling and storage.
Additional components like a hydraulic system power the machine’s operation, while control panels allow for precise adjustments to the forming process and production parameters.
Sizing Up the Options: Barrel Corrugated Making Machine Variations
The world of barrel corrugated making machines isn’t a one-size-fits-all scenario. Manufacturers offer a variety of options to cater to diverse production needs and budgets. Here’s a breakdown of some key factors to consider when choosing a machine:
- Sheet thickness: Different machines are designed to handle various metal sheet thicknesses, impacting the final product’s strength and suitability for specific applications.
- Sheet width: The machine’s capacity to accommodate different sheet widths affects the production output and the size of the final corrugated sheets.
- Corrugated profile: Manufacturers offer machines capable of producing various barrel corrugated profiles, each with distinct dimensions and structural properties.
- Production speed: The machine’s speed determines its production output per hour, directly impacting your manufacturing capacity.
- Level of automation: Some machines offer a high degree of automation, minimizing manual intervention, while others require more operator involvement.
Cost naturally plays a crucial role in the selection process, with more sophisticated and versatile machines typically commanding a higher price tag. Carefully evaluating your specific production needs and budget will guide you towards the most suitable option.
-
Highway Guardrail End Terminal Forming Machine
-
Highway U/C Post Roll Forming Machine
-
2 Waves Highway Guardrail Roll Forming Machine
-
3 Waves Highway Guardrail Roll Forming Machine
-
দ্রাক্ষাক্ষেত্র পোস্ট রোল ফর্মিং মেশিন
-
স্বয়ংক্রিয় আকার পরিবর্তনযোগ্য সিগমা Purlin রোল ফর্মিং মেশিন
-
সি সেকশন ব্রেসিং ওমেগা স্টোরেজ র্যাক খাড়া পোস্ট রোল ফর্মিং মেশিন
-
স্টিল বক্স প্লেট মেকিং রোল ফর্মিং মেশিন
-
বক্স মরীচি স্টীল রোল শেল্ফ কলাম জন্য মেশিন গঠন
Operating a Barrel Corrugated Making Machine: A Glimpse into the Process
While the specifics may vary depending on the chosen machine model, here’s a general overview of the barrel corrugated making process:
- Machine Setup: The operator prepares the machine by loading the desired metal coil onto the uncoiler, selecting the appropriate forming rolls for the desired profile, and setting the required production parameters on the control panel.
- Feeding the Metal Sheet: The metal sheet is fed from the uncoiler into the feeder, ensuring proper alignment and tension.
- Forming the Corrugated Profile: The sheet passes through the forming rolls, each progressively shaping it into the final corrugated profile. The precise design of these rolls and the applied pressure determine the final shape and dimensions of the corrugations.
- Cutting to Length: Once formed, the sheet is precisely cut to the desired length using the shearing mechanism.
- Stacking the Finished Product: The finished corrugated sheets are automatically stacked for easy handling and storage.
Safety precautions are paramount throughout the operation, including wearing proper personal protective equipment and following the manufacturer’s recommended operating procedures.
Advantages and Considerations: Weighing the Pros and Cons
Barrel corrugated making machines offer a multitude of advantages for manufacturers, but it’s essential to consider the associated aspects before making an investment.
Advantages:
- Increased Efficiency: Compared to manual forming methods, these machines offer significantly higher production rates, leading to increased output and reduced labor costs.
- Enhanced Consistency: The precise control offered by the machinery ensures consistent and uniform corrugation profiles across every sheet, leading to a higher quality finished product.
- Reduced Waste: The automated nature of the process minimizes material waste compared to manual methods, contributing to cost savings and environmental sustainability.
- Versatility: Many machines offer the ability to produce various corrugated profiles simply by changing the forming rolls, allowing manufacturers to cater to diverse project requirements.
- Durability: These machines are built to withstand the demands of continuous production, offering long-term reliability and a favorable return on investment.
Considerations:
- Initial Investment: The initial cost of purchasing a barrel corrugated making machine can be significant, requiring careful planning and financial considerations.
- Operational Costs: Factors like power consumption, machine maintenance, and tooling costs need to be factored into the overall operational expenses.
- Technical Expertise: Operating and maintaining these machines often requires specific technical knowledge and training for the workforce.
- Space Requirements: The machine’s footprint and additional space needed for material handling and storage should be considered when planning the production setup.
- Environmental Impact: While the machines themselves may not directly generate pollutants, the environmental impact of the chosen metal material and its production process should be factored in.
By carefully weighing the advantages and considerations, manufacturers can make an informed decision about whether a barrel corrugated making machine aligns with their specific needs and production goals.
Applications: Where Do You See Them?
Barrel corrugated sheets, birthed from the prowess of barrel corrugated making machines, find application in a diverse range of projects:
- Roofing: Their durability, weather resistance, and lightweight construction make them ideal for residential and commercial roofing applications. They are particularly well-suited for regions prone to harsh weather conditions like heavy rain, snow, and strong winds.
- Wall Cladding: দ্য aesthetic appeal and ease of installation of barrel corrugated sheets make them a popular choice for industrial buildings, warehouses, agricultural structures, and even temporary buildings.
- Fences and Gates: Their strength and versatility allow them to be used in fencing and gate applications for various purposes, including perimeter security and animal enclosures.
- Ceilings: Barrel corrugated sheets can be used for interior applications like ceilings, particularly in industrial settings, offering a distinctive aesthetic and contributing to sound absorption.
The potential uses extend beyond these common examples, with creative architects and builders finding innovative applications for barrel corrugated sheets in various projects, pushing the boundaries of their functionality.
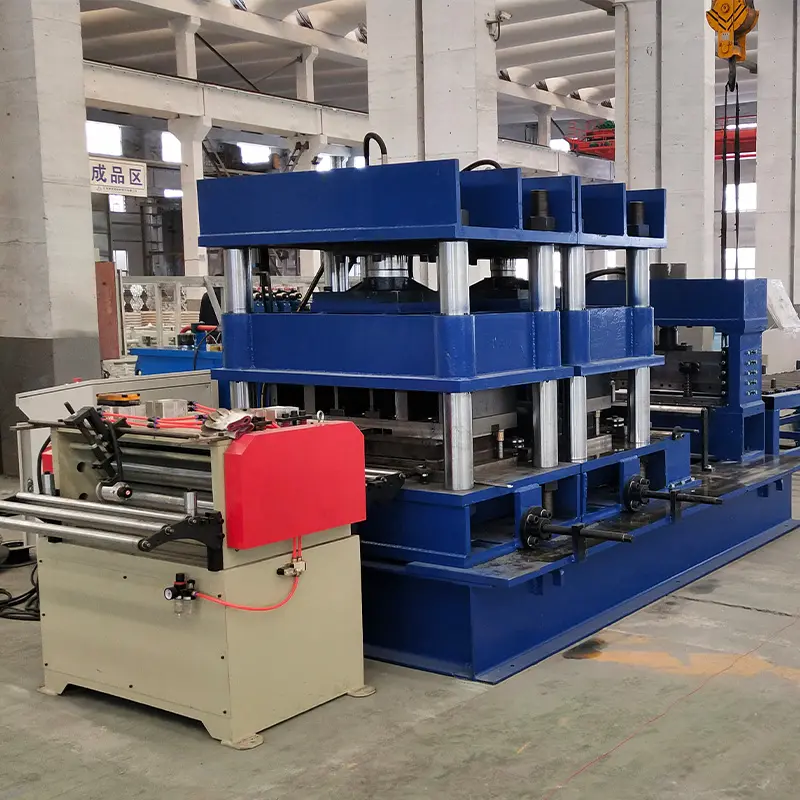
FAQ
What are the typical production speeds of barrel corrugated making machines?
Production speeds can vary depending on the specific machine model, sheet thickness, and desired profile. However, they typically range from 3 to 10 meters per minute.
How do I maintain a barrel corrugated making machine?
Regular maintenance is crucial to ensure the machine’s optimal performance and longevity. This includes adhering to the manufacturer’s recommended maintenance schedule, lubricating moving parts, and inspecting for wear and tear. Consulting the machine’s manual and seeking professional assistance when necessary is essential.
Can barrel corrugated sheets be recycled?
Yes, barrel corrugated sheets made from recyclable metals like steel or aluminum can be recycled at the end of their lifespan. This contributes to environmental sustainability and reduces the need for virgin materials.
What safety precautions should be taken when operating a barrel corrugated making machine?
Always follow the manufacturer’s safety guidelines and wear appropriate personal protective equipment (PPE), such as safety glasses, gloves, and hearing protection. Be aware of moving parts and maintain a safe distance during operation.
Where can I find reputable manufacturers of barrel corrugated making machines?
Conducting online research and attending industry trade shows are effective ways to identify reputable manufacturers. It’s crucial to compare specifications, features, and after-sales support before making a purchase decision.