CZ purlin forming machines are roll forming equipment used to produce C and Z shaped purlins from metal coils. Purlins are structural beams widely used in metal buildings and structures.
What is a CZ Purlin?
A CZ Purlin is a type of structural component used in construction and building applications, particularly in the framing of roofs and walls. Purlins are horizontal beams or members that provide support to the roof covering or wall cladding and help distribute the load of the building’s roof or walls to the main structural frame, such as columns or rafters. They are commonly used in metal building construction.
The term “CZ Purlin” typically refers to two different shapes of purlins:
- C Purlin: A C-shaped purlin is formed like the letter “C” in cross-section, with two horizontal flanges and a vertical web connecting them. C purlins are commonly used for roof framing and wall girts.
- Z Purlin: A Z-shaped purlin is formed like the letter “Z” in cross-section, with a pair of vertical flanges connected by a horizontal web. Z purlins are typically used as roof purlins, and their shape provides added strength and stability compared to C purlins.
CZ Purlins are made from various materials, including steel and aluminum, and they come in different sizes and thicknesses to suit the specific load-bearing requirements of a building’s design. They are essential components in the construction of steel-framed and metal-clad buildings, providing structural support for the roof and walls while also helping to maintain the overall stability and integrity of the structure.
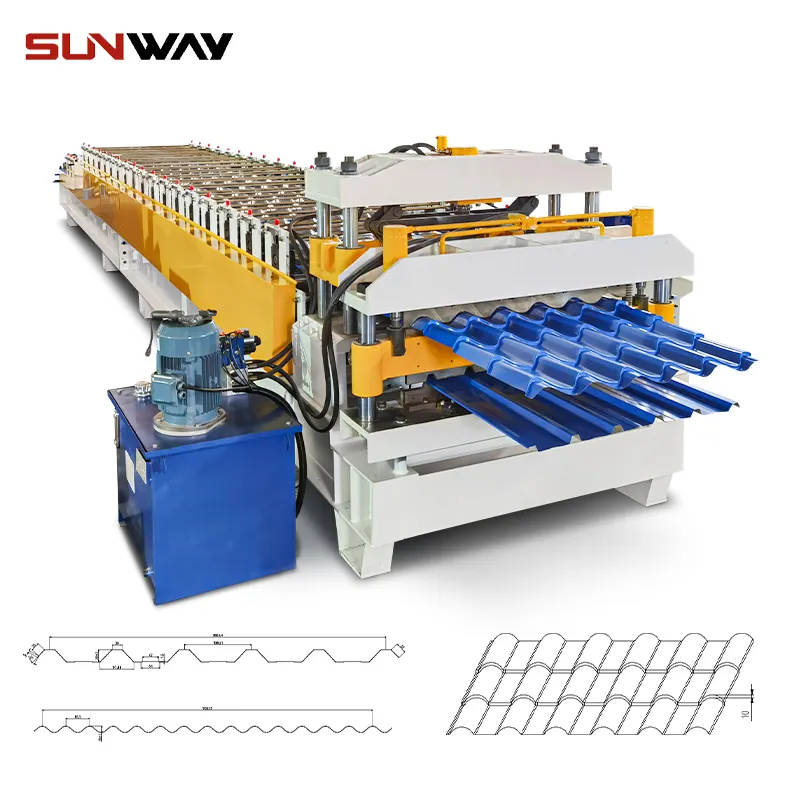
Key Details of CZ Purlin Forming Machines
Key Details | Description |
---|---|
Machine Type | CZ Purlin Forming Machine |
Function | To produce C and Z-shaped purlins from flat metal coils |
Materials Processed | Steel, Aluminum, or other metal materials |
Forming Process | Roll forming or cold roll forming |
Components | Typically includes decoiler, leveling device, punching unit, roll forming unit, cutting unit, and control system |
Profile Shapes | Produces both C-shaped and Z-shaped purlins |
কয়েল প্রস্থ | Adjustable, depending on the machine’s design and capacity |
Thickness Range | Varies based on machine specifications, typically ranging from 1mm to 3mm or more |
Speed of Production | Varies widely depending on the machine model, ranging from 10 to 30 meters per minute or more |
Cutting Method | Hydraulic or mechanical cutting systems |
Roll Forming Stations | Multiple sets of roll forming stations for shaping purlins |
নিয়ন্ত্রণ ব্যবস্থা | PLC (Programmable Logic Controller) for automated operation and precision |
Size and Dimensions | Various machine sizes available, depending on production requirements |
Power Source | Electric, typically three-phase power supply |
Safety Features | Emergency stop buttons, safety guards, and sensors for worker safety |
Usage | Used in manufacturing and construction industries for producing purlins used in building structures |
Customization Options | Machines can be customized based on specific requirements |
Maintenance | Regular maintenance and lubrication required for optimal performance |
Manufacturer Support and Warranty | Usually provided by the machine manufacturer |
Working Principle
- Uncoiler feeds metal strip into machine
- Forming stations progressively shape strip into C or Z profile
- Cutting tool slices beams to required length
- Output table stacks finished purlins
Main Components
- Uncoiling unit
- Straightening rolls
- Accumulator
- Forming stations with top/bottom blades
- Hydraulic system
- Cutting tool
- Control panel
Types of CZ Purlin Forming Machines
Machine Type | Description |
---|---|
Manual CZ Machine | Basic model with manual adjustment for size changes |
Automatic CZ Machine | Fully automatic adjustment of forming parameters |
Double Layer CZ Machine | Produces two purlins simultaneously |
Customized CZ Machine | Customized to produce special purlin designs |
Working Process of CZ Purlin Forming
The working process involves uncoiling the metal coil, feeding it through progressive forming stations to shape the C or Z profile, and cutting the beams to length:
- দ্য uncoiling unit feeds the metal strip into the machine through guiding rolls
- Accumulator controls loop of material for stable feeding
- The metal strip passes through forming stations with upper and lower forming rollers
- Forming rollers have customized blades to bend the strip into C or Z shape through stages
- Hydraulic system adjusts the space between rollers
- The profiled purlin beam passes through the cutting station
- Cutting blades slice the beam at preset length into individual purlins
- Formed purlins are stacked on the output table
-
রোলিং শাটার স্ল্যাট রোল ফর্মিং মেশিন
-
Highway Guardrail End Terminal Forming Machine
-
Highway U/C Post Roll Forming Machine
-
2 Waves Highway Guardrail Roll Forming Machine
-
3 Waves Highway Guardrail Roll Forming Machine
-
বৈদ্যুতিক মন্ত্রিসভা ফ্রেম রোল গঠনের মেশিন
-
দিন রেল রোল ফর্মিং মেশিন
-
দুই তরঙ্গ হাইওয়ে গার্ডেল মেশিন
-
থ্রি ওয়েভ হাইওয়ে গার্ডেল মেশিন
Main Aspects of CZ Purlin Forming
Material Feeding
- Coiled steel or aluminum strip of thickness 0.7-3 mm
- Max coil weight 5 tons
- Uncoiler with mandrel for smooth unroll of coil
- Accumulator controls feed loop for continuous production
Profile Forming
- Up to 8 progressive forming stations
- Stations have customized top and bottom blades
- Hydraulic cylinders adjust clearances between rollers
- Blades customized for specific purlin dimensions
- Quick tooling changeovers for profile changes
Cutting & Slicing
- Top and bottom cutting blades shear purlins at preset length
- Servo motor synchronizes blade action
- Length between 3-13 meters continuously
- Individual purlin lengths of 0.3-9 meters
Customization Capabilities
- Flexible adjustment of all forming parameters
- Custom purlin sizes without blade replacement
- Special hole punching or embossing if needed
- Double layer machines produce two beams together
Technical Specifications
মডেল | Production Speed (m/min) | Finished sizes (mm) | Material Thickness (mm) | Power (kW) |
---|---|---|---|---|
Manual 1000 | 8-10 | 100-300×50-120 | ≤3 | 11 |
Auto 2000 | 15-18 | 100-300×50-150 | 0.7-2 | 37 |
Double Layer 3000 | 8-12 | 150-250×80-100 | ≤2 | 45 |
Suppliers and Price Range of CZ Purlin Forming Machines
Supplier | Location | Price Range |
---|---|---|
Factory A | China | $10,000 – $100,000 |
Factory B | ভারত | $15,000 – $120,000 |
Brand C | Europe | $80,000 – $250,000 |
- Prices vary by production speed, purlin sizes, customization, and automation level
- Chinese machines offer cost advantage
- European brands provide high precision and durability
- Expect bulk order discounts up to 20%
- Additional cost for parameters like hole punching, embossing
Installation, Operation and Maintenance
Stage | বিস্তারিত |
---|---|
Installation | – Civil and electric work needed – Trained technicians required for setup |
Operation | – 1-2 operators per shift – Parameter settings through control panel – Easy switchover between sizes |
Maintenance | – Daily oiling and cleaning – Inspect blade condition weekly – Replace blades annually or as needed – Check hydraulics and electrics biannually |
- Installation takes 1-2 weeks
- Comprehensive operator manual provided
- Online service support available
- Consumables include forming blades, oils, electrics
How to Select a CZ Purlin Forming Machine
Here are key considerations for selecting a CZ purlin forming machine:
Application Requirements
- Type and dimensions of purlins needed
- Production volume per shift/month
- Level of flexibility for future purlin changes
Machine Capabilities
- Size range of machine – min/max purlin depths
- Material thickness handling capacity
- Production speed to match volumes
- Automation vs manual adjustment
Supplier Credentials
- Experience in the industry
- Clientele and reviews
- Responsiveness to inquiries
- Warranties and service support
Budget Constraints
- Available investment capital
- Desired ROI timeline
- Expected operating costs
Understanding application needs is essential before comparing machine specs and supplier proposals.
Pros and Cons of CZ Purlin Forming Machines
Pros | Cons |
---|---|
– High production capacity – Flexible size changes – Low operating costs | – High initial investment – Regular blade maintenance – Limited customization |
Advantages
- Single equipment produces entire range of purlin sizes
- Manual to fully automated options
- Reliable performance for small or large plants
- Low per piece production costs
Limitations
- Regular forming blade replacement
- Limited flexibility for profile changes
- Cannot match custom roll former output
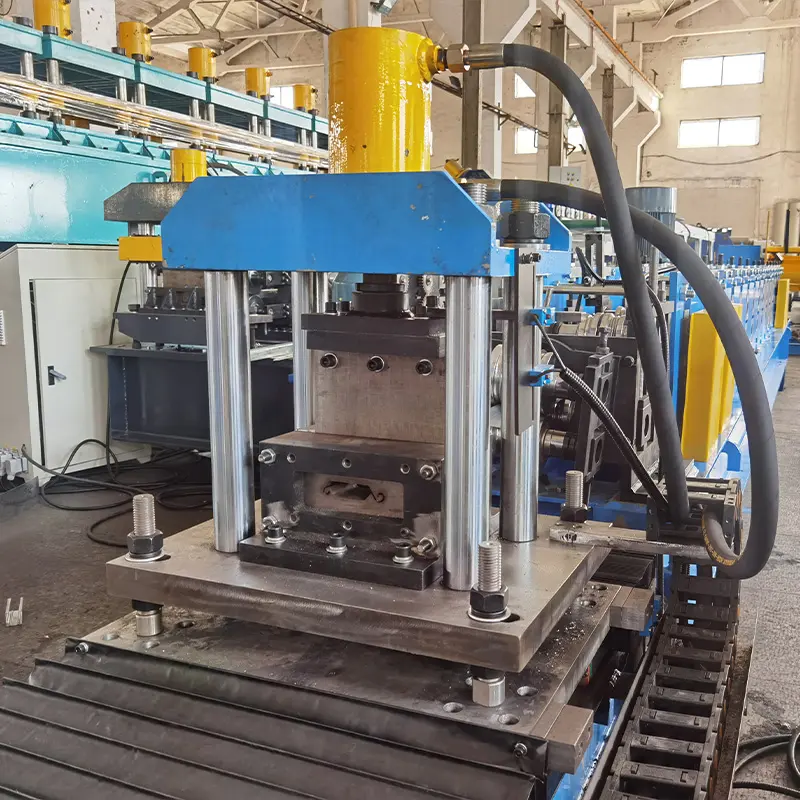
FAQ
Q: What thickness of coils can be handled?
A: Standard input material thickness is 0.7mm to 3mm. Some models support up to 4mm thickness.
Q: How often do the blades need replacement?
A: On average, forming blades require replacement after producing 15,000-25,000 tons depending on the material.
Q: What level of training is required to operate the machine?
A: Basic training takes 1-2 days. Manufacturers provide detailed operating manuals for reference.
Q: Can I get customized purlin designs?
A: Customization is limited to available profiles. For specialized designs, custom roll formers would be preferable.
Q: What safety measures are incorporated?
A: Standard safety features include emergency stop buttons, safety guards near moving parts, and covered electricals.
Q: What is the typical warranty period?
A: Warranty is generally 12 months from the installation date, covering manufacturing defects in materials and workmanship.