ক light keel roll forming machine is an innovative technology used for bending metal sheets and plates into unique keel frame shapes. This advanced forming equipment enables efficient, high-quality, and cost-effective production of lightweight keel structural parts with improved strength for the shipbuilding and construction industries.
Overview of Light Keel Roll Forming Machine
Light keel roll forming is an automated continuous process for progressive bending of metal coils into customized open channel beams and frames with keel-like cross-sections. It utilizes a series of consecutive pairs of counter-rotating rolls to incrementally form the sheet metal into the desired structural shape as it passes through the machine.
Benefits: Higher productivity, reduced labor, superior and consistent quality parts, lower cost, flexible and customizable forming, energy efficiency
Applications: Ship hulls and decks, storage racks, automotive frames, rail car and crane structures, building roof supports
Materials: Carbon steel, stainless steel, aluminum alloys
Product Types: C-, U-, Z-, L-section keels up to 8 m length
Thickness Capacity: 0.5 – 3 mm
Suppliers: Faccin, Peddinghaus, EPIC, Benko Products, Gasparini
In the following sections, we will explore in detail the working principle, main components, processes, selection factors, advantages, limitations, and applications of light keel roll forming lines.
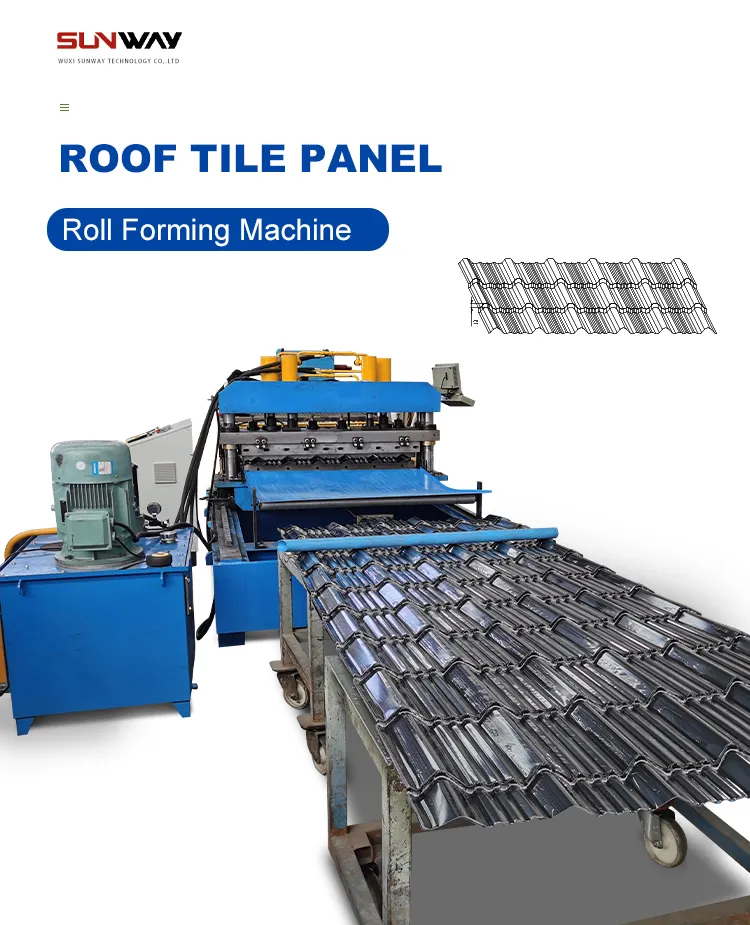
Types of Light Keel Roll Forming Equipment
There are two major categories of keel roll forming systems:
Table 1. Types of keel roll formers
Type | Description |
---|---|
Fixed Keel Rolling Mills | Consist of forming stands arranged in a fixed linear layout for rolling fixed keel frame shapes continuously |
Flexible Roll Forming Lines | Utilize modular forming units that can be rearranged into customized layouts for producing adjustable variable keel geometries |
Fixed Keel Roll Formers
Designed for dedicated high-volume production of standard keel sections. Lower cost, simpler design, easier operation. Limited flexibility in profile shapes.
Flexible Roll Forming Systems
Enable quick changeovers between multiple keel shapes. PLC-controlled. More expensive initial cost but higher adaptability.
Working Principle of Light Keel Roll Former
The working concept of light keel roll formers involves continuous and incremental bending of strip metal stock into a keel-shaped open channel structural beam utilizing a series of roll stations, as illustrated step-by-step below:
Figure 1. Light keel roll forming process
- Sheet coil is loaded at the de-coiler unit
- The strip gets fed through the leveler for flattening
- Forming rolls progressively cold-work the metal into the designated keel shape
- Final keel frame gets extracted and cut at desired length
- Formed keels are offloaded for further fabrication/assembly
During this rolling process, the pre-treated metal strip undergoes consecutive bending and shaping between specialized pairs of gear-driven rolls that operate in opposing directions. As the material passes each stand, incremental deformations are induced leading to the cumulative formation of the keel profile.
Correct design of the roll pass sequences and precise control of rolling parameters like metal feed rate, roll rpm, inter-stand tensions, and lateral positioning are critical to achieving high-quality keels. The latest computerized keel roll mills enable precision forming, reduce defects, and improve performance compared to manual equipment.
Main Components of Light Keel Rolling Lines
Table 2. Components of keel roll formers
Unit | Function |
---|---|
Sheet Coil Payoff | Feed metal coil strip |
Feed Table | Support and guide metal strip |
De-coiler | Unwind sheet coil with controlled tension |
Entry Guide | Align strip entering first rolls |
Sheet Leveler | Eliminate coil curvature for flatness |
Forming Stands | House upper/lower forming rolls to shape metal |
Forming Rolls | Progressively cold-work the strip into keel shape |
Roll Gear Boxes | Provide shaping rolls with rotation torque |
Keel Extractor | Extract formed keel at output |
Cut-Off Shear | Cut keels at specified lengths |
Runout Conveyors | Transport cut keels for unload |
Electrical Cabinet | Controls, PLC units, instruments |
Key Forming Section Equipment
দ্য forming stands with specialized keel forming rolls are the most important parts responsible for bending the strip stock into the desired keel structural shape.
- Typically 4-8 adjustable roll stations for incremental keel forming
- Roll heights, angles, positions optimized for target shape
- Hardened tool steel rolls with quality bearings/gearing
Roll separating pneumatic cylinders precisely set the gaps between upper and lower rolls. Advanced systems have automatic roll gap control for setting profiling space.
Roll Geometry Design Software enables simulation modeling and virtual prototyping of the keel rolling process to optimize equipment parameters.
PLC Control Units enable automatic control of speeds, tool adjustments and interlocks for quality, precision, and safety.
Instrumentation like encoders, sensors and servo motors provide roll position and speed feedback for monitoring and control during keel rolling.
-
Highway Guardrail End Terminal Forming Machine
-
Highway U/C Post Roll Forming Machine
-
2 Waves Highway Guardrail Roll Forming Machine
-
3 Waves Highway Guardrail Roll Forming Machine
-
দ্রাক্ষাক্ষেত্র পোস্ট রোল ফর্মিং মেশিন
-
স্বয়ংক্রিয় আকার পরিবর্তনযোগ্য সিগমা Purlin রোল ফর্মিং মেশিন
-
স্বয়ংক্রিয় আকার পরিবর্তনযোগ্য CZ Purlin রোল ফর্মিং মেশিন
-
স্বয়ংক্রিয় আকার পরিবর্তনযোগ্য Z Purlin রোল তৈরির মেশিন
-
Auto Size Changeable C U Purlin Roll Forming Machine
Working Process of Light Keel Roll Forming
The light keel roll forming process involves six main steps to convert raw metal coils into finished keel-framed products:
Figure 2. Light keel roll forming stages
1. Material Loading
- Carbon steel, stainless steel or aluminum coils loaded onto payoff reel
- Coil strip tail threaded through equipment
2. Strip Feeding
- Strip pulled through de-coiler and straightening machine
- Leveled strip enters forming section
3. Profile Forming
- Metal sheet undergoes staged cold rolling
- Progressively formed into C/Z-shaped keel geometry
4. Keel Extraction
- Formed keel beam extracted at output end
- Extractor guides to cutoff area
5. Cutting Operation
- Shears slice keel at specified lengths
- As per order requirements
6. Unloading
- Formed and cut keels conveyed for unloading
- Transported for further processing
During the cycle, an automated speed control system sets the optimum strip feed rate based on metal properties, thickness, equipment capacity and keel parameters to achieve quality profiling.
In-line quality inspection stations may also be integrated for checking formed keels. Once extracted and cut, the finished parts are offloaded via exit conveyors for subsequent fabrication or dispatch.
Material and Sheet Feeding in Light Keel Rolling
Table 3. Keel roll forming materials
Materials | বৈশিষ্ট্য | Performance |
---|---|---|
Carbon Steel | Low cost, high strength | Most common, easiest to form |
Stainless Steel | Corrosion resistance | Difficult shapeability |
Aluminum Alloys | Lightweight | Challenging feedability |
Sheet Thickness Range – 0.5 mm to 3 mm
Sheet Width – Up to 1250 mm
Coil Weight – Max 10 tons
To improve material handling and feedability:
- De-coiler and unrollers must have adjustable tensions
- Strip accumulation tables for faster line speeds
- Additional feed rollers/straighteners as per metal grade
- Inter-stand equipment for controlling strip vibration/instability
Precise feed length control enables exact positioning of keels for dimensional accuracy after cutoff. Encoder units provide feedback for automatic speed correction.
Roll Tooling Design in Light Keel Forming
Table 4. Keel forming roll tooling
Section | Components | Purpose |
---|---|---|
Entry Guiding Tools | Steering rolls, directing plates | Guide strip centering, adjust sideways positioning entering first profiling stand |
Contour Rolls | Vertical pairs of top/bottom rolls | Main profiling tools that shape metal through series of bends |
Sizing Rolls | Horizontal pairs of rolls | Calibrate final shape and exact dimensions of formed keel |
Extracting Tools | Extractor rolls, straightening rolls, pinch rolls | Guide finished keel to exit, correct minor defects |
The contour and sizing rolls are the most critical tooling elements that are precisely engineered based on virtual modeling to match the intensities of the bending sequences with the desired keel shape, thickness, strengths of the metal grade, and dimensional targets.
Improperly designed, manufactured or positioned rolls will produce defective, inconsistent keels. Roll repairs, re-machining and replacement also need appropriate setup.
Special large diameter wheeled support stands minimize frictional resistance for the rotating tools to handle heavy forming loads in light keel rolling equipment.
Roll Form Design Software
Dedicated Roll Design Simulation Programs enable virtual prototyping and mathematical modeling of the keel rolling process accounting for:
- Target keel dimensions
- Metal plasticity and strength
- Rolls geometry, surface finish, materials
- Frictional coefficients
- Optimal pass schedules
- Rolling loads and stresses
The software determines the optimal:
- Contour roll diameters, angles and positions
- Roll stroke lengths
- Bending increments
- Inter-stand tensions
- Feed rates for quality profiling
This allows accurate customization of the keel roll designer and tooling parameters for any new sectional shapes prior to physical trials, saving considerable development efforts.
Key Features of Light Keel Forming Lines
Table 5. Light keel roll former features
Feature | Advantages |
---|---|
Flexible Roll Configurations | Enable quick changeovers for variable keel sections |
Easy Roll Adjustments | Allow fast resets of tooling as per new profiles |
Auto Gap Control | Ensure uniform profiling spaces between rolls |
Ethernet Connectivity | Permits diagnostic monitoring and data logging |
Touchscreen HMI | User-friendly programming interface |
Pre-fold Deformation | Improves shape consistency for hard metals |
Modular Frame Design | Allows repositioning/adding stands for new parts |
Laser Positioning Aids | Assist faster realignments during roll changeovers |
Benefits of Light Keel Roll Forming Process
Table 6. Advantages of light keel rolling equipment
Benefits | Elaboration |
---|---|
1. High Productivity | Swift single-pass continuous processing Automated operation with minimal manual handling Quick tooling changeovers through latest hardware/software capabilities |
2. Material Savings | No machining or melting losses Near-net shape forming reduces waste generation Improved yield over casting methods |
3. Adaptability | Flexible roll configurations to make varied keel geometries Easy roll changes and machine adjustments for rapid changeovers Scalable forming modules to handle wide size ranges |
4. Enhanced Quality | Consistent and repeatable profile accuracy Precision roll design, control and instrumentation ensures uniformity Visual inspection stations for real-time checking |
5. Lower Equipment Cost | Only roll tooling needs regular replacement Maintenance is simpler than large stamping presses or fabricating lines |
6. Improved Safety | Fully enclosed forming stands guard against risks Automated material feed with no manual handling at roll sections |
Light keel rolling technology offers an advanced and reliable fabrication method for Marine, construction, mechanical, and automotive sectors requiring straight or tapered angle iron beams in small batches or mass production volumes.
Limitations of Light Keel Roll Forming
Table 7. Challenges in light keel rolling operations
Limitations | Mitigations |
---|---|
1. High Initial Investment | – Optimize production planning and machine utilization to maximize ROI |
2. Trained Staff Necessity | – Invest in skilled workforce and maintain manpower capabilities through training programs |
3. Roll Design Complexity | – Employ advanced roll geometry software tools for accurate modeling |
4. Size Capacity Constraints | – Custom builds available but not cost-effective beyond certain widths and lengths |
5. Shape Limitations | – Keel variants with tighter radii or complex curves may require heavier machines |
6. Thickness Capacity | – Heavier metal gauges need larger and more powerful units increasing cost |
While recent upgrades in automation, instrumentation and simulation programs have made keel roll operations more accessible and consistent, the constraints around machine capacities, tooling design, and metal attributes still require considerable expertise.
Structural Keel Types Produced by Light Roll Forming
Table 8. Keel products manufacturable on light rolling mills
Keel Category | Typical Shapes |
---|---|
Ship Hull Keels | – C-channel keels for hull bottom framing – Z, L and customized keels for decks |
Storage Racks | – Open back C-beams as vertical frames/cross-bracings |
Railway Keels | – Inverted T- and Bridge-section rails and cross members |
Roofing Purlins | – C and Z purlin rafter framings |
Conveyor Systems | – C or enclosed tube rails, frames and supports |
Light keel roll formers offer great flexibility in producing standardized as well as fully custom open beams in C, Z, L, U and T like profiles for their innate structural strengths at optimized weights.
Choosing A Reliable Light Keel Roll Forming Machine Manufacturer
Selecting an established keel roll former producer is vital for getting a robust, productive and trouble-free machine design. Below are key supplier criteria:
Table 9. Selection criteria for keel roll former manufacturer
Parameter | Evaluation Aspects |
---|---|
1. Proven Experience | – Years in business – Equipment supplied successfully already – Strong customer references vouching for product quality and after-sales service |
2. Customization Capabilities | – Range of keel sizes and shapes manufacturable – Offering customized solutions for specific requirements |
3. Roll Design Expertise | – Utilize advanced simulation software for precision roll engineering – Ensure optimal tool geometries for quality keel forming |
4. Production Facilities | – In-house equipment for machining large sized roll tools accurately – Modern fabrication infrastructure for assembling heavy-duty mill frames |
5. Control Systems | – Latest PLC, HMI and instrumentation for monitoring, control and diagnostics |
6. Performance Guarantees | – Verify machine productivity, tolerances, other targets promised – Manufacturer willing to demonstrate capabilities through demos |
Reputed producers like Peddinghaus, EPIC, and Benko employ solid design principles leveraging FEA and virtual modeling tools along with precision machining, fabrication and automation capabilities for delivering high-functionality keel rolling solutions. Prepare detailed specifications covering all operational aspects during supplier selection.
Price Range of Light Keel Rolling Mills
Table 10. Indicative price range of keel roll formers
Machine Width | Price Range |
---|---|
Up to 1000 mm | $100,000 to $250,000 |
1000 mm to 1250 mm | $250,000 to $350,000 |
1300 mm to 1600 mm | $350,000 to $500,000 |
1700 mm to 2200 mm | $500,000 to $800,000 |
- Prices vary based on size, drive designs, instrumentation level.
- Specialized marine-grade machinebuilder quality comes at a premium
- Automated flexible roll former with quick changeover parts more expensive
Total Equipment Cost = Machine Price + Auxiliary Equipment + Automation + Transportation/Installation + Training + Manuals
Indicative Auxiliary Equipment Cost – Around 20-25% of machine price
Total Project Cost = Total Equipment Cost + Building (or rental space) + Utility connections + Manpower + Trial runs + Working capital
Discuss budget, get itemized quotes from shortlisted suppliers. Negotiate discounts on the machine, spares, after-sales service contracts.
Installation and Commissioning
Table 11. Keel roll former installation guidelines
Parameter | Preferred Specifications |
---|---|
1. Location | – Covered, leveled factory floor – Away from hindrances causing vibrations |
2. Foundation | – 200-300 mm thick concrete foundation – Anchor bolts grouted into flooring |
3. Power Supply | – Suitable kVA transformer capacity – Stable power for drives/controls |
4. Electricals | – Cables sized adequately for control panels/drives |
5. Safety | – Adequate illumination – Mark equipment footprint area |
6. Manuals | – Equipment manuals, electrical drawings, P&I diagrams |
7. Installation | – Machines positioned properly, leveled, aligned to layouts |
8. Commissioning | – Calibrate sensors/instruments – Initial test runs with setup material |
Carefully survey the installation site, design foundations as per supplied drawings, and prepare power, compressed air and other utility connections on time.
Ensure supplier technicians align components properly. Observe initial test runs and validate machine performance before accepting delivery.
Operation of Light Keel Rolling Line
Table 12. Operation guidelines for keel roll formers
Stage | Procedure |
---|---|
1. Machine Start | – Turn main power ON – Start hydraulic power packs/cooling systems |
2. HMI Selections | – Select product recipe from list – Check prerequisites selected |
3. Jog Mode | – Inch material through interlocked blocks in jog mode |
4. Auto Mode Start | – Initiate automatic run cycle |
5. First Piece Out | – Check first formed piece dimensions – Make minor machine adjustments if required |
6. Monitor Operation | – Periodically verify product quality viz. tolerances, finish |
7. Temporary Halt | – Retract material away from tooling before stopping |
8. Shutdown | – Stop drive motors/feeds – Turn control system and main power OFF |
Do’s and Don’ts:
- Do conduct trial runs on setup grade material before production pieces
- Don’t exceed equipment load capacity limits
- Do watch forstrip wandering and pre-emptively realign
- Don’t try to alter safety interlocks or roll gaps without authorization
Tips:
- Maintain consistent material quality for steady production
- Clean equipment routinely and lubricate moving joints
- Address even minor defects quickly before they propagate
- Maintain detailed records of machine parameters, output and maintenance
Proper operation procedures are key for maximizing machine up-time while meeting safety and quality norms. Verify production numbers match the rated technical specifications during your test runs.
Maintenance Guidelines for Light Keel Roll Lines
A comprehensive maintenance regimen reduces unplanned downtime losses and maintains light keel roll former health.
Table 13. Maintenance schedule for keel rolling equipment
Activity | Frequency | Tools Needed |
---|---|---|
Forming Roll Inspection | Weekly | Edge finder, micrometer, optical comparators |
Roll Surface Cleaning | Fortnightly | Hard nylon brush, cloth, cleaner solution |
Roll Alignment Checking | Monthly | Laser, dial indicators |
Bearing Greasing | Monthly or as specified | Grease gun filled with lithium/polymer grease |
Fastener Tightening | Quarterly | Hex key wrenches, torque wrenches, sockets |
Gearbox Oil Change | Yearly or per OEM spec | Drain pan, filter cloth, gear oil, seals |
Additional Maintenance Aspects
- Lubricate machine guideways and leadscrews
- Verify hydraulic power pack operation
- Check chain/belt tensioning; adjust or replace as needed
- Calibrate/bump test sensors, load cells periodically
- Inspect wear on forming rolls; re-machine or replace when out of spec
- Keep spare parts like seals, bearings, fuses handy
In-house maintenance vs third-party service contracts have their own pros and cons in terms of convenience and cost. Having personnel trained on machine troubleshooting allows faster problem resolution.
Key Considerations When Buying a Light Keel Roll Former
Table 14. Buying criteria for light keel rolling line
Factor | Evaluation Aspects |
---|---|
1. Production Parameters | – Coil widths, metal thicknesses likely needed – Keel lengths required; batch sizes – Annual quantities projected |
2. Part Performance Needs | – Ask for tolerances, surface finishes feasible – Operating speeds possible; Quick changeover ability |
3. Ease of Operation | – Control simplicity, diagnostics capabilities – Optimized safety provisions |
4. Expandability | – How convenient to adapt machine later for extra capacity or new parts |
5. Technical Support | – Installation, maintenance and operator training offered – Service response time |
6. Total Costs | – Machine price, spares pricing, after-sales costs – Evaluate TCO over lifetime not just initial price |
Carefully detail your production requirements, quality expectations, available budget and any foreseeable future needs during preliminary discussions with suppliers.
Request equipment trial runs on your representative materials at manufacturer sites during due diligence. Independent performance certificates also build confidence.
Prioritize reliable after-sales back-up over lowest price offerings to minimize headaches later. Discuss payment plans, maintenance contracts etc. to negotiate extended flexible terms for cash flow relief.
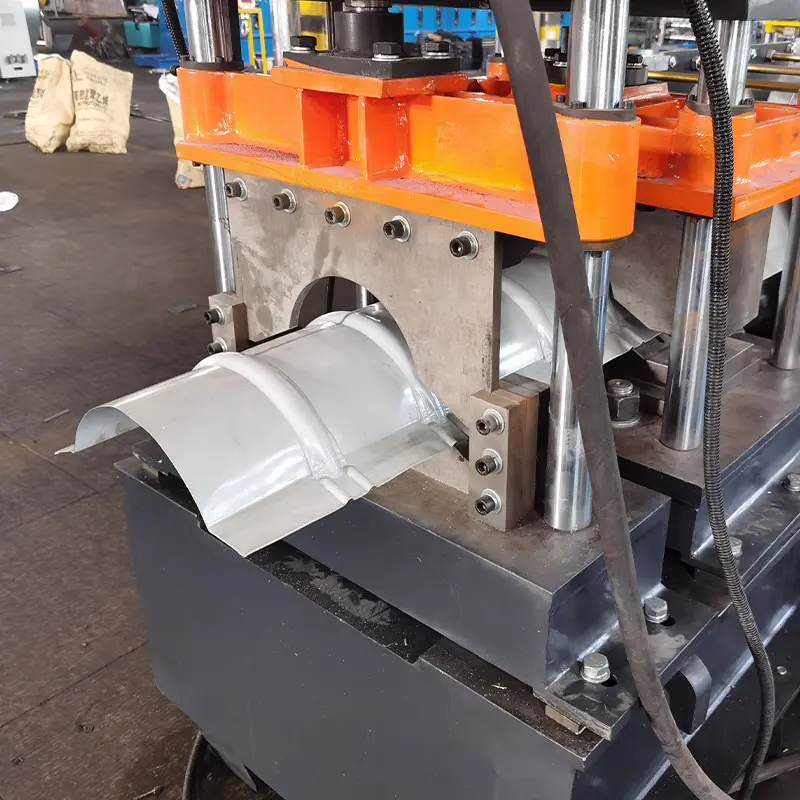
Pros and Cons of Light Keel Roll Forming Process
Table 15. Advantages and limitations of light keel roll forming
Pros | Cons |
---|---|
– High production rates – Tight tolerances – Low operating costs – Minimal secondary processing – Low replacement tooling cost | – High initial equipment investment – Dedicated machines offer low flexibility – Size and shape limitations – Complex roll design engineering – Trained workforce requirement |
When weighing light keel roll forming equipment options, consider key technical attributes like:
- Material width ranges needed now and in future
- Thickness capabilities cover present and expected material grades
- Tool adjustment flexibility for current and alternate shapes
- Precision and tolerances achievable
- Costs of automation features or manual operation tradeoffs
- Overall operating plus maintenance expenses
Discuss realistic expectations around flexibility, changeover speeds, and reliability relative to capabilities stated by the manufacturer during demonstrations and verify if their solution can address your requirements with the optimal balance of cost versus capability.
FAQs
Q1. What are typical maintenance costs for light keel rolling mills?
A1. About 2-4% of machine cost per year inclusive of spares, repairs and third party service charges. Proper preventive maintenance minimizes overall expenses.
Q2. Can these machines make tapered keels for ships?
A2. Yes, specialized flexible keel lines with ability for quick tooling changes can produce longitudinally tapered keels by varying the roll gaps along the length.
Q3. What qualification checks are required during roll forming machine installation?
A3. Mainly dimensional alignment verification between shafts, roll clearances, level checking and sensor calibrations per supplier documented procedures.
Q4. How to calculate keel roll forming machine productivity rates?
A4. Productivity = Line Speed x Keel Length Per Minute. Output rated in meters or feet per minute of keels produced based on material width and thickness.
Q5. What safety mechanisms do these keel rolling mills employ?
A5. Fully enclosed forming stands, emergency stop buttons, interlocked guards, dual circuits, roll retraction to name some typical provisions.