Purlin রোল তৈরির মেশিন are an essential equipment for factories producing purlins for roofing and wall cladding applications. This comprehensive guide provides detailed information on purlin roll forming machine manufacturers, working process, types of machines, raw material requirements, production capacity, customization options, installation, operation and maintenance procedures, cost analysis, and tips for selecting the best supplier.
Overview of Purlin Roll Forming Machines
A purlin roll forming machine is used to continuously bend and form metal coils into customized purlin profiles as per the required size and shape specifications. Purlins serve as secondary roofing support elements which are mounted on the primary structures. They are widely used in industrial, commercial and residential building construction.
The raw material needed is metal coils, usually galvanized steel, galvalume steel, or aluminum. The metal strip is passed through a series of roller dies to shape it into C, Z or sigma shaped purlins with the desired dimensional and structural properties.
Advanced purlin roll forming machine lines can create complex custom profiles, emboss logos, cut to length, stack, and bundle the formed purlins automatically for easy shipping.
Benefits of Using Purlin Roll Formers
- Continuous, high speed production up to 100 meters per minute
- Consistent and uniform profiles ensuring structural integrity
- Cost effective versus other manufacturing processes
- Flexible production with quick die changeovers
- Custom profiles for strength and aesthetic needs
- Reduced labor requirement with automated features
Main Components of Purlin Rolling Lines
The major sections in a purlin rolling line are:
- Uncoiling Unit: Rotates the coil for smooth and controlled feeding of strip
- Feeding Rack: Transports strip through machine at set speed
- Forming Stations: Bend strip progressively using roller dies
- Hydraulic System: Applies pressure for precise forming
- Cutoff Device: Cuts profiles at desired length
- Stacking Unit: Collects cut purlins and stacks neatly
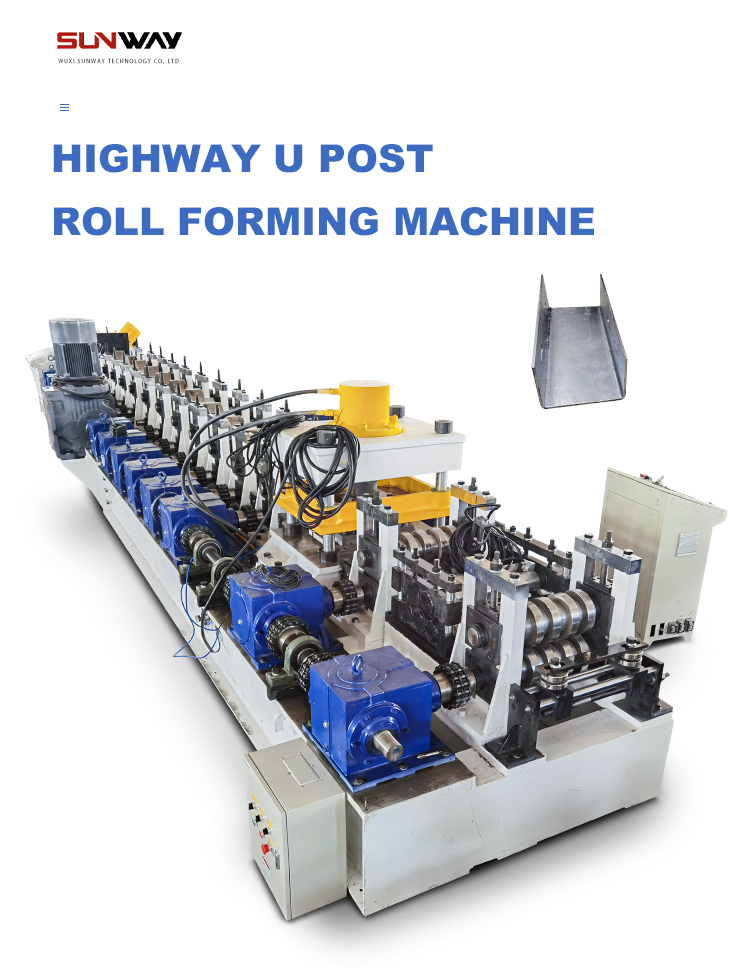
Types of Purlin Rolling Machines
Type | Description |
---|---|
Manual Purlin Machine | Basic roll former with manual controls and no automation |
Automatic Purlin Line | Feature automated uncoiling, feeding, cutting, stacking to minimize manual handling |
All-Electric Purlin Roller | Powered fully by electric motors and drives for precision control |
CNC Purlin Roller | Computer numerical control for on-demand profile changes |
High-Speed Purlin Machine | Produces up to 100 meters of purlins per minute |
Working Process of Purlin Roll Forming Machines
The full manufacturing process on a modern high-speed purlin roll forming production line generally follows the steps shown below:
1. Decoiling
The strip decoiler machine holds the metal coil and rotates it to unroll and straighten the strip. The decoiler feeds the strip into the roll former at a consistent speed and tension.
**2. Forming **
The metal strip is fed through a series progressive rolling stations – each with an upper and lower forming roller die made to the profile specifications. As it passes through each station, the geometry of the strip is incrementally bent into the final purlin shape.
3. Hydraulic Pressing
Special hydraulic cylinders provide downward pressure on the roller dies for tight tolerance and fine detailing of the purlin profile. The hydraulic system controls the precision of the forming process.
4. Cutting
After the full purlin profile is formed, the cutoff press slices the purlins at the set length by punching or sawing action. The length can range from 2 meters to 12 meters generally.
5. Counting
Sensors count the cut purlin pieces as they exit the line. This allows the machine to monitor production rate and totals.
6. Bundling
A specially designed bundling unit neatly arranges up to 5 purlins together into a bundle for easy handling and transport. Strapping can also be integrated.
7. Stamping
If required, an inkjet printing device can imprint logos, part numbers, dimensional data and other product information on the purlins.
8. Packing
The stacking table arranges cut purlin bundles onto pallets or skids for shipment to customers. This automates the entire post-forming packing process.
Raw Material Requirements
The primary raw material needed for the purlin rolling process is metal strips and coils. Galvanized steel is most commonly used. Other materials like galvalume steel and aluminum are options for specialized applications.
Key strip parameters:
- পুরুত্ব – Commonly 0.7mm to 3.0mm
- Width – Up to 1250mm wide coils supported
- Surface – Hot-dipped galvanized, color coated, pre-painted etc.
It is recommended to use high grade steel with consistent thickness, proper surface treatments, and defined mechanical properties to achieve best production results.
Production Capacity of Purlin Rolling Machines
The output capacity of a purlin roll forming system depends on:
- Line speed (meters per minute)
- Operating hours per day
- Desired purlin length
- Time for coil changes
Output Rate Estimate
For example, a 100 meter per minute line, running 16 hours per day, at 6 meter long purlins can produce:
100 m/min x 60 min/hr x 16 hrs = 96,000 meters per day
At 6 m length = 16,000 purlins per day
Thus high speed purlin roll forming machines can manufacture over 5000-6000 tonnes annually depending on length.
-
ঢেউতোলা প্যানেল রোল তৈরির মেশিন
-
হালকা গেজ ইস্পাত রোল গঠন মেশিন
-
স্টিল বক্স প্লেট মেকিং রোল ফর্মিং মেশিন
-
বৈদ্যুতিক মন্ত্রিসভা ফ্রেম রোল গঠনের মেশিন
-
দিন রেল রোল ফর্মিং মেশিন
-
ওমেগা পুরলিন রোল ফর্মিং মেশিন
-
CZ Purlin রোল তৈরির মেশিন
-
সম্পূর্ণ স্বয়ংক্রিয় সি purlin রোল গঠন মেশিন দ্রুত পরিবর্তন
-
স্ট্যান্ডিং সীম ছাদ প্যানেল তৈরির মেশিন
Customization Features
Modern purlin rolling mills offer extensive customization options to produce special purlins:
Profile Options
- C or Z or Sigma cross-section
- Depth & width per needs
- Thickness 0.7mm to 2.0mm
- Custom ridge & valley detailing
Special Shapes
- Emboss logo or patterns
- Connection holes
- Offset & standing seams
- Vertical stiffeners
Dimensional Range
- Thickness up to 3mm
- Width up to 1250mm
- Length 2m to 14m
- Special angles & tapers
Materials
- Galvanized steel
- Galvalume steel
- Aluminum
- Color coated steel
Secondary Operations
- Inkjet printing on purlins
- Cutting & punching
- Bundling & packing
Purlin Roll Forming Machine Manufacturers
There are many manufacturers across China, India, and Western countries specializing in high quality purlin rolling mill equipment. Here are the top exporters:
প্রতিষ্ঠান | Location | Product Range |
---|---|---|
Beijing Hi-Lite Machinery | China | Manual, automatic, high-speed lines |
Rollmech Machines | ভারত | Customized purlin & decking plants |
Gasparini SpA | ইতালি | CNC controlled precision roll lines |
Metform | USA | American made innovative purlin rollers |
DAHILI Machinery | Taiwan | Affordable small to mid-sized systems |
When selecting a supplier, you must evaluate technical capability, production quality, customization flexibility, service support, and commercial terms like pricing and delivery.
Installation of Purlin Rolling Lines
Proper installation is vital for smooth functioning of a purlin roll forming system. Here are the key requirements:
Site
- Covered shed with concrete floor
- Minimum area 1200 sq.ft for line
- Proper lighting & ventilation
- Power supply access
Equipment Positioning
- Line should be fully anchored
- Decoiler located for easy loading
- Forming sections level & aligned
- Cutoff presssecured in place
- Exit table at waist height
Commissioning
- Electrical connections checked
- Emergency stops & safety tested
- Hydraulic power pack verified
- Trial runs conducted & validated
Check that all anchor bolts, bearings, gears engage accurately as per manufacturers manual during commissioning.
Operation of Purlin Rolling Machines
Purlin rolling mills are designed for safe, convenient operation via the following modes:
Electric Control Panel
The panel features motor starters, emergency stop, system indicators for joystick based control of production.
Automatic Mode
In auto mode, the full rolling process from feeding to cutting to bundling runs in sequence by sensor based control logic. Operator inputs product dimensions.
Manual Mode
Individual sections like decoiler, forming stations, cutoff press can be independently operated for setups, maintenance or trials.
Safety Features
- Emergency stop buttons
- Failsafe circuits
- Markers & barricades
- Warning alarms & lights
Operation must always follow standard guidelines per the equipment handbook from the purlin machine manufacturer.
Maintenance of Purlin Roll Forming Lines
To maximize uptime and production efficiency, purlin rolling mills need systematic preventive maintenance as outlined below:
Daily Checks
- Inspect rollers, strippers for wear
- Check hydraulic oil levels
- Verify electric panel readings
- Test emergency stop function
Weekly Checks
- Clean oil filters & radiators
- Tighten bolts, nuts, clamps
- Examine belt tension & gears
- Apply lubricants on bearings
- Adjust roller alignment
Quarterly Checks
- Thorough cleaning of line debris
- Coil mandrel wear verification
- Inspect & coat transmission chains
- Flush hydraulic systems
- Gearbox oil change
Yearly maintenance schedules must also examine entire line foundation, calibration of sensors, control software upgrades in detail.
Cost Analysis of Purlin Rolling Mills
The economics determining affordability and ROI on purlin roll forming machine investment includes:
Key Cost Factors
- Equipment Price – $35,000 to $250,000 per line
- Setup Expense – Approximately 15-20% of machine cost
- Raw Material – Steel coil inputs based on tonnage rate
- Utilities – Power consumption plus backups
- Consumables – Lubricants, filters, spares & accessories
- Manpower – Skilled labor for efficient running
Savings & Revenues
- Continuous Processing – High speed & reliability maximizes production versus manual methods
- Quality Profiles – Superior forming generates smooth and strong purlins meeting certification standards.
- Lower Labor Costs – Automated feeding, stacking and bundling reduces manual effort substantially.
- Ideal For Roofing Contractors – Enables fast supply of custom purlins for construction projects
Approximate payback period is 1-2 years for affordable purlin rolling lines. Precision CNC machines may take longer ROIs but offer superior accuracy.
Choosing the Best Purlin Roll Forming Machine Manufacturer
Selection criteria to ensure procurement of high performance purlin rolling equipment:
Technical Factors
- Proven Design & Engineering – Specialization in building modern purlin roll formers
- Build Quality – Use of premium components like motors, drives for reliability
- Production Output – Speed, efficiency and accuracy metrics
- Customization Range – Capability to produce exact niche purlin profiles
- Automation Features – Essential for reducing human effort
Commercial Factors
- Pricing – Competitive capital and operational costs via tech optimization
- Payment Terms – Flexible installments, LC, TT options
- Delivery Schedule – Fast manufacturing and shipment
- Service Support – Minimal downtimes via training, parts supply, upgrades
Verification of the above parameters through reference checks allows selection of purlin roll former company matching application needs and budget.
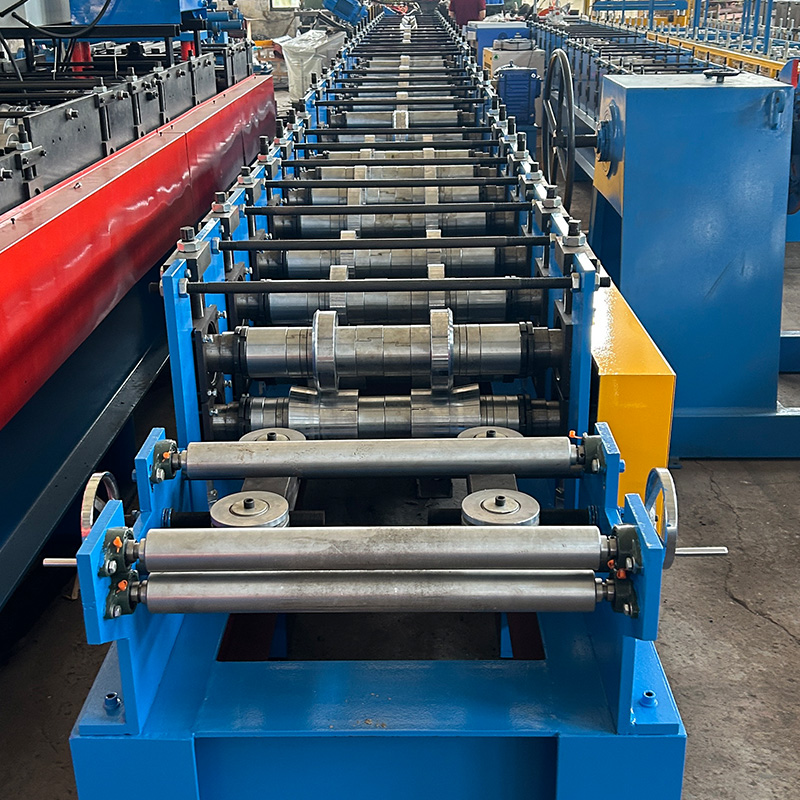
FAQ
Q: What thickness of purlins can be formed?
A: Standard machines can handle up to 3 mm thickness. Special heavy gauge lines are available for 4 mm strips.
Q: What is the typical production rate from these machines?
A: Speeds up to 100 meters per minute are possible. Output depends on parameters like operating hours, length, and product mix.
Q: Can Z, C and Sigma profiles be made on the same machine?
A: Yes, by quick die changeovers, different profile shapes can be easily formed as most roll toolings are modular in design nowadays.
Q: What pre-treatment must be done on coils before using in this process?
A: Hot-dipped galvanizing is highly recommended as corrosion resistance coating along with correct sizing and degreasing.
Q: What safety precautions are required during operation?
A: Mandatory usage of protective gear like helmets, shoes, gloves along with marking unsafe zones, emergency controls, and proper staff training.
Q: What is the typical life expectancy of these purlin rolling machines?
A: Approximately 15-20 years with regular preventive maintenance as per manufacturers manual and by using good quality consumables spares & lubricants.
Q: What factors affect the pricing of purlin roll forming equipment?
A: Key elements are maximum strip width & thickness supported, production speed, automation features, customization scope, raw material grade, and optional secondary processes integrated.
Q: How is the quality of the formed purlins and process stability ensured?
A: The latest computerized lines offer intelligent monitoring with feedback loops. Parameters like line speed, hydraulic pressure, motor load, die pressures are continuously controlled to minimize deviations.
Q: What expertise is required to efficiently operate purlin rolling mills?
A: Mechanical engineering background with experience using heavy fabricated equipment is preferred. Control panel operations can be learned through detailed manufacturer training programs.
Q: Is regular maintenance and service support provided by equipment suppliers?
A: Yes, responsible manufacturers offer maintenance manuals, spare parts supply, periodic service visits, and hardware/software upgrades to maximize lifespan of machines.