Roll forming is an efficient, continuous process for producing parts with long uniform cross-sections. The রোল গঠনের মেশিন is the heart of the production line that shapes sheet metal coil into desired profiles using a series of roller dies.
Choosing a dependable roll former OEM factory is crucial for getting capable equipment, prompt after-sales support and value for investment.
This guide covers major roll forming machine manufacturers across geographies, their offerings, strengths and selection factors for partnership.
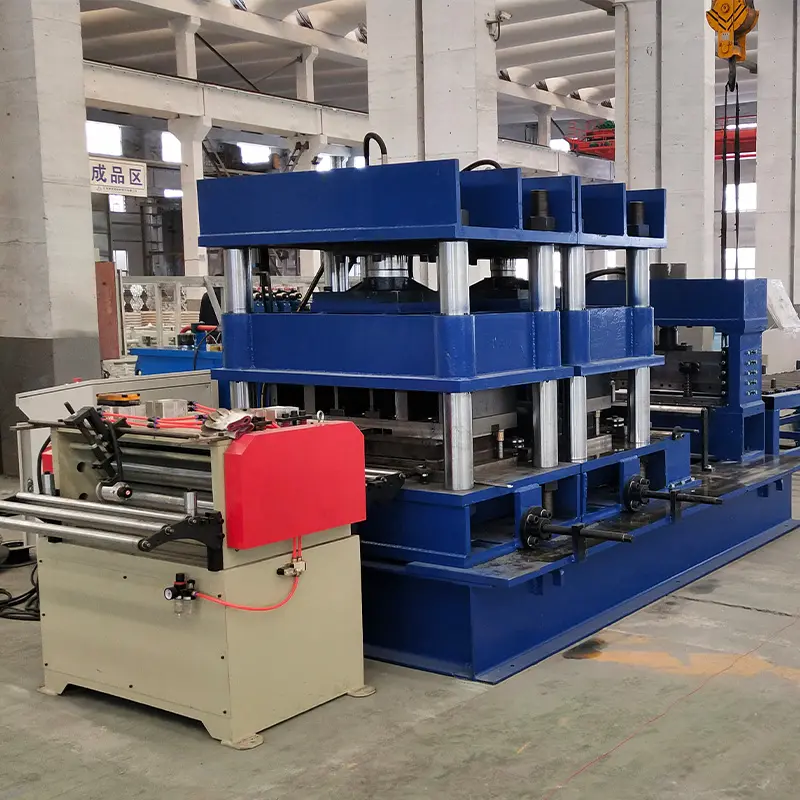
Overview of Roll Forming Process
Roll forming works by passing sheet or coil stock through consecutive roller die stands which apply incremental cold forming until the final shape is achieved. Common roll formed profiles include roofing panels, racks, door sections and electronic enclosures.
Figure 1: Roll forming progression from flat strip to finished part
The advantages of roll forming are fast production, efficient raw material utilization, flexibility for automation and low tooling maintenance over long runs.
রোল ফর্মিং মেশিনের প্রকার
Roll formers come in different configurations based on production needs:
Table 1: Major Roll Forming Machine Types
Machine Type | Description | Typical Applications |
---|---|---|
In-line Roll Former | Uncoiler-feed straight into forming-cutoff line | High volume long production runs |
Reversible Roll Former | Reversing rollers to return sheet through dies | Low volume applications, save space |
Portable Roll Former | Compact on wheels for mobility | On-site production requirements |
Custom Roll Former | Engineered for specialized profiles | Unique proprietary cross-sections |
In addition to working width and forming length, options like number of die stations, level of automation, secondary operation capability and software flexibility differentiate machine models.
Top Roll Forming Machine Factories
Some leading global OEMs with decades of expertise in roll former engineering are:
Dimeco – USA
Key Models: Helios, UltraFab, MaxxForm
Dimeco is a major American roll forming equipment brand with over 50 years of know-how. Key strengths include:
- Modern plant infrastructure and stringent quality norms
- High end automation options like robotic part handling
- R&D investments in IoT for data-driven improvements
- Responsive technical support through trained representative network
They offer the latest solutions like the Helios series with smart IoT connectivity for predictive maintenance and production monitoring.
Gasparini – Italy
Key Models: FlexyRoll, FastRoll, ServRoll
Gasparini from Italy has over 60 years of industry presence. They focus on speed and flexibility:
- High speed production at >100 ft/min
- Quick change-over modular tooling
- Easy integration of secondary operations
- Advanced software for efficient changeovers
Gasparini’s FlexyRoll range offers versatile roll solutions paired with intelligent production management capabilities.
Formtek – Canada
Key Models: Orion, Maxima, Optimax
With over 25 years of specialization, Canadian brand Formtek provides made-to-order forming solutions. Their advantages include:
- Custom engineering of roll formers
- Precision quality assurance over the full process
- Niche finishing solutions through partner networks
- Roll design simulation software for optimal equipment builds
They are experts in tailoring solutions from scratch based on customer needs via their proprietary simulation and controls software.
Bradbury Group – USA
Key Models: SelectRoll, EasyForm, Pro-Formpak
The Bradbury Group have been pioneers in pioneering roll forming for over 70 years. Their strengths lie in:
- High-end fully customized roll solutions
- Integrated extrusion and embossing modules
- Specialists in high speed thin gauge production
- Extensive spare part inventory and field service crew
Bradbury’s SelectRoll models paired with Pro-Formpak software offer high efficiency automation.
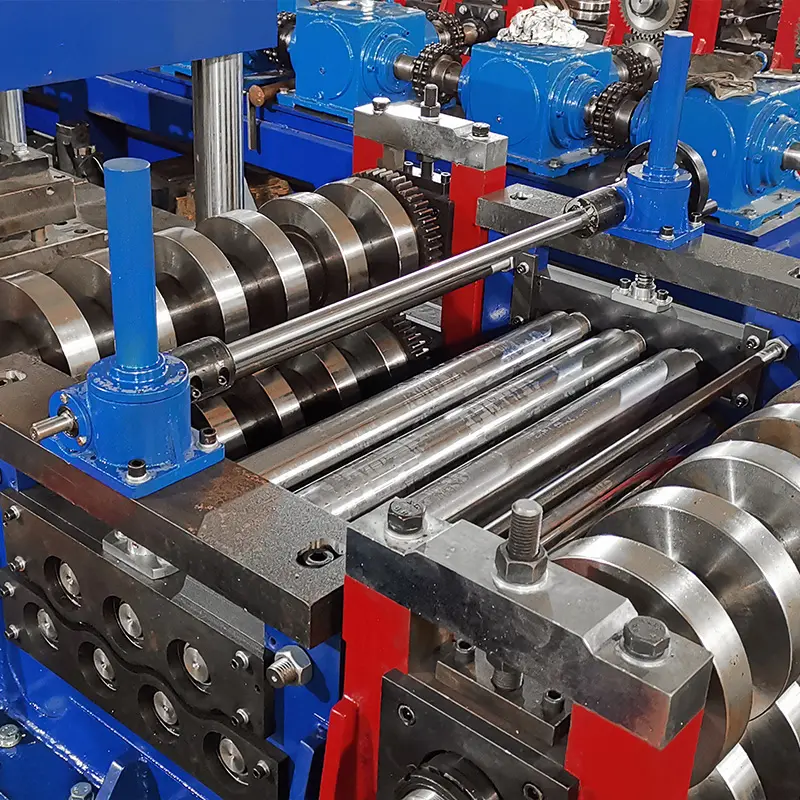
Comparison of Top Roll Former Producers
Table 2: Leading রোল ফর্মিং মেশিন Brand Comparison
Manufacturer | Location | Roll Models | Price Range | Max. Speed | Strengths | Limitations |
---|---|---|---|---|---|---|
Dimeco | USA | Helios, UltraFab | $150k to $500k | 80 ft/min | Automation, IIoT connectivity | Complex shapes capability |
Gasparini | ইতালি | FlexyRoll | $250k to $1 Mil | 100 ft/min | High speed forming | Inline secondary ops |
Formtek | Canada | Orion, Optimax | $100k to $800k | 60 ft/min | Custom engineering | Budget automated lines |
Bradbury | USA | SelectRoll | $150k to $600k | 120 ft/min | Thin gauge high speed | proprietary electronics |
Evaluate manufacturers against production targets, quality, customization ability and service infrastructure.
Inside a Roll Forming Machine Factory
Modern roll former OEM factories leverage the latest infrastructure for quality and productivity. Here is what the shopfloor typically looks like:
Key Sections:
- Fabrication – Where structural frames, gears, guards etc. are made
- Sub Assembly – Gear stands, conveyors etc. are built up
- Machining – Where roller dies, shafts, blades are CNC machined
- Assembly – Where machines are integrated and wired
- Testing and Validation – Where roll ops are verified before dispatch
- Automation Focus – Robots, conveyor systems for material Handling
- Quality Checks – Laser alignment, dimensional checks using CMMs
- Flexibility – Modular builds, quick changeovers
The layout is optimized for efficient material and information flows across interconnected work stations.
Ancillary Equipment with Roll Forming Lines
Often customized secondary operation stations are integrated in the production line:
Table 3: Common Roll Forming Line Ancillary Equipment
Machine | Role | Method |
---|---|---|
Embossing press | Imparts raised textures and logos | Stamping dies |
Hole punch | Create lightening holes and hardware slots | Punch and die set |
Shear/slitter | Longitudinal cut for width control | Rotary shear blades |
Decoilers | Alternative coil holding and feeding | Motorized tension regulated unwind stands |
Ink marking | Printing date stamps, barcodes etc. | Inkjet digital printer |
Panel bender | Add transverse bends for ducts | Adjustable snap folders |
These help impart additional features or functionality to roll formed base profiles.
Testing Standards at Roll Former Factories
To prove performance key tests are conducted:
- Dimensional checks – Using height gauges and CMMs
- Bend quality – By measuring formed angles and observing for defects
- Speed trials – Testing at high feeds for continuous runs
- Overload – Stressing dynamic components close to peak capacity
- Environmental – Temperature, humidity, vibration testing
- Field evaluations – Beta testing at customer plants before final design sign-off
Extensive prototyping validates capability prior to releasing production grade machines.
Global Certification Standards
Reputed factories comply with:
- ISO 9001 – Quality Management System
- ISO 14001 – Environmental Management System
- OHSAS 18001 – Occupational Health and Safety Assessment
This ensures they meet the highest organizational, manufacturing and sustainability benchmarks.
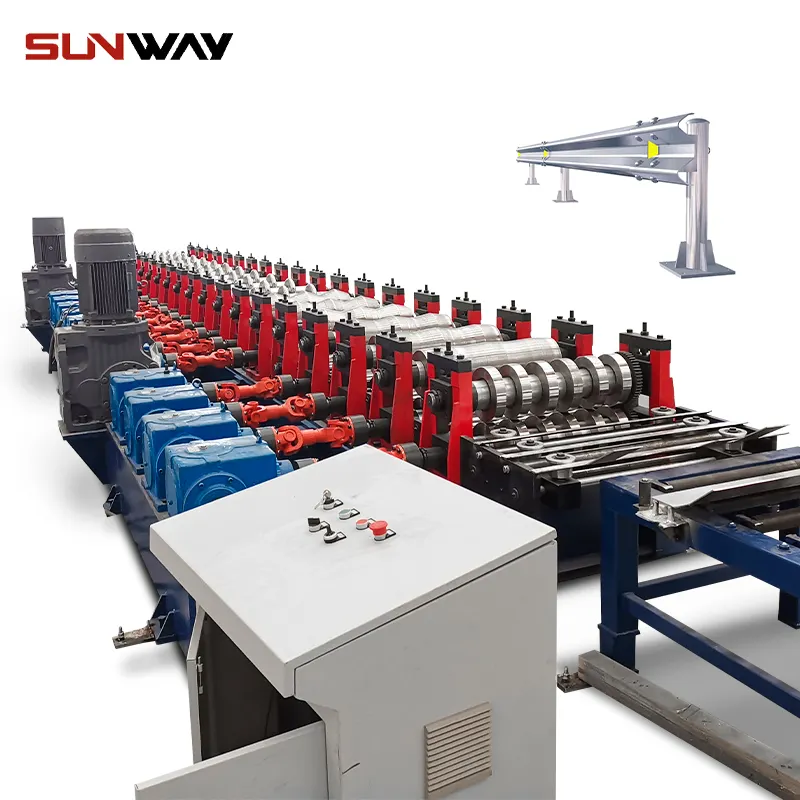
Choosing Your Roll Forming Machine Partner
Aspects to evaluate when shortlisting manufacturers:
Table 4: Roll Former OEM Selection Criteria
Parameter | Guidelines |
---|---|
অভিজ্ঞতা | Number of years in business |
Domain Knowhow | Understands nuances your specific product needs |
Quality Focus | Stringent norms, global certifications |
Delivery Record | History of on-time, on-quality execution |
Customization Skills | Ability to customize for special needs |
Service Infrastructure | Trained technicians, adequate spare part stocks |
Pricing and Value | Price commensurate with quality and features |
Interact with multiple vendors in detail to choose the best fit for needs.
Summary
Partnering with an expert রোল গঠনের মেশিন factory with proven technology, quality and support credentials ensures access to robust equipment that delivers productivity with precision. Invest time to clearly outline production requirements and evaluate supplier strengths on all aspects. This guide covered leading international OEMs like Dimeco, Gasparini and Formtek along with capabilities to look for. Leverage the latest innovations in roll forming for maximizing output.