Working Principle
The working principle of mould cutting downpipe roll forming machine involves sequential bending and shaping of metal coil feedstock through consecutive roller die stations to gradually form an angled downpipe profile.
Integral punch presses or other secondary operations create holes, notches and hardware fits. An additional mould cutting module shears the formed piece from the strip, creating finished drain pipes ready for installation.
Benefits over manual methods include:
- Automated process for high production rates
- Precision calibration and sizing
- Integrated features like holes, slots, tabs
- Standardized outputs with minimal variability
- Limited manual labor aside from setup
mould cutting downpipe roll forming machine Types
Downpipe roll former machinery classifications include:
Table 1. Major Downpipe Roll Former Equipment Specifications
Type | Width | পুরুত্ব | Speed | Stations |
---|---|---|---|---|
Light | <200mm | 0.4-0.8mm | 10m/min | 8 |
Medium | 200-300mm | 0.5-1.2mm | 15m/min | 10 |
Heavy | >300mm | 0.8-1.5mm | 20m/min | 12+ |
Table 1 highlights how max strip width, metal thickness, running speed and number of forming stations differentiate roll former models.
mould cutting downpipe roll forming machine Production Process
A complete downpipe roll forming production sequence comprises:
- Loading raw metal coils
- Decoiling and feeding strip through guides
- Forming stations shape profile
- Hardware insertion – tabs, holes, notches
- Shearing die punch separates pieces
- Exit conveyor stacks finished drain pipes
The process allows swift precision part creation with minimal manual input between automated steps. Operators simply maintain equipment settings and offload finished downpipes.
Materials and Customization
Metals well-suited for mould cut downpipe roll forming include:
- Hot dipped galvanized steel – durable exterior corrosion protection with zinc coating
- Prepainted steel – colored aesthetic coating
- Aluzinc steel – zinc-aluminum alloy coating
- Copper – traditional material with long service lifespans
- Stainless steels – premium grades like 304 and 316
Profile customization options:
- Dimensional sizing to fit existing rainware infrastructure
- Square, rectangular, round and oval shapes
- Mounting tabs, seam caps and other hardware
- Decorative stamped patterns
- Matching elbows and connector fittings
- Rainwater filter basket attachments
This flexibility suits residential buildings along with large commercial roof drainage product needs.
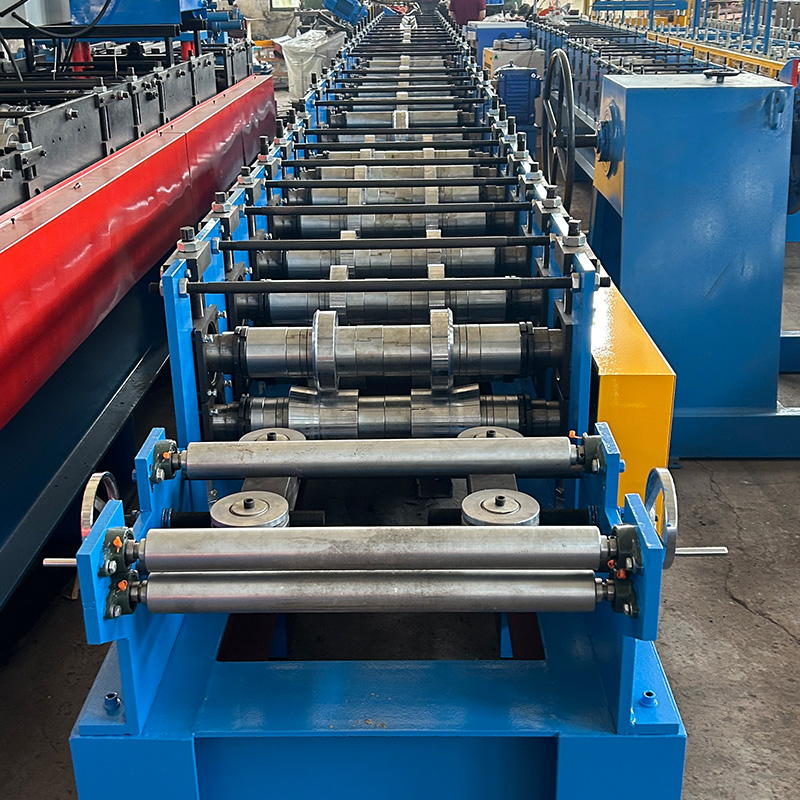
Suppliers and Pricing
There are over 40 major international downpipe roll former equipment manufacturers globally. A sample includes:
Table 2. Notable Mould Cutting Downpipe Roll Former Manufacturers
প্রতিষ্ঠান | Location | Base Pricing |
---|---|---|
Botou Xianfa | China | $7,500 – $65,000 |
Jouanel | ফ্রান্স | $185,000 – $500,000 |
Metform | Turkey | $15,500 – $115,000 |
Rollwiz | ভারত | $9,500 – $140,000 |
Shanghai Rollwell | China | $18,500 – $260,000 |
Cost factors include:
- Maximum strip width
- Secondary processing capabilities
- Construction materials
- Brand reputation
- Support services offered
Budget Chinese manufacturers offer affordable equipment while premium Western suppliers provide heavy output but with higher equipment price points.
Installation, Operation, Maintenance
To install a mould cutting downpipe roll former:
- Offload components using forklift/crane
- Anchor reinforced frame to level concrete
- Wire necessary electrical, pneumatic lines
- Position decoiler, loop feeder, stations per design
- Insert tooling packs based on profile
For operation:
- HMI and PLC automate actual roll process
- Input production variables – width, thickness, lengths
- Monitor strip flow, shearing, finish quality
Maintenance best practices:
- Inspect/replace forming rollers
- Check hydraulic fluid levels
- Clear metal fines
- Test emergency stop buttons
- Audit safety mechanisms
Proactive preventative maintenance protects operational uptime on downpipe roll forming equipment.
Choosing Manufacturers
Crucial factors when selecting reputable mould cutting downpipe roll former suppliers:
Table 3. Key Manufactuer Vetting Considerations
Factor | Description |
---|---|
Production Expertise | Specialized knowledge of roof drainage fabrication |
Customization Range | Broad profile variation and hardware insertion capabilities |
Construction Quality | Use of premium components for longevity |
Responsiveness | Rapid technical support and service response |
Overall Value | Balance of quality, reliability and affordable pricing |
No singular manufacturer dominates every category – end users should rank decision factors appropriately for their specific guttering production requirements during the downpipe roll former selection process.
-
বৈদ্যুতিক মন্ত্রিসভা ফ্রেম রোল গঠনের মেশিন
-
দিন রেল রোল ফর্মিং মেশিন
-
তারের মই রোল ফর্মিং মেশিন
-
পিভি মাউন্টিং বন্ধনী সি শেপ প্রোফাইল রোল ফর্মিং মেশিন
-
তারের ট্রে রোল ফর্মিং মেশিন
-
স্টিল কয়েল কাট টু লেংথ লাইন মেশিন
-
স্টিল কয়েল কাট টু লেংথ লাইন মেশিন
-
স্টিল কয়েল কাট টু লেংথ লাইন মেশিন
-
পিভি মাউন্টিং ব্র্যাকেট রোল ফর্মিং মেশিন (HAT / ওমেগা প্রোফাইল)
Comparative Analysis
Compared to manual cutting and fabricating methods, powered mould cutting downpipe roll forming provides:
Table 4. Relative Pros and Cons
Metric | Mould Cut Roll Forming | Manual Fabrication |
---|---|---|
Setup Time | Medium | Very quick |
Operating Costs | Lower material/energy use | Higher labor costs |
Build Consistency | Optimized software control | Worker variability |
Throughput Speed | High continuous volumes | Very slow pace |
Size Capabilities | 300mm+ widths possible | ~200mm max typical |
Hardware Integration | Inline automation available | Manual insertion only |
Precision | Excellent, software-corrected | Approximate sizing |
Changeovers | Tooling pack swaps | New fabrication |
In summary, automated roll forming generates superior downpipe components over manual methods – both in productivity, consistency, accuracy and integrated hardware capabilities.
Frequently Asked Questions
Q: What drainage capacities can downpipe roll formers accommodate?
A: With large width capacities, high volumes like multi-story buildings, stadiums, industrial plants can be matched to local precipitation data.
Q: How long does a downpipe roll former tooling pack last?
A: Approximately 40,000 linear feed meters of strip. For two daily 10 hour shifts at 20m/min line speeds, changeover comes around every 2 months.
Q: Can elbow fittings be created on the same downpipe roll line?
A: Yes, some advanced models integrate elbow forming stations or secondary endformers to produce right-angle downpipe connectors without requiring manually welded elbows.
Q: What factors affect downpipe roll former machine pricing?
A: Key considerations include: overall line width, material thickness capacity, secondary processing features, construction materials used, brand reputation, support services, and customization capabilities.
Q: Can a small shop produce their own customized downpipes?
A: Lower cost manual bending brakes allow small scale custom downspouts but labor, precision and consistency issues make automated roll forming preferable for volume production runs.
Q: How are decorative patterns added to downpipes?
A: Textures, logos and styling can be built into the profile tooling. Painting is also possible but may require pre-treatment to ensure adhesion suitability on various drainage material surfaces.