Trapezoidal sheets made by roll forming have angled side flutes resembling trapezoids in cross-section. Their structural strength and forming efficiency make them ideal for roofing, cladding, buildings, shelters, wall liners and window profiles. This guide covers the end-to-end system for setting up trapezoidal sheet production lines.
Overview of trapezoidal sheet roll forming machine
Roll forming can continuously shape metal coils into various trapezoidal sheet profiles using consecutive roller dies. Key benefits are:
- High throughput production for cost efficiency
- Flexible output with quick die changeovers
- Consistent quality with tight tolerances
- Just-in-time supply eliminating stockpiles
- Fully automatic operation reducing labor
- Small equipment footprint saving facility space
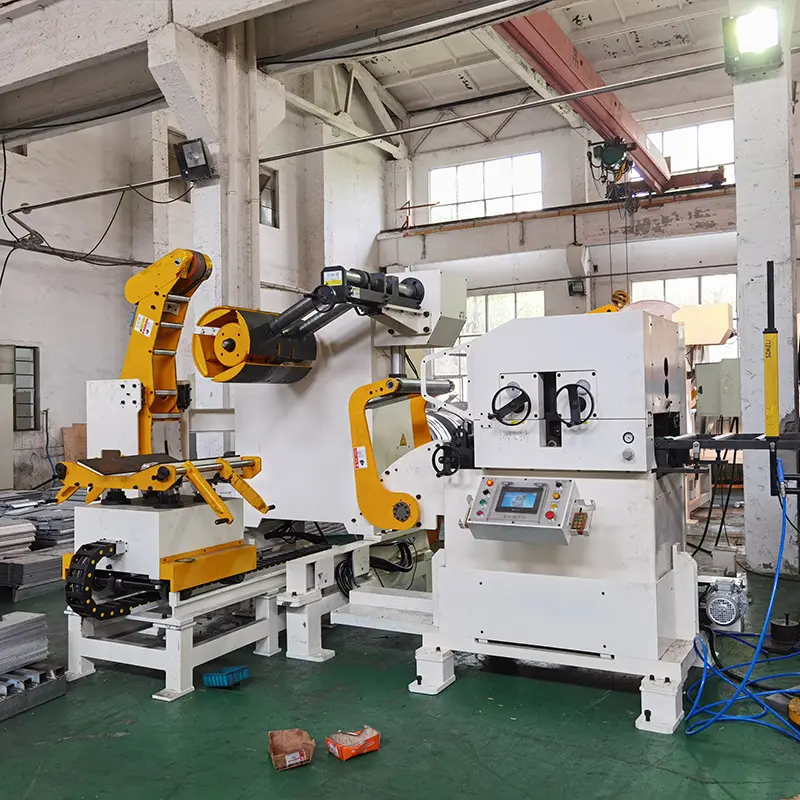
Main Components of trapezoidal sheet roll forming machine
Table 1: Key Components of a Trapezoidal Sheet Roll Line
Component | Description | Purpose |
---|---|---|
Coil holding rack | Mounts raw material coils | Supports strip coils |
ডিকয়লার | Feeds stock into system | Unwinds coils |
Feed table | Pre-forming strip guidance | Provides stability |
Forming stands | House profile shaping rolls | Incremental bending |
Cutting unit | Cuts sheets from strip | Chops sheets to length |
Stack table | Gathers production | Collects sheets |
- Coil rack: Holds inventory reserve material
- Decoiler: Pays off coil stock into the roll former
- Feed table: Pre-forming material stability
- Forming stands: Progressively bend strip
- Cutter: Separates continuous output
- Stack table: Gathers production
Profile Options for Trapezoidal Sheets
Table 2: Typical Trapezoidal Sheet Shapes Produced by Roll Formers
Profile | Description | Characteristics |
---|---|---|
Plain trapezoidal | Flat angled flutes | Material saving structure |
Double trapezoidal | Two rows of bends | Enhanced load capacity |
Perforated trapezoidal | Punched flute holes | Heat exhaust ventilation |
Trapezoidal with edge curls | Rolled border edges | Safety, weatherproofing |
Embossed trapezoidal | Textured surface | Anti-slip, aesthetics |
- Plain: Simple symmetrical flutes
- Double: Dual trapezium channels
- Perforated: Venting and airflow
- Curled edges: Water drainage, no sharp corners
- Embossed: Decorative textures
Choosing suitable shapes optimizes functionality.
Technical Specifications
Key technical parameters for custom trapezoidal sheet roll lines are:
Table 3: Typical Specifications for Trapezoidal Roll Lines
Parameter | Range | Unit |
---|---|---|
Line speed | 15 – 50 | m/min |
Forming stands | 10 – 25 | Nos. |
Material thickness | 0.45 – 1.2 | mm |
Sheet width | 600 – 1500 | mm |
Installed load | 20 – 75 | kW |
- Speed: Production rate capability
- Stands: Number of profile shaping stations
- Thickness: Raw material coil gauge
- Sheet width: Maximum forming range
- Power needs: Electricity supply
The ideal specification combination depends on performance targets, space constraints, and budget.
Material Feed Options
Common material inputs for trapezoidal sheet roll forming:
Table 4: Strip Stock Feeding Methods into Roll Lines
Method | Description | Suitability |
---|---|---|
Automatic coil carousel | Rotates multiple coils sequentially | High-volume, unmanned production |
Joining | Butt-welds tail of exhausted coil to new head | Lower-volume, continuous run |
Manual loading | Operator replaces empty coils | Prototyping, start-up volumes |
- Carousel: Allows automatic sequential coil changeovers
- Joining: Provides continuous welding of coil ends
- Manual: Operator replaces empty coils
Higher automation levels minimize downtimes for coil replenishment.
-
Highway Guardrail End Terminal Forming Machine
-
Highway U/C Post Roll Forming Machine
-
2 Waves Highway Guardrail Roll Forming Machine
-
3 Waves Highway Guardrail Roll Forming Machine
-
দ্রাক্ষাক্ষেত্র পোস্ট রোল ফর্মিং মেশিন
-
স্বয়ংক্রিয় আকার পরিবর্তনযোগ্য সিগমা Purlin রোল ফর্মিং মেশিন
-
দুই তরঙ্গ হাইওয়ে গার্ডেল মেশিন
-
থ্রি ওয়েভ হাইওয়ে গার্ডেল মেশিন
-
পিভি মাউন্টিং বন্ধনী সি শেপ প্রোফাইল রোল ফর্মিং মেশিন
Post-Forming Secondary Processes
Common additional operations after roll forming trapezoidal sheets:
Table 5: Typical Post-Forming Operations
Process | Method | Purpose |
---|---|---|
Cutting | Flying shear | Chops sheets from continuous strip |
Hole punching | Hole punch press | Ventilation gaps |
Embossing | Inkjet, laser | Sheet numbering |
Stack handling | Mechanical arms | Organize sheets before transport |
Packaging | Wrapping machine | Makes bundles |
- Cutting: Separates sheets from continuous strip
- Punching: Addgaps for heat exhaust
- Embossing: Identification and traceability
- Stack handling: Systematic palletizing
- Packaging: Prepare parts for shipping
Efficient post-processing avoids output bottlenecks after forming.
Global Manufacturers
Table 6: Leading International Trapezoidal Sheet Roll Former Manufacturers
প্রতিষ্ঠান | Headquarters | যোগাযোগ |
---|---|---|
Gasparini | ইতালি | [email protected] |
FD Machinery | USA | [email protected] |
Sigma | Turkey | [email protected] |
LT Metal | China | [email protected] |
Joung Jin | South Korea | [email protected] |
- Gasparini: Robust European-built production lines
- FD Machinery: Reliable USA-made roll forming equipment
- Sigma: High-quality Turkish manufacturing
- LT Metals: Cost-effective Chinese fabricators
- JoungJin: Competitively priced Korean company
These companies offer complete trapezoidal sheet production solutions.
Indicative Pricing
Table 7: Typical Price Ranges for Trapezoidal Sheet Roll Lines
Production speed | Price range |
---|---|
15 – 25 m/min | $45,000 – $98,000 |
25 – 40 m/min | $98,000 – $210,000 |
40 – 55 m/min | $210,000 – $315,000 |
Influencing cost factors:
- Desired output rate and automation level
- Type and number of ancillary modules
- Degree of customization
- Overall line length based on part sizes
- Manufacturer’s brand value
- Taxes and shipment costs
Higher flexibility lines enable rapid product changes but cost more initially. Starting smaller and incrementally scaling production keeps initial capex lower.
Installation and Commissioning
Key tasks in installing trapezoidal sheet roll forming lines:
Table 8: Roll Line Installation Activities
Task | বিস্তারিত | Purpose |
---|---|---|
Site preparation | Floor flatness, access routes | Stable foundation |
Positioning | Machine clearances | Smooth material flow |
Anchoring | Anchor to floor | Prevent vibrational drifts |
Alignment | Level forming sections | Decentered rolls distort strips |
Connection | Electrical, hydraulic, pneumatic systems | Actuate motors, cylinders |
Safety | Guarding, emergency switches | Operator protection |
Testing | Validate performance | Reduce debug losses |
Careful installation enhances equipment lifetime and prevents defects from component misalignment. Thorough testing during commissioning decreases faults occurring later during production.
Maintenance Activities
Proactive maintenance of trapezoidal sheet roll forming lines involves:
Table 9: Recommended Maintenance Schedule
Frequency | Task | Purpose |
---|---|---|
Daily | Fluid level checks | Prevent unplanned outages |
Weekly | Sensor recalibration | Ensure correct strip tracking |
Monthly | Lubricate moving parts | Reduce wear and friction |
Quarterly | Re-alignment if needed | Re-orient forming sections |
Annually | Oil changes for gearboxes | Extend mechanical lifetime |
As-needed | Worn component replacement | Restore normal function |
- Inspections: Early detection of issues
- Recalibration: Maintain output accuracy
- Lubrication: Smooth low-friction operation
- Re-alignments: Correct directionality
- Fluid changes: Keep oil contaminant-free
- Part replacement: Fix faulty components
Scheduled preventive servicing minimizes unplanned stoppages and quality defects.
Supplier Selection Parameters
Key parameters for evaluating trapezoidal sheet roll former manufacturers are:
Table 10: Comparison Criteria for Roll Forming Equipment Suppliers
Factor | Description |
---|---|
অভিজ্ঞতা | Successfully built reference plants |
Quality | Robust fabrication from branded components |
কাস্টমাইজেশন | Offer needed specification range |
Design support | Help optimize forming process |
Responsiveness | Quick issue resolution during production |
Delivery | On-time equipment availability |
Cost | Reasonable pricing fitting budget |
- Experience: Domain expertise benefits design
- Quality: Reliable and durable equipment
- Customization: Meeting project targets
- Design support: Process optimization
- Responsiveness: Support during production
- Delivery: Prevent delays
- Cost: Agreeable pricing and payment terms
Assessing OEMs on these aspects minimizes project execution risks.
Advantages of trapezoidal sheet roll forming machine
Table 11: Benefits and Limitations of Roll Forming Trapezoidal Sheets
Pros | Cons |
---|---|
High production speeds | Significant initial capital cost |
Continuous single-step forming | Multiple debugging iterations initially |
Precision quality with tight tolerances | Maximum sheet widths restricted by coil stock |
Lower operating costs via automation | Production halts for die changeovers |
On-demand buffered supply | Require peripheral equipment |
Compact equipment footprint | Skilled workforce required |
Key Benefits:
- Fast low-cost production
- Parameter controlled repeatable quality
- Lower long term overheads through automation
- Minimal inventories with Just-in-time supply
- Retrofittable capacity upgrading extensions
Major Limitations:
- High initial capex investment
- Multiple iterations needed stabilizing new profiles
- Sheet widths constrained by raw coil dimensions
- Downtime during die changeover for profile switches
- Dependence on extra ancillary modules like recoilers, stackers etc.
- Specialized skill needed for programming and maintenance
Weighing pros and cons allows equitable assessment for production needs.
End Use Sectors
Table 12: Major Application Areas for Roll Formed Trapezoidal Sheets
Sector | আবেদন | Example Uses |
---|---|---|
Construction | Wall cladding, roofs | Metal buildings, shelters |
Infrastructure | Large span structures | Airport hangers, metro stations |
Storage | Warehouses, barns | Storage buildings, agricultural shelters |
Utilities | Power and desal plants | Panel cladding, water tanks |
Transport | Bus stands, container buildings | Passenger shelters, freight storage |
- Construction: External weatherproof building envelopes
- Infrastructure: Outer metal cladding for vast span buildings
- Storage: Pre-engineered agricultural sheds, barns etc.
- Utilities: Sturdy exterior paneling applications
- Transport: Bus stop enclosures, container storage shelters
The combination of strength, corrosion resistance, and formability makes trapezoidal sheets suitable for roofing and cladding structures across sectors.
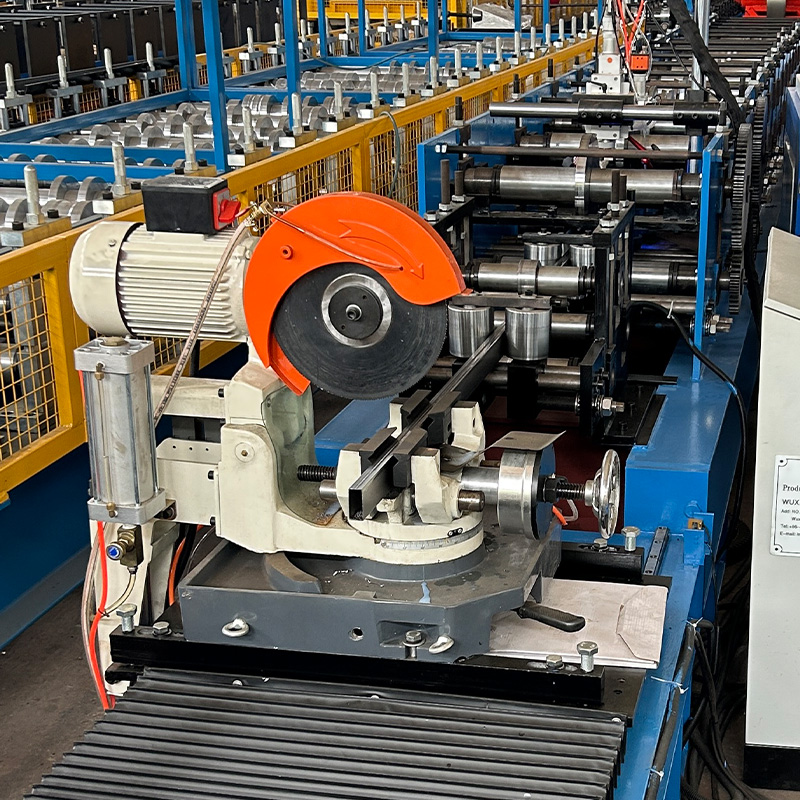
Frequently Asked Questions
Q: What type of steel is generally roll formed into trapezoidal sheets?
A: Prepainted galvanized steel and aluminum coils are commonly used to produce weatherproof trapezoidal sheets.
Q: What thickness of trapezoidal sheets provides optimal strength?
A: Sheet thicknesses between 0.5 mm to 0.7 mm offer adequate bending strength and load bearing capacity for most building structures.
Q: What is the benefit of punched perforations in trapezoidal sheets?
A: Flute perforations allow uniform ventilation and exhaust heat buildup especially for industrial warehouse roofs and metal barn cladding.
Q: How are trapezoidal sheets joined together on site?
A: Self-drilling fasteners through overlapping sidelaps or structural bolts along the central panel flats are used to connect adjacent trapezoidal sheets.
Q: Can custom patterns be incorporated on trapezoidal sheet surfaces?
A: Yes. Custom male-female roller dies can create personalized surface relief effects like wood grain, leather etc. textures inline during roll forming.
উপসংহার
OEM roll forming lines enable high volume mass production of various trapezoidal structural sheet profiles. With comprehensive planning guided by this reference spanning relevant aspects, manufacturers can gain strategic and economic benefits from adopting in-house trapezoidal sheet production. Their combination of efficiency, versatility, and customizability make these machines ideal for metal building product fabricators.