Silo roll forming machines produce round metal grain, aggregate and pellet containment vessels supporting agricultural bulk storage and processing sites. This guide provides farmers, contractors and manufacturers detailed specifications, configurations, comparisons and considerations when investing in these specialized heavy-duty automated roll forming system solutions.
Introduction to silo roll forming machine
Roll formed silos provide unique advantages versus alternatives:
- On-demand field manufacturing agility unconstrained by road transportation
- Inline fabrication reduces secondary site assembly welding labor
- Lower equipment investment than fixed regional plants
- Versatile forming capability for variety of diameters and slants
- Integral structural corrugations add hoop strength
This guide covers key factors evaluating roll forming lines producing silos:
- Working Principle and Process Overview
- Type Comparison – Mobile vs Fixed Mill Machines
- Material, Color and Gauge Capability Ranges
- Forming Speed, Accuracy and Dimensional Adjustability
- Profiles – Corrugations, Flanges, Conical Ends
- Supplier Price Bands and Configurations
- Installation Requirements and Site Planning
- Operation, Changeovers and Preventative Maintenance
- Pros vs Cons: Roll Formed vs Site Assembled Silos
- FAQs on Grain Storage Standards
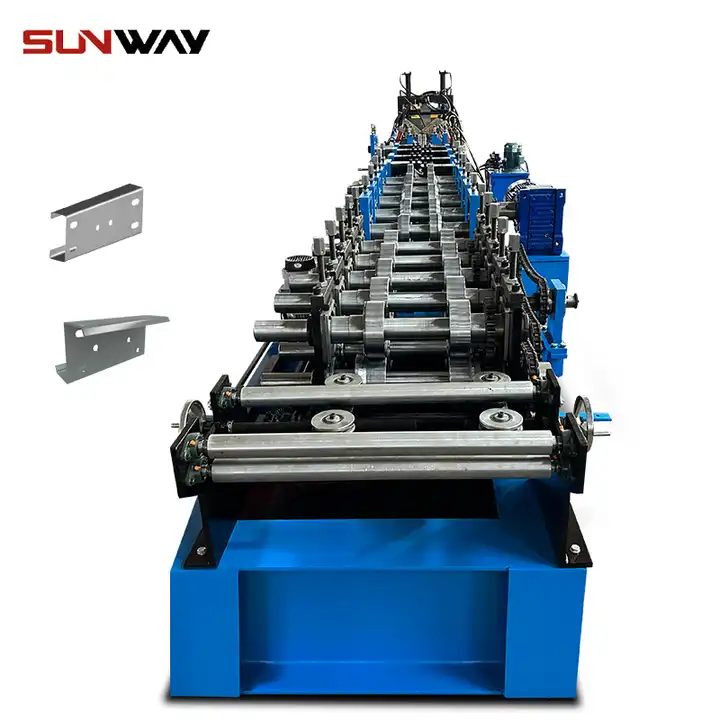
Working Principle of silo roll forming machine
Roll forming transforms steel coil continuously through a progression of bending rollers andforming dies into rounded interlocking vessels when the leading sheet end welds to the trailing end.
Table 1 depicts the typical standalone process steps in sequence:
# | Station | Purpose |
---|---|---|
1 | Decoiling | Sheet loaded onto powered unwind reel |
2 | Feeding | Sheet threaded into initial roller dies |
3 | Rounding | Radial rolls gradually shape flat sheet into concentric curving hoops |
4 | Profiling | Structural corrugations profiled along length |
5 | Conical Reducing | Ends tapered to closures |
6 | Welding | Automatically fuses trailing/leading edges |
7 | Evacuating | Exits fully formed for ring lifting |
Computerized controls manage piece dimensions, roller die positions, weld heat input and ram pressure synchronization to produce each custom silo within strict tolerances.
Iterative simulation combined with small scale prototyping refines limited run parameters for responsibly shaping specialty vessels previously restricted through manual steel fabrication.
Comparing Mobile vs Fixed Silo Machines
Grain silos suit repetitive dedicated regional plants amortizing costs over annual volume production orders. However portable lines offer contractors and farmers logistics agility quick to deploy near seasonal storage sites.
Table 2 compares capabilities:
Mobile Trailer System | Fixed Factory System | |
---|---|---|
Location Flexibility | Position near field sites | Permanent builds limit destinations |
Section Length | Up to 60 foot single pieces | 100 foot + requiring splicing |
Section Range | Common diameters standardized | Greater variety possible |
Rate | 10 – 25 feet per minute | 25 – 45+ feet per minute |
Accuracy | +/- 1mm over 30 feet | +/- 0.5mm over 100 feet |
Computerization | Manual set up | Fully automated SCADA |
Evaluate tradeoffs like delivery, precision, changeover ease and site variables. Component modularity suits frequent relocation so starter lines later upgrade retaining primary roll units.
Material, Color and Gauge Capability Ranges
Grain silos require metals that withstand weather alongside internal load pressures from large volumes of aggregate.
Table 3 Shows typical grades and thicknesses shaped:
Material | Common Gauges |
---|---|
Hot Rolled Steel | 2.5 – 4 mm plate |
Cold Rolled Steel | 1.5 – 2 mm plate |
Stainless Steel | 0.8 – 1.5 mm sheet |
Aluminum | 2 – 4 mm sheet |
Steel grades SS400 or S250GD galvanized typical based on regional availability, cost and rust prevention lifecycle objectives.
Machines normally form thinner gauges up through 6 mm steel plate with increasing gear ratios and cylinder ram force tonnage for heavier walls spreading tooling stress over additional roller dies.
Larger silo diameters targeting greater volume capacity require thicker metals resisting hoop stresses. Carefully select targeted material specifications balancing rated bushel capacity, hardware compatibility, weather sealing properties and budget.
Forming Speed, Precision and Dimensional Configurability
Depending on selected diameter complexity silos roll form between 10 – 25 feet per minute with relationships between accuracy and rate.
Table 4 indicates normal expectation ranges:
Low Volume Machine | High Speed Machine | |
---|---|---|
Speed | 10 – 15 ft/min | 20 – 30+ ft/min |
Tolerance | +/- 2 mm | +/- 1 mm |
Stands | 10 – 12 stands | 15 – 22 stands |
Diameter Range | 2 size Quick change sets | 10+ size modular tooling |
Reputable heavy duty platforms with reinforced roller box frames evenly spread 400+ kN of uncoiling force as metal sheet incrementally forms into rounded vessels.
Design flexibility includes various symmetrical corrugation patterns and conical slope angles changeable with quick new die sets. Carefully quantify dimensional expectations when researching purchase options to prevent unrealistic capability assumptions that hamper ROI.
Structural Profiles: Corrugations, Flanges, Conical Ends
Standard silo body requires reinforcing rings and tapered grain flow endings made through forming process enhancements:
Table 5
Profile | Purpose |
---|---|
Corrugations | Hoop strength prevents bulge swell failure |
Flanges | Mating hardware compatibility |
Conical Reducer | Slope promotes gravity extraction |
Decorative Branding | Logo embossing |
Serial Codes | Traceability stamping |
Assess specialized requirements during upfront design stages best planned before ordering equipment. Attempt integrating features that maximize productivity efficiency over relying upon secondary manual fabrication later.
Supplier Price Bands and Model Evaluation
Reputable silo roll former manufacturers offer specially engineered lines with major upfront capital costs that demand long term planning.
Table 6 indicates general price ranges:
Line Configuration | Price Range |
---|---|
Basic Manual Mobile Trailer | $125,000 – $250,000 |
Automated Mobile Trailer | $250,000 – $400,000 |
Permanent Fixed Factory Mill | $400,000 – $1,500,000 |
Pricing depends heavily on degree of automation, cylindrical dimension accuracy grades designed into lasting machines plus quick change modular tooling libraries suited for producing recognized variety over operational decades servicing agricultural commodity verticals. Significant regional cost differences exist between domestic and imported sources.
Carefully project long term business growth models when evaluating capitol outlay seeking balance between startup cash constraints versus sustaining consistent responsiveness as cyclical seasonal order ebbs and flows unpredictably shift every year.
Installation Planning Requirements
Specialized silo roll forming machinery requires extensive planning to position multi-ton production lines without foundation damage during delivery.
Table 7 overviews site considerations:
Factor | Details Checklist |
---|---|
Space/Access | Survey transport route access, turn radiuses, bridge/overpass clearances ensuring no obstruction |
Foundation | Level bed of packed crushed stone covering buried electrical & plumbing utilities |
পাওয়ার সাপ্লাই | Available transformers & distribution disconnects suiting drive load profiles |
Network Comms | Cellular data links |
Compressed Air | Utility air drier if control actuators require |
Safety Controls | Implement perimeter excluding untrained operators from rigging activities |
Logistics | Coordinate truck unloading delivery using ground guidance personnel |
Careful planning combined with effective site communication prevents delays introducing such capital equipment.
Operations, Training and Preventative Upkeep
Silo roll forming machinery relies upon orchestrated engagement between automated manufacturing sequences guided through properly calibrated instrumentation synchronizing hundred of actuations along entire process flow.
Staff roles include:
- Conductor – Directs recipe production schedules while positioning worker skillsets to smoothly execute planned job sequence changeovers between machine A and B activity batches to output pieces without injury or quality violations through oversight.
- Operators – Carefully stage heavy mill coil stock using flatbeds and boom cranes while monitoring sheet tracking through subsequent forming stations. Continually reviews vessel roundness, assessing diameters visually down the length.
- Quality technician – Validates finished geometries like flange hole patterns, corrugation forms/frequency against engineering drawings using hand calipers further supported with laser scanning automated reporting.
- Maintenance lead – Sustains equipment integrity through both routine preventative servicing based on run time thresholds and break-fix diagnostics troubleshooting functional failures down to root causes for correction by trades personnel.
- Electrical lead – Masters software, sensors and data analytics including PLC code improvements beyond generic factory settings by tuning servo gains and motion profile synchronization logic.
- Tooling specialist – Metrologist able to quantify roll stand parallelism, press ram force consistency and calibrate inline sensors providing mechanical support adjusting roller boxes during accelerated maintenance or new die changeover reducing downtimes.
Carefully plan staffing competency models across these interdisciplinary roles seeking combination of internally upskilled trades working together with niche external partners able to setup initial configurations further optimizing output as incremental enhancements qualify over years. Recognize the long runway reaching rated capability maturity over multiple seasons necessitating unwavering commitment through valleys despite amplified peaks. Patience pays compounding dividends over enough turns of the flywheel.
Pros vs Cons: Roll Formed vs Assembled Silos
Roll formed silos provide unique advantages but also limitations over manual alternatives:
Table 8
Parameter | Roll Formed | Assembled |
---|---|---|
Speed | Rapid install after forming | Slower site fabrication |
Efficiency | Automated process done in days | Highly labor intensive over weeks |
Accuracy | Superior diameter precision reliability | Risk of uneven weld alignment |
Strength | Full thickness walls entire length | Individual welded sheet butt joints |
Investment | Major equipment cost | Lower – uses existing site tools |
Other considerations:
- Automated factories achieve lengths impossible to handle hoisting manually limiting scale
- Controls ensure precise repeatability preventing rework variability signed off silo-to-silo
- Capital equipment enables volume responsiveness against reliance upon specialist availability
When engineered to rigorous standards, automated machines produce unsurpassed quality otherwise unattainable relying solely upon variable workmanship vulnerable to defects without guardrails. Pragmatic evaluation between capability delivery against resource constraints helps discover the ideal investment balance point delineating engagement strategies across the two approaches.
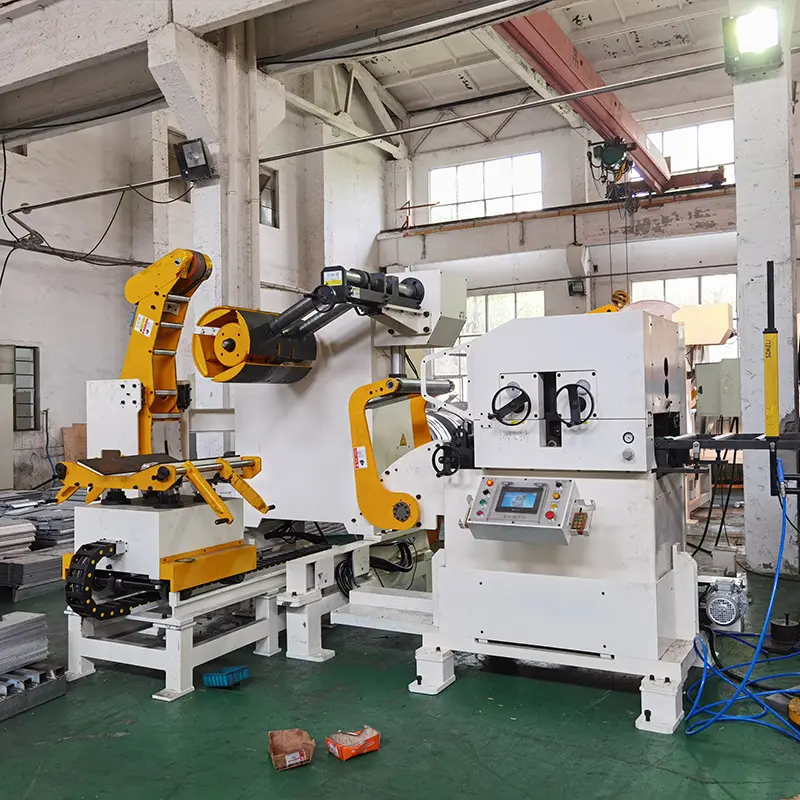
FAQs
Table 9 – Common Buyer Questions
FAQ | Answer |
---|---|
What warranty expectancy comes with silos? | 5-20 years depending on material grade selected |
Should I request design qualification data? | Yes further risk reduction by reviewing engineering stress simulations prior to procurement |
How are interlocking joints tested for air sealing? | Smoke visualization combined with laser scanning to quantify smoke escaping through shell |
What specialty equipment aids installation? | Laser projection guidance matched to 3D CAD models provide verticality and plumbness references as sheets get welded |
Is expert maintenance advise available long term? | Yes manufacturers offer ongoing support partnership services ensuring sustained safety |
Table 10 – Additional Silo Standards
FAQ | Answer |
---|---|
What natural disaster load safety factors should I consider? | Wind, seismic, snow and flood levels are defined per geography through IBC/ASCE 7 analysis |
How frequently should I audit my bins? | Annual inspection recommended checking fastener torque, steel swelling and foundation settling over time |
Is rodent damage prevention available? | Yes sealed pathway exclusion combined with chemical perimeter control options exist |
What specialty design options are popular? | Increased flow hopper angles, dust mitigation platforms, safety fall arrest rings and portable ladders integrated |
Can automated grain level sensors be incorporated? | Yes with IoT cloud connectivity capability now increasingly adopted |