Roll forming is a metalworking process used to form sheet metal into customized profiles using a series of consecutive rolling stands. It allows continuous production of variable cross-section parts at a high rate. Channel roll forming machines are designed specifically to form channel sections, which have a C-shaped cross-section.
How Channel Roll Forming Works
A channel roll forming machine forms channel sections by passing sheet metal strip through a series of rolling stands. Each stand incrementally forms the sheet into the desired C-shaped channel profile.
The process starts by feeding a flat strip of sheet metal into the roll former. The strip passes through a straightening mechanism to remove any coil curvature. It then enters the forming stands, each of which make small bends until the final shape is achieved.
The key components of a channel roll forming machine include:
- Uncoiler: Feeds the sheet metal coil strip into the machine
- Feed table: Supports and guides the strip through the process
- Forming stands: Bend and form the strip progressively into channel sections
- Cut-off press: Cuts finished channels to length
The forming stands utilize hardened steel rolls engraved with the desired profile. The top and bottom rolls spin to grip and bend the strip as it passes through. Each stand makes a small incremental bend, typically 5-15 degrees.
By the time the strip exits the last stand, it has been bent into the final C-shaped channel form. The channels then move to the cutoff press to be cut to the required length. They are offloaded for further processing or direct use.
Benefits of Roll Formed Channels
Channel roll forming provides many benefits compared to other metal forming processes:
- High productivity: Channels can be mass-produced at fast linear speeds up to 100m/min
- Flexibility: Profiles can be changed by adjusting or replacing the rolls
- Accuracy: Channels have precise dimensions along the entire length
- Quality: Consistent profiles and smooth surface finishes are achieved
- Low cost: Efficient production results in cost savings compared to other methods
- Material savings: Less scrap is produced compared to stamping or fabricating
- Strength: Work hardening during forming improves strength
These advantages make roll formed channels ideal for high volume production. The channels can be used directly or incorporated into various structures and assemblies.
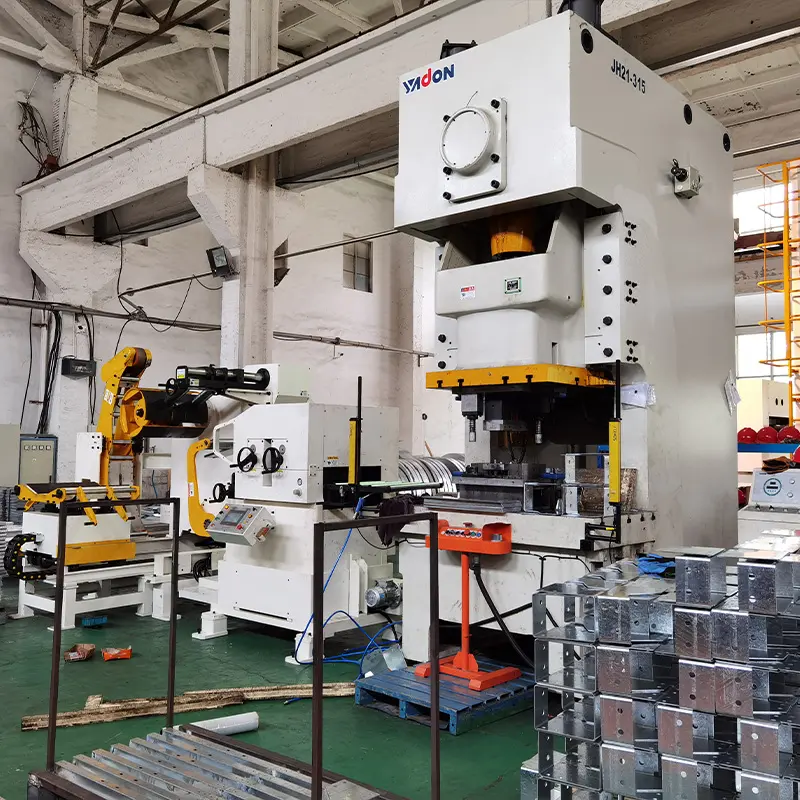
Channel Roll Forming Machine Components
Channel roll forming lines incorporate a range of components and subsystems. These include:
Uncoiling Equipment
The sheet metal strip is supplied in large coils weighing several tons. Uncoiling equipment such as a de-coiler or reel is used to unwind the coil and feed the strip into the roll former. Features such as powerized uncoiling, coil car, and coil handling cranes automate the process.
Feed Table
This is a flat table structure that supports the strip as it enters the roll former. It centers the strip and guides it in a straight path into the forming stands. The feed table may have powerized or automated feeding features.
Forming Stands
The heart of the machine. Typically 10-16 forming stands bend the strip incrementally to form the channel profile. Each stand consists of:
- Top and bottom rolls engraved with the outline profile
- Housings supporting the roll shafts
- Roll adjustment mechanisms
- Roll drive motors and transmission
Quick change forming stations allow rapid profile changes. The stands are often modular for flexibility.
Shearing Station
A powered shearing machine cuts the finished channels to length as they exit the last forming stand. The shear capacity must match the channel size and material thickness.
Transfer Tables
Roller conveyors transfer the channel segments from the shear to offline processes such as deburring, marking, packing, or fabrication stations.
নিয়ন্ত্রণ ব্যবস্থা
PLC-based controls coordinate the roll forming sequence. They control functions like strip feed speed, roll RPMs, shear operation, and transfer tables.
Safety Equipment
Safety guards, fences, emergency stops, and other devices protect workers according to machinery safety standards.
Roll Former Configurations
Channel roll forming machines are available in different configurations:
Horizontal Roll Forming
The strip passes horizontally through the stands. Easy to operate and suitable for low-medium production rates.
Vertical Roll Forming
The strip travels vertically upwards through the stands. Allows high production rates but the strips require support against gravity.
Curved Roll Forming
The stands are arranged in a curved C-shape. Permits high speeds and avoids strip buckling. Needs additional floor space.
Rotary or Spinning Head Roll Forming
The strip passes around a rotating head with spiral forming passes. Compact arrangement but lower speeds than inline machines.
The optimal roll former layout depends on the channels sizes, production rates, and space requirements.
Roll Forming Process Design
Proper process design is crucial for producing quality roll formed channels:
- Channel profile design using CAD
- Developing the sequential bending plan
- Roll pass schedule optimization
- Roll pass design – profile, contours, match lines
- Virtual simulation using FEA
- Prototype validation on roll forming machine
- Finalizing the roll pass design
Experienced roll forming engineers are needed to convert a channel shape into a robust production process. Virtual prototyping using CAD and FEA reduces the development time and cost.
Roll Forming Tooling
The tooling consists of the rolls which actually form the channel profile. Key tooling design factors are:
Roll Materials
- Hot rolled or cold rolled steel rolls with hardness 58-62 HRC
- Adamite for extended roll life
- Iron or steel sleeves shrunk fit over steel cores
Roll Manufacturing
- CNC machining of rolls with profile engraving
- Surface treatments like nitriding to increase hardness
Roll Geometry
- Profile matching between top and bottom rolls
- Contour design to avoid ripples
- Radii, fillets, and smoothening
Splines and Drives
- Splined shafts transmit torque from gearbox to rolls
- Drive pins allow longitudinal roll adjustment
Experienced tooling engineers optimize the roll geometry for quality channels and long production runs.
Setting Up a Roll Forming Line
When installing a channel roll forming system:
- Anchor the machine securely to the floor
- Level all the stands and components
- String align the forming stands in the machine direction
- Install the electrical cabinets, wiring, and controls
- Add any safety guarding devices
- Test run to confirm smooth operation
Setup must be very precise for proper strip tracking and alignment through the roller stands. Field service from the machine manufacturer is advisable.
Roll Forming Process Parameters
Key process parameters include:
- Strip Width: 25mm to 2500mm possible
- Strip Thickness: 0.5 to 8mm thickness range
- Strip Material: Mild steel, stainless steel, aluminum
- Forming Speed: Up to 100m/min based on the profile
- Cut length: 0.5m to 15m (set by the shear)
The machine’s capacity limits should match the required channel specifications.
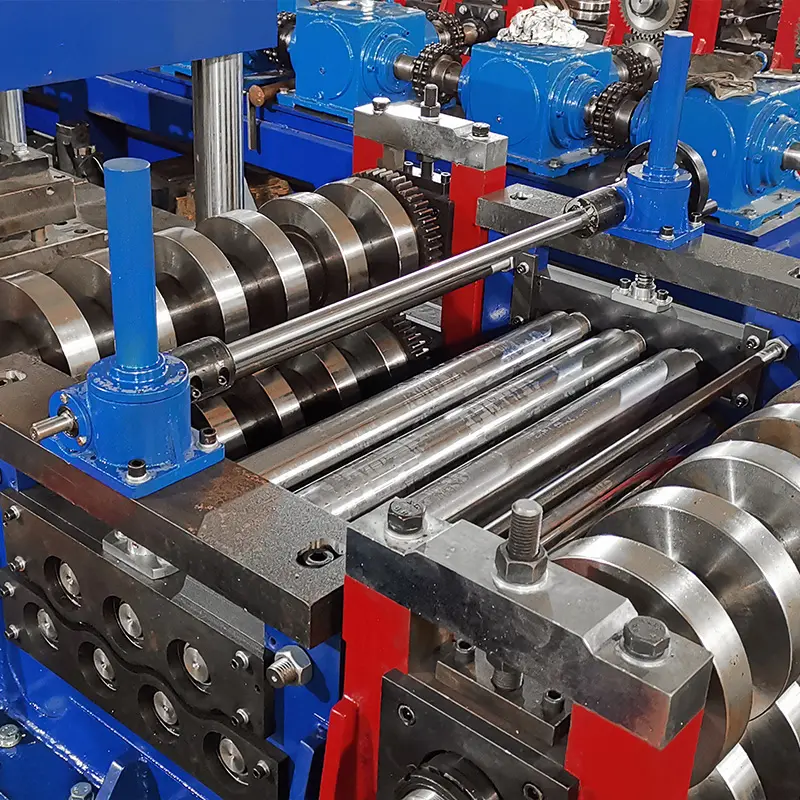
Channel Profile Design Considerations
The channel geometry impacts formability, quality, and tooling. Factors to consider:
- Channel depth vs width: Deep, narrow channels are more difficult to roll
- Inside radius: A larger radius is easier to form
- Wall angles: Gradual bends spread over more stands
- Web flatness: A convex web helps avoid deflections
- Flanges: Wide flanges may need support rolls
- Symmetry: Similar top and bottom profiles are ideal
Avoid thick walls and tight curves. FEA simulation validates the profile design.
Metals Suitable for Roll Forming
The most commonly roll formed metals include:
- Mild steel: Low carbon steel with good formability. Most economical.
- High strength steel: Stronger but harder to form. May need more forming passes.
- Stainless steel: More expensive but has high corrosion resistance. Needs high precision tooling.
- Aluminum: Lightweight and corrosion resistant but tricky to form without cracking.
Pre-painted steel and galvanized steel coatings are also possible.
Secondary Operations
Common secondary processes after roll forming include:
- Cutting: Shearing the channels to specified lengths
- Hole punching: Punching holes for connections
- Hardware insertion: Attaching clips, brackets, connectors
- Packaging: Banding, stacking, wrapping for transportation
- Additional fabrication: Joining, welding, mechanically fastening
Automated parts handling can integrate secondary processes for high productivity.
Channel Roll Forming Applications
Common applications of roll formed channel sections include:
- Building construction: Framing studs, window sections, cladding, purlins, girts
- Rooftop structures: Standing seam roofs, canopies, walkways, solar panel frames
- Shelving and racking: Supermarket shelving, industrial racks, storage systems
- Furniture: Chairs, desks, display units
- Automotive: Roof rails, rocker panels, running boards, truck bed liners
- Appliances: Washing machine drums, refrigerator liners
- Shipping containers: Side and roof panels, doors
- Electrical: Bus bars, cable trays, junction boxes
Roll formed channels provide excellent functional performance combined with efficiency and economy.
Roll Forming Advantages Over Other Methods
Compared to other metal forming methods, roll forming provides:
- Lower cost vs stamping or fabricating
- High productivity with linear continuous processing
- Material savings due to flat sheet input
- Flexibility from quick roll change tooling
- Strength from cold working
- Good accuracy along full length
- Quality surfaces free of warp or distortion
- Ideal for long parts like building framing
- Quiet operation suitable for office areas
These benefits make roll forming the process of choice for producing channels, studs, roofing profiles, and other high volume components.
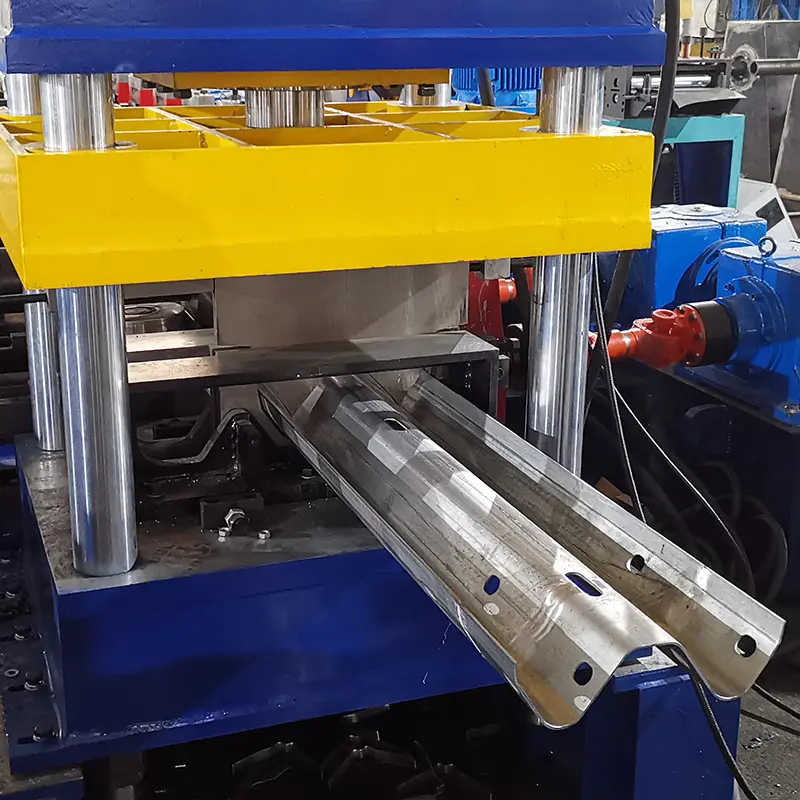
FAQ
What materials can be roll formed into channels?
- Most common are low carbon steel, high strength steel, stainless steel. Aluminum is also possible but challenging. Finished metals like galvanized, pre-painted, and weathering steel can also be roll formed.
What thickness range can be roll formed?
0.5mm to about 8mm can be formed. Thinner material may springback excessively. Thicker requires more roll forming passes.
How long can a roll formed channel be?
Up to 15m lengths are possible. Only limited by the material coil size and handling capabilities.
How many different profiles can a machine make?
With quick change tooling, 100s of different profiles are possible on one machine. Roll changeover takes 1-2 hours.
What tolerances can be held on a channel?
Roll forming can achieve tolerances around +/- 0.5mm. Precision requires well aligned tooling and process control.
How fast is the production rate?
Up to 100m/min is possible depending on the profile complexity. Typical production rates are 10-40m/min.
How quickly can roll tooling be changed over?
With quick change style tooling, profile changeover takes 1-2 hours. Fixed tooling changeover takes longer.
What expertise is needed for roll tooling design?
Experienced roll tooling engineers are required for quality profile development, simulation, and prototyping.
How should channels be designed for ease of roll forming?
Avoid thick walls, tight radii and highly asymmetric shapes. Convex webs and large radii also help.
What safety equipment should be used on roll formers?
Full machine guarding, emergency stops, lockouts, and PPE like hearing protection and safety glasses.
উপসংহার
Channel roll forming provides an economical way to mass produce C-shaped channel sections with accuracy and repeatability. With capabilities to form diverse profiles from thin to thick material, channel roll forming machines are the ideal equipment for construction, building, automotive, and general manufacturing.