ভূমিকা
Roofing is a crucial aspect of any construction project, whether it’s residential, commercial, or industrial. In recent years, the roofing industry has witnessed significant advancements in technology, leading to increased efficiency and quality of roofing materials. One such innovation is the Ameco Roofing Roll Forming Machine, a cutting-edge solution that has revolutionized the roofing manufacturing process.
একটি ছাদ রোল ফর্মিং মেশিন কি?
Before we delve into the benefits and features of the Ameco Roofing Roll Forming Machine, let’s understand what it is and how it works. A roofing roll forming machine is an automated equipment used to fabricate metal roofing panels and profiles in continuous lengths. The process involves feeding a metal coil through multiple rollers that gradually shape the material into the desired roofing profile.
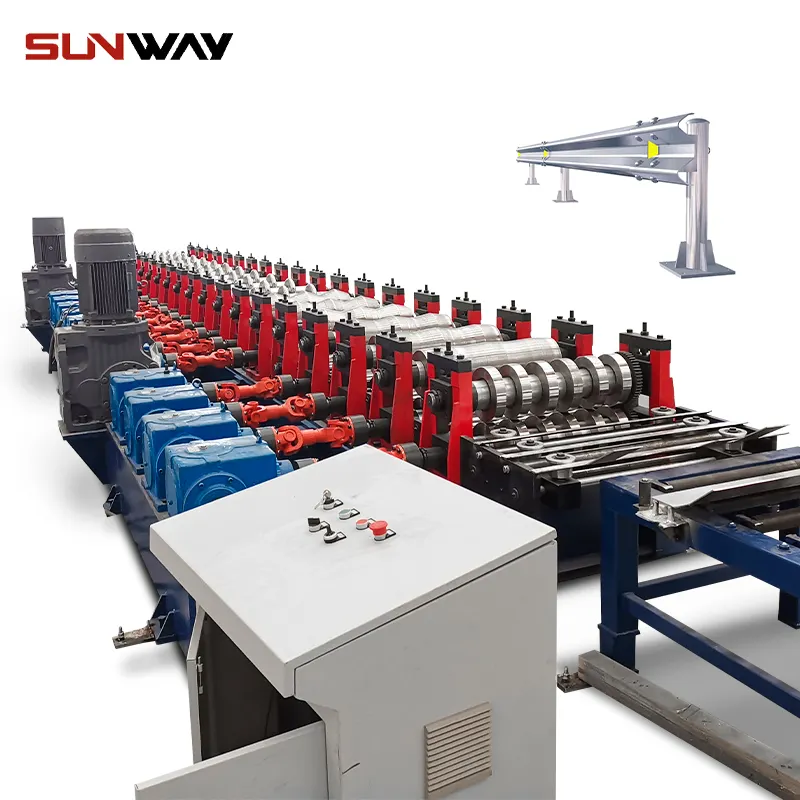
Advantages of Using Ameco Roofing Roll Forming Machine
Increased Efficiency
The Ameco Roofing Roll Forming Machine significantly enhances the productivity of roofing manufacturers. By automating the roll forming process, it eliminates the need for manual labor, reducing production time and costs. This increased efficiency allows manufacturers to meet tight deadlines and fulfill large orders with ease.
Consistent Quality
Achieving uniformity in roofing profiles is essential for a successful roofing project. The Ameco Roofing Roll Forming Machine ensures consistent quality in each panel it produces, minimizing variations and defects. This consistency translates into durable and reliable roofing materials that can withstand harsh weather conditions.
Versatility in Roofing Profiles
One of the key advantages of the Ameco Roofing Roll Forming Machine is its versatility. It can produce a wide range of roofing profiles, from traditional corrugated panels to modern standing seam designs. This flexibility allows roofing manufacturers to cater to diverse customer preferences and market demands.
Cost Savings
While the initial investment in the Ameco Roofing Roll Forming Machine may seem significant, it offers long-term cost savings. By streamlining the manufacturing process and reducing material wastage, the machine helps minimize overall production costs, leading to higher profit margins for manufacturers.
Key Features of Ameco Roofing Roll Forming Machine
High-Quality Material
Ameco uses premium-quality materials to manufacture its roofing roll forming machines. Sturdy construction and high-grade components ensure durability and longevity, even in demanding production environments.
User-Friendly Controls
Operating the Ameco Roofing Roll Forming Machine is a breeze, thanks to its user-friendly controls. Intuitive interfaces and easy-to-understand settings enable operators to set up and operate the machine efficiently, reducing the learning curve for new users.
Customizable Options
The machine offers customization options to meet specific roofing requirements. From panel dimensions to color coatings, manufacturers can tailor the output according to their clients’ preferences.
Safety Measures
Safety is paramount in any industrial setting. The Ameco Roofing Roll Forming Machine is equipped with safety features such as emergency stop buttons, safety guards, and sensors to ensure a secure working environment for operators.
How Does the Ameco Roofing Roll Forming Machine Work?
The Ameco Roofing Roll Forming Machine follows a well-defined process to create high-quality roofing panels. The process involves the following steps:
- Material Loading: A metal coil is loaded onto the machine, ready to be fed through the rollers.
- Roll Forming: The metal coil passes through a series of rollers, each designed to shape a specific part of the roofing profile.
- Cutting: After the desired length of the roofing panel is formed, the machine automatically cuts it to size.
- Stacking: The finished panels are neatly stacked for packaging and transportation.
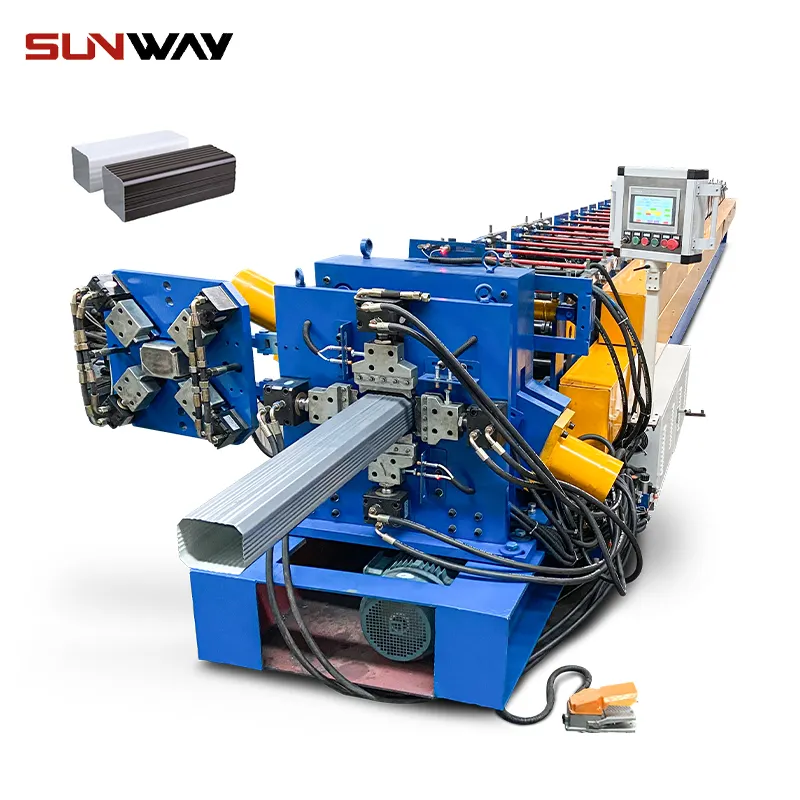
Factors to Consider When Choosing an Ameco Roofing Roll Forming Machine
Selecting the right roofing roll forming machine for your manufacturing facility requires careful consideration of various factors:
Production Capacity
The production capacity of the machine determines how quickly it can manufacture roofing panels. Assess your production requirements and choose a machine that meets your daily output needs.
গঠন গতি
Forming speed influences the rate at which the machine shapes the metal coil. A higher forming speed can boost productivity but might require more advanced controls and maintenance.
Material Compatibility
Ensure that the machine can handle the type and gauge of metal coil you plan to use for your roofing profiles.
Maintenance and Support
Check the maintenance requirements of the machine and inquire about the support provided by the manufacturer for troubleshooting and repairs.
Tips for Operating and Maintaining the Ameco Roofing Roll Forming Machine
Proper operation and maintenance are essential to ensure the longevity and optimal performance of the Ameco Roofing Roll Forming Machine.
Regular Inspection and Cleaning
Perform routine inspections of the machine to identify any signs of wear or damage. Regular cleaning helps prevent debris buildup, which can affect the quality of the roofing panels.
Lubrication of Moving Parts
Lubricate the moving parts as per the manufacturer’s recommendations to minimize friction and extend the life of critical components.
Calibration and Alignment
Regularly calibrate and align the machine to maintain accurate panel dimensions and profiles.
Training and Safety Guidelines
Train operators on the proper operation of the Ameco Roofing Roll Forming Machine and ensure they follow safety guidelines. Provide comprehensive training to operators, covering machine controls, maintenance procedures, and emergency protocols.
Real-Life Applications of Ameco Roofing Roll Forming Machine
Residential Roofing
In the residential construction sector, the Ameco Roofing Roll Forming Machine plays a vital role in producing high-quality roofing panels for various housing projects. From traditional asphalt shingles to modern metal roofs, the machine can fabricate a wide range of roofing profiles to cater to diverse architectural styles.
Commercial Roofing
Commercial buildings often require large-scale roofing installations, and the Ameco Roofing Roll Forming Machine’s efficiency and productivity make it an ideal choice for such projects. Its ability to produce long, continuous roofing panels reduces installation time and labor costs, making it a cost-effective solution for commercial roofing contractors.
Industrial Roofing
Industrial facilities often have unique roofing requirements due to their large spans and specialized needs. The Ameco Roofing Roll Forming Machine’s customization options allow manufacturers to create roofing panels tailored to industrial applications, ensuring optimal performance and durability.
Future Trends in Roofing Roll Forming Technology
As technology continues to advance, the roofing industry can expect several trends in roofing roll forming technology:
- Advanced Material Compatibility: Roofing roll forming machines will be designed to handle a broader range of materials, including innovative composites and sustainable options.
- Smart Automation: Automation will become even more sophisticated, integrating artificial intelligence and machine learning to optimize production processes and reduce human intervention.
- Energy Efficiency: Future machines will focus on energy-efficient operation, minimizing energy consumption and lowering environmental impact.
- Integration with Digital Platforms: Roofing roll forming machines will likely integrate with digital platforms to streamline data management, maintenance tracking, and production scheduling.
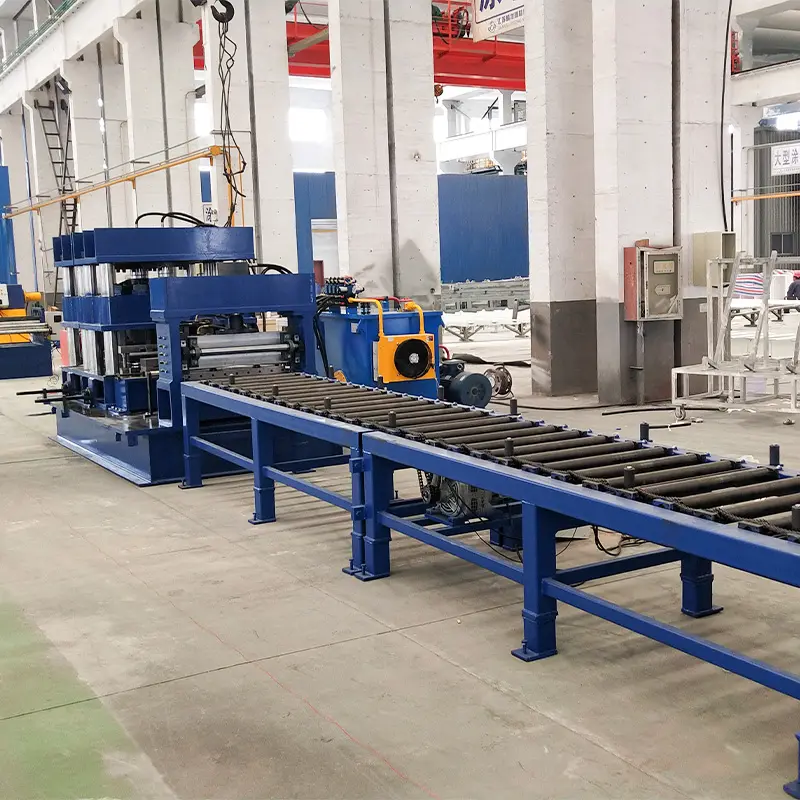
উপসংহার
The Ameco Roofing Roll Forming Machine has revolutionized the roofing industry, offering increased efficiency, consistent quality, and versatility in roofing profiles. Its user-friendly controls and safety measures make it an excellent investment for roofing manufacturers looking to enhance productivity and reduce costs. As technology continues to evolve, roofing roll forming machines are set to play a more significant role in meeting the industry’s growing demands for durable and innovative roofing solutions.
FAQs
What materials can the Ameco Roofing Roll Forming Machine handle?
The Ameco Roofing Roll Forming Machine can handle various materials, including galvanized steel, aluminum, and stainless steel.
Is the machine suitable for small-scale roofing projects?
Yes, the Ameco Roofing Roll Forming Machine can be adjusted to suit both small-scale and large-scale roofing projects.
Can the machine be integrated into existing production lines?
Absolutely! The Ameco Roofing Roll Forming Machine can be seamlessly integrated into existing production lines, enhancing overall efficiency.
How long does it take to set up the machine for a new roofing profile?
The setup time depends on the complexity of the roofing profile, but with its user-friendly controls, the machine can be quickly configured for new profiles.
Does Ameco provide technical support and training?
Yes, Ameco provides comprehensive technical support and training to ensure operators can maximize the machine’s capabilities and troubleshoot any issues effectively.