Introduction:
The construction industry has witnessed significant advancements in recent years, especially in the manufacturing of structural components like purlins. Among the various technologies, the CZ purlin রোল তৈরির মেশিন stands out for its efficiency, versatility, and cost-effectiveness. This article delves into the world of C Z purlin roll forming machines, exploring their working principles, advantages, types, operation, maintenance, safety, and applications.
What is a C Z Purlin Roll Forming Machine?
A C Z purlin roll forming machine is a specialized equipment used in the production of C and Z-shaped purlins, which are essential elements in constructing roofs and walls of buildings and other steel structures. The machine takes coils of steel and processes them through a series of steps to form uniform purlin sections of desired lengths.
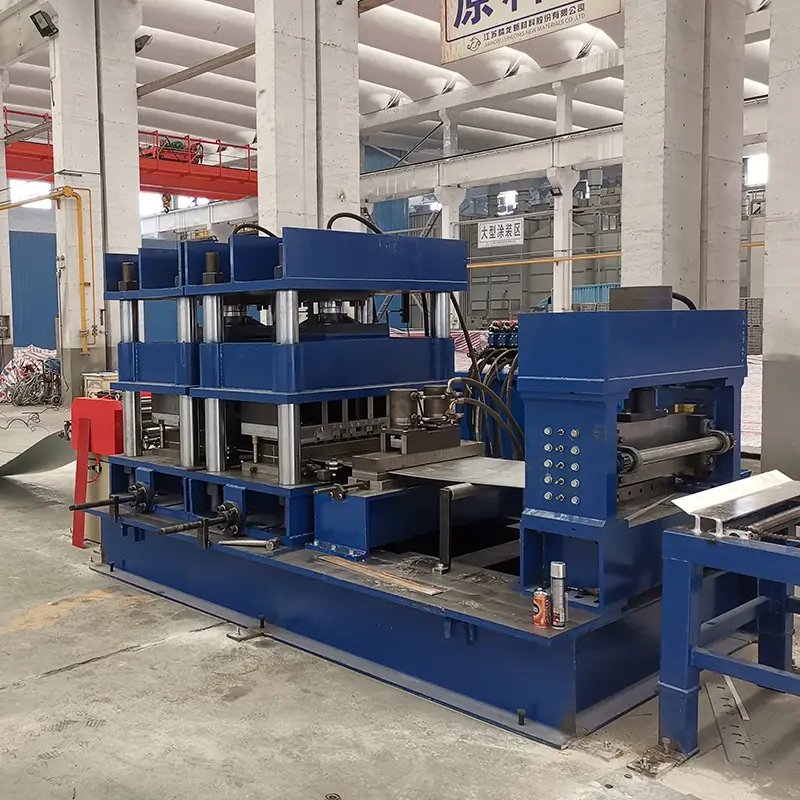
Advantages of Using C Z Purlin Roll Forming Machine:
- Cost-effective Production: The roll forming process is highly efficient, reducing material waste and lowering production costs.
- Customization and Flexibility: C Z purlin roll forming machines can produce purlins of various sizes, shapes, and thicknesses to meet specific construction requirements.
- High Production Speed: These machines can achieve high production rates, making them suitable for large-scale projects.
- Reduced Material Waste: The precise nature of roll forming minimizes material scrap, making it an environmentally friendly option.
Components of a C Z Purlin Roll Forming Machine:
- Uncoiler: This component holds and feeds the raw material coil into the machine.
- Feeding System: It guides the material into the roll forming unit accurately.
- Roll Forming Unit: This is the heart of the machine where the actual shaping of the purlins occurs.
- Punching System: It creates holes or slots as per design requirements.
- Cutting System: This cuts the formed purlins to the desired lengths.
- Control System: It governs the entire operation and settings of the machine.
- Stacker: The stacker neatly collects the finished purlins for further processing.
Working Principle of C Z Purlin Roll Forming Machine:
- Step 1: Material Loading: The process begins with feeding the coil into the uncoiler, which gradually unwinds the steel coil.
- Step 2: Material Guiding: The material is then guided through the feeding system to ensure proper alignment.
- Step 3: Roll Forming: The roll forming unit shapes the material into the desired C or Z purlin profile.
- Step 4: Punching and Cutting: Holes or slots are punched as needed, and the purlins are cut to the required lengths.
- Step 5: Stacking: The stacker collects and arranges the finished purlins for easy handling and transportation.
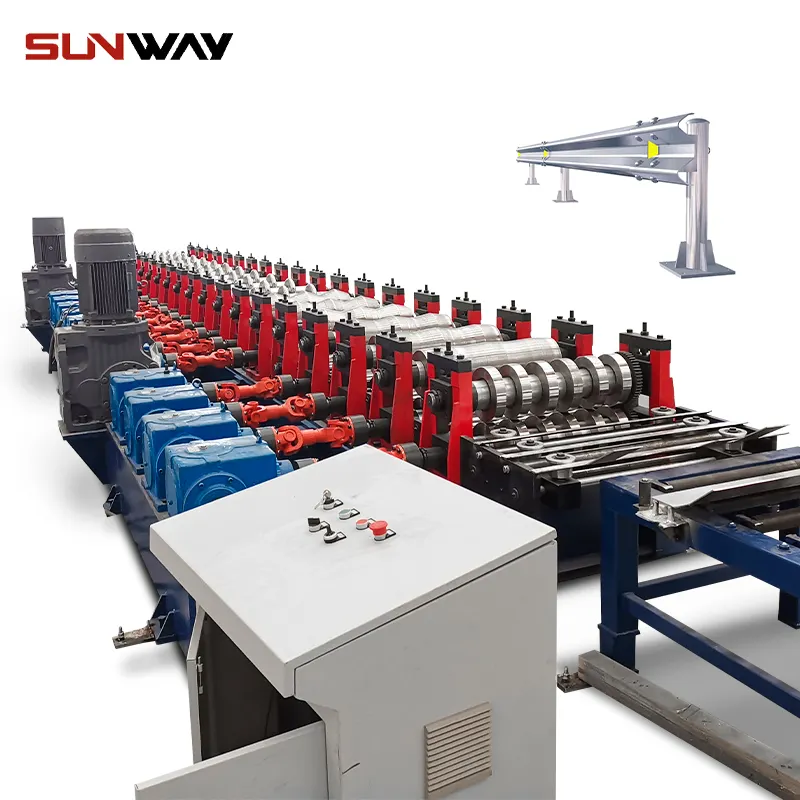
Different Types of C Z Purlin Roll Forming Machines:
- Single C/Z Purlin Roll Forming Machine: Ideal for small-scale or customized production needs.
- Double C/Z Purlin Roll Forming Machine: Allows for simultaneous production of two different purlin profiles.
- Interchangeable C/Z Purlin Roll Forming Machine: Offers quick and easy switching between C and Z profiles, improving efficiency.
Factors to Consider When Choosing a C Z Purlin Roll Forming Machine:
When selecting a C Z purlin roll forming machine for your production needs, several crucial factors should be taken into account:
- Material Thickness and Width: Ensure the machine can handle the required material thickness and width to produce the desired purlin profiles.
- Production Speed and Capacity: Consider the machine’s production speed and capacity to meet project deadlines efficiently.
- Automation and Control Features: Look for advanced control systems that offer ease of operation and reduce human errors.
- Maintenance and Support: Choose a machine that comes with reliable maintenance support and spare parts availability.
How to Operate a C Z Purlin Roll Forming Machine?
Operating a C Z purlin roll forming machine involves several steps:
- Machine Setup: Ensure the machine is correctly installed and calibrated for the desired purlin specifications.
- Material Loading and Adjustment: Load the coil into the uncoiler and adjust the feeding system for accurate material alignment.
- Running the Machine: Start the machine and monitor the roll forming, punching, and cutting processes.
- Inspecting the Output: Regularly check the formed purlins for any defects or deviations from specifications.
Common Quality Issues and Troubleshooting:
- Uneven Roll Forming: Adjust the roll forming unit and ensure the material is properly aligned and guided.
- Material Jamming: Check for obstructions in the feeding system and clear any blockages.
- Punching and Cutting Errors: Verify the punching and cutting mechanisms for proper functioning.
Safety Measures When Operating a C Z Purlin Roll Forming Machine:
- Personal Protective Equipment (PPE): Operators should wear appropriate safety gear, such as gloves, safety glasses, and ear protection.
- Machine Guards and Safety Devices: Ensure all safety guards and devices are in place and functioning correctly.
- Regular Maintenance and Inspection: Schedule regular maintenance and inspection to identify and address potential safety hazards.
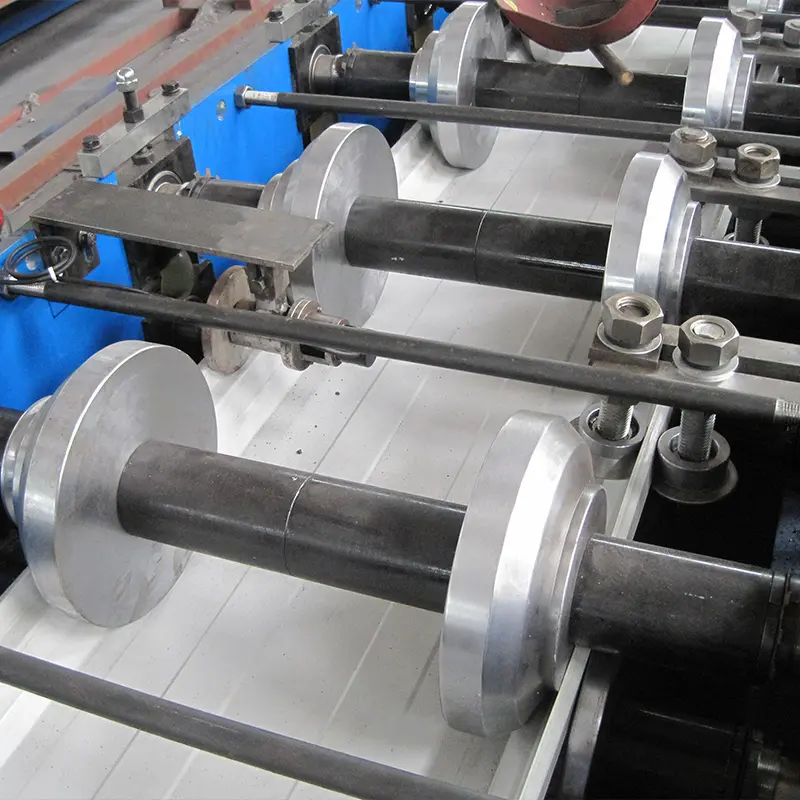
Maintenance Tips for C Z Purlin Roll Forming Machine:
- Lubrication: Regularly lubricate moving parts to minimize wear and ensure smooth operation.
- Cleaning and Dust Removal: Keep the machine clean and free from dust and debris that can affect its performance.
- Component Inspection and Replacement: Inspect machine components regularly and replace any worn-out parts promptly.
Applications of C Z Purlin Roll Forming Machine:
C Z purlin roll forming machines find widespread applications in various industries, including:
- Construction Industry: For the production of structural components in residential, commercial, and industrial buildings.
- Pre-engineered Buildings: To fabricate pre-engineered building systems with speed and precision.
- Infrastructure Projects: Used in the construction of bridges, warehouses, and other infrastructure projects.
Future Trends and Innovations in Roll Forming Technology:
The roll forming industry is continuously evolving, and some promising trends and innovations include:
- Advanced Control Systems: Incorporating sophisticated control systems to enhance accuracy and production efficiency.
- Eco-friendly Materials: The adoption of sustainable and eco-friendly materials in roll forming processes.
- Integration of AI and IoT: Leveraging artificial intelligence and the Internet of Things to optimize machine performance and predictive maintenance.
Comparison with Other Purlin Manufacturing Methods:
- Hot Rolled Purlins: C Z purlin roll forming offers a more cost-effective and precise alternative to traditional hot rolling methods.
- Cold Formed Purlins: The roll forming process ensures consistent and accurate purlin profiles, unlike cold forming, which may result in dimensional variations.
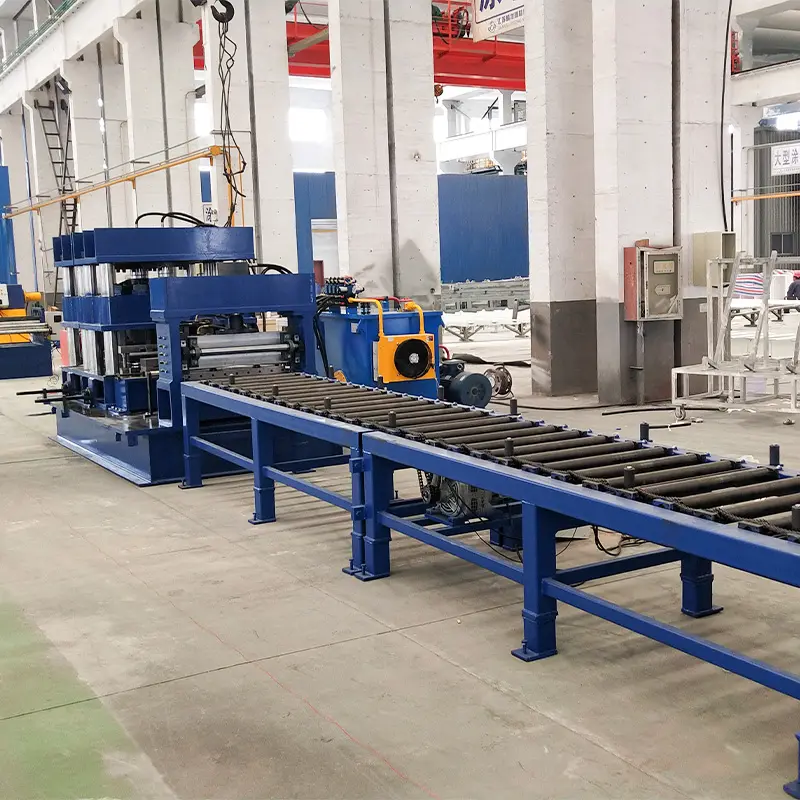
Conclusion:
The C Z purlin roll forming machine has revolutionized the production of purlins, offering a cost-effective, efficient, and versatile solution for various construction projects. Its ability to produce customized purlin profiles at high speeds while minimizing material waste makes it a valuable asset in modern construction. As technology continues to advance, we can expect even more innovative developments in roll forming technology.
FAQs:
1. How long does it take to set up a C Z purlin roll forming machine? Setting up a C Z purlin roll forming machine typically takes a few hours, depending on its complexity and the operator’s experience.
2. Can the machine handle different types of materials? Yes, C Z purlin roll forming machines can process various materials, including galvanized steel, stainless steel, and aluminum.
3. Is training required to operate the machine? Yes, operators should receive proper training to understand the machine’s controls, safety protocols, and maintenance procedures.
4. Can a C Z purlin roll forming machine produce other profiles? While specialized for C and Z purlins, some machines can be adapted to produce other custom profiles as well.
5. What is the typical warranty period for such machines? Warranty periods vary by manufacturer but usually range from one to three years. Additionally, extended warranties may be available.