ভূমিকা
In the world of modern construction, precision and efficiency are paramount. Manufacturers and builders constantly seek advanced technologies to streamline their processes, reduce costs, and enhance the quality of their products. One such technology that has gained significant popularity is the Automatic C Purlin Roll Forming Machine. This revolutionary equipment has revolutionized the production of C-shaped steel purlins, offering numerous benefits that traditional manufacturing methods cannot match.
What is an Automatic C Purlin Roll Forming Machine?
An Automatic C Purlin Roll Forming Machine is a specialized piece of equipment designed to efficiently fabricate C-shaped steel purlins used in various structural applications. These purlins serve as horizontal beams providing structural support for roofs, walls, and floors in buildings and infrastructure projects. The roll forming machine takes flat strips of steel, passes them through a series of rollers, and shapes them into the desired C-profile.
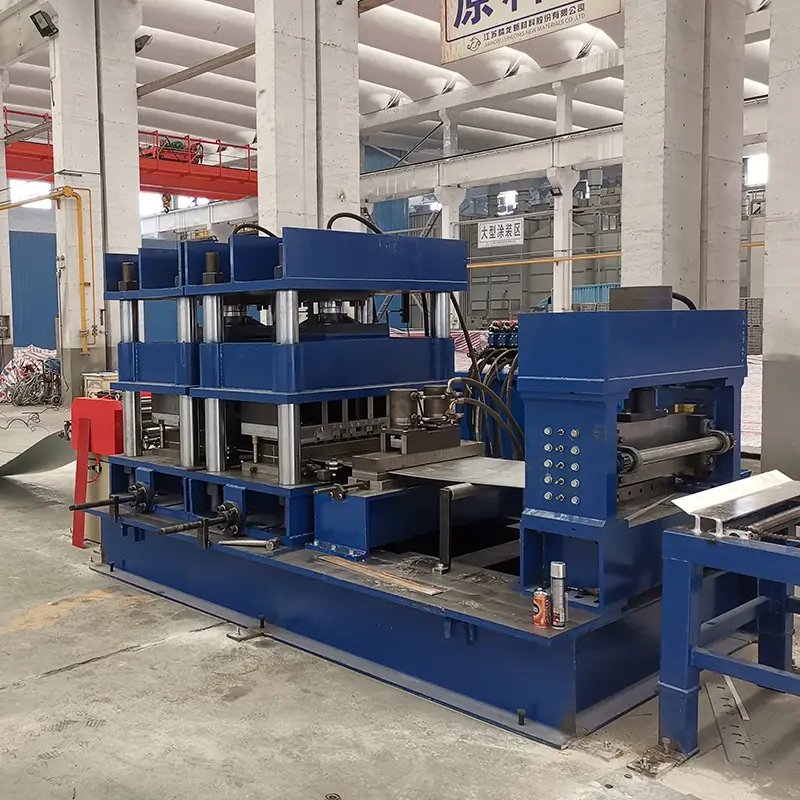
How Does an Automatic C Purlin Roll Forming Machine Work?
Step 1: Material Loading
The process begins with loading the raw material, typically steel coils, onto the machine’s decoiler. The machine’s control system ensures smooth and precise material feeding.
Step 2: Guiding and Feeding
The steel strip is then guided through a set of rollers that gradually shape it into the C-profile. The guiding and feeding mechanisms maintain the proper alignment of the strip for accurate forming.
Step 3: Roll Forming Process
During this stage, the steel strip goes through a series of forming rollers. Each set of rollers progressively bends and shapes the material into the desired C-shaped profile. The machine’s computerized control system ensures uniform dimensions and consistent quality.
Step 4: Cutting and Shearing
Once the C-profile is formed, the machine’s cutting unit precisely cuts the profile to the required length. Shearing mechanisms ensure clean and accurate cuts.
Step 5: Stacking and Discharging
The finished C purlins are then stacked and discharged from the machine, ready for further processing or direct use in construction projects.
Advantages of Using an Automatic C Purlin Roll Forming Machine
Increased Efficiency
Unlike traditional manufacturing methods that involve multiple manual steps, an automatic roll forming machine streamlines the entire production process. This results in higher production rates and shorter lead times, increasing overall efficiency.
Precision and Consistency
The automated nature of the machine ensures precise and consistent production of C purlins. Manufacturers can achieve tight tolerances and uniform profiles, reducing material wastage and ensuring better fit during assembly.
Versatility
Automatic C Purlin Roll Forming Machines can produce a wide range of C-profiles with varying dimensions and thicknesses. This versatility allows manufacturers to cater to different project requirements without the need for extensive retooling.
Cost-Effectiveness
While the initial investment in an automatic roll forming machine may seem substantial, the long-term cost savings are significant. Reduced labor costs, higher productivity, and minimized material wastage contribute to substantial cost-effectiveness.
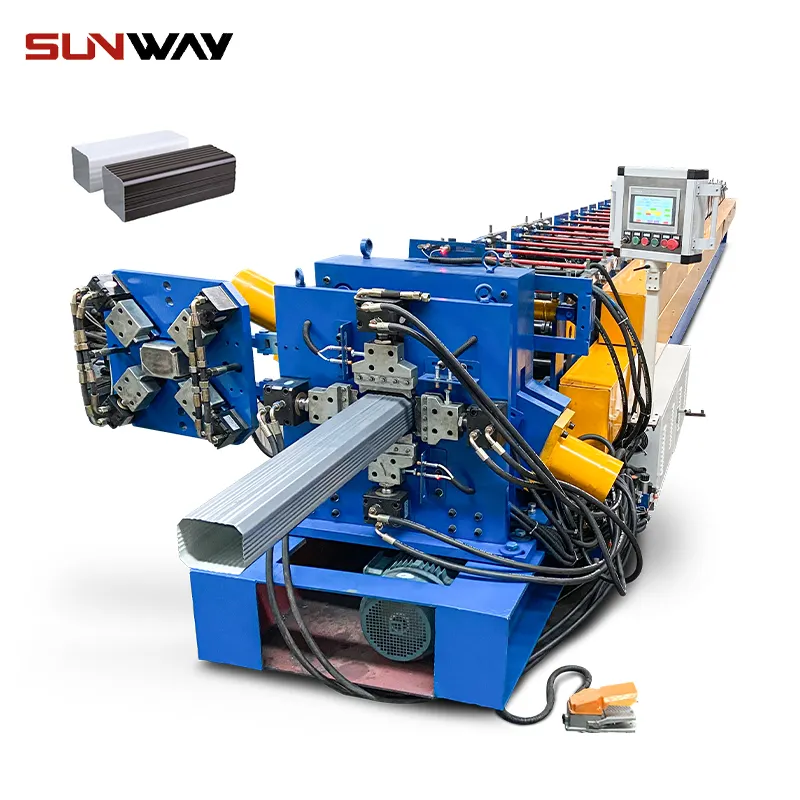
Applications of Automatic C Purlin Roll Forming Machines
The versatility and efficiency of automatic C purlin roll forming machines make them indispensable in various industries and applications:
Construction Industry
In the construction sector, C purlins are widely used for framing roofs and walls in commercial and residential buildings. The high-quality and consistent output of automatic roll forming machines ensures sturdy and reliable structures.
Infrastructure Projects
Large-scale infrastructure projects, such as bridges and highways, often require sturdy support structures. C purlins produced by roll forming machines offer the required strength and load-bearing capacity.
Warehouse and Storage Solutions
Industrial warehouses and storage facilities benefit from the use of C purlins as they provide cost-effective and durable roofing solutions. Roll-formed purlins are lightweight yet robust, making them ideal for large-span structures.
Automotive Industry
In the automotive sector, C purlins find applications in carports, parking structures, and industrial garage buildings. Their easy installation and structural integrity make them a popular choice in the automotive industry.
Solar Panel Mounting Systems
Roll-formed C purlins are also used in solar panel mounting structures. Their ability to provide a strong, reliable foundation for solar panels contributes to the widespread adoption of renewable energy solutions.
Factors to Consider When Choosing an Automatic C Purlin Roll Forming Machine
Investing in an automatic C purlin roll forming machine requires careful consideration of several crucial factors:
Machine Specifications
Evaluate the machine’s specifications, including the roll forming speed, capacity, and control features. Choose a machine that aligns with your production requirements.
Material Compatibility
Ensure that the machine can handle the specific materials you intend to use, such as galvanized steel, stainless steel, or aluminum.
Customization Options
Look for machines that offer flexibility in producing various sizes and profiles of C purlins to meet diverse project needs.
Budget and ROI Analysis
While cost is a critical factor, focus on the long-term return on investment (ROI) by considering productivity gains and material savings.
After-Sales Support and Service
Select a reputable manufacturer that provides excellent after-sales support, including maintenance, training, and spare parts availability.
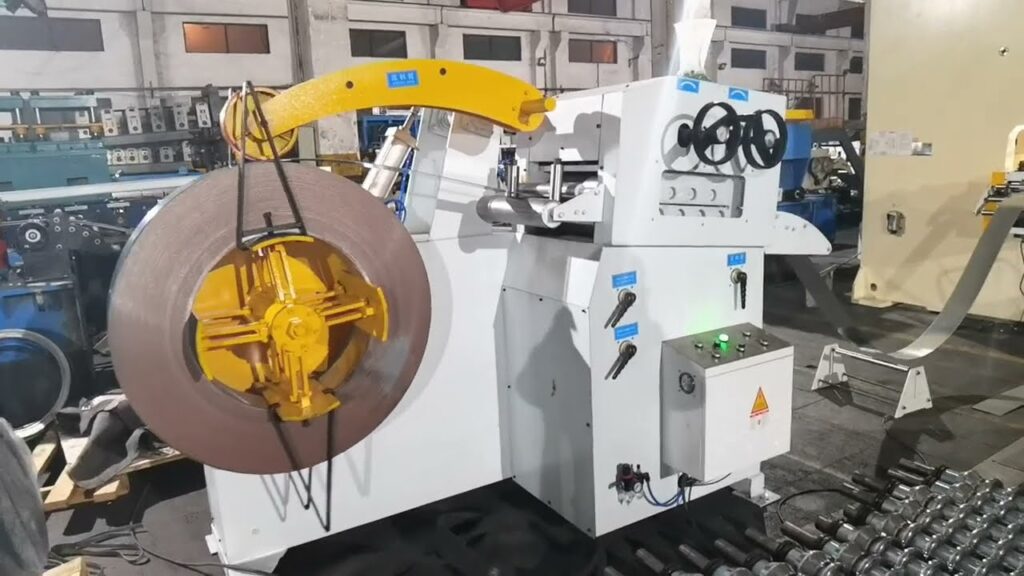
Maintenance and Care for an Automatic C Purlin Roll Forming Machine
To ensure the optimal performance and longevity of your automatic C purlin roll forming machine, follow these maintenance practices:
Regular Inspections
Schedule routine inspections to identify and address any potential issues before they escalate into major problems.
Lubrication and Cleaning
Keep the machine’s moving parts properly lubricated and clean to reduce friction and prevent dust accumulation.
Safety Measures
Adhere to safety guidelines and ensure that operators use appropriate personal protective equipment (PPE) during machine operation.
Tips for Optimizing Performance and Productivity
To maximize the benefits of an automatic C purlin roll forming machine, implement the following strategies:
Operator Training
Ensure that operators are adequately trained in operating and maintaining the machine to prevent operational errors and downtime.
Proper Material Handling
Optimize material handling processes to minimize material wastage and improve workflow efficiency.
Workflow Management
Implement efficient production planning and workflow management to streamline the roll forming process.
Quality Control Measures
Implement stringent quality control checks to ensure the produced C purlins meet required specifications.
Trends and Innovations in Automatic C Purlin Roll Forming Technology
The roll forming industry is constantly evolving, and several trends and innovations are shaping the future of automatic C purlin roll forming machines:
Advanced Control Systems
Modern roll forming machines come equipped with advanced control systems that offer enhanced precision, real-time monitoring, and seamless integration with other manufacturing processes.
Energy Efficiency Features
Manufacturers are incorporating energy-efficient components and systems into roll forming machines to reduce overall energy consumption.
Integration with CAD/CAM Software
Integration with computer-aided design (CAD) and computer-aided manufacturing (CAM) software allows for seamless transfer of design data to the roll forming machine, improving accuracy and reducing setup times.
Common Challenges and Troubleshooting
Despite the numerous benefits of automatic C purlin roll forming machines, certain challenges may arise during operation. Here are some common issues and troubleshooting tips:
Material Jamming
Material jams can occur due to improper material feeding or irregularities in the steel strip. Regularly inspect the feeding system and ensure the material is free from defects or debris.
Forming Defects
Inconsistent roll forming can lead to defects such as waves or buckling in the purlins. Adjust the roll forming parameters and inspect the rollers for wear or damage.
Machine Malfunctions
Regular maintenance and prompt repairs are essential to avoid unexpected machine breakdowns. Address any malfunctions immediately to minimize downtime.
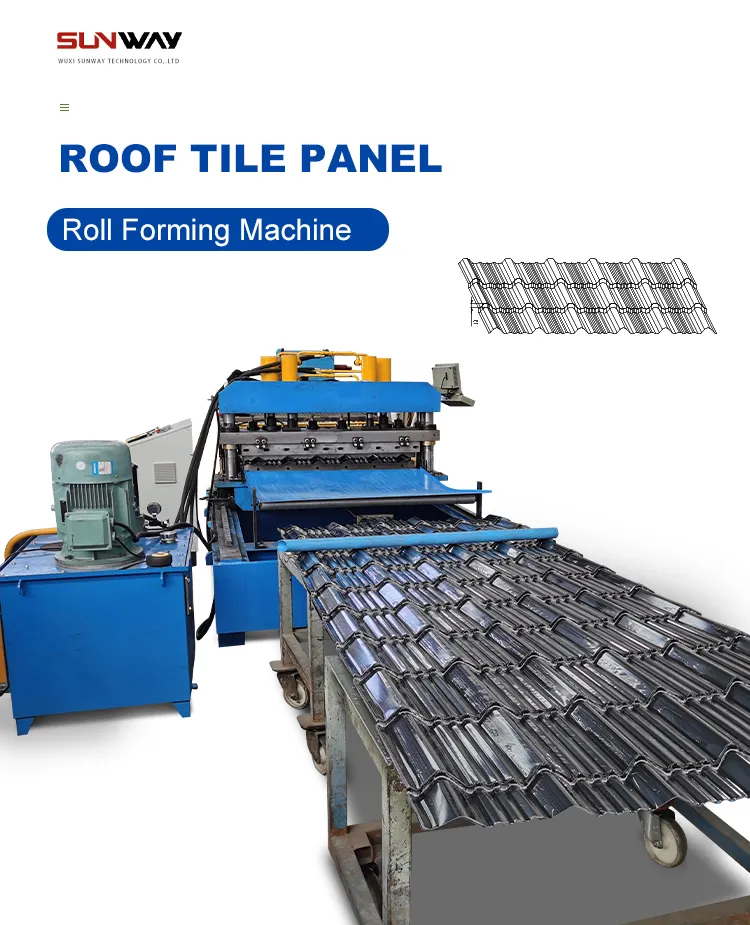
Environmental Impact and Sustainability Considerations
As sustainability becomes a growing concern in the manufacturing industry, the environmental impact of roll forming operations should be considered:
Material Recycling
Promote the recycling and responsible disposal of scrap material to reduce the environmental footprint of roll forming processes.
Energy Consumption
Implement energy-efficient practices and invest in energy-saving technologies to minimize the machine’s energy consumption.
Emissions Reduction
Explore emission reduction strategies, such as using cleaner energy sources or optimizing the machine’s combustion processes.
Safety Regulations and Compliance in Roll Forming Operations
Operating an automatic C purlin roll forming machine requires adherence to safety regulations and compliance standards:
OSHA Guidelines
Follow the guidelines set by the Occupational Safety and Health Administration (OSHA) to ensure a safe working environment for machine operators.
Risk Assessment and Mitigation
Conduct thorough risk assessments and implement safety measures to minimize workplace accidents and injuries.
Personal Protective Equipment (PPE)
Ensure that all operators wear appropriate personal protective equipment, including gloves, safety glasses, and ear protection.
Case Studies: Successful Implementation of Automatic C Purlin Roll Forming Machines
Learn from real-world examples of successful roll forming machine implementations:
Project A: Residential Building Construction
A construction company increased its productivity and reduced material waste by investing in an automatic C purlin roll forming machine for their residential building projects.
Project B: Solar Farm Installation
A renewable energy company improved the structural integrity and lifespan of its solar panel mounting structures by using roll-formed C purlins.
Project C: Industrial Warehouse Development
An industrial warehouse developer reduced construction time and labor costs by incorporating automatic roll forming technology.
Future Prospects of Automatic C Purlin Roll Forming Machines
The future of automatic C purlin roll forming machines looks promising:
Industry Growth
As the construction and infrastructure industries continue to expand, the demand for roll-formed C purlins is expected to rise.
Technological Advancements
Advancements in roll forming technology will lead to even more precise and efficient machines.
Market Forecast
Market analysts predict significant growth in the roll forming machinery market, driven by the need for sustainable construction solutions.
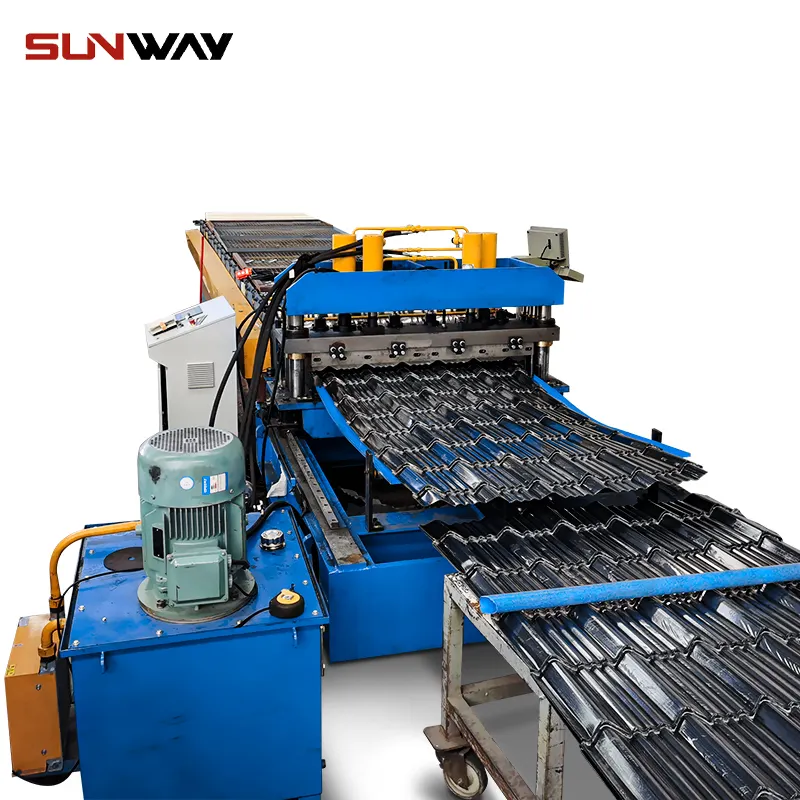
উপসংহার
The automatic C purlin roll forming machine has revolutionized the construction industry by providing a fast, efficient, and cost-effective method of producing high-quality C-shaped steel purlins. With its numerous advantages and diverse applications, this innovative technology continues to reshape the way we build and construct structures.
FAQs
- Are C purlins only used in the construction industry? C purlins are commonly used in the construction industry, but their applications extend to other sectors such as automotive and solar panel mounting.
- Is an automatic roll forming machine suitable for small-scale operations? Yes, automatic roll forming machines can be used for both large-scale and small-scale operations, offering efficiency and precision regardless of the project size.
- Can an automatic C purlin roll forming machine handle different materials? Yes, many automatic roll forming machines can handle various materials, including steel, stainless steel, and aluminum.
- Is operator training necessary for using an automatic roll forming machine? Yes, proper operator training is essential to ensure safe and efficient machine operation.
- What kind of maintenance does an automatic roll forming machine require? Regular inspections, lubrication, and cleaning are essential for maintaining the machine’s optimal performance and longevity.