ভূমিকা
Gutters are an essential part of any building’s drainage system, preventing water damage by channeling rainwater away from the roof and foundation. Traditional gutter manufacturing methods involve manual labor, which can be time-consuming and lead to inconsistencies in quality and design. The introduction of water gutter roll forming machines has revolutionized the gutter manufacturing industry by streamlining the production process and ensuring high-quality output. In this article, we will explore the functionality, benefits, types, components, maintenance, safety, and applications of water gutter roll forming machines.
What is a Water Gutter Roll Forming Machine?
A water gutter roll forming machine is an automated production line designed to fabricate gutters continuously from coils of metal, such as aluminum, steel, or copper. The machine shapes the metal into a desired gutter profile through a series of rolling operations, resulting in precise dimensions and uniform quality.
How Does a Water Gutter Roll Forming Machine Work?
The operation of a water gutter roll forming machine involves multiple stages. First, the decoiler feeds the metal coil into the machine, which then passes through a series of rollers, each responsible for gradually shaping the metal into the desired gutter profile. The roll forming unit is complemented by a cutting mechanism that trims the gutter to the required length. The entire process is controlled through an integrated control panel, allowing for easy adjustments and real-time monitoring.
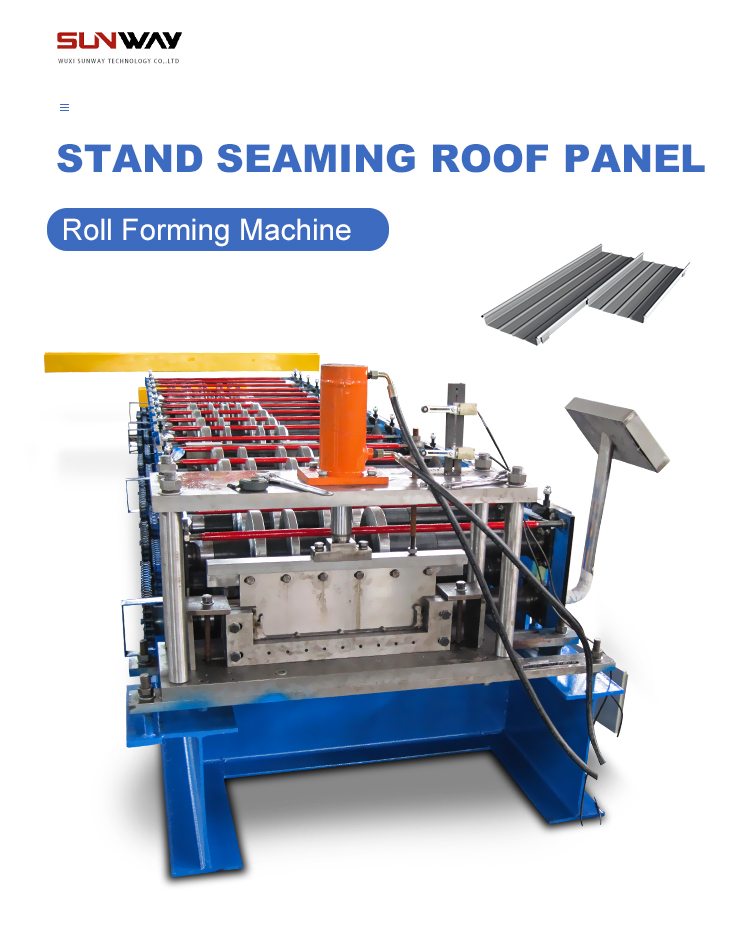
Benefits of Using a Water Gutter Roll Forming Machine
Cost-effective Production
Water gutter roll forming machines enable efficient and cost-effective production due to their automation, reducing the need for manual labor and increasing production speeds.
Customization and Flexibility
Roll forming machines offer a high degree of customization, allowing manufacturers to produce gutters in various sizes and profiles to meet diverse customer requirements.
High-Quality Output
The automated nature of roll forming ensures consistent and high-quality gutter production, minimizing defects and enhancing customer satisfaction.
Time Efficiency
By eliminating manual steps and reducing production time, water gutter roll forming machines optimize the overall manufacturing process.
Durability and Longevity
Gutters produced using roll forming machines are known for their durability and longevity, ensuring long-lasting performance and customer value.
Types of Water Gutter Roll Forming Machines
Water gutter roll forming machines come in various types, each designed to produce specific gutter profiles. The most common types include:
Continuous Gutter Roll Forming Machines
Continuous gutter roll forming machines produce seamless gutters of continuous lengths, making them ideal for large-scale projects where long gutters are required without joints.
Box Gutter Roll Forming Machines
Box gutter roll forming machines are used to create box-shaped gutters commonly used in commercial and industrial buildings due to their high capacity for water flow.
K-Style Gutter Roll Forming Machines
K-style gutter roll forming machines are versatile and widely used in residential applications, offering an attractive profile with efficient water flow capabilities.
Half-Round Gutter Roll Forming Machines
Half-round gutter roll forming machines produce semi-circular gutters, which are aesthetically pleasing and often used in historical or architectural restoration projects.
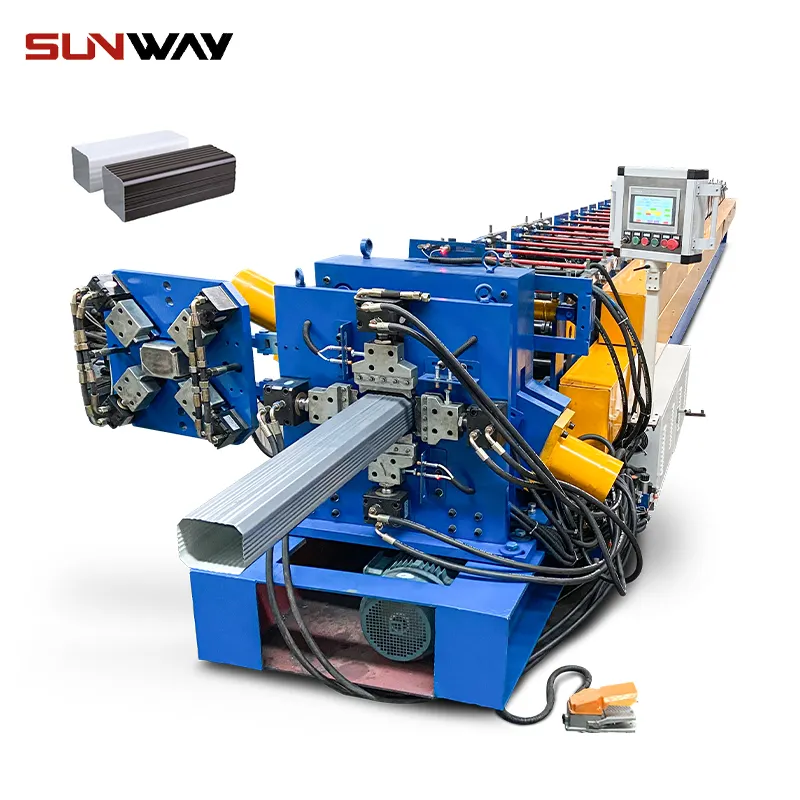
Key Components of a Water Gutter Roll Forming Machine
Understanding the key components of a water gutter roll forming machine is essential for maximizing its performance and ensuring smooth operations. These components include:
ডিকয়লার
The decoiler holds the metal coil and provides a continuous feed of material to the roll forming unit, ensuring uninterrupted production.
Roll Forming Unit
The roll forming unit consists of a series of rollers, each responsible for shaping the metal into the desired gutter profile gradually.
Cutting Mechanism
The cutting mechanism trims the gutter to the required length, ensuring precision and accuracy.
Control Panel
The control panel is the brain of the machine, allowing operators to set parameters, monitor production, and make adjustments as needed.
Factors to Consider When Choosing a Water Gutter Roll Forming Machine
Selecting the right water gutter roll forming machine for a business requires careful consideration of various factors:
Material Compatibility
Ensure that the machine is compatible with the metal material being used for gutter fabrication, such as aluminum, steel, or copper.
Production Speed
Consider the production speed and output capacity of the machine to meet the demands of your target market.
Machine Size and Capacity
Choose a machine that fits your available space and has the capacity to handle the gutter sizes and profiles you intend to produce.
Level of Automation
Assess the level of automation the machine offers to determine its ease of use and potential labor cost savings.
After-Sales Support and Warranty
Select a reputable manufacturer that provides reliable after-sales support and warranty coverage to ensure long-term satisfaction and assistance.
Maintenance and Care Tips for Water Gutter Roll Forming Machines
Proper maintenance is crucial for the optimal performance and longevity of a water gutter roll forming machine. Here are some essential maintenance tips:
Regular Cleaning and Lubrication
Keep the machine clean and well-lubricated to prevent rust and ensure smooth operation.
Inspection and Repair
Regularly inspect the machine for any signs of wear and tear, and promptly address any issues to prevent further damage.
Training and Operator Skill Development
Provide adequate training to machine operators to ensure safe and efficient use of the equipment.
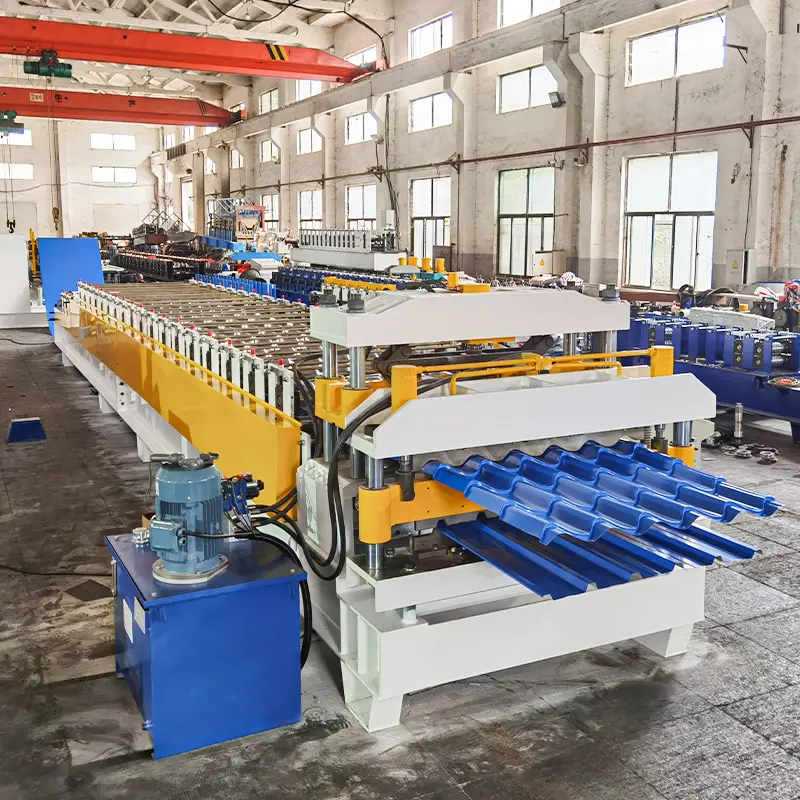
Safety Precautions While Operating a Water Gutter Roll Forming Machine
Safety is paramount when operating heavy machinery like water gutter roll forming machines. Implement these safety precautions:
Operator Training
Ensure all operators are properly trained to use the machine, understand its safety features, and know emergency procedures.
Use of Personal Protective Equipment (PPE)
Mandate the use of appropriate PPE, such as helmets, gloves, and safety goggles, to protect operators from potential hazards.
Emergency Stop Procedures
Clearly communicate and practice emergency stop procedures to quickly halt the machine in case of an emergency.
Trends and Innovations in Water Gutter Roll Forming Technology
The water gutter roll forming industry continues to evolve, with innovative technologies driving efficiency and sustainability. Some notable trends include:
Advanced Material Options
Manufacturers are exploring new materials, such as eco-friendly alloys and composites, to create gutters that offer enhanced performance and environmental benefits.
Energy Efficiency Features
Modern roll forming machines are designed with energy-saving features to reduce power consumption and operating costs.
Integration of Smart Technology
Smart technology is being integrated into water gutter roll forming machines, enabling remote monitoring, predictive maintenance, and data-driven insights.
Applications of Water Gutter Roll Forming Machines
Water gutter roll forming machines have a wide range of applications beyond traditional residential gutter systems:
Residential Gutter Systems
Gutters produced by roll forming machines are extensively used in residential buildings to protect roofs and foundations from water damage.
Commercial and Industrial Gutter Systems
Large-scale commercial and industrial buildings rely on roll-formed gutters to manage the substantial volume of rainwater runoff.
Rainwater Harvesting Systems
Roll-formed gutters play a vital role in rainwater harvesting systems, efficiently collecting and storing rainwater for various purposes.
Green Building Initiatives
Sustainable construction practices are promoting the use of roll-formed gutters made from eco-friendly materials.
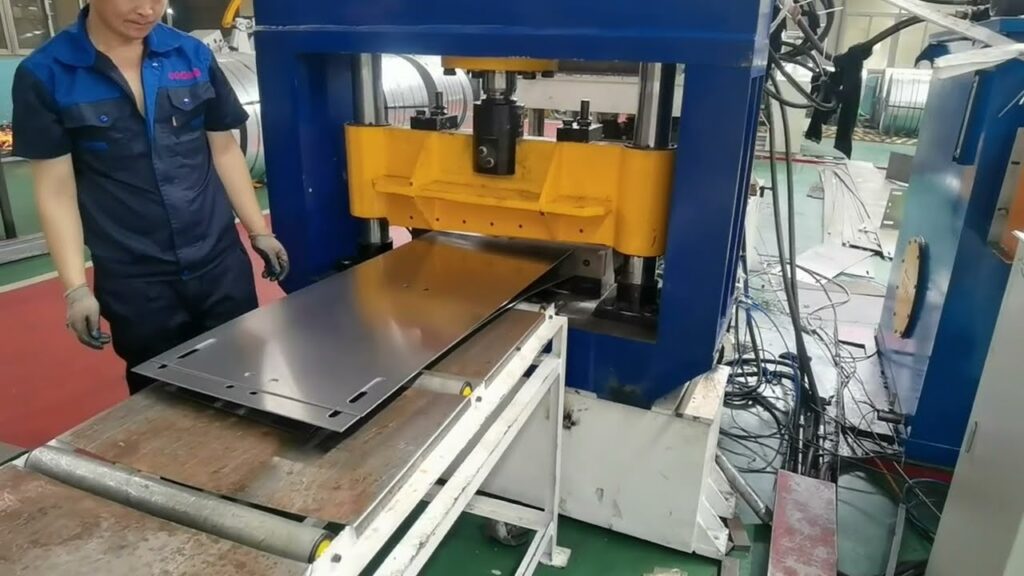
How to Maintain Quality Control in Water Gutter Roll Forming
Ensuring consistent quality is essential for customer satisfaction and brand reputation. Implement these quality control measures:
Raw Material Inspection
Thoroughly inspect incoming materials to ensure they meet required specifications and standards.
Regular Quality Checks
Conduct regular quality checks during and after production to identify and address any deviations or defects.
Customer Feedback and Satisfaction
Seek feedback from customers to understand their needs better and improve product quality based on their preferences.
Environmental Impact of Water Gutter Roll Forming
Manufacturers are increasingly adopting environmentally responsible practices in water gutter roll forming:
Sustainable Materials and Practices
Using recyclable materials and adopting energy-efficient processes can reduce the environmental impact.
Recycling and Waste Reduction
Implement recycling programs to manage metal waste generated during the roll forming process.
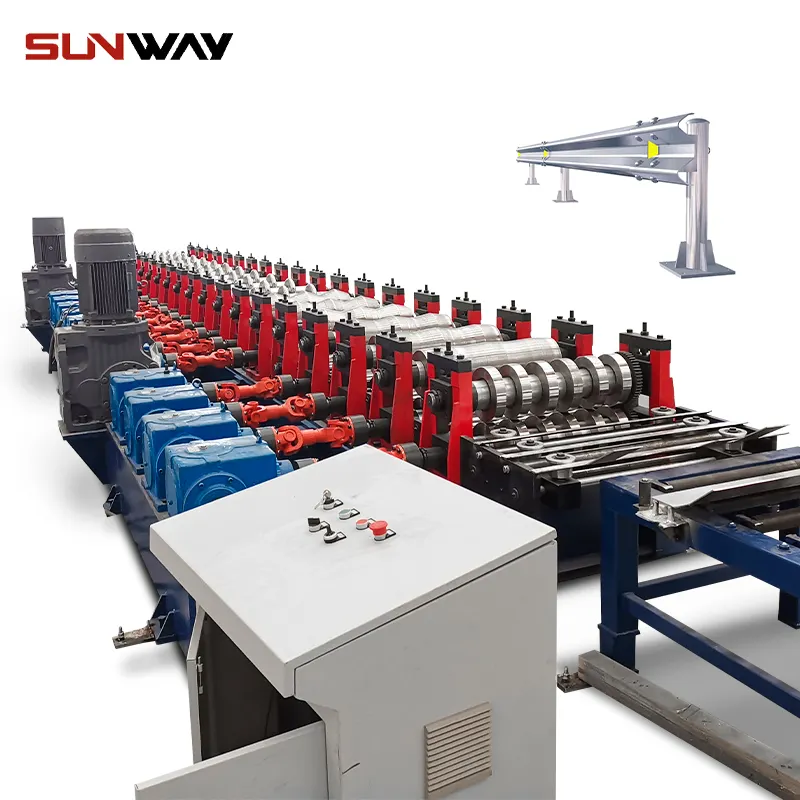
উপসংহার
Water gutter roll forming machines have transformed the gutter manufacturing industry by streamlining production, ensuring high-quality output, and promoting sustainability. As demand for efficient drainage systems grows, these machines will continue to play a pivotal role in meeting market needs and enhancing building infrastructure.
FAQs
Q: Are water gutter roll forming machines suitable for both residential and commercial applications?
A: Yes, water gutter roll forming machines can produce gutters for both residential and commercial buildings, offering a wide range of profiles to meet various requirements.
Q: What materials can be used with water gutter roll forming machines?
A: Water gutter roll forming machines are compatible with materials like aluminum, steel, and copper, commonly used for gutter fabrication.
Q: Are roll-formed gutters more durable than traditional gutters?
A: Yes, roll-formed gutters tend to be more durable and long-lasting due to their uniform construction and higher quality control.
Q: Can water gutter roll forming machines be customized for unique gutter profiles?
A: Yes, water gutter roll forming machines can be customized to produce specific and unique gutter profiles to meet customer demands.
Q: What safety precautions should be taken when operating a water gutter roll forming machine?
A: Operators should receive proper training, wear appropriate PPE, and be familiar with emergency stop procedures to ensure safety during operation.