ভূমিকা
In the realm of sheet metal production, efficiency and precision play vital roles in meeting the demands of various industries. One key technology that has revolutionized the process is the ঢেউতোলা শীট রোল মেশিন গঠন. This article delves into the intricacies of this machine, exploring its benefits, components, working principle, and factors to consider when choosing one. So, let’s dive into the world of corrugated sheet roll forming machines and discover how they streamline sheet production.
What is a Corrugated Sheet Roll Forming Machine?
A corrugated sheet roll forming machine is a specialized equipment used to fabricate corrugated sheets from flat metal coils. It employs a continuous process that involves feeding the coil into the machine, where it undergoes a series of roll forming operations to shape it into the desired corrugated profile. The machine seamlessly transforms the flat sheet into a corrugated one, ready for various applications.
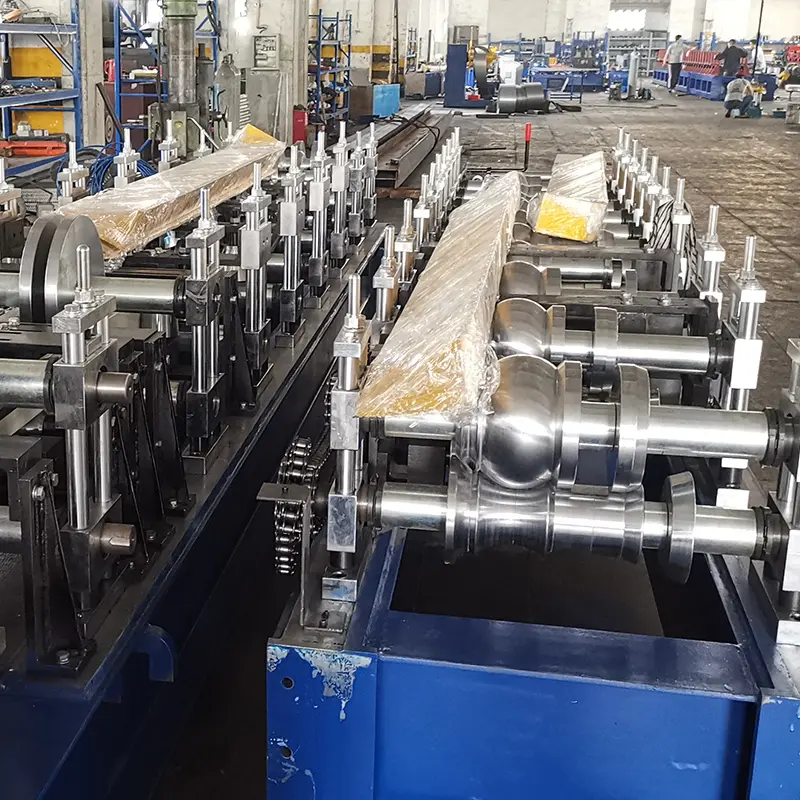
Benefits of Using a Corrugated Sheet Roll Forming Machine
Efficient Production Process
The corrugated sheet roll forming machine offers remarkable advantages in terms of production efficiency. By automating the process, it eliminates the need for manual labor, thereby reducing production time and costs. The continuous operation allows for a high output rate, ensuring a steady supply of corrugated sheets to meet market demands promptly.
Versatile Applications
Corrugated sheets find applications across multiple industries, such as construction, packaging, automotive, and more. The roll forming machine enables the production of corrugated sheets with different profiles, sizes, and materials, making them versatile for various applications. Whether it’s roofing, cladding, or protective packaging, the machine can meet diverse requirements.
Customization Options
One of the key advantages of a corrugated sheet roll forming machine is its ability to offer customization options. Manufacturers can tailor the machine settings to create sheets with specific corrugation profiles, thicknesses, and lengths. This flexibility allows businesses to cater to unique customer needs and gain a competitive edge in the market.
Components of a Corrugated Sheet Roll Forming Machine
A corrugated sheet roll forming machine consists of several essential components that work together seamlessly to produce high-quality corrugated sheets.
আনকোয়লার
The uncoiler is the first component of the machine and is responsible for holding and releasing the flat metal coil. It ensures a steady and controlled feed of the coil into the subsequent roll forming process.
Feeding System
The feeding system is responsible for guiding the flat metal coil into the roll forming stations accurately. It ensures the material is fed consistently and evenly, preventing any potential defects in the final corrugated sheet.
Roll Forming Stations
The roll forming stations are the heart of the corrugated sheet roll forming machine. They consist of a series of rollers, each with a specific contour and function. As the flat metal coil passes through these stations, the rollers progressively shape it into the desired corrugated profile.
কাটিং সিস্টেম
After the sheet has been formed, the cutting system comes into play. It trims the corrugated sheet to the desired length, ensuring precision and accuracy. Different cutting mechanisms, such as shear or flying cutoff, can be used depending on the requirements.
নিয়ন্ত্রণ ব্যবস্থা
The control system acts as the brain of the corrugated sheet roll forming machine. It oversees and regulates the entire production process, controlling the speed, length, and other parameters. Modern control systems often feature user-friendly interfaces, making it easier for operators to monitor and adjust the machine settings.
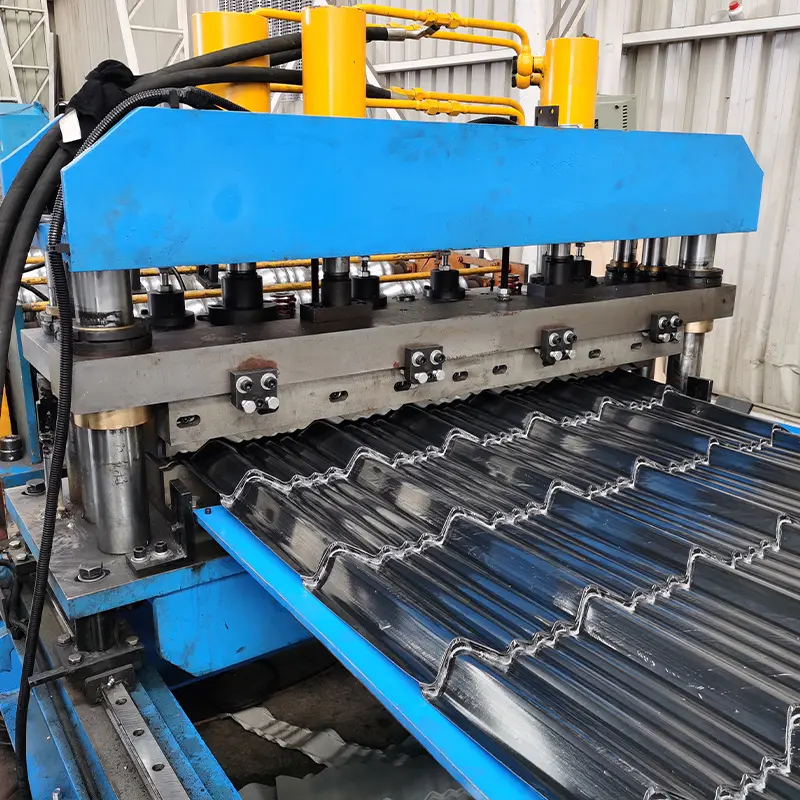
Working Principle of a Corrugated Sheet Roll Forming Machine
The working principle of a corrugated sheet roll forming machine involves a continuous process that transforms the flat metal coil into a corrugated sheet. The machine’s feeding system feeds the coil into the roll forming stations, where the rollers gradually shape the material into the desired corrugation profile. The formed sheet then undergoes the cutting process, resulting in precise lengths of corrugated sheets ready for further applications.
Factors to Consider When Choosing a Corrugated Sheet Roll Forming Machine
Selecting the right corrugated sheet roll forming machine is crucial for optimal production and business success. Several factors should be considered before making a decision.
Production Capacity
The production capacity of the machine determines the quantity of corrugated sheets it can produce within a given time frame. Evaluating the required production volume and matching it with the machine’s output capability is vital to meet market demands effectively.
Material Compatibility
Different materials, such as steel, aluminum, or copper, may require specific machine configurations for optimal performance. Understanding the material compatibility of the roll forming machine is crucial to ensure efficient and accurate sheet production.
Machine Durability
Investing in a durable and reliable machine is essential for long-term profitability. Consider the build quality, durability of components, and reputation of the manufacturer when assessing the machine’s overall reliability.
Cost and Return on Investment
The cost of the corrugated sheet roll forming machine and its associated operating expenses should align with the anticipated return on investment. Evaluating the machine’s price, maintenance costs, and potential productivity gains will help make an informed decision.

Maintenance and Troubleshooting Tips
Maintaining a corrugated sheet roll forming machine properly is essential to ensure its longevity and uninterrupted production. Here are some maintenance and troubleshooting tips:
Regular Lubrication
Lubrication plays a critical role in preventing friction and wear between the machine’s moving parts. Regularly lubricating the rollers, chains, and other components will help minimize downtime and extend the machine’s lifespan.
Cleaning and Inspection
Regular cleaning and inspection of the machine will help identify and address any issues promptly. Remove debris, check for loose connections, and inspect the cutting blades for wear. Performing these tasks regularly can prevent unexpected breakdowns.
Common Issues and Solutions
Some common issues with corrugated sheet roll forming machines include misalignment, material jamming or improper sheet formation. If misalignment occurs, it’s crucial to check and adjust the rollers’ positions to ensure proper shaping of the sheet. In case of material jamming, carefully remove any debris or stuck material to restore the smooth flow of the coil through the machine.
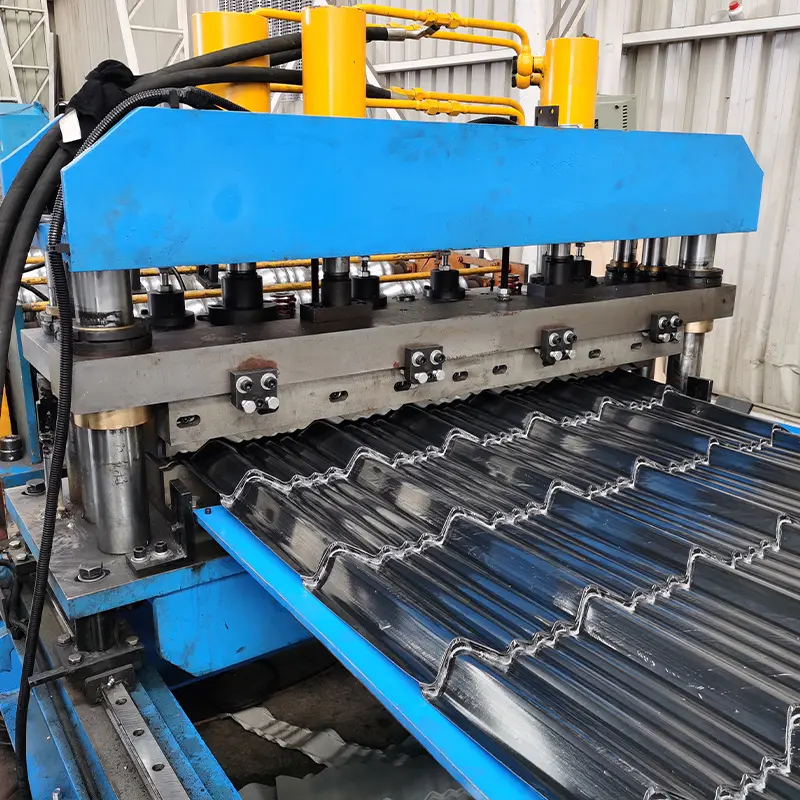
উপসংহার
The corrugated sheet roll forming machine revolutionizes the production process by offering efficiency, versatility, and customization options. With its various components working in harmony, it seamlessly transforms flat metal coils into high-quality corrugated sheets. When choosing a machine, factors such as production capacity, material compatibility, machine durability, and cost must be considered. Proper maintenance, regular lubrication, cleaning, and troubleshooting will ensure optimal performance and extend the machine’s lifespan.
FAQs
1. Can a corrugated sheet roll forming machine produce sheets with different profiles?
Yes, a corrugated sheet roll forming machine can be adjusted to produce sheets with various corrugation profiles according to specific requirements.
2. What industries can benefit from corrugated sheets produced by roll forming machines?
Corrugated sheets have versatile applications and are widely used in industries such as construction, packaging, automotive, and more.
3. How long does it take to set up and start producing sheets with a corrugated sheet roll forming machine?
The setup time depends on the complexity of the machine and the operator’s familiarity with its operation. Once set up, the machine can start producing sheets immediately.
4. Are corrugated sheet roll forming machines easy to maintain?
Corrugated sheet roll forming machines require regular maintenance, including lubrication, cleaning, and inspection. Following the manufacturer’s guidelines and performing routine maintenance tasks will ensure smooth operation.
5. Can a corrugated sheet roll forming machine handle different types of materials?
Yes, corrugated sheet roll forming machines can be designed to handle various materials such as steel, aluminum, copper, and others. It’s important to choose a machine that is compatible with the desired material for optimal results.