ভূমিকা
In the world of manufacturing, efficiency, speed, and accuracy are paramount. When it comes to producing shelf panels, a crucial component of various storage and display systems, having the right equipment can make a significant difference. This is where a বালুচর প্যানেল রোল মেশিন গঠন comes into play. In this article, we will explore the functionality, benefits, key components, working principles, and applications of shelf panel roll forming machines. We will also provide insights into choosing the right machine and offer maintenance tips for optimal performance.
একটি শেল্ফ প্যানেল রোল ফর্মিং মেশিন কি?
A shelf panel roll forming machine is a specialized piece of equipment used in the production of shelf panels. These machines utilize a continuous bending process to transform flat metal sheets into highly durable, customized panels with various profiles. The roll forming process involves feeding the metal coil through a series of roller dies, gradually shaping it into the desired form. The result is a precisely formed panel ready for use in a wide range of applications.
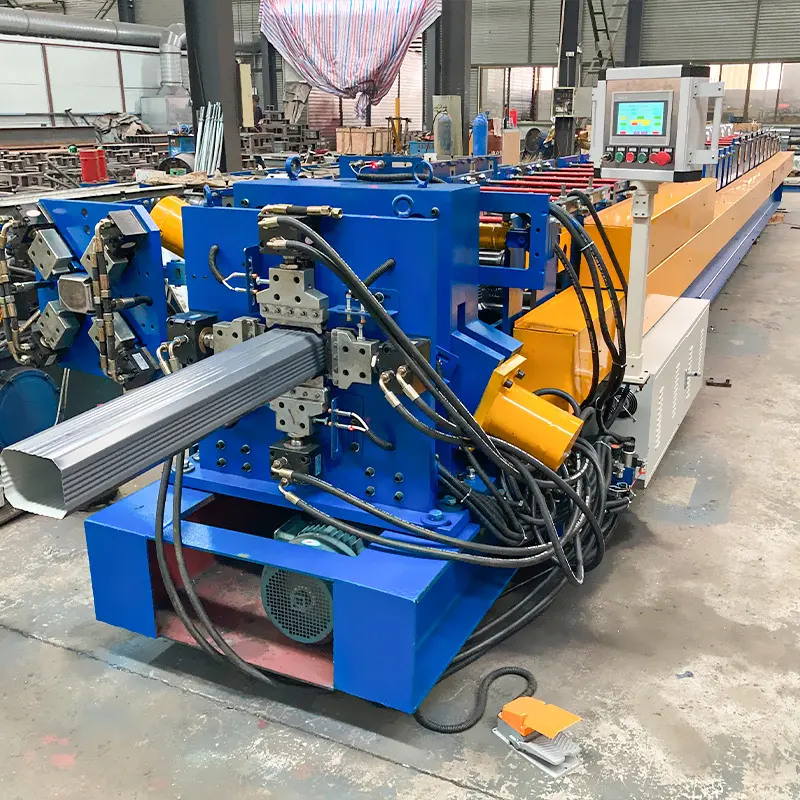
Benefits of Using a Shelf Panel Roll Forming Machine
High Efficiency and Productivity
One of the primary advantages of using a shelf panel roll forming machine is the significant increase in efficiency and productivity it offers. These machines are designed for high-speed production, enabling the continuous manufacturing of panels without compromising on quality. With the ability to produce panels at a rapid pace, manufacturers can meet demanding production schedules and reduce lead times.
Customizable Designs and Flexibility
Shelf panel roll forming machines provide manufacturers with the flexibility to create customized designs tailored to specific requirements. By adjusting the roller dies and other settings, different panel profiles, dimensions, and hole patterns can be achieved. This adaptability allows for the production of panels suitable for various shelving and storage systems, ensuring a perfect fit for diverse applications.
Cost Savings
Investing in a shelf panel roll forming machine can lead to significant cost savings in the long run. With streamlined production processes, reduced material waste, and enhanced efficiency, manufacturers can lower their overall manufacturing costs. Additionally, the ability to create panels in-house eliminates the need for outsourcing and minimizes transportation expenses, further contributing to cost savings.
Durable and High-Quality Output
Shelf panel roll forming machines produce panels with exceptional durability and quality. The continuous roll forming process ensures uniformity and precision in panel dimensions, eliminating variations commonly found in manual or other manufacturing methods. The panels produced are sturdy, able to withstand heavy loads, and exhibit excellent surface finishes, meeting the highest quality standards.
Working Principles of a Shelf Panel Roll Forming Machine
Shelf panel roll forming machines operate on the principle of continuous bending and shaping of metal sheets. The process begins with a metal coil being unwound from a decoiler, which feeds the coil into the machine’s feeding system. The metal passes through a series of roll forming stations, where roller dies gradually shape the material into the desired profile. The final step involves cutting the formed panels to the required lengths using a cutting system. The control system ensures precise coordination of all machine components, allowing for seamless operation and optimal output.
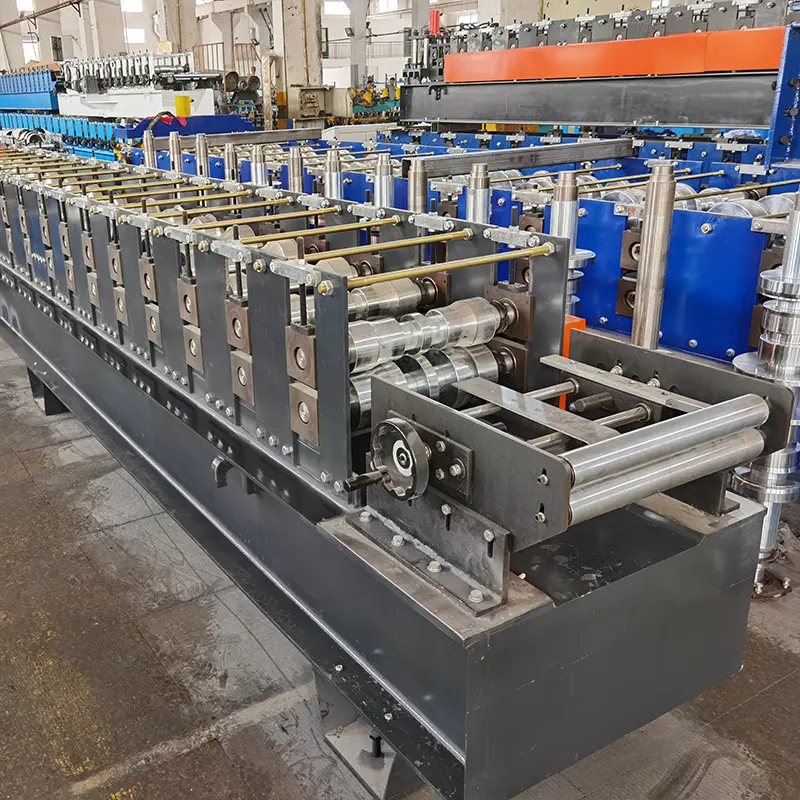
Key Components of a Shelf Panel Roll Forming Machine
A shelf panel roll forming machine consists of several key components, each playing a vital role in the production process. Let’s take a closer look at these components:
ডিকয়লার
The decoiler serves as the starting point of the roll forming process. It holds the metal coil and feeds it into the machine’s feeding system. The decoiler ensures a continuous and controlled supply of material, maintaining an uninterrupted production flow.
Feeding System
The feeding system transports the metal coil from the decoiler into the roll forming stations. It ensures proper alignment and feeding of the material, preventing any misalignment or damage during the bending process.
Roll Forming Stations
The roll forming stations are the heart of the machine, where the actual bending and shaping of the metal occur. These stations consist of multiple pairs of rollers, each gradually forming a specific section of the panel. The number and configuration of the roll forming stations depend on the desired panel design and complexity.
কাটিং সিস্টেম
Once the panel has been formed, it needs to be cut into the desired lengths. The cutting system, often equipped with flying or stationary shears, performs this task with precision and accuracy. Some machines also incorporate punching units to create holes or slots in the panels during the cutting process.
নিয়ন্ত্রণ ব্যবস্থা
The control system acts as the brain of the shelf panel roll forming machine, ensuring the coordination and synchronization of all machine components. It allows operators to set parameters, monitor the production process, and make adjustments as needed. Advanced control systems may feature touchscreen interfaces and remote access capabilities for enhanced convenience.
শেল্ফ প্যানেল রোল ফর্মিং মেশিনের প্রকার
Shelf panel roll forming machines come in various types, each offering specific advantages for different production requirements. Here are three commonly used types:
Single-Sided Roll Forming Machines
Single-sided roll forming machines produce panels from one side of the metal coil, typically forming panels with a uniform profile along the length. These machines are suitable for applications where only one side of the panel will be visible or require a consistent design.
Double-Sided Roll Forming Machines
Double-sided roll forming machines can produce panels with different profiles on both sides of the metal coil simultaneously. This type of machine is ideal for applications where both sides of the panel will be visible or need specific designs.
Continuous Roll Forming Machines
Continuous roll forming machines enable the continuous production of panels without interruptions, resulting in a highly efficient process. These machines are often used for applications requiring long lengths of panels, such as shelving systems in large warehouses or retail displays.
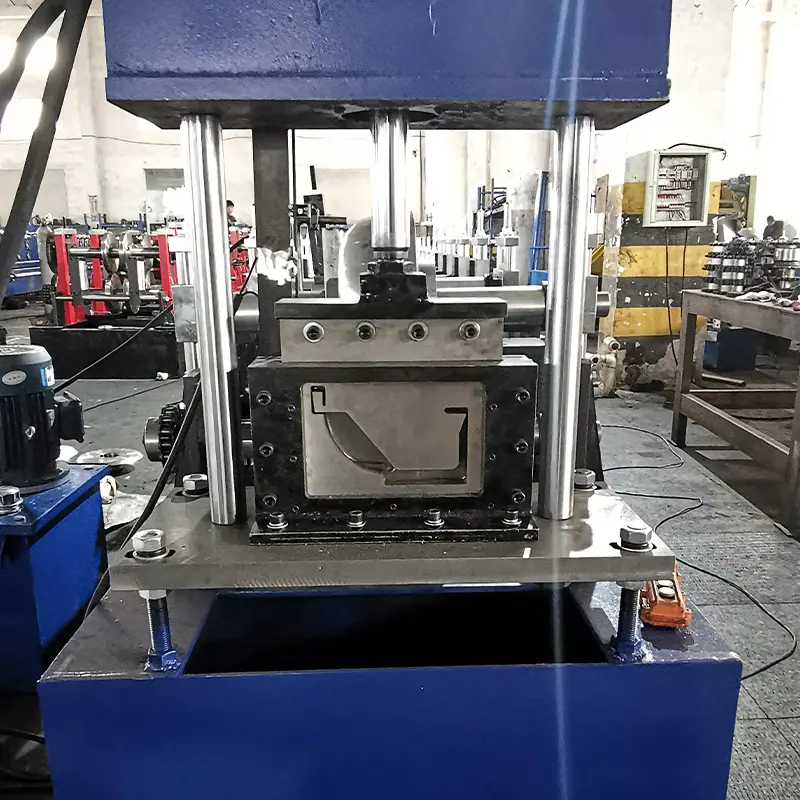
Factors to Consider When Choosing a Shelf Panel Roll Forming Machine
Selecting the right shelf panel roll forming machine for your production needs is crucial for maximizing efficiency and output quality. Here are some key factors to consider:
Production Requirements
Evaluate your production volume and determine the desired output capacity of the machine. Consider factors such as the required panel dimensions, production speed, and the number of shifts the machine will operate. Choosing a machine that aligns with your production requirements will ensure optimal utilization and avoid bottlenecks.
Material Compatibility
Different shelf panel roll forming machines are designed to work with specific materials, such as steel, aluminum, or galvanized metal. Ensure that the machine you choose is compatible with the material you intend to use for your panels. It’s also important to consider the material thickness and strength requirements for your specific applications.
Machine Configuration and Features
Examine the machine’s configuration and features to ensure they align with your production needs. Look for features such as quick-change systems for easy adjustment of roller dies, automatic lubrication systems for maintenance efficiency, and precision measurement systems for accurate panel dimensions. Additionally, consider any optional features or customization options that can enhance productivity and versatility.
Reliability and After-Sales Support
Investing in a shelf panel roll forming machine is a long-term commitment, so it’s crucial to choose a reputable manufacturer known for producing reliable and durable machines. Research customer reviews, warranty policies, and after-sales support services to ensure that you will have access to technical assistance and spare parts when needed. A reliable machine with good support will minimize downtime and maximize your return on investment.
Common Applications of Shelf Panel Roll Forming Machines
Shelf panel roll forming machines find applications in various industries where storage, organization, and display solutions are required. Some common applications include:
Warehouse Shelving Systems
Shelf panels produced by roll forming machines are extensively used in warehouse shelving systems. These systems provide efficient storage solutions for products of different sizes and weights. The durable and accurately formed panels ensure stability and load-bearing capacity, enabling safe and organized storage of goods.
Retail Displays and Racks
Retail environments often require attractive and versatile display solutions to showcase products effectively. Shelf panels produced by roll forming machines can be customized to fit specific display requirements, such as adjustable heights, shelving configurations, and branding elements. These panels contribute to visually appealing and functional retail displays.
Industrial Storage Solutions
Roll-formed shelf panels are integral components of industrial storage systems, such as pallet racking and mezzanine platforms. These systems optimize storage space and facilitate easy access to goods in manufacturing facilities, distribution centers, and logistics operations. The versatility of roll-formed panels allows for efficient customization based on the specific storage needs of different industries.
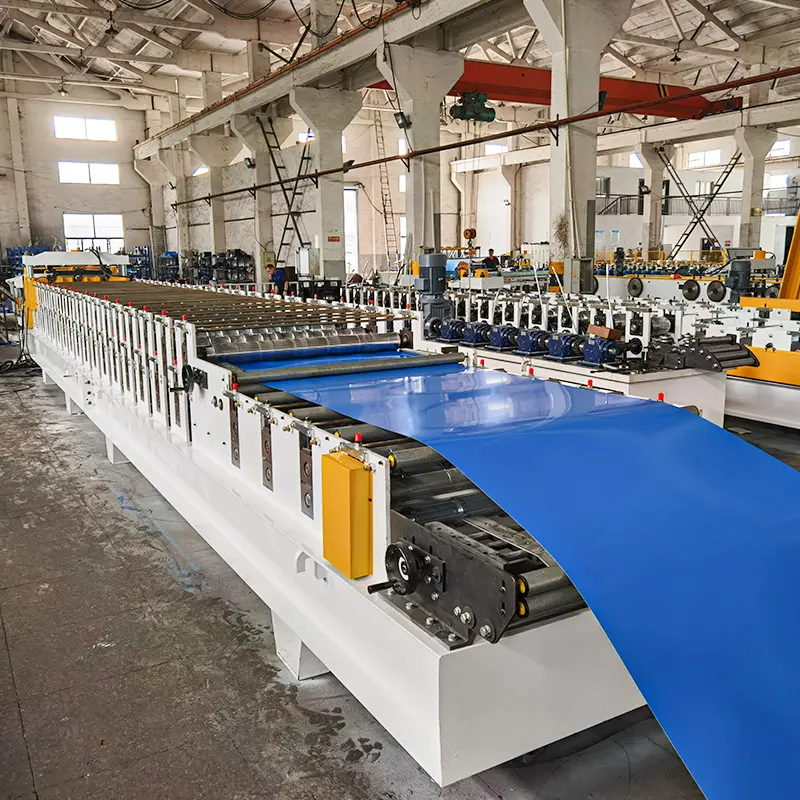
Maintenance and Care for Shelf Panel Roll Forming Machines
To ensure the longevity and optimal performance of your shelf panel roll forming machine, regular maintenance and care are essential. Here are some maintenance tips to follow:
- Lubrication: Regularly lubricate the moving parts of the machine to minimize friction and wear. Follow the manufacturer’s guidelines for lubricant types and intervals.
- Cleaning: Keep the machine clean from dust, debris, and accumulated material. Regularly inspect and clean the rollers, cutting blades, and other components to prevent contamination and maintain accurate panel dimensions.
- Inspection: Conduct routine inspections of the machine to identify any signs of wear, misalignment, or damage. Promptly address any issues to avoid further complications and ensure consistent production quality.
- Operator Training: Train machine operators on proper operation, maintenance procedures, and safety protocols. Well-trained operators can detect potential issues and perform routine maintenance tasks effectively.
- Spare Parts Inventory: Maintain an inventory of essential spare parts to minimize downtime in case of component failure. Consult with the machine manufacturer to identify critical spare parts that may need replacement over time.
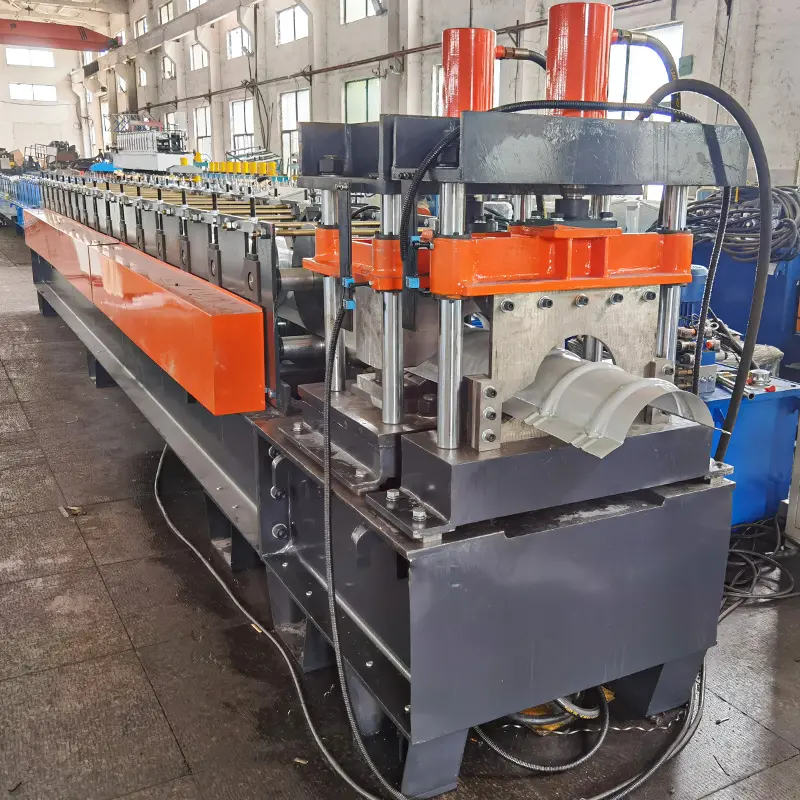
উপসংহার
Shelf panel roll forming machines offer manufacturers the ability to produce customized, high-quality panels with efficiency and precision. By investing in the right machine and following proper maintenance practices, manufacturers can streamline their production processes, reduce costs, and meet the diverse storage and display needs of various industries. Whether it’s for warehouse shelving, retail displays, or industrial storage systems, a well-maintained shelf panel roll forming machine is an invaluable asset for enhancing productivity and achieving optimal results.
FAQs
1. How long does it take to set up a shelf panel roll forming machine?
The setup time for a shelf panel roll forming machine can vary depending on factors such as machine complexity, panel design, and operator experience. Generally, it takes a few hours to set up the machine, including adjusting roller dies, configuring settings, and performing initial test runs.
2. Can a shelf panel roll forming machine produce different panel sizes?
Yes, shelf panel roll forming machines can be adjusted to produce panels of different sizes. By changing the roller dies and making necessary machine adjustments, manufacturers can customize the panel width, length, and profile according to their specific requirements.
3. What types of materials can be used with a shelf panel roll forming machine?
Shelf panel roll forming machines can work with various materials, including steel, aluminum, and galvanized metal. The choice of material depends on factors such as the desired panel strength, load-bearing capacity, and specific industry requirements.
4. Are shelf panel roll forming machines easy to operate?
Shelf panel roll forming machines are designed to be user-friendly and intuitive. However, proper training and familiarity with the machine’s controls and operating procedures are essential for safe and efficient operation. Manufacturers should provide training to operators to ensure smooth machine operation and optimal productivity.
5. How often should maintenance be performed on a shelf panel roll forming machine?
Regular maintenance should be performed on a shelf panel roll forming machine according to the manufacturer’s guidelines. It typically includes routine lubrication, cleaning, inspection, and replacement of worn parts. The frequency of maintenance tasks may vary based on factors such as machine usage, operating conditions, and production volume. Regular inspections should be conducted to identify any signs of wear or issues that require immediate attention.