In the world of metal sheet production, efficiency and precision are key factors in meeting the demands of various industries. Roll forming technology has long been a popular choice for shaping metal sheets into specific profiles, but advancements in this field have led to the emergence of ডবল লেয়ার রোল তৈরির মেশিনs, which offer even greater capabilities and flexibility. In this article, we will explore the concept of double layer roll forming machine, its advantages, working principles, applications, and factors to consider when choosing a machine. So let’s roll!
ভূমিকা
Metal sheet production plays a vital role in industries such as construction, automotive, and appliance manufacturing. Roll forming, a process where metal sheets are progressively shaped into desired profiles, has been a go-to method for years. However, traditional roll forming machines are limited to producing a single profile at a time, leading to time-consuming production cycles. This is where double layer roll forming machines come into play.
Understanding Roll Forming
Before diving into the specifics of double layer roll forming machines, it’s important to understand the basics of roll forming itself. Roll forming is a continuous process where a flat strip of metal is passed through a series of roller dies, gradually bending and forming it into a desired shape. This process offers high precision and repeatability, making it ideal for mass production.
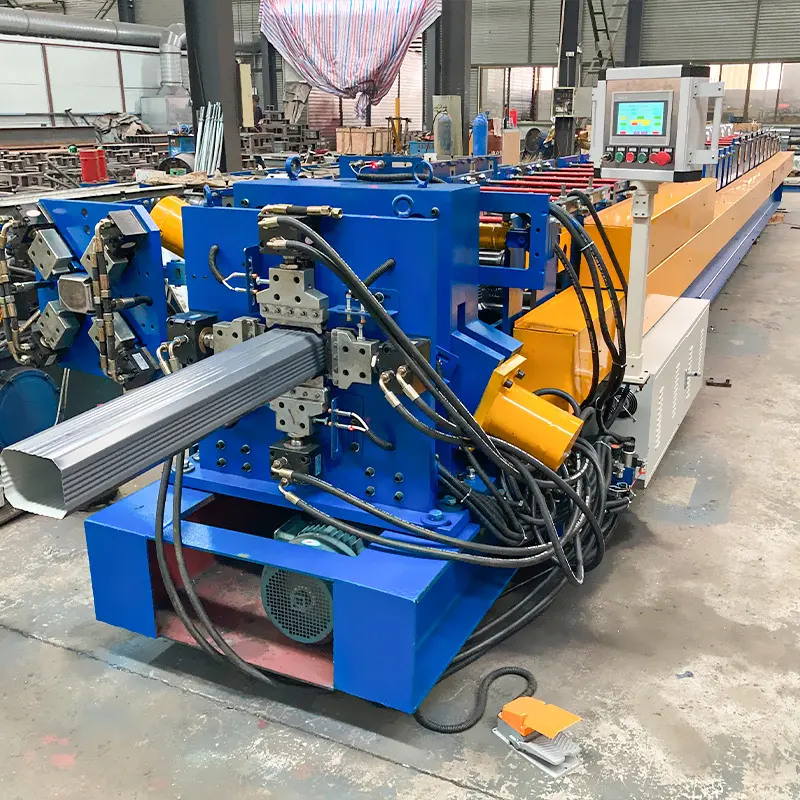
The Need for Double Layer Roll Forming Machines
While traditional roll forming machines have served the industry well, the need for increased efficiency and productivity has pushed the boundaries of this technology. Double layer roll forming machines have gained popularity due to their ability to produce two different profiles simultaneously. By utilizing two sets of roller dies, these machines effectively cut production time in half while maintaining the quality and precision of the formed profiles.
Advantages of Double Layer Roll Forming Machines
Double layer roll forming machines offer a range of advantages over their single-layer counterparts. Let’s take a closer look at some of the key benefits:
Increased Efficiency
By producing two profiles simultaneously, double layer roll forming machines significantly improve production efficiency. This results in shorter lead times, reduced labor costs, and increased overall output.
Cost Savings
With reduced production time and labor costs, businesses can experience substantial cost savings when using double layer roll forming machines. The higher output and improved efficiency contribute to a more profitable operation.
Versatility
Double layer roll forming machines provide the flexibility to produce a wide range of profiles, catering to diverse industry requirements. This versatility makes them an excellent choice for manufacturers dealing with multiple product lines.
Space Optimization
As double layer roll forming machines produce two profiles within the same machine, less floor space is required compared to running two separate machines. This allows manufacturers to optimize their workspace and maximize productivity.
Improved Quality
The precise control and accuracy of double layer roll forming machines ensure consistent and high-quality profiles. This is essential for meeting strict industry standards and delivering products that meet customer expectations.
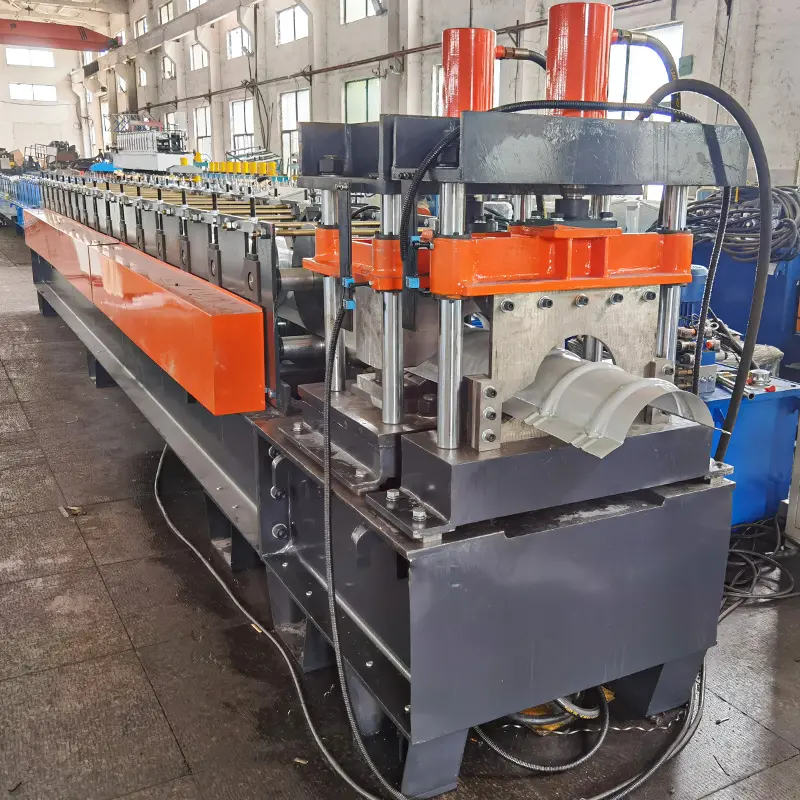
Components and Working Principle of Double Layer Roll Forming Machines
To fully grasp the inner workings of a double layer roll forming machine, it’s important to understand its key components and the working principle behind it.
Feeding System
The feeding system is responsible for continuously supplying the metal strip to the machine. It typically consists of a decoiler, straightening unit, and a feeding roller system that ensures smooth material flow.
Roller Dies
The heart of any roll forming machine is its roller dies. In the case of double layer roll forming machines, there are two sets of roller dies aligned side by side. Each set is designed to shape a specific profile, and the metal strip passes through both sets simultaneously.
Forming Stations
Forming stations are the series of rollers through which the metal strip passes, gradually forming it into the desired profile. The number and arrangement of forming stations depend on the complexity of the profiles being produced.
Cutting Mechanism
Once the metal strip has been shaped into the desired profiles, a cutting mechanism is employed to separate them from the remaining strip. Various cutting methods can be used, including hydraulic shearing, flying cutoff, or post-cut punching.
নিয়ন্ত্রণ ব্যবস্থা
Modern double layer roll forming machines are equipped with advanced control systems that allow operators to adjust various parameters such as roller positions, cutting length, and speed. These systems ensure precise and consistent production.
The working principle of a double layer roll forming machine involves the continuous feeding of the metal strip, which passes through the roller dies and forming stations. As the strip moves forward, it is shaped into two different profiles simultaneously. Finally, the profiles are cut to the desired length and collected for further processing or packaging.
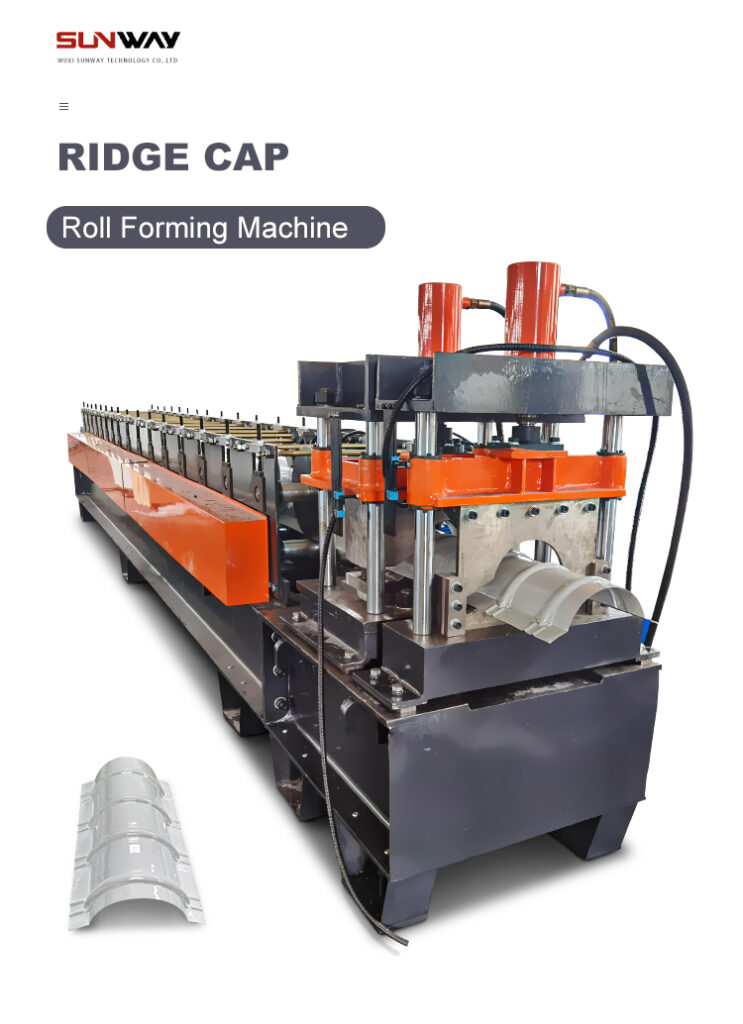
Applications of Double Layer Roll Forming Machines
The versatility of double layer roll forming machines opens up a wide range of applications across multiple industries. Some common applications include:
Building and Construction
Double layer roll forming machines are widely used in the construction industry for producing profiles such as roofing sheets, wall cladding, and ceiling panels. The ability to efficiently produce multiple profiles makes them an ideal choice for construction projects of various scales.
Automotive
In the automotive industry, double layer roll forming machines are employed for manufacturing components like car body panels, door frames, and roof rails. The high precision and quality offered by these machines ensure the structural integrity of automotive parts.
Appliance Manufacturing
From refrigerators to washing machines, the appliance manufacturing industry relies on double layer roll forming machines to shape metal sheets into components like outer panels, door frames, and handles. The ability to produce multiple profiles simultaneously contributes to the overall efficiency of the manufacturing process.
Shelving and Racking Systems
Double layer roll forming machines find extensive use in the production of shelving and racking systems for warehouses, retail stores, and logistics centers. These machines can efficiently produce profiles with varying lengths, shapes, and load-bearing capacities, catering to specific storage requirements.
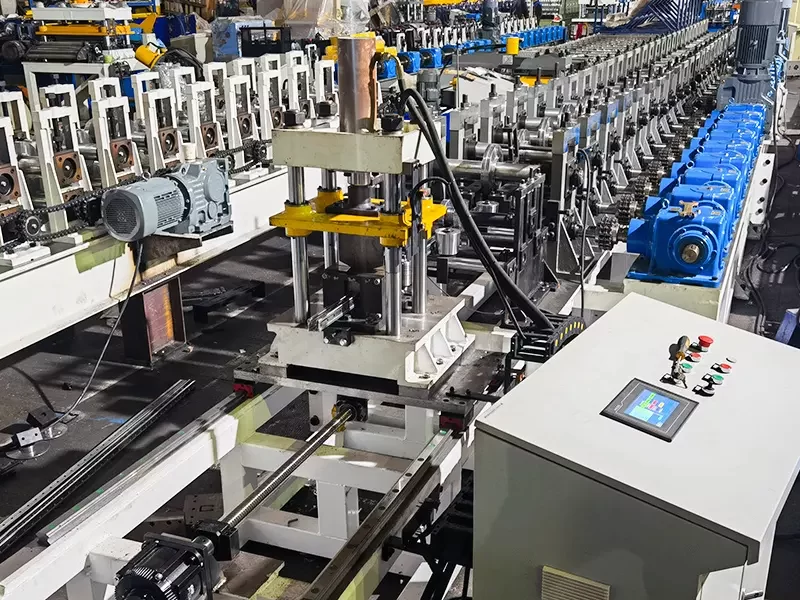
Factors to Consider When Choosing a Double Layer Roll Forming Machine
When selecting a double layer roll forming machine for your manufacturing needs, it’s essential to consider various factors to ensure the best fit for your requirements. Some key considerations include:
Production Capacity
Assess your production requirements in terms of output volume and speed. Choose a double layer roll forming machine that can meet or exceed your desired production capacity to avoid bottlenecks and delays.
Profile Complexity
Consider the types of profiles you need to produce. Some machines may be better suited for simple profiles, while others can handle more complex shapes and designs. Ensure that the machine you choose can accommodate the specific profiles you require.
Material Compatibility
Different double layer roll forming machines may have limitations when it comes to the types of materials they can effectively shape. Ensure that the machine you select is compatible with the specific metal materials you work with, such as steel, aluminum, or copper.
Customization Options
If your production requires frequent profile changes or customization, opt for a machine that offers quick and easy tooling changeovers. This will minimize downtime and increase overall efficiency.
Machine Durability and Reliability
Investing in a reliable and durable machine is crucial for long-term productivity. Look for machines built with high-quality materials and components that can withstand the demands of continuous production.
Safety Features
Ensure that the double layer roll forming machine is equipped with proper safety features to protect operators and prevent accidents. Safety mechanisms such as emergency stops, safety guards, and overload protection should be in place.
After-Sales Support and Service
Choose a reputable manufacturer or supplier that offers comprehensive after-sales support, including maintenance services, spare parts availability, and technical assistance. This ensures smooth operations and minimizes downtime in case of any issues.
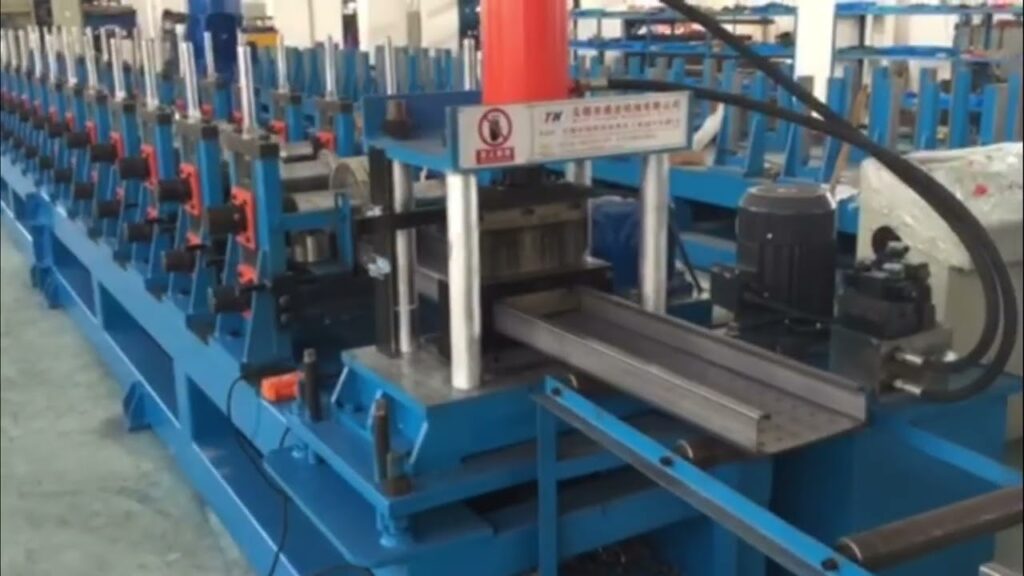
Maintenance and Care for Double Layer Roll Forming Machines
To maintain the optimal performance and longevity of your double layer roll forming machine, regular maintenance and care are essential. Here are some maintenance tips to keep in mind:
Cleaning and Lubrication
Regularly clean the machine to remove any dirt, debris, or metal shavings that may accumulate during operation. Additionally, ensure proper lubrication of moving parts to minimize friction and prevent premature wear.
Inspection and Adjustment
Perform regular inspections of the machine’s components, including roller dies, forming stations, and cutting mechanisms. Check for any signs of damage, misalignment, or excessive wear. Make necessary adjustments or replacements as needed.
Calibration and Alignment
Maintain proper calibration and alignment of the machine to ensure accurate profile shaping. Check and adjust the roller positions, cutting length, and any other relevant parameters to achieve the desired results.
Operator Training
Provide comprehensive training to machine operators to ensure they understand the proper operation and maintenance procedures. Proper handling and care by trained operators can significantly extend the lifespan of the machine.
Documentation and Records
Keep detailed records of maintenance activities, including cleaning schedules, lubrication routines, inspections, and any repairs or adjustments made. This documentation will help track the machine’s performance and identify any recurring issues.
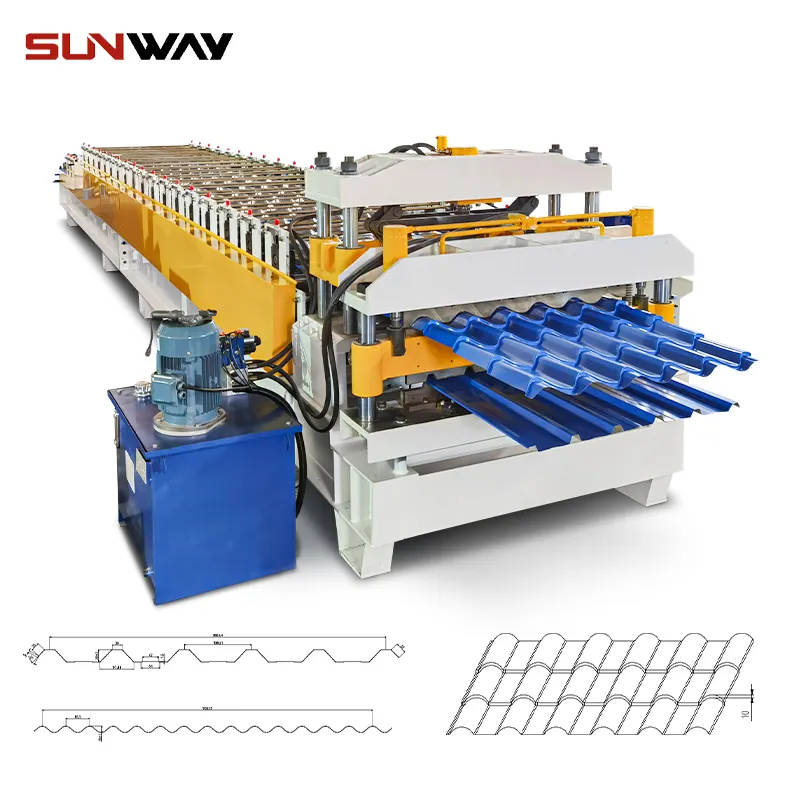
Future Developments in Double Layer Roll Forming Technology
As technology continues to advance, the field of double layer roll forming is not exempt from innovation. Here are some potential future developments to look out for:
Enhanced Automation
Automation plays a vital role in streamlining production processes. Future double layer roll forming machines may incorporate advanced robotics, artificial intelligence, and machine learning algorithms to optimize efficiency, reduce manual intervention, and improve overall accuracy.
Integration with IoT
The Internet of Things (IoT) has the potential to revolutionize manufacturing operations. Double layer roll forming machines may be equipped with IoT capabilities, allowing real-time monitoring, data analysis, predictive maintenance, and seamless integration with other production systems.
Advanced Material Compatibility
Research and development efforts are continually expanding the range of materials that can be effectively shaped using roll forming technology. Future double layer roll forming machines may offer increased compatibility with innovative materials, such as advanced composites or lightweight alloys, opening up new possibilities for various industries.
Energy Efficiency
With a growing emphasis on sustainability, future double layer roll forming machines may prioritize energy efficiency by incorporating smart power management systems, regenerative braking mechanisms, and other energy-saving technologies. This would contribute to reduced environmental impact and lower operational costs.
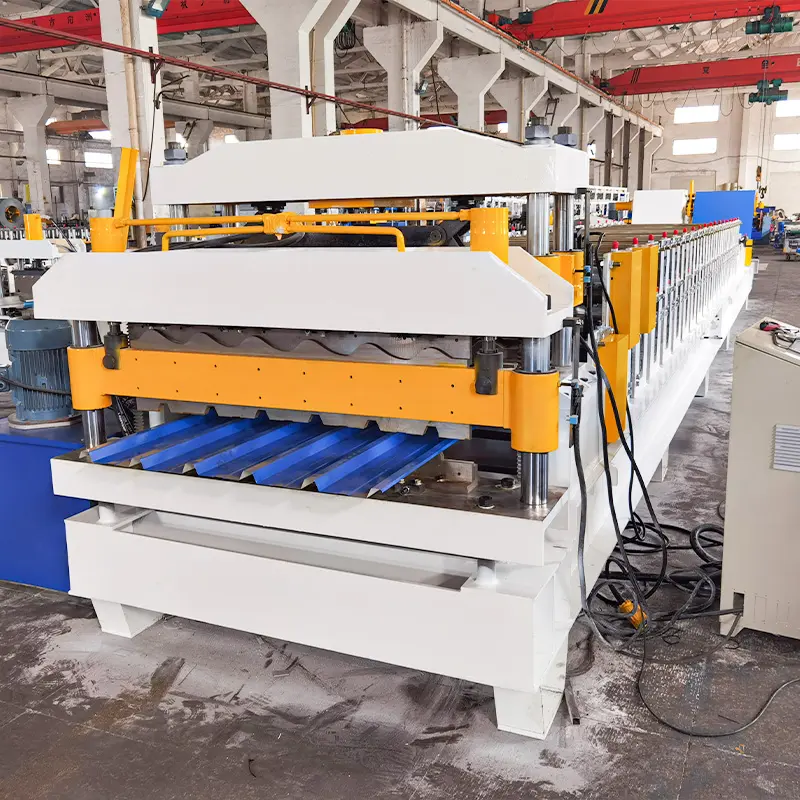
উপসংহার
Double layer roll forming machines have revolutionized metal sheet production by offering increased efficiency, versatility, and cost savings. These machines allow manufacturers to produce two different profiles simultaneously, reducing production time and labor costs while maintaining high-quality standards. By understanding the components, working principles, applications, and factors to consider when choosing a machine, businesses can make informed decisions to enhance their metal sheet production capabilities. As technology continues to advance, the future of double layer roll forming holds even greater potential for innovation, automation, and sustainability.
FAQs
Q1: Can double layer roll forming machines produce profiles with different dimensions?
Yes, double layer roll forming machines can be adjusted to produce profiles with varying dimensions. The machine’s roller positions, cutting length, and other parameters can be customized to meet specific size requirements.
Q2: Are double layer roll forming machines suitable for small-scale production?
Double layer roll forming machines are commonly used for medium to large-scale production due to their efficiency and output capabilities. However, they can still be used for small-scale production if the profiles and quantities justify the investment.
Q3: How long does it take to change the roller dies for different profiles?
The time required to change roller dies depends on the complexity of the profiles and the design of the machine. Some machines offer quick tooling changeovers, allowing operators to switch between profiles in a relatively short time, while others may require more extensive adjustments.
Q4: Can double layer roll forming machines work with non-metal materials?
Double layer roll forming machines are primarily designed for shaping metal sheets. While it may be possible to adapt them for certain non-metal materials, such as plastics or composites, the machine’s compatibility and performance with such materials may vary.
Q5: Are double layer roll forming machines suitable for prototyping purposes?
Double layer roll forming machines are generally used for mass production rather than prototyping due to the upfront tooling and setup costs involved. However, if the prototype quantities are significant or the profiles are part of a larger production run, they can still be considered as a cost-effective option.
Remember, choosing the right double layer roll forming machine for your specific needs, ensuring regular maintenance, and staying updated with future advancements in the field will help your business stay competitive and meet the evolving demands of the metal sheet production industry.