ভূমিকা
Standing seam roofs are a popular choice for residential and commercial buildings due to their durability and aesthetic appeal. These roofs consist of interlocking metal panels that provide excellent weather resistance and longevity. The process of manufacturing standing seam roof panels involves the use of specialized machinery known as standing seam roof panel roll forming machines. In this article, we will explore the various aspects of standing seam roof panel roll forming machines, including their types, benefits, working mechanism, and factors to consider when choosing one.
Understanding Standing Seam Roof Panel Roll Forming Machine
A standing seam roof panel roll forming machine is a specialized equipment designed to fabricate standing seam roof panels from metal coils. It utilizes a continuous process where the metal coil is fed into the machine, and the roll forming process transforms it into a finished standing seam roof panel. The machine consists of multiple rollers and cutting tools that shape and cut the metal as it passes through the machine.
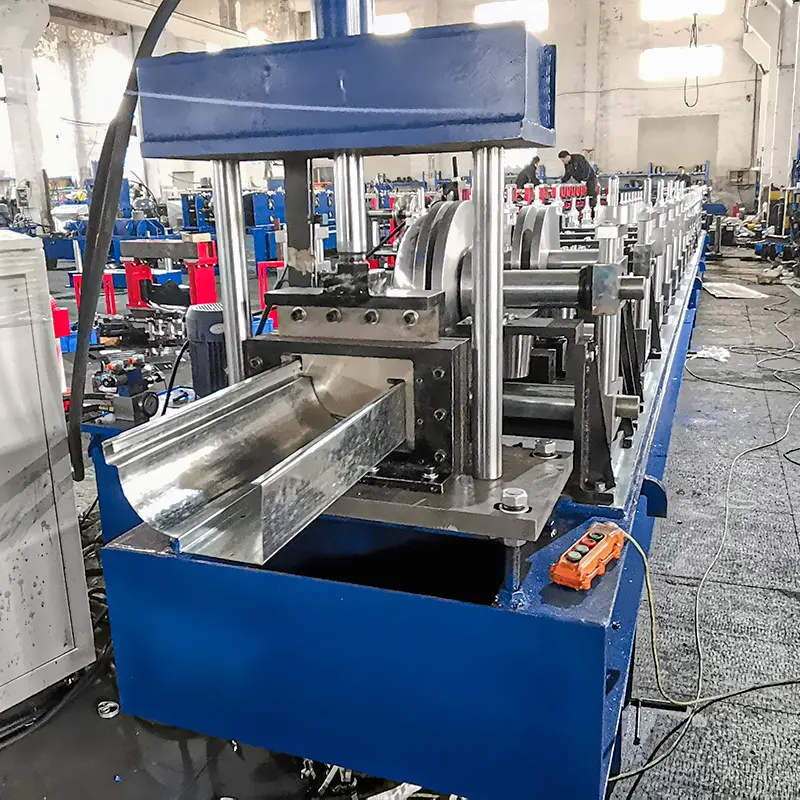
Benefits of Standing Seam Roof Panel Roll Forming Machine
Using a standing seam roof panel roll forming machine offers several advantages, including:
- Cost-effective production: Roll forming machines can produce standing seam roof panels at a high speed, reducing labor costs and increasing production efficiency.
- Customization options: These machines allow for easy customization of panel dimensions, profiles, and other design elements to meet specific project requirements.
- Consistent quality: The roll forming process ensures uniformity in panel dimensions and profiles, resulting in high-quality and precise roof panels.
- Time-saving: Roll forming machines can produce standing seam roof panels rapidly, enabling faster project completion times.
- Versatility: Standing seam roof panel roll forming machines can handle a wide range of metal materials, including steel, aluminum, and copper.
- Longevity: The roof panels produced by these machines are known for their durability and resistance to weather elements, ensuring long-term performance.
Types of Standing Seam Roof Panel Roll Forming Machines
There are several types of standing seam roof panel roll forming machines available in the market. The most common ones include:
Single Profile Standing Seam Roof Panel Roll Forming Machine
A single profile standing seam roof panel roll forming machine is designed to produce roof panels with a single profile, typically with a standing seam. This type of machine is suitable for projects where a consistent profile is required throughout.
Double Profile Standing Seam Roof Panel Roll Forming Machine
A double profile standing seam roof panel roll forming machine can produce roof panels with two different profiles, allowing for more design flexibility. This type of machine is ideal for projects that require alternating profiles or a combination of different profiles.
Snap Lock Standing Seam Roof Panel Roll Forming Machine
A snap lock standing seam roof panel roll forming machine is specifically designed to create snap lock standing seam panels. These panels have a unique interlocking mechanism that eliminates the need for separate clips or fasteners, making installation faster and more efficient.
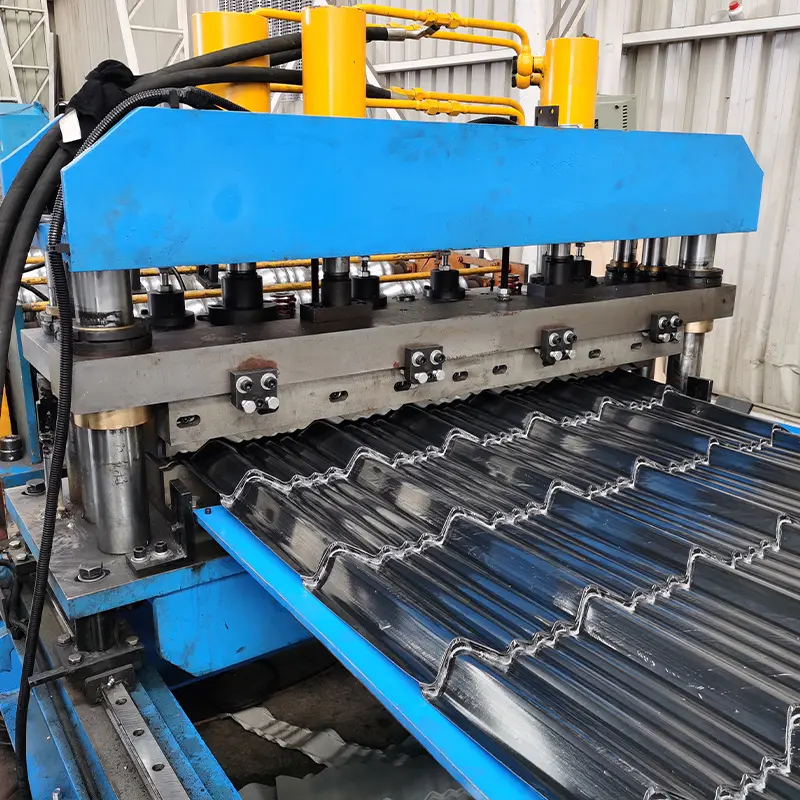
Key Features of Standing Seam Roof Panel Roll Forming Machine
When choosing a standing seam roof panel roll forming machine, it is essential to consider its key features, such as:
- Material compatibility
- Production speed
- Customization options
- Durability and reliability
- Ease of operation
- Safety features
- Maintenance requirements
Working Mechanism of Standing Seam Roof Panel Roll Forming Machine
The working mechanism of a standing seam roof panel roll forming machine involves several steps:
- Coil feeding: The metal coil is fed into the machine using a decoiler, which holds and controls the release of the coil.
- Material shaping: The coil passes through a series of rollers that gradually shape it into the desired profile, including the standing seam.
- Cutting and shearing: Once the panel reaches the desired length, cutting and shearing tools trim it to the required dimensions.
- Stacking and packaging: The finished panels are stacked and packaged for easy transportation and storage.
Factors to Consider when Choosing a Standing Seam Roof Panel Roll Forming Machine
When selecting a standing seam roof panel roll forming machine, it is crucial to consider the following factors:
Material Compatibility
Ensure that the machine can handle the specific metal materials required for your project, such as steel, aluminum, or copper.
Production Speed
Consider the production speed of the machine to meet project deadlines and optimize efficiency.
Customization Options
Choose a machine that offers flexibility in profile dimensions, panel width, and other design elements to accommodate various project requirements.
Durability and Reliability
Select a machine made of high-quality materials and components to ensure long-term durability and reliable performance.
Maintenance and Care for Standing Seam Roof Panel Roll Forming Machine
To maintain the optimal performance of a standing seam roof panel roll forming machine, regular maintenance and care are necessary. Some key maintenance practices include:
- Regular cleaning of the machine to remove debris and prevent build-up.
- Lubrication of moving parts to minimize friction and wear.
- Inspection and replacement of worn-out or damaged components.
- Calibration of the machine to ensure accurate panel dimensions and profiles.
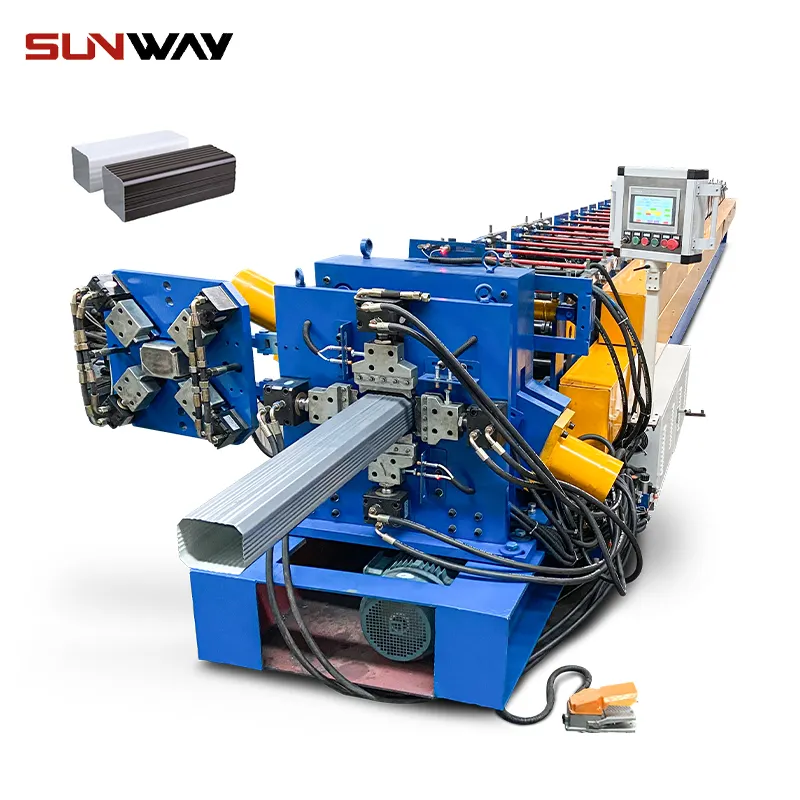
উপসংহার
Standing seam roof panel roll forming machines play a vital role in the efficient production of standing seam roof panels. These machines offer numerous benefits, including cost-effectiveness, customization options, and consistent quality. By understanding the various types, key features, working mechanism, and maintenance requirements of these machines, you can make an informed decision when selecting the most suitable one for your project.
Frequently Asked Questions (FAQs)
1. How long does it take to produce standing seam roof panels using a roll forming machine?
The production time depends on factors such as the machine’s speed, panel dimensions, and complexity. However, roll forming machines can typically produce standing seam roof panels at a rapid pace, significantly reducing production time compared to other methods.
2. Can a standing seam roof panel roll forming machine handle different metal materials?
Yes, most standing seam roof panel roll forming machines are designed to handle various metal materials, including steel, aluminum,copper, and more. It is important to ensure that the machine you choose is compatible with the specific metal material required for your project.
3. Are standing seam roof panels produced by roll forming machines durable?
Yes, standing seam roof panels manufactured using roll forming machines are known for their durability. These panels are designed to withstand harsh weather conditions, provide excellent protection against moisture, and have a long lifespan.
4. Can roll forming machines create different profiles for standing seam roof panels?
Yes, roll forming machines can produce a variety of profiles for standing seam roof panels. Whether you require a single profile, double profile, or snap lock profile, there are machines available that can cater to your specific design needs.
5. How often should a standing seam roof panel roll forming machine be maintained?
Regular maintenance is crucial to keep the roll forming machine in optimal condition. It is recommended to follow the manufacturer’s guidelines regarding maintenance schedules. Typically, routine cleaning, lubrication, inspection, and calibration should be performed periodically to ensure smooth operation and prolong the machine’s lifespan.