مقدمة
عندما يتعلق الأمر ب metal forming, two of the most commonly used techniques are roll forming and press braking. Both processes shape metal sheets into precise profiles, but they differ in speed, efficiency, cost, and suitability for different applications.
So, which one should you choose?
In this guide, we’ll compare roll forming vs. press braking في 2025, covering:
✅ How each process works
✅ Key differences in speed, cost, precision, and efficiency
✅ Best applications for each method
✅ Which industries rely on roll forming vs. press braking?
✅ Why roll forming is the preferred choice for high-volume production
Let’s dive in!
فهم التشكيل بالدرفلة
ما هو تشكيل اللفة؟
Roll forming is a continuous metal forming process that shapes sheet metal into long, uniform profiles using a series of roller stations. The material passes through multiple rollers that gradually shape it into the desired cross-section.
كيف يعمل التشكيل بالدرفلة
الخطوة | Process Description |
---|---|
1. Coil Loading | A metal coil is fed into the roll forming machine. |
2. Progressive Forming | The sheet passes through a series of rollers that gradually bend the metal into shape. |
3. Inline Cutting & Punching | The profile is cut to length و punched if necessary. |
4. Final Inspection & Packaging | The finished profiles are quality-checked and prepared for shipment. |
نصيحة محترف: Roll forming is best for high-volume, continuous production من uniform metal profiles.
Understanding Press Braking
What is Press Braking?
Press braking is a metal bending process that uses a هيدروليكي or mechanical press brake to bend metal sheets into specific angles. The metal is placed between a punch and die, which exert force to form the sheet into the desired shape.
How Press Braking Works
الخطوة | Process Description |
---|---|
1. Sheet Placement | A flat metal sheet is positioned on the press brake. |
2. Die & Punch Selection | The appropriate die and punch combination is chosen for the required bend. |
3. Bending Process | The press brake applies force, bending the sheet into the desired angle. |
4. Inspection & Adjustment | The formed part is checked for accuracy and adjusted if necessary. |
نصيحة محترف: Press braking is best for low-volume production و custom one-off bends.
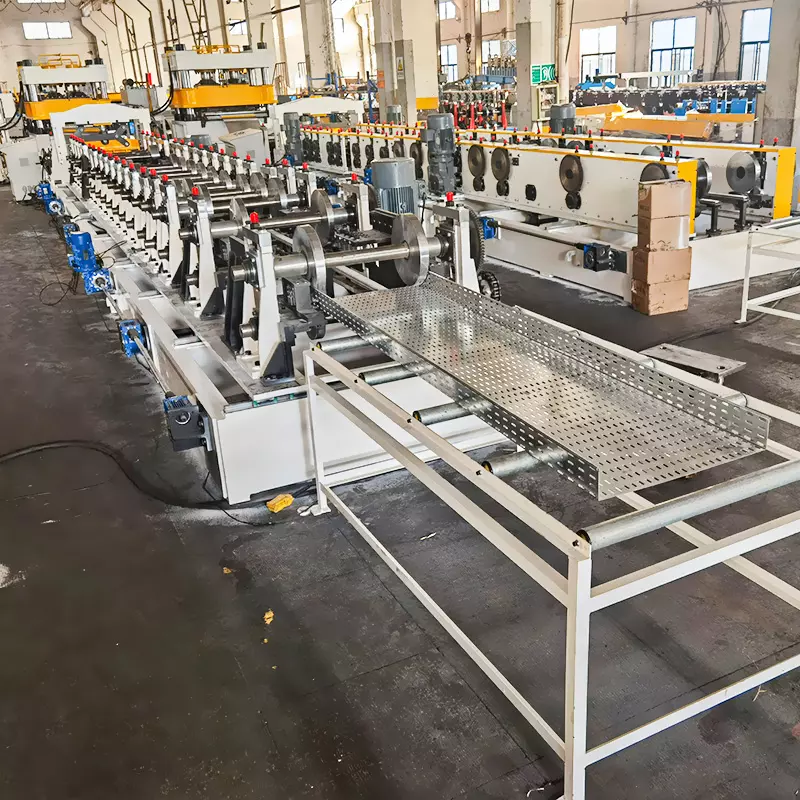
Roll Forming vs. Press Braking: Key Differences
الميزة | تشكيل لفة | الضغط على المكابح |
---|---|---|
سرعة الإنتاج | Continuous, high-speed production (up to 50m/min) | Slower, batch-based production |
Best for | الإنتاج بكميات كبيرة من uniform profiles | Low-volume, custom bends |
تكلفة الأدوات | Higher initial tooling cost but lower per-unit cost | Lower tooling cost but higher per-unit cost |
المرونة | Limited to pre-designed profiles | Highly flexible for custom bends |
Precision & Tolerance | Highly precise, minimal distortion in long profiles | Good for shorter sections, but less accurate for long profiles |
النفايات المادية | Minimal waste due to continuous process | More waste due to trial-and-error adjustments |
الأتمتة | Fully automated with inline cutting, punching, and welding | Requires manual adjustments |
Labor Intensity | Low labor requirement | High labor requirement |
الحكم:
- Roll forming is better for large-scale industrial production where speed, consistency, and cost-efficiency matter.
- Press braking is better for custom, small-batch, or prototype production where flexibility is required.
When to Use Roll Forming vs. Press Braking
Roll Forming is Best For:
✅ الإنتاج بكميات كبيرة (e.g., automotive, construction, solar industries)
✅ Long, uniform profiles (e.g., C & Z purlins, metal roofing, highway guardrails)
✅ Reducing material waste and labor costs
✅ Achieving high precision with minimal distortion
Press Braking is Best For:
✅ Low-volume, custom jobs (e.g., small fabrication shops, prototyping)
✅ Short-length metal components that require angular bends
✅ Quick setup with minimal tooling costs
If you need high-speed, cost-efficient production, go with roll forming. If you need flexibility for low-volume jobs, press braking is the better choice.
Industries That Use Roll Forming vs. Press Braking
الصناعة | تشكيل لفة | الضغط على المكابح |
---|---|---|
السيارات | Structural components, crash-resistant beams | Custom brackets, low-volume parts |
الإنشاءات | Metal roofing, wall panels, purlins | Custom trim, window frames |
أرفف ورفوف | Warehouse storage racks, uprights, beams | Custom shelf brackets |
الطاقة الشمسية | PV mounting structures, solar panel frames | Small mounting brackets |
الفضاء الجوي | High-strength structural components | Custom one-off parts |
نصيحة محترف: Roll forming is widely used in industries requiring mass production, while press braking serves more niche, low-volume applications.
Why Roll Forming is the Future of Metal Forming
As industries move towards automation, efficiency, and cost reduction, roll forming is becoming the preferred choice for large-scale manufacturers.
Advantages of Roll Forming Over Press Braking
✅ 50% faster production speeds
✅ 70% lower labor costs due to automation
✅ الحد الأدنى من نفايات المواد
✅ Inline processing reduces post-production work
✅ Perfect for industries with high-volume needs
Looking for a high-speed, precision roll forming machine? ماكينة صنواي العروض state-of-the-art roll forming solutions لـ global manufacturers.
Common Problems & Solutions in Roll Forming vs. Press Braking
Even with advanced roll forming and press braking technologies, manufacturers may encounter challenges such as material deformation, misalignment, and production inefficiencies. Addressing these issues early يضمن consistent quality, reduced downtime, and improved efficiency.
Troubleshooting Guide for Roll Forming vs. Press Braking
الإصدار | Roll Forming Cause & Solution | Press Braking Cause & Solution |
---|---|---|
تشويه الملف الشخصي | Misaligned rollers, incorrect pressure settings → Recalibrate rollers and adjust forming pressure | Incorrect punch and die selection → Use properly matched punch and die |
Material Wrinkling | Uneven material feeding → Ensure uniform material tension and adjust guide rolls | Over-bending of the sheet → Reduce bending force or adjust die clearance |
أبعاد غير متناسقة | Roller wear or incorrect CNC settings → Inspect rollers and recalibrate CNC programs | Manual setup errors → Use automated press brakes for higher accuracy |
Surface Scratches | Dirty rollers or improper lubrication → Clean rollers and apply anti-scratch coatings | Poor-quality punch/die or excessive force → Use high-precision tools and adjust force settings |
Slow Production Speed | Overloaded machine or incorrect material thickness → Optimize material input and machine settings | Manual bending sequence errors → Use CNC-controlled press brakes |
نصيحة محترف: عادي machine calibration and preventive maintenance can reduce errors by up to 60% و increase production efficiency significantly.
Future Trends in Roll Forming & Press Braking (2025 & Beyond)
ال metal forming industry is evolving rapidly, with automation, AI, and sustainability تشكيل مستقبل roll forming and press braking technologies.
Key Innovations for 2025
1. AI-Powered Quality Monitoring
- AI-driven real-time defect detection improves quality control.
- Reduces material waste and ensures consistent accuracy.
2. IoT-Enabled Smart Factories
- Machines are now integrated with cloud-based monitoringتمكين remote diagnostics and predictive maintenance.
- التحسينات production tracking and operational efficiency.
3. Servo-Driven Press Brakes & Roll Forming Machines
- يحسن speed control, accuracy, and energy efficiency.
- يقلل wear and tear on mechanical components, increasing machine lifespan.
4. Fully Automated Profile Adjustments
- Eliminates manual adjustments when switching between different profiles.
- CNC-controlled automatic profile changeovers reduce downtime and improve efficiency.
Upgrading to AI-powered roll forming and press braking technologies can increase production efficiency by up to 50%!
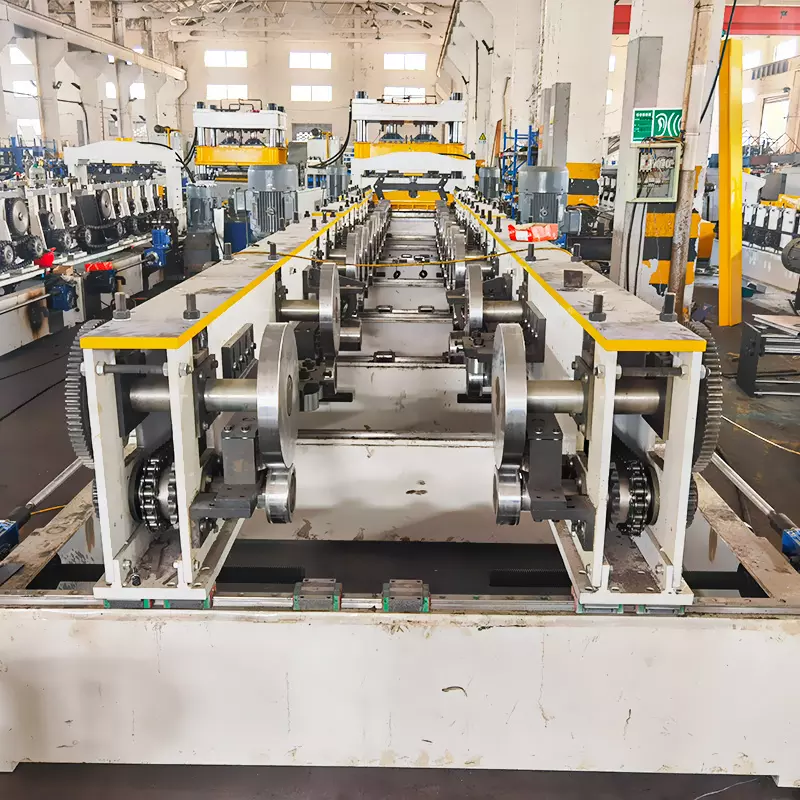
Automation in Roll Forming vs. Press Braking
Automation is revolutionizing roll forming and press braking, making them smarter, faster, and more cost-efficient.
Comparison of Automation Features in Roll Forming & Press Braking
Automation Feature | تشكيل لفة | الضغط على المكابح |
---|---|---|
CNC & PLC Control | Ensures precise profile formation with minimal waste | Fully automated bending sequences for accuracy |
AI-Based Defect Detection | Identifies defects in real-time, reducing material waste | Detects bending errors and corrects force distribution |
IoT & Remote Monitoring | Allows manufacturers to track machine performance remotely | Enables predictive maintenance and operational tracking |
Automated Profile Changeover | Reduces downtime when switching between profiles | CNC-controlled punch and die selection for multi-bend jobs |
Energy-Efficient Motors | Lowers operational costs and improves sustainability | Servo-driven systems enhance accuracy and speed |
Fully automated roll forming machines from ماكينة صنواي improve production efficiency by up to 40%!
Essential Maintenance Tips for Roll Forming & Press Braking Machines
مناسب maintenance يضمن extended machine lifespan و consistent production quality.
Maintenance Checklist for Roll Forming & Press Braking Machines
المهمة | التردد | الغرض |
---|---|---|
Lubricate Rollers & Bearings | أسبوعياً | Prevents wear and tear |
Check Roller & Die Alignment | شهرياً | Ensures accurate profile production |
Inspect Cutting & Bending Mechanism | ربع سنوي | Prevents defective cuts, bends, and misalignment |
Clean Machine Components | يومياً | Removes dust and debris that can affect performance |
Update Software & Calibration | Semi-Annually | Keeps automation functions optimized |
نصيحة محترف: Scheduled maintenance can extend machine lifespan by 50% و reduce failures by 70%.
FAQ: Roll Forming vs. Press Braking
1. Which method is better for high-volume production?
- Roll forming is superior for high-volume production due to its continuous process and automation capabilities.
- Press braking is better for low-volume or custom jobs that require manual flexibility.
2. Is roll forming or press braking more cost-effective?
- Roll forming has a higher initial tooling cost but a lower per-unit cost, making it more cost-effective for large-scale production.
- Press braking has lower initial costs but higher labor expenses and slower production rates, making it less efficient for mass production.
3. Which method produces more precise parts?
- Roll forming ensures higher precision for long, uniform profiles.
- Press braking is more precise for small, angular bends but can have variations in long sections.
4. Can roll forming replace press braking entirely?
- لا يوجد, because some industries require custom bends and low-volume production, which press braking handles better.
- However, roll forming is preferred for most industrial applications where uniformity and speed are critical.
5. What materials can be used in both methods?
- Both roll forming and press braking support steel, aluminum, stainless steel, and titanium.
- Roll forming is better for thinner materials, while press braking is ideal for thicker sheets.
6. Where can I buy a high-quality roll forming machine?
ل custom-built, high-speed roll forming machines, visit WUXI SUNWAY MACHINERY CO.، LTD.
الأفكار النهائية
Both roll forming and press braking have their advantages, but if you’re looking for high-speed, cost-efficient, large-scale production, roll forming is the superior choice.
WUXI SUNWAY MACHINERY CO.، LTD هو leading global manufacturer من ماكينات التشكيل بالدلفنة المصممة حسب الطلبتقدم advanced technology, expert support, and competitive pricing.
Want a high-quality roll forming machine? Contact us today!