По мере развития глобальной инфраструктуры растет спрос на эффективные и надежные системы электропроводки. Кабельные лотки, используемые для поддержки изолированных кабелей для распределения электроэнергии, связи и управления, играют важнейшую роль в современных строительных и промышленных проектах. Чтобы удовлетворить растущий спрос, Машины для формовки кабельных лотков стали краеугольным камнем производства, позволяя выпускать высококачественные кабельные лотки в промышленных масштабах.
Эти машины необходимы для создания лестничные лотки, перфорированные лотки, лотки со сплошным дном и лотки из проволочной сетки, среди прочих. Автоматизация процесса формовки валков позволяет производителям обеспечить точность, сократить количество отходов, повысить эффективность и предоставлять индивидуальные решения, отвечающие уникальным потребностям различных отраслей промышленности.
В этом подробном руководстве мы рассмотрим области применения, характеристики оборудования, производственные процессы, цены, мировые тенденциии почему Уси Sunway машины является надежным лидером в области технологии валковой формовки для производства кабельных лотков.
Что такое профилегибочная машина для кабельных лотков?
А Профилегибочная машина для кабельных лотков это специализированная промышленная система, предназначенная для производства компонентов для систем управления кабелями. Эти машины обрабатывают необработанные металлические листы или рулоны - как правило, из оцинкованная сталь, нержавеющая сталь или алюминий-и формируют из них точные профили, которые образуют конструктивные и функциональные элементы кабельных лотков.
Типы производимых кабельных лотков
- Лестничные лотки: Идеально подходит для кабелей большой емкости с улучшенным теплоотводом.
- Перфорированные лотки: Имеют прорези или отверстия для вентиляции и крепления кабелей.
- Лотки со сплошным дном: Обеспечьте полный корпус для кабелей, обеспечивающий максимальную защиту.
- Лотки с проволочной сеткой: Легкий и гибкий, используется в центрах обработки данных и коммерческих помещениях.
- Канальные лотки: Компактный и подходит для небольших кабельных трасс.
Автоматизируя производство этих типов лотков, рулоноформовочные машины помогают производителям эффективно и точно удовлетворять разнообразные отраслевые требования.
Области применения машин для формовки кабельных лотков
Универсальность Машины для формовки кабельных лотков позволяет им обслуживать широкий спектр отраслей. Вот как эти машины преобразуют системы управления кабелями:
1. Коммерческое строительство
- Пример использования: Производство кабельных лотков для офисных зданий, торговых центров и небоскребов.
- Почему это важно: Обеспечивает организованную прокладку кабелей для систем электропитания, связи и ОВКВ.
2. Промышленные объекты
- Пример использования: Производство сверхпрочных кабельных лотков для заводов, электростанций и нефтеперерабатывающих заводов.
- Почему это важно: Надежные решения для управления высоковольтными и промышленными кабелями.
3. Центры обработки данных
- Пример использования: Изготовление сетчатых лотков для структурированных кабелей в центрах обработки данных.
- Почему это важно: Обеспечивает эффективную прокладку кабелей, поддерживая воздушный поток и снижая накопление тепла.
4. Возобновляемая энергия
- Пример использования: Производство коррозионностойких лотков для солнечных электростанций и ветроэнергетических установок.
- Почему это актуально: Обеспечивает долговечность в суровых внешних условиях.
5. Транспортная инфраструктура
- Пример использования: Производство кабельных лотков для туннелей, аэропортов и систем метрополитена.
- Почему это необходимо: Обеспечивает огнестойкую и безопасную прокладку кабелей для критически важных объектов инфраструктуры.
6. Жилые проекты
- Пример использования: Производство компактных канальных лотков для небольших электропроводок.
- Почему это полезно: Предлагает экономичные решения для жилищных проектов и квартир.
Основные характеристики Wuxi Sunway кабельные лотки роликовые формовочные машины
Уси Sunway машины известна своими передовыми решениями в области валковой формовки, специально разработанными для индустрии кабельных лотков. Вот отличительные особенности их машин:
1. Многопрофильные возможности
- Что он поддерживает: Машины могут производить различные типы лотков, включая лестничные, перфорированные и лотки со сплошным дном.
- Почему это полезно: Позволяет производителям обслуживать несколько отраслей с помощью одной машины.
2. Высокоскоростное производство
- Производительность: Может производить до 20-40 метров лотков в минутув зависимости от материала и сложности.
- Почему это важно: Отвечает требованиям большого объема строительных и промышленных проектов.
3. Универсальность материалов
- Поддерживаемые материалы:
- Оцинкованная сталь
- Нержавеющая сталь
- Алюминий
- Почему это важно: Позволяет производителям удовлетворять особые требования к проектам, такие как коррозионная стойкость или легкость конструкции.
4. Встроенная система перфорации
- Что он предлагает: Встроенные системы перфорации для создания пазов, отверстий или нестандартной перфорации.
- Почему это необходимо:
- Уменьшает необходимость во вторичных операциях.
- Обеспечивает точную и равномерную перфорацию для вентиляции и поддержки кабелей.
5. Настраиваемая оснастка
- Что это позволяет: Быстросменные системы оснастки для создания нестандартных профилей, соответствующих уникальным конструкциям кабельных лотков.
- Почему это ценно: Поддерживает инновации и гибкость производителей на конкурентных рынках.
6. Интеграция IoT и автоматизации
- Что это дает: Мониторинг в режиме реального времени, автоматическая настройка и обнаружение ошибок с помощью технологии IoT.
- Почему это изменит игру:
- Повышает эффективность производства.
- Сокращает время простоя и количество отходов.
- Предоставляет действенные сведения для предиктивного обслуживания.
7. Совместимость с огнестойкими покрытиями
- Что это дает: Оборудование для обработки предварительно покрытых материалов с огнестойкими свойствами.
- Почему это важно: Поставляет компоненты, отвечающие стандартам безопасности для критически важных инфраструктурных проектов.
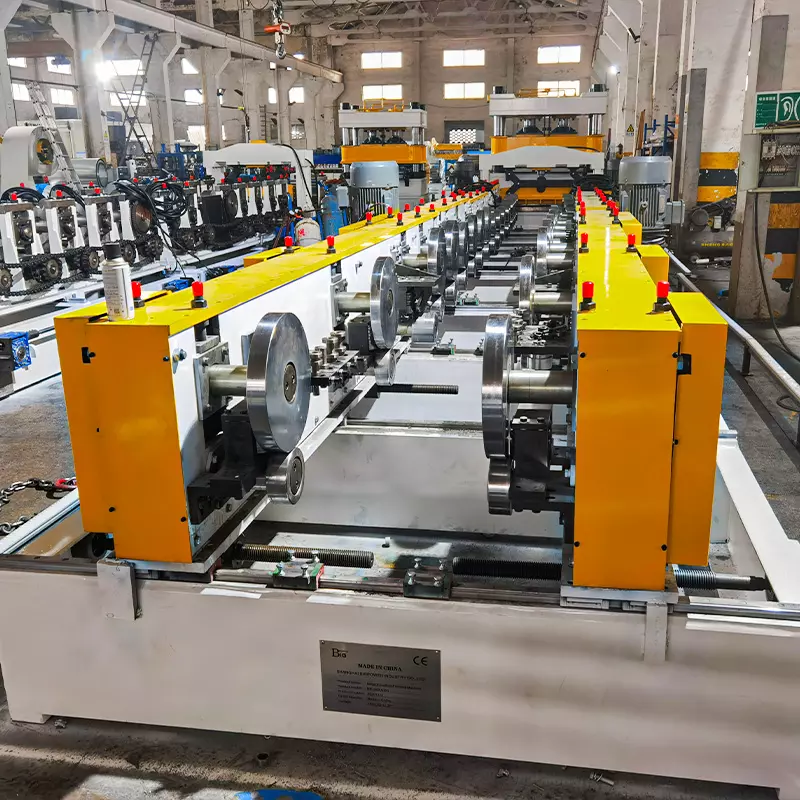
Производственный процесс машины для формовки кабельных лотков
Процесс производства кабельных лотков разработан таким образом, чтобы обеспечить точность и эффективность на каждом этапе. Вот обзор типичного рабочего процесса:
1. Загрузка материала
- Металлические катушки установлены на станке разматыватель, который подает материал в систему.
2. Выпрямление
- Система выравнивания обеспечивает ровный и бездефектный материал перед поступлением на участок формовки рулонов.
3. Формование рулонов
- Материал проходит через ряд роликов, которые придают ему нужный профиль.
4. Перфорация
- Интегрированные системы создают прорези, отверстия или перфорацию по желанию заказчика.
5. Резка по длине
- Высокоточные системы резки обрезают профили до нужной длины.
6. Проверка качества
- Готовые компоненты проверяются на точность размеров, качество обработки поверхности и соответствие промышленным стандартам.
7. Штабелирование и упаковка
- Заполненные лотки укладываются в штабель и подготавливаются к транспортировке или дальнейшей сборке.
Цены на Оборудование для формовки кабельных лотков
Стоимость Профилегибочная машина для кабельных лотков зависит от его характеристик, производственных мощностей и возможностей настройки. Ниже приведены общие цены для 2025 года:
Тип машины | Возможности | Диапазон цен (USD) |
---|---|---|
Стандартные машины | Производство основного профиля | $100,000–$250,000 |
Передовые машины | Высокоскоростной и многопрофильный вывод | $250,000–$500,000 |
Настраиваемые машины | Включая перфорацию, IoT и автоматизацию. | $500,000–$750,000 |
Для получения подробной информации о ценах и возможностях финансирования обращайтесь Уси Sunway машины.
Тенденции рынка машин для формовки кабельных лотков в 2025 году
Рынок кабельных лотков ожидает значительный рост, обусловленный развитием электротехнической инфраструктуры и строительства. Вот тенденции, определяющие внедрение Машины для формовки кабельных лотков:
1. Расширение проектов по использованию возобновляемых источников энергии
- Тренд: Установки солнечной и ветряной энергетики стимулируют спрос на коррозионностойкие кабельные лотки.
- Как машины помогают:
- Материалы для обработки подходят для наружной среды.
- Изготовление индивидуальных профилей для уникальных энергетических проектов.
2. Рост числа центров обработки данных
- Толчок: Рост облачных вычислений и IoT стимулирует строительство центров обработки данных по всему миру.
- Почему это актуально:
- На рулоноформовочных станках производятся сетчатые лотки, идеально подходящие для структурированных кабелей в центрах обработки данных.
- Поддерживает масштабируемость для быстро растущих объектов.
3. Фокус на "умные города
- Возможность: Урбанизация и проекты "умных городов" увеличивают потребность в эффективной электрической инфраструктуре.
- Машинный вклад:
- Производите компактные и легкие лотки для городского применения.
- Поддержка инновационных разработок интеллектуальной инфраструктуры.
4. Акцент на пожарной безопасности
- Толчок: Ужесточение правил пожарной безопасности стимулирует спрос на огнестойкие кабельные лотки.
- Как машины помогают:
- Обрабатывайте предварительно покрытые материалы с огнестойкими свойствами.
- Обеспечение соответствия международным стандартам безопасности.
Вопросы и ответы о станках для формовки кабельных лотков
Вопрос | Ответ |
---|---|
Какие материалы могут обрабатывать эти машины? | Обычно используются оцинкованная сталь, нержавеющая сталь и алюминий. |
Какова средняя скорость производства? | Машины могут производить до 20-40 метров лотков в минутув зависимости от материала и сложности. |
Могут ли эти машины изготавливать нестандартные конструкции? | Да, станки Wuxi Sunway оснащены настраиваемой оснасткой для изготовления профилей по индивидуальному заказу. |
Каков типичный срок службы этих машин? | При надлежащем обслуживании эти машины могут прослужить 15-25 лет или больше. |
Являются ли эти машины энергоэффективными? | Безусловно! Станки Wuxi Sunway оснащены энергосберегающими двигателями и оптимизированными рабочими процессами. |
Соответствуют ли эти машины мировым стандартам? | Да, они разработаны в соответствии с ISO, IEC и другими международными стандартами. |
Предоставляется ли обучение при покупке? | Да, Wuxi Sunway предлагает комплексное обучение и послепродажную поддержку для всех клиентов. |
Соответствие мировым стандартам производства кабельных лотков
Для обеспечения безопасности, долговечности и эффективности кабельные лотки должны соответствовать международным стандартам. Машины для формовки кабельных лотков на Уси Sunway машины разработаны для производства компонентов, отвечающих этим строгим нормам, что дает производителям конкурентное преимущество на мировых рынках.
Стандарт | Регион | Требование |
---|---|---|
ISO 9001 | Глобальная | Устанавливает принципы управления качеством для производственных процессов. |
IEC 61537 | Глобальная | Регулирует производительность и безопасность систем управления кабелями. |
NEMA VE 1 | США | Определяет стандарты для систем кабельных лотков в промышленных и коммерческих условиях. |
EN 61537 | Европа | Рассматриваются механические и электрические свойства кабельных лотков. |
Маркировка CE | Европа | Подтверждает соответствие нормам безопасности и экологическим нормам ЕС. |
AS/NZS 3013 | Австралия/Новая Зеландия | Стандарт для огнестойких систем электрических кабельных лотков. |
Придерживаясь этих стандартов, Уси Sunway машины гарантирует, что ее рулоноформовочные машины производят кабельные лотки, отвечающие требованиям безопасности, качества и долговечности.
Преимущества рулонных формовочных машин для кабельных лотков с точки зрения экологичности
В современном мире, где все больше заботятся об окружающей среде, производители вынуждены внедрять экологически безопасные методы. Машины для формовки кабельных лотков Вносить свой вклад в эти усилия, сокращая количество отходов, оптимизируя использование материалов и поддерживая экологически чистые производственные процессы.
1. Точное использование материала
- Преимущество: Точное проектирование обеспечивает эффективное использование сырья, сводя к минимуму отходы.
- Воздействие на окружающую среду:
- Сокращает потребность в избыточном сырье.
- Снижает "углеродный след" производственных процессов.
2. Переработка вторичного сырья
- Что это дает: Машины могут перерабатывать вторичные металлы, такие как оцинкованная сталь и алюминий.
- Почему это важно:
- Поощряет повторное использование материалов, способствуя развитию циркулярной экономики.
- Снижает зависимость от невозобновляемых ресурсов.
3. Энергоэффективные операции
- Инновации: Усовершенствованные двигатели и оптимизированные рабочие процессы снижают потребление электроэнергии.
- Почему это важно:
- Снижение общего энергопотребления на производстве.
- Оказывает поддержку производителям в достижении целей устойчивого развития.
4. Прочность и долговечность компонентов
- Результат: Кабельные лотки, изготовленные на рулоноформовочных машинах, отличаются высокой прочностью и устойчивостью к износу и коррозии.
- Почему он устойчив:
- Продлевает срок службы кабельных систем, сокращая количество отходов.
- Сводит к минимуму необходимость частой замены.
5. Модульное производство
- Вклад: Станки производят компоненты для модульных систем кабельных лотков.
- Почему это важно:
- Модульные системы легче ремонтировать, изменять конфигурацию или расширять, что сокращает количество отходов.
- Способствует долгосрочному использованию и адаптации.
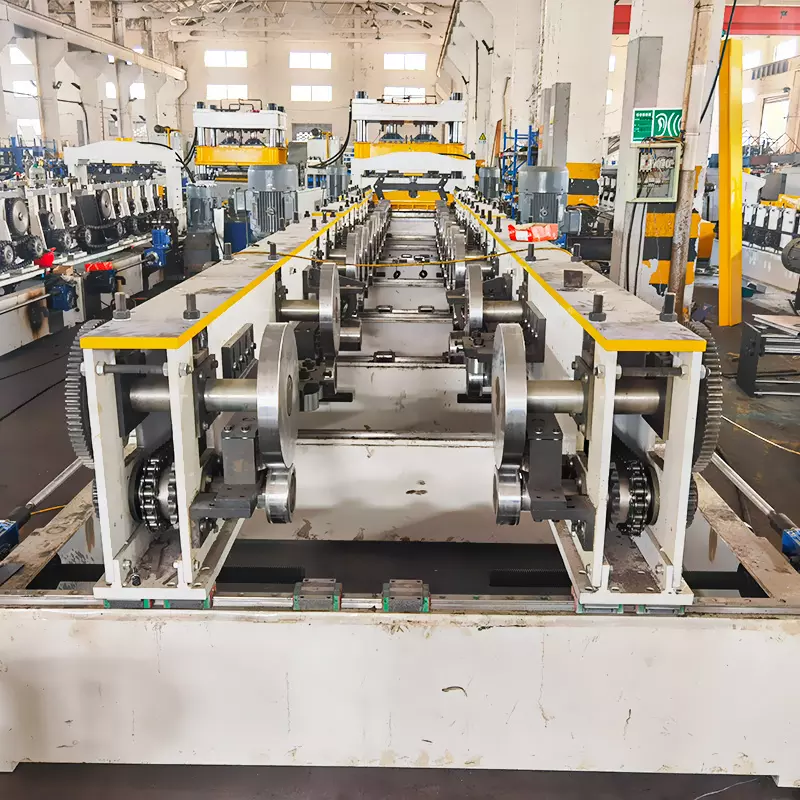
Реальные примеры применения машин для формовки кабельных лотков
Чтобы лучше понять влияние Машины для формовки кабельных лотковДавайте рассмотрим несколько реальных приложений, в которых эти машины преобразуют промышленность.
1. Проекты по возобновляемым источникам энергии
- Сценарий: Разработчику солнечной электростанции требуются коррозионностойкие кабельные лотки для наружной установки.
- Машинный вклад:
- Обрабатывает оцинкованную сталь для производства прочных и устойчивых к атмосферным воздействиям кабельных лотков.
- Создает специальные профили для оптимальной прокладки кабелей на открытом воздухе.
- Обеспечивает крупносерийное производство в соответствии с проектными сроками.
2. Строительство центров обработки данных
- Сценарий: Технологическая компания строит современный центр обработки данных с большими требованиями к прокладке кабелей.
- Машинный вклад:
- Производит сетчатые лотки, которые обеспечивают эффективную прокладку кабелей и воздушный поток.
- Обеспечивает точную перфорацию для отвода тепла.
- Легкие, но прочные лотки для удобной установки.
3. Транспортная инфраструктура
- Сценарий: Для модернизации системы метрополитена требуются огнестойкие кабельные лотки для туннелей и станций.
- Машинный вклад:
- Обрабатывает предварительно покрытые материалы с огнестойкими свойствами.
- Обеспечивает соблюдение международных стандартов безопасности.
- Компактные профили, подходящие для использования в условиях ограниченного пространства.
4. Промышленные заводы
- Сценарий: Химический завод нуждается в сверхпрочных кабельных лотках для поддержки высоковольтных кабелей в коррозионной среде.
- Машинный вклад:
- Создает прочные лестничные лотки с высокой грузоподъемностью.
- Обрабатывает нержавеющую сталь для максимальной устойчивости к коррозии.
- Поставляет прецизионные компоненты для бесшовной сборки.
5. Коммерческое строительство
- Сценарий: Подрядчик устанавливает кабельные лотки в высотном офисном здании.
- Машинный вклад:
- Перфорированные лотки для организованной прокладки кабелей.
- Обеспечивает легкость конструкции для удобства перемещения и установки.
- Поддержка настраиваемых профилей для соответствия конкретным требованиям проекта.
Расширенный раздел FAQ по станкам для формовки кабельных лотков
Вопрос | Ответ |
---|---|
Какие материалы могут обрабатывать эти машины? | Оцинкованная сталь, нержавеющая сталь, алюминий и материалы с предварительным покрытием. |
Какова средняя скорость производства? | Машины могут производить до 20-40 метров лотков в минутув зависимости от материала и сложности. |
Могут ли эти машины работать с индивидуальными проектами? | Да, станки Wuxi Sunway оснащены настраиваемой оснасткой для изготовления профилей по индивидуальному заказу. |
Насколько долговечны производимые кабельные лотки? | Лотки отличаются высокой прочностью, отличной устойчивостью к коррозии и износу, что обеспечивает длительный срок службы. |
Соответствуют ли эти машины мировым стандартам? | Да, они разработаны в соответствии с ISO, NEMA, IEC и другими международными стандартами. |
Каков типичный срок службы этих машин? | При надлежащем обслуживании эти машины могут прослужить 15-25 лет или больше. |
Предоставляется ли обучение при покупке? | Да, Wuxi Sunway предлагает комплексное обучение и послепродажную поддержку для всех клиентов. |
Являются ли эти машины энергоэффективными? | Безусловно! Они оснащены энергосберегающими двигателями и оптимизированными рабочими процессами для снижения потребления электроэнергии. |
В каких отраслях наиболее выгодно использовать эти машины? | Такие отрасли, как строительство, возобновляемые источники энергии, транспорт, центры обработки данных и промышленные объекты. |
Почему Wuxi Sunway Machinery является лидером отрасли
Уси Sunway машины зарекомендовала себя как надежное имя в индустрии рулонного формования, предлагая инновационные решения, разработанные с учетом уникальных потребностей производителей кабельных лотков. Вот почему они лидируют на рынке:
- Десятилетия опыта: Имея многолетний опыт, компания Wuxi Sunway понимает всю сложность производства кабельных лотков.
- Глобальное присутствие: Клиенты из Азии, Европы, Америки и других регионов доверяют компании Wuxi Sunway свои потребности в рулонном оборудовании.
- Инновационные технологии: Такие особенности, как интеграция IoT, высокоскоростное производство и настраиваемая оснастка, отличают Wuxi Sunway.
- Обязательства в области устойчивого развития: Машины разработаны в соответствии с экологичными технологиями производства, что позволяет сократить количество отходов и энергопотребление.
- Надежная поддержка: От установки до обучения и технического обслуживания, Wuxi Sunway обеспечивает комплексную поддержку клиентов.
- Универсальные решения: Их оборудование способно производить широкий спектр профилей кабельных лотков, отвечающих требованиям различных отраслей промышленности.
Заключение: Лидерство в производстве кабельных лотков
The Профилегибочная машина для кабельных лотков это переломный момент для производителей, желающих эффективно и экологично производить высококачественные кабельные лотки. Обеспечивая точность проектирования, высокую скорость производства и индивидуальный подход, эти станки позволяют предприятиям соответствовать требованиям современной электротехнической инфраструктуры.
Хотите совершить революцию в производстве кабельных лотков? Сотрудничайте с Уси Sunway машины сегодня и ознакомьтесь с их передовыми решениями в области рулонной формовки. Вместе мы проложим путь к более разумным и эффективным электрическим системам - по одному лотку за раз!