ए Z profile roll forming machine is an efficient equipment used to continuously bend and form metal coils into customized Z shaped profiles. This guide provides a comprehensive overview of Z profile roll forming technology, working principles, components, capabilities, suppliers, applications in various industries, operation and maintenance procedures.
What is a Z Profile Roll Forming Machine?
A Z profile roll forming machine continuously forms metal coil strips into ‘Z’ shaped sections using a series of consecutive roll stations. The forming rolls incrementally bend the strip through a series of bending steps to gradually shape it into the desired profile.
These versatile roll formers produce lightweight Z profiles that offer excellent strength for roofing, walling, structures and other industrial uses. Custom Z shapes with any dimensional specifications can be formed by adjusting the roll tooling design.
Benefits of Z Profile Roll Forming
- High production efficiency and speeds up to 100 m/min
- Consistent and high quality finished profiles
- Custom and complex shapes can be formed
- Low setup times for profile changeovers
- Applicable for high strength steels and advanced alloys
- Automated inline processing like punching and cutting
- Lower production costs compared to other methods
Industries Using Z Profile Roll Forming
- Construction and building
- Infrastructure and transportation
- Agriculture and farming
- Automotive and rail
- Aviation and aerospace
- Furniture and shelving
- Electrical and electronics
- Defense and armory
- Commercial applications
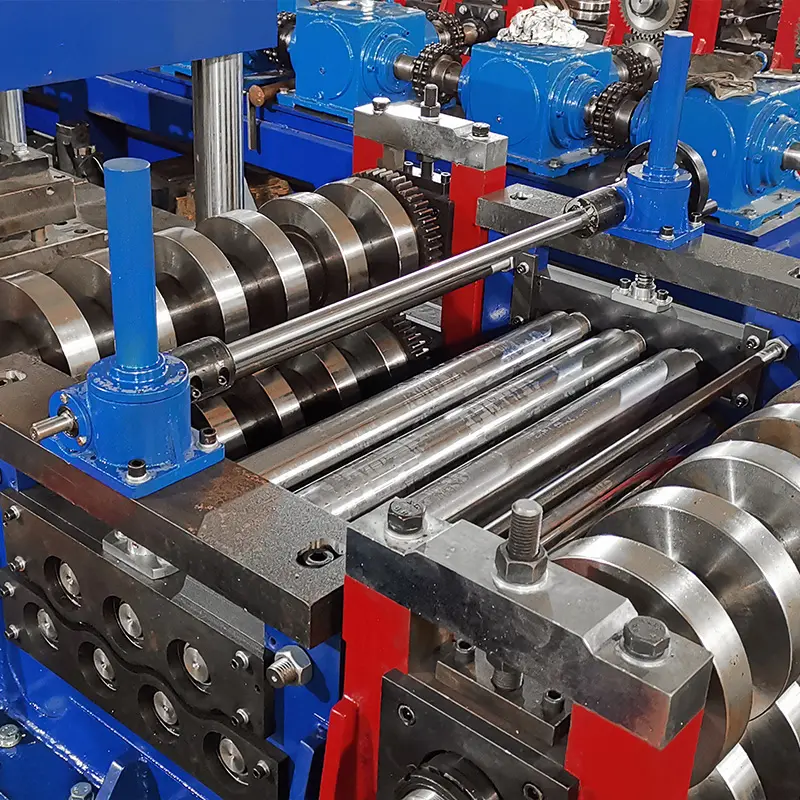
How Does a Z Profile Roll Forming Machine Work?
A Z profile roll forming line has three major functional zones – the decoiling and feeding unit, multiple roll forming stands, and the exit section with cutoff press. Here is an overview of the roll forming process:
1. Decoiling and Feeding
Metal coils of the required material and thickness are loaded onto powered decoilers. The strip is fed through a straightening mechanism to correct coil curvature and deformation stresses. An servo feeder control system pulls the pre-straightened strip into the roll forming section at the desired speed.
2. Roll Forming Section
The strip enters a series of rolling stations each with three rolls – upper, lower and wrapper rolls. As it passes through consecutive stands, the profile is gradually bent into the Z shape through small increments. Tooling on the rolls make stepwise bends until the final form is achieved. Integrated punching units allow holes and cutouts to be created in the profile during the forming process.
3. Finishing
At the exit end, features like final calibration, hole punching, embossing, marking and shearing can be incorporated in sequence. The cutoff press cuts the continuously produced Z profile into required lengths as per the order specification. The finished parts are stacked for dispatch or moved via conveyor for additional downstream treatments.
Main Components of a Z Profile Roll Forming Machine
Component | Function |
---|---|
Decoiler/Payoff Reel | Feed metal strips from coils |
Sheet Guiding System | Guide strip into line |
Feeder & Straightener | Pulls & straightens strip |
Roll Forming Stands | Main progressive bending |
Punches and Die | Makes cutouts on profile |
Shearing Unit | Cuts profile to length |
Conveyors and Stacking | Material flow management |
Control Panel | HMI controls the automation |
Types of Z Profile Roll Formers
Z profile roll forming equipment are available in standard and customized configurations based on production scale, automation needs, inline processing, and applications.
Table: Z Profile Roll Former Types
Type | Description |
---|---|
Standard | Pre-engineered models for common Z shapes |
Customized | Tailored to produce special profiles |
Manual | Basic versions with manual adjustments |
Automatic | Servo motor drives and control automation |
Batch Production | Lower capacity intermittent operation |
Mass Production | High speed continuous lines |
Single Component | Only roll forming section |
Complete Line | Decoiler, feeder, cutoff press included |
Plain Z Profile | Only forming rolls for basic profiles |
In-die Punching | Integrated hole punching while rolling |
Embossing | Surface pattern creation on profile |
Programmable Logic Control | Automated recipe set ups and changeovers |
Choosing the Right Z Profile Roll Former
Selection of optimal roll former type depends on key determinants:
- Annual production volume – Batch or mass production
- Profile shape complexity – Standard or custom profiles
- Secondary processing needs – Plain forming only? In-die punching? Calibration? Embossing?
- Level of automation – Manual, semi-automatic or fully automatic?
- Speed and efficiency requirements
- Available space and layout constraints
- Operator skill level for running and maintaining equipment
- Cost considerations – Initial investment, running costs & TCO
Consultation with experienced roll forming experts is advised to identify the best forming solution tailored for the production needs.
Z Profile Design Considerations
Profile design is a crucial precursor step before the roll forming process can begin. The key aspects that determine Z profile design include:
Application Requirements
The intended application of the Z profile sets the technical specifications and performance criteria that the component needs to fulfill. These application parameters prescribe shape, dimensions, thickness, mechanical properties and testing standards that should be met.
Functional Performance
Engineers analyze stiffness, buckling strength, loading capacity, deflection limits, service life estimating durability subject to cyclic fatigue, corrosive environments etc. The Z profile cross section geometry that satisfies structural rigidity, stability and weight targets is designed.
Manufacturing Constraints
The producibility limitations that are inherent to the roll forming process impose certain restrictions that should be accommodated:
- Minimum Bend Radius: Depends on material grade, thickness, internal stresses
- Angular precision: Gradual bends minimize springback deviation
- Strip widening/narrowing: Compensating web design
- Roll design aspects like minimum possible fillet radius, groove radius constraints, limiting angular increments between stands etc. should be considered.
The feasibility to successfully roll form the profile without defects should be assessed through numerical simulation modeling and prototype trials before committing to mass production.
Material Selection
Selection of appropriate coil material and thickness is vital depending on strength, durability, corrosion resistance requirements. Common materials include mild steel, galvanized steel, stainless steel and aluminum. High strength steels allow lightweight structural sections to be formed.
Coil Width Considerations
The Z profile width determines the required coil strip width that should be sourced. Narrower coils are cheaper, more readily available and easier to consistently feed at high speeds without drifting. Excessive strip widening in the roll forming process should be avoided and may require intermediate slitting.
Cost Optimization
An optimal balance between performance and production cost must be achieved through value analysis and engineering. Simpler shapes, common tooling, higher yields and productivity translate to lower overall manufacturing expenses.
-
Highway Guardrail End Terminal Forming Machine
-
Highway U/C Post Roll Forming Machine
-
2 Waves Highway Guardrail Roll Forming Machine
-
3 Waves Highway Guardrail Roll Forming Machine
-
वाइनयार्ड पोस्ट रोल बनाने की मशीन
-
ऑटो आकार बदलने योग्य सिग्मा शहतीर रोल बनाने की मशीन
-
विद्युत कैबिनेट फ्रेम रोल बनाने की मशीन
-
दीन रेल रोल बनाने की मशीन
-
दो लहरें राजमार्ग रेलिंग मशीन
Z Profile Roll Forming Process Capabilities
Modern Z profile production lines offer flexible and efficient forming capabilities to create high quality products:
Table: Z Profile Roll Forming Features
Feature | विवरण |
---|---|
Materials | Mild steel, HSS, stainless steel, aluminum alloys |
Thickness Range | 0.3 mm to 8 mm |
Width Range | 50 mm to 2500 mm |
Lengths | Up to 30 m long profiles |
Speed | Up to 100 meters per minute |
Tolerances | Dimensional accuracy within ±0.5 mm |
Surface Finish | Smooth, markings within 40 microns |
Corner Radii | As low as 1 mm attainable |
Hole Punching | Round, slotted and complex cutouts |
In-line Processing | Embossing, labeling, annealing, bending, packing |
Changeover Time | 10 mins with preset roll sets |
Range of Shapes | C, U, Z, V, Omega and custom asymmetric |
Secondary Operations | Cutting, drilling, welding, coating etc. |
With versatile tooling designs and precision roll form equipment, complex custom shapes with strict tolerances can be reliably mass produced.
Applications of Z Profiles
The lightweight yet strong structural Z sections serve varied applications across industries:
Building & Construction
- Wall Panel Framing
- Roof Trusses & Purlins
- Building Facades
- Steel Structures
- False Ceilings
- Partition Framing
- Scaffolding
Infrastructure
- Electrical Poles
- Telecom Towers
- Railway Sleepers
- Road Signs and Signals
- Drainage Channels
- Crash Barriers
- Transmission Towers
Automotive
- Chassis and Axle Beams
- Side Impact Beams
- Seat Frames
- Towing Equipment
Rail and Mass Transit
- Car Body Structures
- Interior Paneling
- Luggage Racks
- Handrails and Grab Poles
Aviation and Aerospace
- Aircraft Body Frames
- Engine Cowlings and Nacelles
- Wings and Control Surfaces
Furniture
- Shelving Systems
- Table Legs
- Cabinet Racks
Appliances
- Washing Machine Drums
- Refrigerator Racks
- Oven Racks
Electrical Enclosure
- Control Panels
- Distribution Boxes
- Battery Racks
The thin-walled Z sections provide excellent strength-to-weight ratio for lightweight and sustainable design across diverse industries.
Suppliers of Z Profile Roll Forming Machines
Many international roll forming equipment manufacturers offer standardized or tailored Z profile production lines with supporting services:
Table: Leading Z Profile Roll Former Manufacturers
कंपनी | Location | Product Range |
---|---|---|
Formtek | USA | Custom roll lines for profiles, tubes |
सैमको मशीनरी | Canada | Machines up to 100 m/min speeds |
Rollvis | Germany | Complete high speed roll lines |
Gasparini | इटली | Custom roll design and production |
Botou Xianfa | China | Box & C/U/Z roll forming lines |
Jouanel | फ्रांस | Roll tooling and profile design |
Reco | इटली | Steel, aluminum & special alloys |
Form Process Engineering | भारत | Machines for Roofing, Decking |
Voestalpine | Austria | High speed 27+ station lines |
Bradbury | USA | Leading supplier since 1956 |
Shanghai Metal Corporation | China | Affordable small production lines |
These established manufacturers offer standardized as well as custom engineered Z profile forming solutions backed by commissioning, operator training as well as maintenance support.
Cost Considerations
Turnkey Z profile production lines are premium roll forming equipment with capital investment ranging from:
- Basic – $35,000 to $55,000
- Standard – $65,000 to $120,000
- High speed – $150,000 to $350,000
- Fully automated – Over $500,000
The expenditure depends on production rate, level of automation, secondary processing like punching and material conveying mechanisms. Production volume, cost of raw materials, maintenance, and energy consumption determine the operating costs. Hence both CAPEX and OPEX should be evaluated during equipment selection.
Installing a Z Profile Roll Forming Line
The foundation layout and site preparation are key prerequisites before installing a roll forming system:
- A leveled concrete floor with sufficient load bearing strength is constructed.
- The required space for the roll former (length x width x height) is prepared by considering the decoiler, roll stands and exit press dimensions.
- Infeed and outfeed areas for the coils and finished products are allocated.
- Power supply lines (voltage, max load) are routed as per electrical design.
- Compressed air lines are laid out for pneumatic components as needed.
The machine is delivered in completely assembled or semi knock-down condition. Mechanical assembly and positioning is carried out followed by electrical connections and pneumatic fittings. A test run confirms correct functioning after which operator training is conducted. The line is then ready for commencing production after tool trials and setup.
Operation of Z Profile Roll Lines
Efficient functioning of the Z profile forming line depends on standardized operating procedures for:
Daily Startup
- Visual check of all guards, safety devices
- Lubricating roll bearings, sliding parts
- Checking electrical, pneumatic supplies
- Loading decoiler with required coil
- Feeding strip through machine
- Setting forming depth, punch offsets
- Speed and straightener settings
- Test run and first article inspection
Batch Production
- Selecting product recipe on HMI
- Monitoring strip tracking, thickness
- Quality checks after each batch
- Counter checks length, features
- Stack formed profiles on exit
- Ensure minimal wastage
Shift Change
- Record production data
- Material consumption data
- Any stoppages or defects
- Pending orders status
- Inspection of critical parts
- Handover status to next shift
Planned Shutdown
- Stopping production
- Retracting all parts to home position
- Cleaning from debris, oil, dirt
- Covering machine against weather, dust
Documented work instructions and training programs focus on productivity while preventing occupational hazards.
Maintenance of Z Profile Roll Lines
Preventative maintenance is vital for uninterrupted functioning and extended service life.
Table: Maintenance Aspects for Z Profile Roll Lines
Activity | Frequency | Method |
---|---|---|
Inspect Roll Bearings | Monthly | Ultrasonic check for wear |
Re-lubricate Bearings | 3 Months | Grease gun application |
Recondition Transfer Rolls | 6 Months | Hard chrome plating |
Roll Turning | Yearly | Precision grinding to restore OD |
Replace Worn Rollers | 2 Years | New roll set replacement |
Inspect Gearboxes | Yearly | Check vibration, noise levels |
Electrical Servicing | Yearly | Thermal checks, contact tightness |
Pneumatic Maintenance | Quarterly | Filter replacing, leak fixes |
Machine Alignment | Yearly | Laser alignment if vibration rises |
A full maintenance schedule covers daily, weekly, monthly and yearly upkeep activities including consumables replenishment, observations, measurements and necessary corrections.
Choosing a Z Profile Roll Forming Machine Manufacturer
The criteria for selecting a capable machinery producer are:
Technical Expertise
- Years of experience designing roll formers specifically
- In-house capabilities for machine design, build, automation
- Familiar with target industry applications and norms
- Able to engineer special profiles as per requirements
Quality & Testing
- Product quality certifications like ISO 9001
- Quality control checks and protocols during manufacturing
- Final machine testing and platen before dispatch
Customization Offering
- Flexibility to tailor standard models as needed
- Feasibility to design special tooling
- Integration of secondary processing modules
Service Support
- Responsiveness to technical queries
- Maintenance training for operators
- Assistance with breakdowns through service network
- Inventory of wearing spares and ability to ship replacements
- Upgrade support as production needs change
The manufacturer’s production facilities, installed base, client reviews and service infrastructure should be assessed during selection.
Pros and Cons of Z Profile Roll Forming Process
Advantages
- High production rates up to 100 meters per minute
- Excellent consistency and process control
- Low setup times for rapid changeovers
- Simplifies work flow with automated material handling
- Low maintenance equipment with long operational life
- Defect rates typically under 1%
- Tooling design flexibility allows any custom shape
- Capital and operating costs lower than press brakes or machining
Limitations
- Higher initial machine investment for automated lines
- Requirement of expert roll design and simulation engineering
- Precision ancillary equipment is needed for secondary processing
- Stringent quality monitoring of lubrication levels, wear etc.
- Limitations in finishing quality vs alternatives like extruded profiles
- Composite materials cannot be formed unlike steel and aluminum
If both advantages and limitations are weighed, roll formed profiles offer the optimal balance on performance, quality and costs for high volume production.
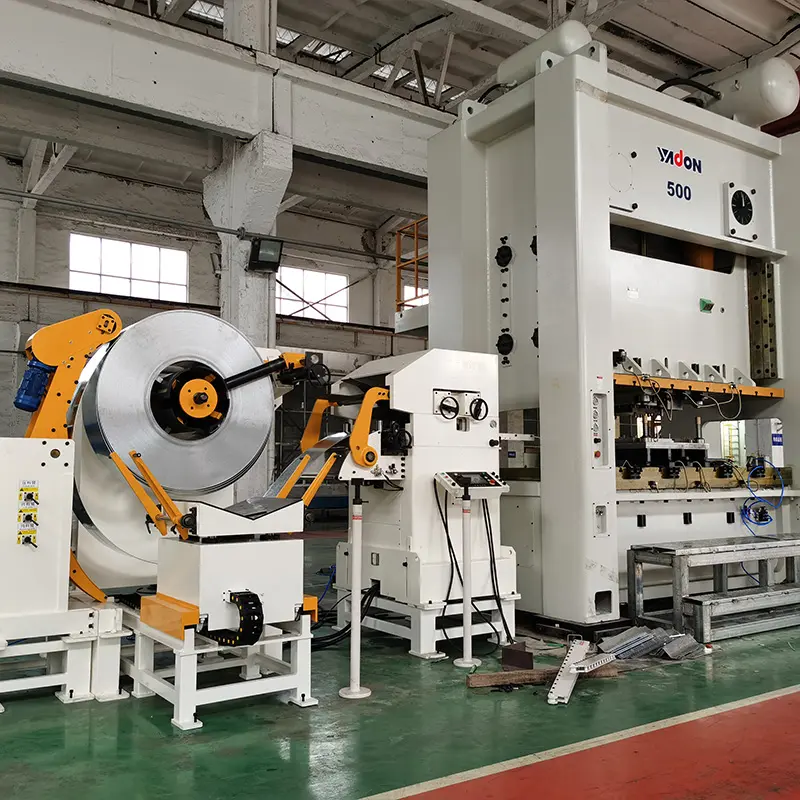
सामान्य प्रश्न
Q: What materials can be effectively Z profile roll formed?
A: Most structural and construction grade materials are suitable – low carbon steels, HSS, galvanized steels, stainless steels. Aluminum alloys 6xxx and 7xxx grade used if lightweight properties are required. Special alloys may need preliminary trials.
Q: How low can the inside bend radius be for a tight Z shape?
A: The minimum achievable inside bend radius is 1T where T is material thickness. However for commercial viability and preventing thinning defects, 2T to 3T is recommended.
Q: What tolerances are attainable on typical Z profile dimensions?
A: Roll formed components generally achieve dimensional accuracy within ±0.5 mm (±0.02 inches) or ±0.2% range along profile lengths. Precision secondary dies can further improve tolerance control.
Q: How are holes and notches punched consistently along the Z profile length?
A: Inline hydraulic piercing presses synchronized to the rolling speed punch holes and featured at set intervals with great location accuracy via indexing control.