रोल बनाने की मशीनें have become an essential tool for businesses that work with metal products. These machines are used to produce complex shapes and sizes of metal products quickly, efficiently, and with high precision. If you are new to the world of roll forming, you may have questions about how these machines work, their applications, and how to choose the right one for your business needs. In this post, we present The Ultimate Guide to Roll Forming Machine, a comprehensive resource that covers everything you need to know about roll forming machines. From the different types of machines to the roll forming process, maintenance and choosing the right machine for your business, we have got you covered. Let’s dive into The Ultimate Guide to Roll Forming Machine and discover how this technology can help your business grow.
रोल बनाने की मशीन के प्रकार
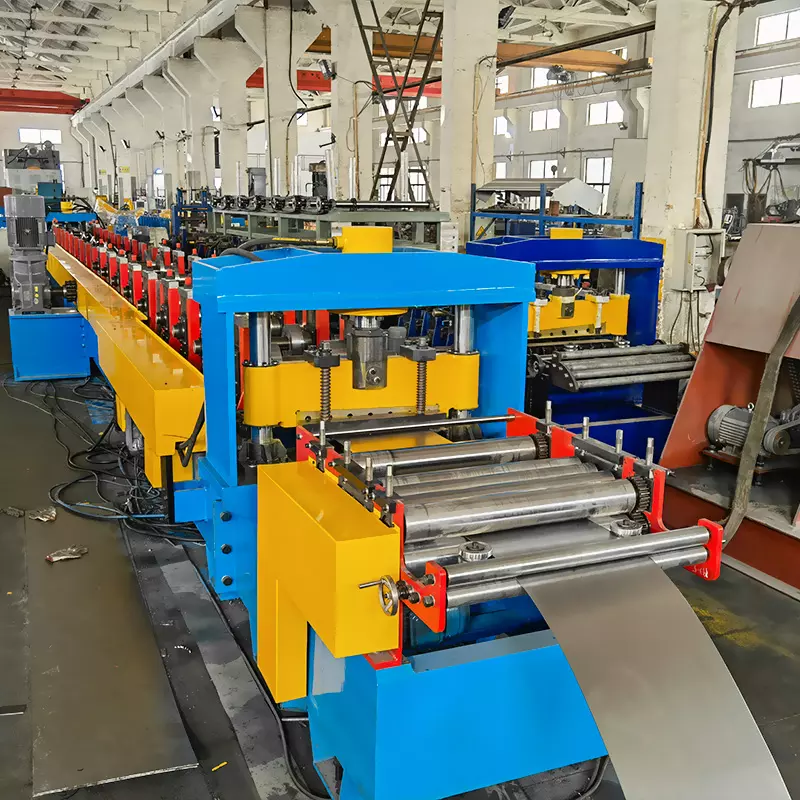
Roll forming machines come in different types, each with its own unique advantages and applications. Here are some of the most common types of roll forming machines:
- Single-pass Machines: As the name suggests, single-pass machines form a product in a single pass through the rolls. These machines are ideal for producing simple profiles with consistent cross-sections. They are often used in high-volume production settings to produce parts such as metal studs, tracks, and hat channels.
- Multi-pass Machines: Multi-pass machines have multiple sets of rolls that progressively form the product. These machines are capable of producing more complex profiles with varying cross-sections. They are often used in the automotive and aerospace industries to produce parts with precise shapes and dimensions.
- Duplex Machines: Duplex machines have two sets of rolls that operate simultaneously, forming the product on both sides. These machines are often used in the production of symmetrical parts such as Z-shaped or C-shaped profiles.
- Tandem Machines: Tandem machines consist of two or more roll forming mills, each forming a specific section of the product. These machines are ideal for producing long and heavy parts such as roofing panels, wall panels, and metal decking.
The choice of roll forming machine will depend on the specific application and production requirements. Single-pass machines are best suited for high-volume production of simple profiles, while multi-pass machines are ideal for producing complex profiles with tight tolerances. Duplex and tandem machines are used for more specialized applications where symmetrical or long and heavy parts are required.
Roll Forming Process
The roll forming process involves the continuous bending of a long strip of metal through a series of rollers, gradually forming it into the desired shape. Here are the main steps involved in the roll forming process:
- Material Selection: The first step in the roll forming process is to select the appropriate material for the product. Roll forming machines can be used with a variety of materials such as aluminum, steel, copper, and stainless steel.
- Material Preparation: Once the material has been selected, it is fed into the roll forming machine. The material is usually in the form of a coil, which is loaded onto an uncoiler and then fed through the machine.
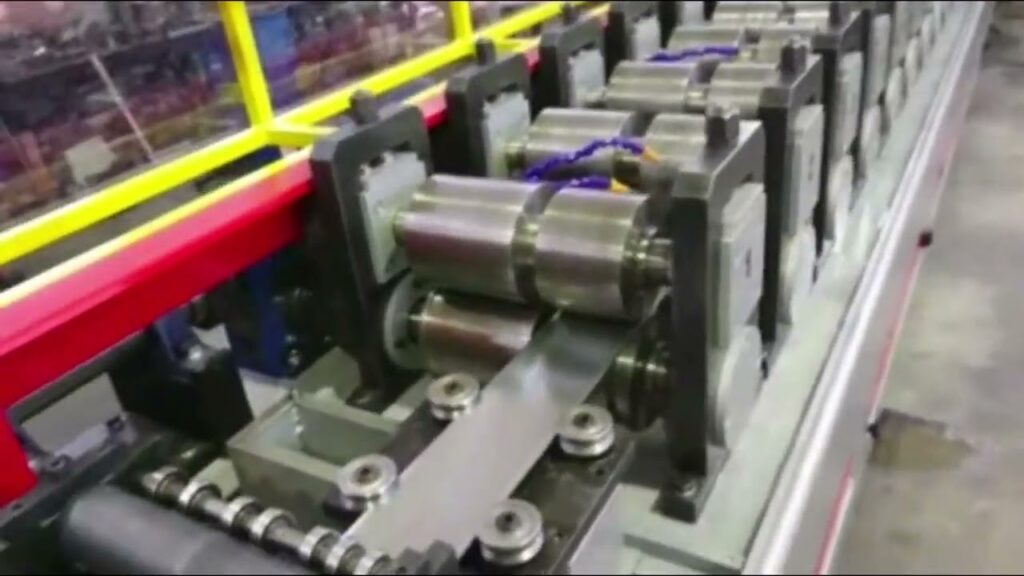
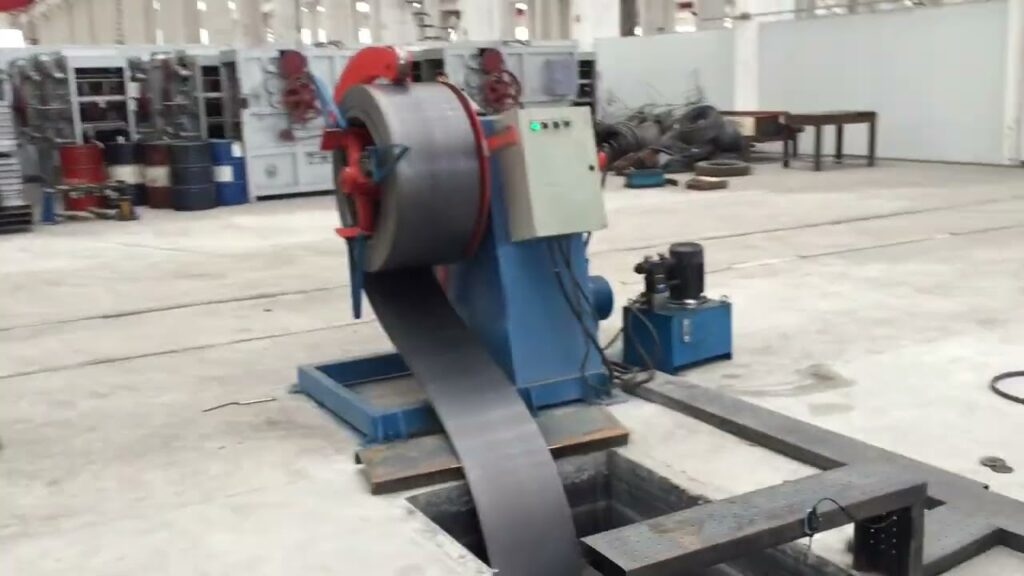
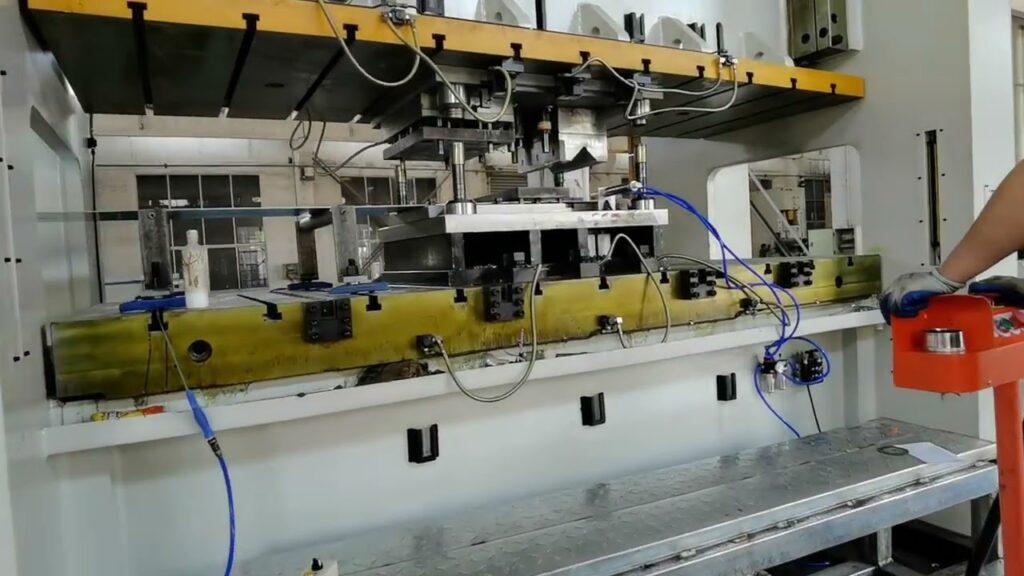
- Pre-Cut: In some cases, the material is pre-cut into the desired length before being fed through the roll forming machine.
- Forming: The material is fed through a series of rollers that gradually form it into the desired shape. The rollers are designed with specific contours that shape the material as it passes through.
- Cutting: Once the material has been formed, it is cut to the desired length using a cut-off die.
- Finishing: After the material has been cut, it may be finished using various techniques such as painting, powder coating, or galvanizing.
Several factors can affect the quality of the finished product in the roll forming process. The shape and contour of the rollers, the speed of the machine, and the properties of the material being formed can all impact the final product. Additionally, proper maintenance of the roll forming machine and the tooling is essential to ensure consistent quality.
In summary, the roll forming process involves the continuous bending of a long strip of metal through a series of rollers, gradually forming it into the desired shape. The selection of appropriate material, proper machine settings, and regular maintenance of the roll forming machine and tooling are essential to ensure consistent quality in the finished product.
Maintenance and Troubleshooting of roll forming machines
-
विद्युत कैबिनेट फ्रेम रोल बनाने की मशीन
-
दीन रेल रोल बनाने की मशीन
-
केबल सीढ़ी रोल बनाने की मशीन
-
पीवी माउंटिंग ब्रैकेट सी शेप प्रोफाइल रोल बनाने की मशीन
-
केबल ट्रे रोल बनाने की मशीन
-
पीवी माउंटिंग ब्रैकेट रोल बनाने की मशीन (एचएटी / ओमेगा प्रोफाइल)
-
पीवी माउंटिंग ब्रैकेट जेड शेप प्रोफाइल रोल बनाने की मशीन
-
सौर बढ़ते अकड़ चैनल रोल बनाने की मशीन
-
स्ट्रट चैनल रोल बनाने की मशीन
Proper maintenance is essential to ensure the optimal performance and longevity of roll forming machines. Here are some tips on how to maintain roll forming machines:
- Regular Cleaning: Clean the machine regularly to prevent the accumulation of dirt, dust, and debris. Wipe down the rollers, guides, and tooling with a cloth, and use compressed air to blow out hard-to-reach areas.
- Lubrication: Lubricate the machine regularly to prevent wear and tear on the rollers and tooling. Use the recommended lubricants for the machine, and make sure to apply them to the appropriate parts.
- Inspection: Conduct regular inspections of the machine to identify any issues or wear and tear. Check the rollers, bearings, tooling, and other parts for damage, and replace any worn-out parts.
- Calibration: Calibrate the machine regularly to ensure that it is producing the desired shapes and dimensions accurately. Check the machine’s settings and make adjustments as needed.
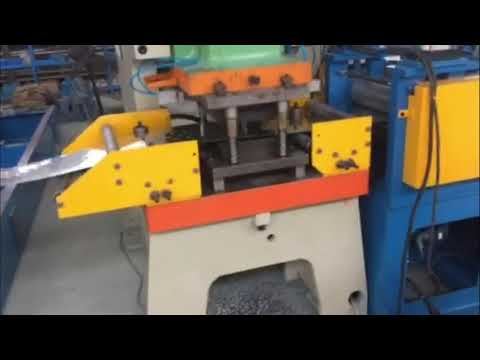
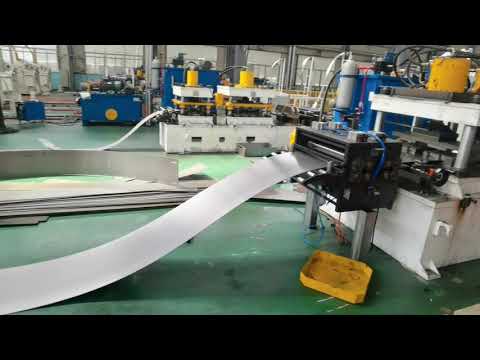
Here are some common issues that can arise with roll forming machines and how to troubleshoot them:
- Uneven Material Feed: Uneven material feed can cause the finished product to be inconsistent. Check the uncoiler to ensure that the coil is feeding evenly and adjust the tension as needed.
- Improper Cutting: Improper cutting can result in the finished product being too short or too long. Check the cut-off die to ensure that it is aligned properly and making clean cuts.
- Misaligned Tooling: Misaligned tooling can cause the finished product to be off-spec. Check the alignment of the rollers and tooling and make adjustments as needed.
- Roller Wear: Roller wear can cause the finished product to be inconsistent. Inspect the rollers regularly and replace them if they show signs of wear and tear.
In summary, proper maintenance is essential to ensure the optimal performance of roll forming machines. Regular cleaning, lubrication, inspection, and calibration can help prevent issues and prolong the lifespan of the machine. Common issues such as uneven material feed, improper cutting, misaligned tooling, and roller wear can be addressed through troubleshooting and regular maintenance.
Choosing the Right Roll Forming Machine
Choosing the right roll forming machine is essential for businesses to achieve optimal production efficiency and profitability. Here are some factors that businesses should consider when selecting a roll forming machine:
- Production Requirements: Consider the volume and complexity of the products to be produced. Determine the required production speed, accuracy, and tolerance, and choose a machine that meets those requirements.
- Machine Capacity: Consider the size and weight of the products to be produced, and choose a machine that can handle the required capacity. Machines with larger roll diameters and higher horsepower are capable of producing larger and heavier parts.
- Budget: Roll forming machines can range in price from a few thousand dollars to several hundred thousand dollars. Consider your budget when choosing a machine, and balance the initial investment with the potential long-term cost savings.
- Technical Support: Consider the level of technical support and after-sales service provided by the manufacturer. Choose a manufacturer that offers training, troubleshooting, and maintenance support to ensure the machine’s optimal performance.
In summary, businesses should consider production requirements, machine capacity, budget, and technical support when choosing the right roll forming machine for their needs. By carefully evaluating these factors, businesses can select a machine that meets their specific requirements and achieve optimal production efficiency and profitability.
In conclusion, the roll forming machine is an essential tool for businesses that work with metal products. With the knowledge gained from The Ultimate Guide to Roll Forming Machine, businesses can understand the different types of machines, the roll forming process, tooling, advantages, maintenance, safety considerations, and how to choose the right machine for their business needs. By following the maintenance tips and troubleshooting common issues, businesses can ensure optimal machine performance and consistent product quality. Choosing the right roll forming machine can also improve production efficiency and profitability. Roll forming machines offer businesses the ability to produce complex shapes and sizes of metal products quickly, efficiently, and with high precision.