ए U profile making machine is an important piece of equipment used to form U-shaped metal profiles for various construction and manufacturing applications. This comprehensive guide will provide detailed information on U profile machine types, working processes, components, suppliers, installation, operation, maintenance, and more.
Overview of U Profile Making Machine
A U profile making machine takes flat metal sheets or coils as input and processes them through a series of progressive bending and forming stations to output the desired U channel shape. Key features include:
- High production capacity up to 120 meters per minute
- Forming capacities from 0.5mm to 15mm metal thickness
- Motorized functions for automated control
- Interchangeable tooling for different profile sizes
- Safety features like emergency stop buttons
U profile machines utilize techniques like roll forming, press braking, or rotary bending to shape sheets into the U form consisting of a flat strip with two 90 degree bends along the edges. The versatile U shape allows for easy joining and construction applications.
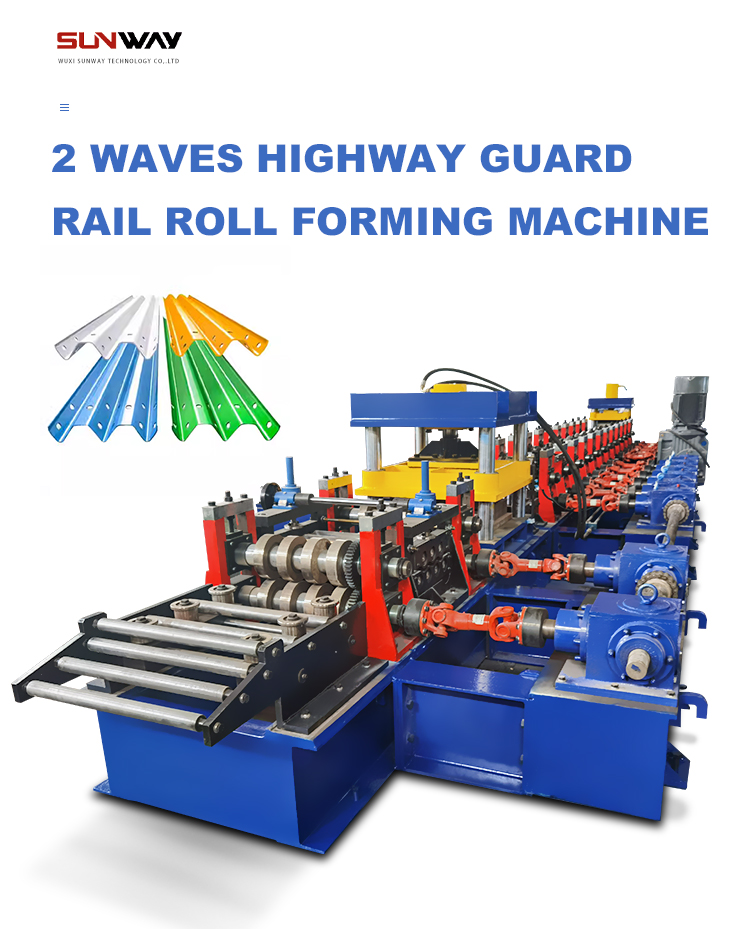
Types of U Profile Making Machines
There are three main types of U profile making machines:
रोल बनाने वाली मशीनें
Roll forming uses a series of roller dies to progressively shape the metal through each station into the U form. High output speed and accuracy are advantages.
Press Brake Machines
A press brake uses a vertical ram with punch and die blocks to make defined bends. Lower investment cost but slower than roll forming.
Rotary Bending Machines
Rotary bending uses wrapped dies and adjustable pressure bars to make longitudinal bends. Compact footprint but lower accuracy.
Machine Type | Method | Accuracy | Speed | Cost |
---|---|---|---|---|
रोल बनाना | Roller dies | High | High | High |
Press Brake | Punch + die | Medium | Low | Low |
Rotary Bending | Wrapped dies | Low | Medium | Medium |
Working Process of a U Profile Making Machine
The working process to form the U channel shape involves continuous feeding of the raw metal sheet and forming through progressive stations:
- Material Feeding: Sheet coils are loaded onto a de-coiler and fed into the first station.
- Edge Forming: The sides of the sheet get initial edge bends from the roller dies.
- पूर्व काटने: Cutting units pre-cut the sheet to finished U profile lengths.
- Final Forming: The sheet progresses through the last stations to complete the U shape profile creation.
- Output: The finished U profile pieces exit the final station ready for downstream processes.
Correct tooling setup and profile dimension settings are necessary to control the desired bending. Modern machines feature PLC touchscreens for easy control parameter input.
Major Components of a U Profile Making Machine
The main components of a U profile making machine include:
Uncoiling Unit: Loads and unrolls sheet metal coils up to 15 tons capacity
Feeding System: Motorized rollers move sheet through stations
Forming Sections: Bending dies and compression rollers
Hydraulic System: Generates precision ram pressure up to 160 tons
Cutting Unit: Pre-cuts sheets to length by saw or laser
PLC Control Panel: Menu-driven parameter selection
Conveyor System: Transports finished profiles to exit
Proper installation, settings calibration, and maintenance of these components ensures high performance and output. Most suppliers offer options to customize the line per application requirements.
U Profile Machine Design and Tooling
The tooling setup directly controls the final U profile dimensions produced. This includes:
- Die Entry: First bend angle and initial shaping
- Forming Rollers: Gradually form material into U channel
- Final Bending Dies: Finish angles and dimensions
- Cutoff Blades: Shearing or laser cuts to length
Common design options include:
- Closed Heights: 25mm to 300mm
- Flange Widths: 10mm to 80mm
- Web Depth: 10mm to 150mm
- Metal Thickness: 0.5mm to 15mm
- Temper Condition: Hot/cold rolled, galvanized, stainless, etc.
CAD software helps model custom profile specifications. Tooling must be precision CNC machined to handle high forming pressures without cracks or defects. Suppliers provide guidance on ideal design configurations.
-
नालीदार पैनल रोल बनाने की मशीन
-
लाइट गेज स्टील रोल बनाने की मशीन
-
सी सेक्शन ब्रेसिंग ओमेगा स्टोरेज रैक अपराइट पोस्ट रोल बनाने की मशीन
-
स्टील बॉक्स प्लेट रोल बनाने की मशीन बनाना
-
शेल्फ कॉलम के लिए बॉक्स बीम स्टील रोल बनाने की मशीन
-
पैलेट रैकिंग स्टेप बीम पी बीम रोल बनाने की मशीन
-
गोदाम शेल्फ ईमानदार रोल बनाने की मशीन
-
दीन रेल रोल बनाने की मशीन
-
ओमेगा शहतीर रोल बनाने की मशीन
Key Applications of U Profile Machines
U profile structures see heavy usage across sectors like:
- Construction: Wall studs, floor joists, roof rafters
- एचवीएसी: Ducting, air conduits
- Furniture: Racks, storage, frames
- Automotive: Chassis, trailers, railings
- Electrical: Cable trays, enclosures
- Agriculture: Greenhouses, livestock equipment
The versatile 90 degree open channel shape allows for shelving, joining plates, hanging hooks, and convenient fastening. Custom profiles enhance load bearing strength or aesthetic styling.
U Profile Machine Suppliers in India
Many Indian manufacturers offer U profile making equipment covering output from 10-15 tons per day to large >100 tons per day turnkey projects.
Supplier | Location | Capacity | Price Range |
---|---|---|---|
SSM Machines | Gujarat | Up to 100 TPD | ₹35 – 75 Lakhs |
Anshul Engineering | Punjab | Up to 60 TPD | ₹15 – 55 Lakhs |
Sree Engineering | Bangalore | Up to 120 TPD | ₹45 – 90 Lakhs |
Sahil Graphics | Mumbai | Up to 80 TPD | ₹25 – 70 Lakhs |
BNP Machines | Indore | Up to 50 TPD | ₹20 – 50 Lakhs |
Imported European brands likerestricted andrestricted offer high precision roll forming lines from ₹1.2 – 2.5+ Crores.
When sourcing suppliers, consider machine capacity, material thickness capability, overall accuracy, line integration features, and component quality. Reputed manufacturers provide performance guarantees plus after-sales service support.
Installation and Commissioning
Proper U profile machine installation by experts ensures smooth starting and operations. Key steps include:
- Site Preparation: Level concrete flooring to prevent vibration issues
- Equipment Unloading: Use forklifts, cranes for safe handling without damage
- Position Assembly: Arrange sections as per layout drawings
- Alignment Checks: Confirm tight tolerances between forming stages
- Electrical Connections: Power cables, control wires setup as specified
- Pneumatic Hookups: Compressor lines to rams/cylinders
- Trial Runs: Validate working parameters, performance before full production
This standardized process validates all components function safely at rated speeds, pressures, accuracies before final buyer approval.
U Channel Making Machine Operations
The typical U profile making line involves continuous automated sheet feeding and bending through inline stations:
- Loading: Worker mounts a 20 ton sheet coil using overhead crane
- Feeding: Decoiler feeds metal sheet into process flow
- Forming: Gradually forms U shape through roller dies
- Cutting: Shears finished pieces to length
- Unloading: Conveyor operator offloads cut profiles
Operators at each station monitor for any jams, errors via touchscreen PLC and ensure non-stop production. Periodic tooling maintenance checks are advised for quality control.
Maintenance and Safety
Routine maintenance activities ensure maximum uptime:
- Daily Checks: Sensor cleaning, oil/grease lubrication
- Weekly Checks: Hydraulic leaks, belt tensioning
- Monthly Checks: Forming tool wear checks
- Quarterly Checks: Motor alignment, wiring checks
- Annual Overhaul: Ram seal replacements, calibration
Lockout tagout procedures are mandatory when accessing internal areas to prevent accidental operation. Only certified technicians should attempt repairs.
Important factory safety guidelines:
- Enclose all pinch points with guards
- Ensure noise levels < 85 dB
- Provide anti-skid flooring
- Install emergency stop circuits
- Train workers on safety procedures
Proactive preventative maintenance minimizes unplanned outages and improves longevity.
Choosing the Right U Profile Making Machine
Key aspects to consider when selecting a U profile line:
Production Volume: Match capacity to monthly/annual requirement
Material Type: Mild steel, stainless steel, aluminum etc.
Sheet Thickness: Maximum metal coil thickness
Profile Size Range: Dimensional capabilities
Power Consumption: Utilities available
Space Constraints: Overall machine footprint
Budget: Balance functionality against cost
Buying Factors for U Profile Making Lines
Important factors when purchasing U profile production lines:
Technical Specifications
- Production Speed: 50 to 120 meters per minute
- Drive Motor Power: 15 kW to 55 kW capacity
- Forming Stations: 10 to 16 progressive stages
- Thickness Capacity: 0.5mm to 15mm metal coil
- Profile Width: 50mm to 300mm width range
- Cut Length Range: 3 meters to 12 meters adjustable
- Closed Height Size: 25mm to 250mm profiles
- Tooling Sets: 20 to 100+ quick changeover sets
Higher numbers generally mean bigger output volumes and size range flexibility.
Build Construction
- Steel Grade: Mild steel frame and stations suited for heavy industrial use
- Gearbox Rating: Helical gear type with AGMA 12+ quality grade
- Bearing Life: 50,000 hour rated or higher
- Cabinet Protection: IP54 or better electrical panel rating
- Paint Coating: Powder coating paintwork resists scratches, corrosion
- Component Brands: Premium brands like SKF, Schneider, Siemens indicate quality
Robust framework and branded components improve longevity and reliability.
Feature Set
- PLC Control System: Touchscreen programming interface
- Servo Motor Drives: For speed and tension feedback control
- Safety Circuits: Light curtains, emergency stops for protection
- Sensor Integration: Auto shutoff if jams detected
- Conveyors: Motorized rollers for automated flow handling
- डेकोइलर: 20 tons capacity with pendulum system
- Tool Change: Hydraulic assisted for quick size switching
- Portability: Locking castor wheels for movement flexibility
Advanced automation enhances ease of operation and control.
Vendor Credentials
- Years in Business: Experience level of 10 to 35 years
- Industry Certifications: ISO 9001 quality system registered
- Past Clientele: Reputable customer names
- Customization Ability: Offer flexible machine modifications
- R&D Investment: Continual improvements of models
- After Sales Service: Support for maintenance, spare parts
- Process Guarantees: Assured performance levels
Reliable manufacturers are transparent and offer post-purchase backup.
Pros and Cons of U Profile Making Machines
Advantages
- High hourly production up to 10 tons metal processed
- Consistent and accurate 90 degree bend forms
- Quick tooling changeover for different profiles
- Variable speed control for optimal shaping
- Automated operation with minimal manual work
- Low maintenance and operating costs
- Smaller footprint versus press brakes
Limitations
- Higher capital cost for complete roll forming line
- Fixed tooling shapes without custom bends
- Size constraints based on model limits
- Trained staff needed for programming and maintenance
- Lubrication and wear on forming dies over time
Applications of U Channel Profiles
U profiles find wide usage in industrial frameworks:
Building Construction
- Door and window frames
- Wall paneling
- Structural supports
- Roof trusses
- Foundation pilings
Automotive Industry
- Chassis and trailers
- Side crash barriers
- Roof rails
- Step boards
- Exterior paneling
Infrastructure
- Highway guide railings
- Traffic signage poles
- Bridge decking
- Warehouse storage racks
- Scaffolding
Agriculture/Farming
- Greenhouse frameworks
- Fences and animal cages
- Irrigation equipment
- Silo architecture
- Implements like rakes
Furniture
- Shelving units
- Cabinet carcasses
- Table frames
- Overhead lighting
Custom bent pieces add aesthetic appeal for decorative purposes. U channel profiles bring modular and adaptable design across all construction domains.
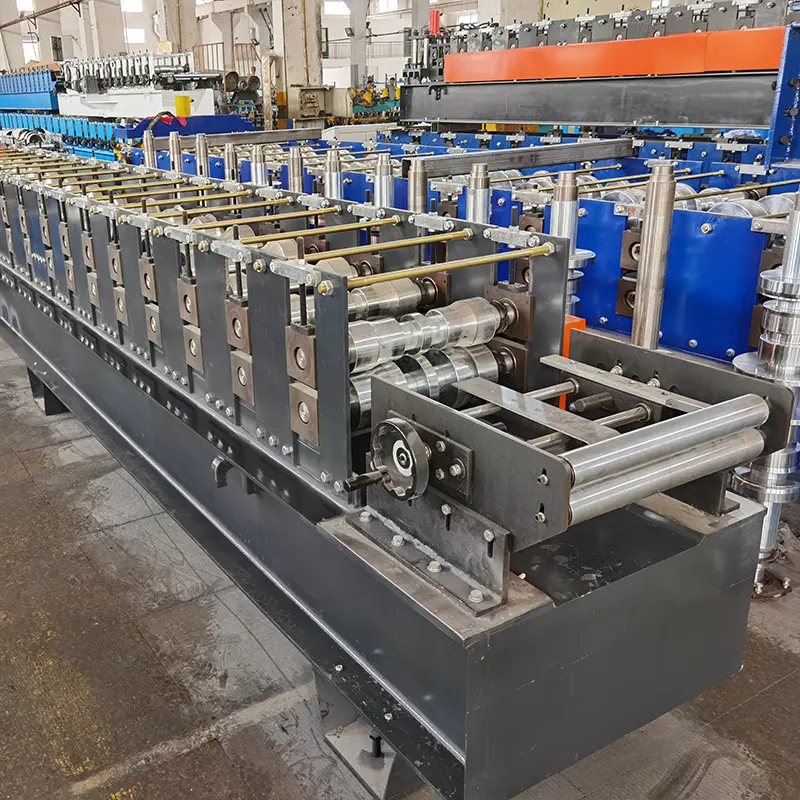
FAQs
Q: What sheet metal thickness does U profile machines handle?
A: Standard input material thickness ranges from 0.5mm to 12mm grade mild steel. Special models go up to 15mm thickness capacity with customized tooling.
Q: Can I get custom profile dimensions if needed?
A: Machine suppliers offer profile design services. By changing tooling dimensions and machine settings virtually any U width/depth within model limits can be formed.
Q: How long does it take to switch between U profile sizes?
A: Automated tool change systems allow quick changeover in 15-20 minutes between stored profile settings.
Q: What length of U channel can be formed?
A: Cutoff saw cut lengths range from 3 to 12 meters depending on machine cutting capacity and decoiler size equipped. Multi-cutoff models create longer panic door beams.
Q: What is the typical U profile machine price range?
A: Turnkey lines start around ₹35 Lakhs and go up based on output speed,decoiler capacity chosen. Imported European models exceed ₹2.5 Crores. Local suppliers offer balance of cost and production efficiency.
Q: Does the machine require any foundations?
A: Yes, reinforced concrete flooring helps dampen vibration. Leveling feet anchor units in place. Some portable models work without fixed mounting.
Q: What are common tooling maintenance activities?
A: Periodic inspection of wear, resurfacing excessively worn areas, hardening treatments to regain hardness, and replacing damaged components.
Q: What safety tests are required?
A: Suppliers handle detailed safety reviews including finger probe, light curtain checks, electrical system tests before customer handoff. Lockout tagout training is advised.
Q: What is the typical line life expectancy?
A: Approximately 15 years or more with preventative maintenance and timely parts replacement when required. Quality components improve longevity.