परिचय
Roll forming is a metalworking process used to bend metal strips into structural shapes. Flashing roll forming machines are a specialized type of roll former used to create metal flashing. Flashing is sheet metal installed to prevent water intrusion at roof valleys, around chimneys, windows, doors and other areas where water could enter a building. Flashing roll formers bend metal coil into various hemmed profiles that interlock shingle-style to cover gaps and joints. This article will discuss the benefits of flashing roll forming machines, how they work, common flashing profiles produced, applications and the future of this technology.
Benefits of Flashing Roll Forming Machines
Flashing roll formers provide several advantages over other flashing fabrication methods:
Efficient and Automated
Flashing roll forming is highly efficient and automated. Coiled aluminum or galvanized steel is fed into the machine which cold forms it into various profiles at linear speeds over 100 ft/min. This automated process eliminates many manual steps required with other fabrication methods. The increased efficiency leads to lower labor costs and faster production.
Consistent Quality and Accuracy
Roll formed flashing profiles feature extremely consistent dimensions and quality. Computer-controlled rollers precisely shape each profile eliminating deviations common with manual methods. The automation also improves accuracy for interlocking seams and edges. This consistent quality allows the flashing to be quickly installed for a tight, water-resistant fit.
Flexible Production
Flashing roll formers can produce various hemmed profiles by changing the rollers. This allows for flexible production of many flashing shapes from the same machine. It also enables custom profiles to be created as needed. Different colors and metals can also be run as required.
Lower Waste
Roll forming generates less waste versus other fabrication processes. The coil stock can be continuously formed to needed lengths without cutting and shaping individual pieces. Scrap is limited to the remnants at either end of production runs. Less waste means lower materials cost.
Safer Operation
Flashing roll formers are equipped with safeguards to protect operators. This includes barriers around moving parts and controls that automatically shut down the machine if problems arise. The automation increases safety by reducing direct worker involvement. This lessens injury risk compared to manual flashing production.
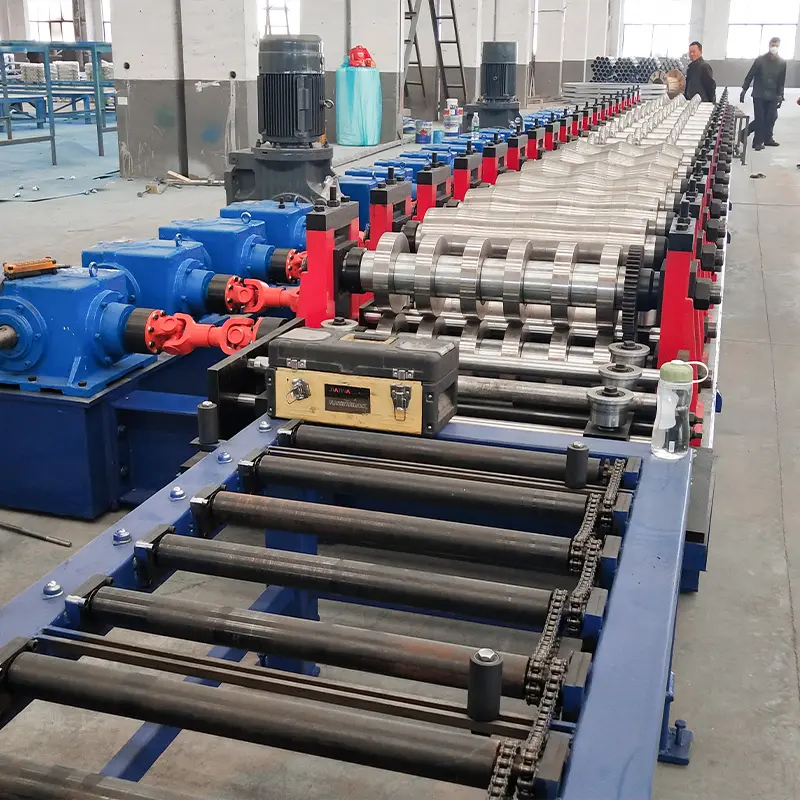
How Flashing Roll Forming Machines Work
Flashing roll forming machines bend and shape metal coils into various profiles using a series of progressively formed rollers. Here are the basic components and operation:
Coil Feed
Coiled aluminum or galvanized steel is loaded onto a powered unwind reel at the rear of the machine. The coil feed system steadily pulls the metal strip into the roll former.
Break Press
After the material is straightened, it passes through a pneumatic break press. This press lightly flattens the strip to remove coil memory and prepare the metal for forming.
Roll Forming Stations
The strip advances through a series of roll forming stations housed in a mill. Each station has a roller die set that incrementally forms the strip through a series of bends. The multiple bending steps shape the strip into the desired profile.
Shear Station
A pneumatic shear at the exit of the mill accurately cuts the formed profile to length as it emerges. A programmable controller times the shear to produce required lengths.
Conveyor Table
The cut lengths are deposited onto a powered conveyor table for operator removal. Sections can be offloaded manually or automatically for additional processing if needed.
The roll forming mill can be rapidly changed to produce different hemmed flashing profiles by switching out the roller dies. This flexible process allows efficient production of various shapes from a single machine.
Common Flashing Profiles Produced
Flashing roll formers can produce different profiles designed for specific waterproofing applications:
Drip Edge
Drip edge has a projecting lip that overhangs the roof edge. The drip edge diverts rainwater runoff into the gutter preventing it from infiltrating the roof covering.
Rake Edge
Rake edge flashing is installed along sloped roof edges. The profile fits over roof decking and under shingles providing a water-tight transition.
Valley Flashing
Valley flashing is used in roof valley areas. The open hemmed profile interlocks over overlapping roofing material for enhanced water runoff control.
Step Flashing
Step flashing features multiple tabs used to cover chimneys, walls and other roof penetrations. Each piece interlocks shingle-style ascending up the protrusion.
Counterflashing
Counterflashing secures over wall flashing at roof-to-wall transitions. The hemmed edge provides a finished look while sealing the flashing joint.
Custom Profiles
Custom hemmed shapes can also be produced. Special profiles are useful for unique architectural features that require distinctive flashing designs.
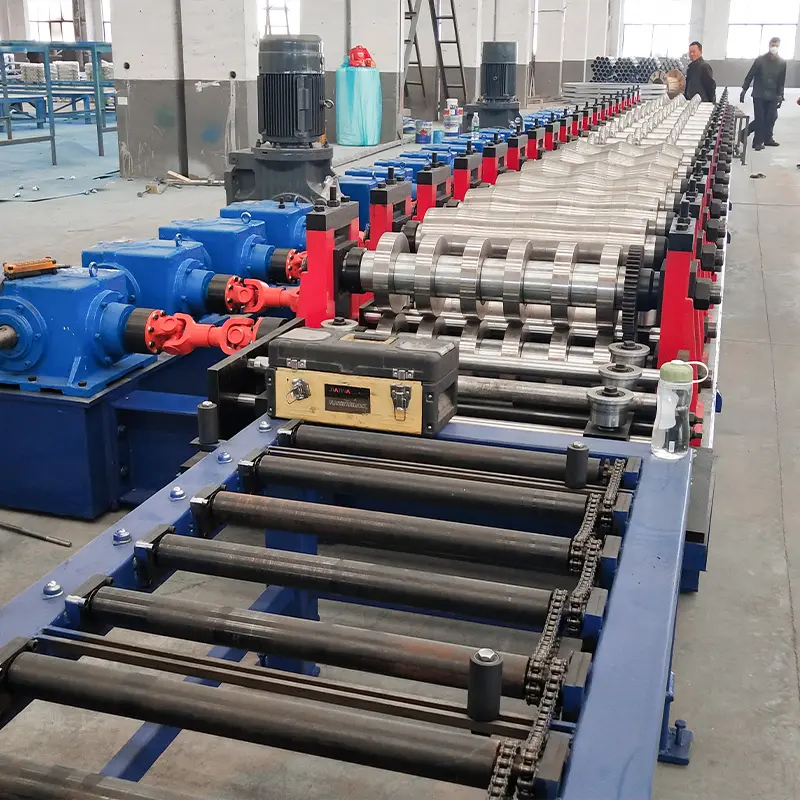
Flashing Roll Forming Applications
Flashing roll formed on these machines has become an essential component in many construction applications:
Metal Roofing
It is commonly used to provide weather-tightness on metal roofing systems. Flashing integrates with architectural panels to cover joints and direct waterflow.
Tile Roofs
Roll formed aluminum or galvanized steel flashing is ideal for tile roofs. The profiles interlock under tiles and provide durable weather protection.
Residential Construction
Homes utilize various flashing profiles to seal vulnerable areas like chimneys, skylights and deck additions against water infiltration.
Commercial Buildings
Large structures require extensive flashing to waterproof valleys, parapets, equipment curbs and complex rooflines. Roll formed flashing is easy to mass produce.
Retrofit and Repair
Damaged flashing on aging roofs can be replaced with new roll formed pieces. The interlocking sections readily integrate with existing flashing.
Specialty Applications
Custom profiles produced on these machines have other specialty uses that require formed metal shapes with hemmed edges.
Future of Flashing Roll Forming Technology
Flashing roll forming machines will continue evolving with technological improvements:
Advanced Materials
New specialty metals like copper, zinc and lead-coated steel provide enhanced durability and weather-resistance while still being formable.
Smart Controls
Artificial intelligence and machine learning will allow more intelligent and autonomous control of the roll forming process. This maximizes efficiency and quality.
Increased Automation
Robotic part handling systems will allow fully automated operation from coil feeding to finished part stacking. Human involvement will be reduced.
Flexible Configuration
Next generation roll formers will have reconfigurable frame designs allowing the mill sections to be readily changed. This enables fast profile switching.
Specialty Profiles
New specialty shapes and attachment features like louvres, snaps and stand-offs will expand capabilities beyond simple linear hemmed profiles.
Composite Production
Flashing roll formers may eventually incorporate technologies to continuously attach insulative or supportive backing materials to the formed metal strips.
निष्कर्ष
Flashing roll forming machines provide an extremely efficient means of producing the many hemmed metal flashing components essential to waterproofing and weatherproofing buildings. The automated process makes it simple to rapidly generate the long linear profiles with accurate, consistent quality impossible to achieve with manual fabrication methods. Flashing profiles can interlock in shingle fashion to provide durable protection against leaks in vulnerable areas. As construction needs grow and technology improves, flashing roll formers will continue gaining popularity over other flashing production techniques. With capabilities exceeding traditional fabrication combined with competitive pricing, these versatile machines will remain an important part of the construction industry.
सामान्य प्रश्न
What metals can be roll formed into flashing?
Flashing is most commonly produced from aluminum or galvanized steel coils. Other formable metals like copper, lead-coated steel and zinc can also be used.
What thickness metals can be formed?
Metals from 26 gauge to 16 gauge (0.5-1.5 mm) can typically be roll formed into flashing profiles. Thinner metals may require special roller designs.
How long of a flashing piece can be formed?
Standard flashing lengths range from 3-20 feet. Extended machines can produce pieces over 40 feet long by adding additional mill sections.
How do you determine the required tonnage?
The tonnage (force applied by the rollers) needed depends on the metal type, thickness and profile complexity. Typical tonnages range from 25-50 tons.
How fast do the machines operate?
The linear feed rate through the mill is 100-150 feet per minute on average. Speeds vary based on profile. Simple shapes can run faster.
How are complex custom profiles created?
Custom profiles require a new roller die set designed specifically for the desired shape. The profile is simulated digitally then machined into the rolls.
What safety features are incorporated?
Common safety features include emergency stops, protective shields, interlocks that halt operation when opened, light curtains and roll back prevention.
How long do flashing roll forming machines last?
With proper operation and maintenance, flashing roll formers typically have a service life of 8-12 years. Some machines continue operating reliably for 15+ years.
How much maintenance is required?
Routine maintenance involves lubrication, inspecting/replacing worn components and adjusting roll gaps. 1-2 hours weekly is typical for preventive maintenance.
What is the primary consumable item?
Roller dies are the most common wearing item. Die life varies based on metals formed and hours run. Typical die replacement intervals range from 9-24 months.
How much does a flashing roll forming machine cost?
Costs range from $60,000 for a compact basic machine to over $200,000 for a fully automated extended length production model.
What factors determine the machine price?
The cost depends on size/length, production speed, automation level, tonnage, added features and included tooling. More complex and robust machines carry higher price tags.
What is the delivery time for a new machine?
For a standard model, delivery lead times are usually 12-16 weeks from order to shipment. Customized or complex machines may require 16-20 weeks for design and construction.
What training is included with a new flashing roll former?
Most manufacturers provide both onsite training on operation and safety procedures as well as maintenance training for personnel who will service the machine.