परिचय
Have you ever wondered how those clean, crisp walls and ceilings in your house come to be? The answer lies in a behind-the-scenes hero: the स्टड और ट्रैक रोल बनाने की मशीन. This ingenious piece of equipment is the backbone of modern construction, silently shaping the metal components that form the framework for countless buildings.
This comprehensive guide dives deep into the world of stud and track roll forming machines, exploring their intricacies, applications, and the factors to consider when choosing the right one for your needs.
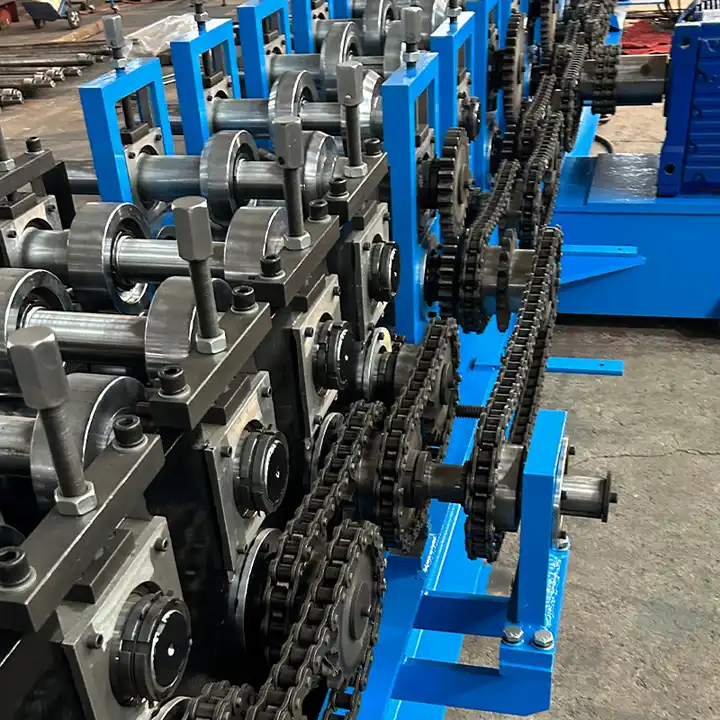
Components of a Stud and Track Roll Forming Machine
Imagine a long, continuous sheet of metal being fed into a sophisticated machine that transforms it into specific shapes. That’s essentially what a stud and track roll forming machine does. Here’s a breakdown of its key components:
- Uncoiler: This is the starting point, where the metal coil is loaded and unwound.
- Roll forming stations: These stations consist of a series of precisely shaped rollers that progressively bend and mold the metal sheet into the desired profile, like a C-shaped stud or a U-shaped track. The number of stations varies depending on the complexity of the profile.
- Cutting unit: Once the desired shape is formed, a cutting unit precisely severs the metal sheet to the required length.
- Stacker or conveyor: This system carefully collects and stacks the finished studs and tracks, ensuring they are ready for further use.
- Control system: The brain of the operation, the control system governs the entire process, regulating the speed, pressure, and sequence of operations to ensure consistent and precise production.
स्टड और ट्रैक रोल बनाने की मशीन के प्रकार
Stud and track roll forming machines come in various configurations to cater to diverse needs. Here are the two main types:
- Non-structural: These machines are designed for applications where the studs and tracks don’t need to bear significant weight, such as interior walls and partitions. They typically produce thinner and lighter gauge metal profiles.
- Structural: As the name suggests, these machines are built for projects requiring sturdier framing, like load-bearing walls, floors, and roofs. They produce thicker and heavier gauge metal profiles to handle greater weight capacities.
-
Auto Changeable C Z Purline Machine
-
नालीदार पैनल रोल बनाने की मशीन
-
वाइनयार्ड पोस्ट रोल बनाने की मशीन
-
मचान तख़्त रोल बनाने की मशीन
-
लाइट गेज स्टील रोल बनाने की मशीन
-
ऑटो आकार बदलने योग्य सिग्मा शहतीर रोल बनाने की मशीन
-
ऑटो आकार बदलने योग्य CZ शहतीर रोल बनाने की मशीन
-
ऑटो आकार बदलने योग्य Z शहतीर रोल बनाने की मशीन
-
ऑटो आकार बदलने योग्य घन शहतीर रोल बनाने की मशीन
Industrial Applications of Stud and Track Roll Forming Machines
The reach of stud and track roll forming machines extends far beyond residential construction. Here are some of their industrial applications:
- Commercial buildings: From office spaces to warehouses, these machines create the framework for various commercial structures.
- Prefabricated construction: The ability to produce consistent and precise shapes makes them ideal for prefabricated construction, where pre-assembled sections are built off-site and then transported to the main location.
- HVAC systems: The lightweight and versatile nature of metal studs and tracks makes them suitable for supporting ductwork and other components in HVAC systems.
- Furniture manufacturing: They can be used to create robust frames for furniture like office cubicles and shelving units.
Factors to Consider When Choosing a Stud and Track Roll Forming Machine
Selecting the right stud and track roll forming machine requires careful consideration of several factors:
- Production needs: Consider the volume and type of profiles you need to produce. If you anticipate high-volume production, a machine with faster cycle times and automated features might be beneficial.
- Material thickness and width: Ensure the machine can handle the desired metal gauge and width to meet your project specifications.
- Profile complexity: More intricate profiles might require machines with additional forming stations and higher levels of precision.
- Budget: Stud and track roll forming machines range in price depending on their capabilities and features. Determine your budget and choose a machine that offers the necessary functionalities while staying within your financial constraints.
- Reputation and service: Research the manufacturer’s reputation for quality and after-sales support. A reliable service network is crucial for ensuring your machine operates smoothly and efficiently for years to come.
Beyond the Basics: Advanced Features and Considerations
While the core functionality remains the same, some advanced features can enhance the capabilities and efficiency of stud and track roll forming machines:
- Automatic punching and flanging: These features allow for the creation of holes and flanges in the profiles, eliminating the need for secondary processes.
- Stacking and bundling systems: These automated systems can streamline the collection and organization of finished products, improving productivity.
- Computer-numeric control (CNC) systems: CNC technology offers precise control over the forming process, ensuring consistent quality and repeatability.
Advantages and Considerations of Using Stud and Track Roll Forming Machines
Stud and track roll forming machines offer several advantages over traditional wood framing methods:
- Increased speed and efficiency: They can produce large quantities of studs and tracks quickly and consistently, significantly reducing construction time.
- Dimensional accuracy: The precise forming process ensures consistent and accurate dimensions, simplifying the assembly process and reducing the potential for errors.
- Lightweight and durable: Metal studs and tracks are lightweight yet offer superior strength and durability compared to wood, especially when exposed to moisture and fire.
- Sustainability: Steel, the primary material used in stud and track roll forming, is recyclable, making it an environmentally friendly choice.
However, it’s important to consider these factors as well:
- Higher initial investment: Compared to traditional wood framing methods, the upfront cost of a stud and track roll forming machine can be higher.
- Learning curve: Operating these machines effectively requires proper training and knowledge of the forming process.
- Limited flexibility: While some machines offer the ability to produce various profiles, they typically cannot match the customizability of wood framing for unique applications.
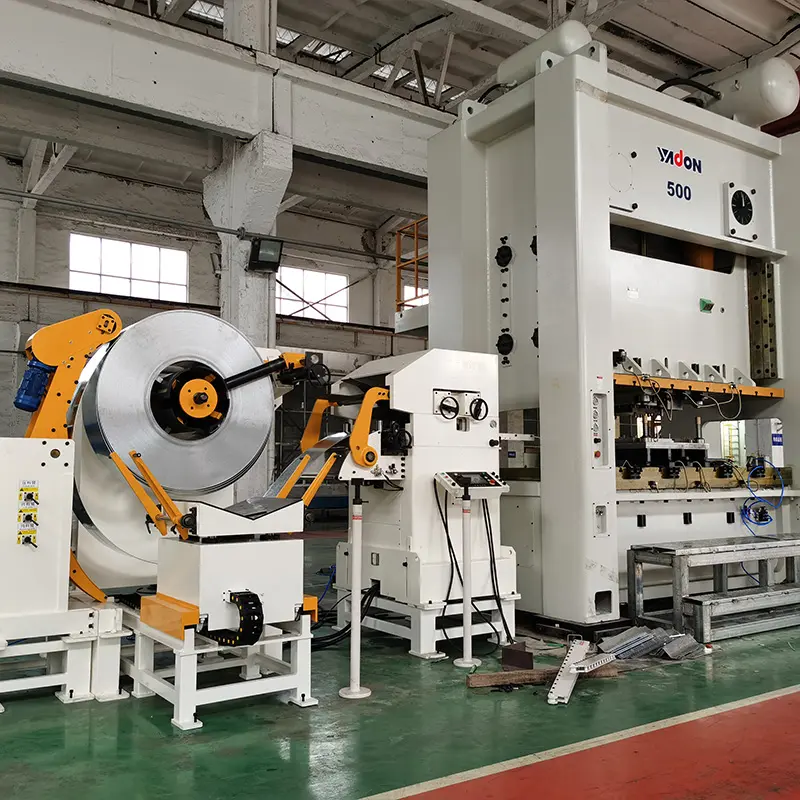
सामान्य प्रश्न
Q: What is the typical lifespan of a स्टड और ट्रैक रोल बनाने की मशीन?
A: With proper maintenance and care, a well-built stud and track roll forming machine can last for decades.
Q: Are there any safety precautions to consider when operating a stud and track roll forming machine?
A: Yes, it’s crucial to follow the manufacturer’s safety guidelines and wear appropriate personal protective equipment (PPE) such as gloves, safety glasses, and hearing protection.
Q: How do I maintain a stud and track roll forming machine?
A: Regular cleaning, lubrication, and proper maintenance practices are essential to ensure smooth operation and prevent costly breakdowns. Refer to the manufacturer’s instructions for specific maintenance procedures.
निष्कर्ष
Stud and track roll forming machines have become an indispensable tool in the modern construction industry. Their speed, precision, and versatility contribute significantly to efficient and sustainable building practices. By understanding their functionalities, capabilities, and considerations, you can make informed decisions when choosing a machine that aligns with your specific needs and contributes to the success of your projects.