ए stud and track forming machine is an innovative technology used to shape different profiles of studs and tracks from metal coils. This versatile equipment has become indispensable for roll forming industries serving construction and engineering sectors.
Overview
A stud and track forming machine, also known as a roll former, efficiently forms studs and tracks in different specifications from coiled metal sheets.
- Features computerized inline production ability, shaping complex ribbed profiles
- Used to produce cold roll-formed studs, tracks, channels and custom profiles
- Rising adoption in construction industry for forming structural framework components
- Caters to high demand growth for cold-formed steel structures and drywall partitions
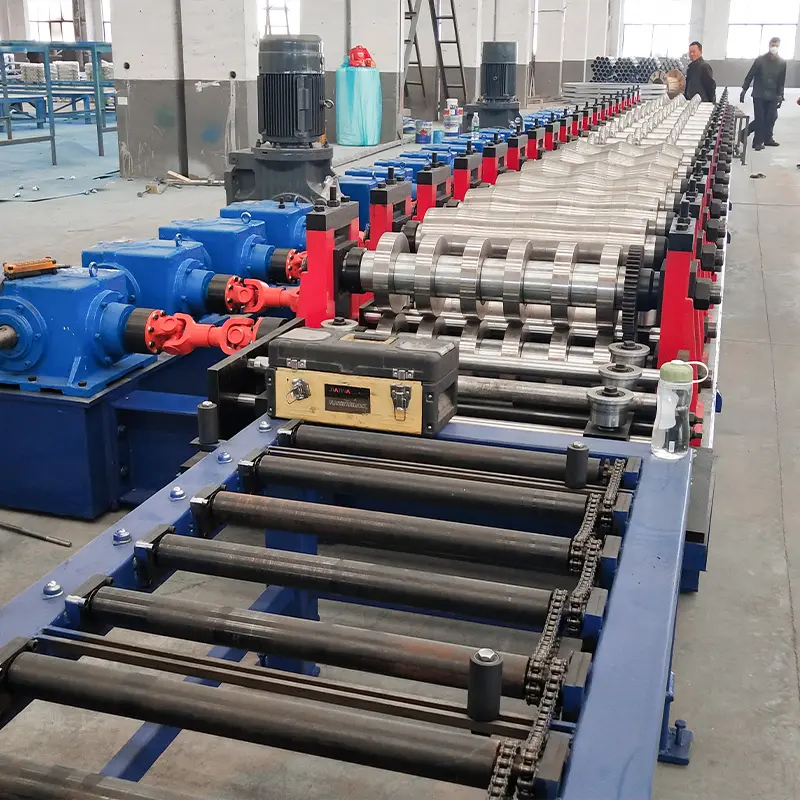
Working Principle
A stud and track roll former works by passing metal coil strips through a series of consecutive sets of rolling dies. The rolled forming stands progressively shape the strips into intended profiles with ribs/flutes through bending.
- Strip Feeding: Coil strips are fed through a de-coiler and guides into the forming stands
- Shaping: Rolls continuously form the strips incrementally as they pass through successive stands
- Flying Cutoff: Cutting knives sever formed profiles to specified lengths
- Stacked Output: Lengths of formed studs & tracks are stacked at the exit for collection
A typical stud and track roll former has 10-16 sets of rolls to create the final profile shape. The number of stands determines the complexity of profiles produced.
Types of Stud And Track Forming Machines
Type | Description |
---|---|
Standard | Most common model with 10-12 forming stands producing general profiles |
High-speed | Advanced model with 16-20 stands for high production rates |
Customized | Tailor-made roll former for specific custom profiles per client design |
Material Feeding System
The de-coiler mechanism feeds metal strips from coils into the forming section:
- Coil Loading: Helps load heavy coils on expanding mandrel to hold it firm
- De-coiling: Smoothly unwinds the metal strip from outer coil circumference
- Threading: Guides strip through the entry guides to first forming stands
- Tension Control: Maintains optimum tension to ease consistent feeding
Forming Section
The multi-stand roll forming section shapes the strips into studs and tracks:
- Progressive Dies: Each stand has top and bottom rolls engraved with profiling grooves
- Bending: Rolls incrementally bend the strip to shape the ribs and walls
- Roll Design: Complex profiles need more fine-tuning stands to avoid defects
- Roll Materials: Hardened steel/alloy rolls have durability for long runs
-
Highway Guardrail End Terminal Forming Machine
-
Highway U/C Post Roll Forming Machine
-
2 Waves Highway Guardrail Roll Forming Machine
-
3 Waves Highway Guardrail Roll Forming Machine
-
वाइनयार्ड पोस्ट रोल बनाने की मशीन
-
ऑटो आकार बदलने योग्य सिग्मा शहतीर रोल बनाने की मशीन
-
ऑटो आकार बदलने योग्य CZ शहतीर रोल बनाने की मशीन
-
ऑटो आकार बदलने योग्य Z शहतीर रोल बनाने की मशीन
-
ऑटो आकार बदलने योग्य घन शहतीर रोल बनाने की मशीन
Cutoff Unit
The cutoff mechanism precision-cuts the continuously formed profiles:
- Flying Cutoff: Rotating saw blades sever the moving profile at high speeds
- Length Control: Cuts profiles to pre-set lengths as per client specifications
- Length Tolerance: Ensure tight length tolerances as low as +/- 0.5 mm
- Stacked Output: Cut lengths smoothly released for automated stacking
Technical Specifications
Parameter | Range |
---|---|
Production Speed | 10 – 25 m/min |
Forming Stands | 10 – 20 stands |
Power Consumption | 15 – 30 kW |
Roll Changing Time | 10 – 15 minutes |
Coil ID Range | 500 – 1500 mm |
Coil OD Range | 1000 – 2500 mm |
Strip Width | 50 – 200 mm |
Strip Thickness | 0.5 – 2 mm |
Stud Heights | 50 – 300 mm |
Design and Customization
Stud and track roll formers can be customized as per application requirements:
- Profile Drawings: Client approved 2D/3D models for profiles
- Roll Design: Forming rolls engraved based on final profile shape
- Machine Layout: Tailor inline layout to fit shop-floor placement
- Control System: Touchscreen HMI and optimized automation
- Commissioning: On-site installation, trial runs and operator training
Industrial Applications
Stud and track forming machines have widespread applications across industries like:
- Construction – Drywall framing, roofing, cladding, partition structures
- Infrastructure – Building frames, purlins, solar mounting, drainage channels
- Engineering – Rack, crane and machine structures, agriculture sheds
- Automotive – Brackets, supports, trailers, storage racks
They enable efficient mass production of cold-formed studs and tracks for structural engineering needs.
Choosing A Reliable Stud And Track Roll Former Supplier
Here are tips on selecting a reliable stud and track roll forming machine manufacturer:
- Technology Expertise: Advanced roll forming knowledge and production ability
- Machines Portfolio: Diverse range of specialized roll forming equipment
- Design Capability: Inhouse engineering to design tooling as per custom profiles
- Quality & Testing: Stringent inspection of formed profiles using gauges
- Certifications: ISO 9001 and CE marked products following safety norms
- Experience Record: Proven track record catering to leading companies
- Clientele: Reputed client base from target industry sectors
- Service Support: Timely after-sales service support across client regions
Careful vendor evaluation ensures obtaining a stud and track roll former that meets quality and output objectives.
Pricing
A new stud and track roll forming machine typically costs between $7,500 to $15,000 based on:
- Type: Standard, high-speed or customized
- Automation level
- Production output rate
- Hours of operation
- Additional finishing attachments
- Buying location
Parameter | Cost Factor |
---|---|
Forming Stands | More stands increases price |
Speed & Output | Advanced models cost more |
Roll Materials | Hardened rolls cost extra |
Automation | Full automation has higher price |
Tooling | Custom roll tooling involves additional charges |
Location | Taxes and shipping influence landed cost |
Advantages of Stud And Track Forming Machines
Stud and track roll formers offer superior benefits than other manufacturing processes:
- Higher Production Volumes: Over 10-25 meters per minute
- Cost Efficiency: Economical for mass production
- Material Savings: Optimized material utilization
- Flexibility: Able to produce varied profiles
- Precision: Consistent and tolerant dimensions
- Lightweight: Cold formed, high strength sections
- अनुकूलन: Client specific profiles feasible
These versatile machines enable companies to profitably address rising market demand.
Limitations of Stud And Track Forming Machines
However, stud and track formers also have certain limitations:
- Initial Investment: Substantial initial machine buying cost
- Space Requirement: Bulky equipment needing ample space
- Skilled Operation: Requires trained staff for best performance
- Roll Maintenance: Regular roll grinding/hardening for consistency
- Fixed Assets: Not viable for very low production volumes
- Strength: Limitations in blank strength and thickness
- Secondary Ops: Handling or drilling holes need other tools
While optimized processes can mitigate the shortcomings, they remain inherent to the technology.
Installation and Commissioning
Specialized engineers undertake on-site installation and commissioning:
- Assembly & Positioning: Assemble machine at shop-floor and bolt it down
- Levelling & Grouting: Fine tune level on foundation using grout packing
- Electricals: Power wiring to control panel from source panels
- Pneumatics: Connect air compressor to actuate cylinder motions
- Trial Runs: Initial test runs using dummy coils to tune functioning
- Final Alignment: Optimize machine geometrics for smooth running
- Staff Training: Impart operating and maintenance training
They ensure optimal uptime through expert machine debugging and demonstrations.
Operation
Trained operators perform stud and track roll former functioning:
- Safety Gear: Wear protective gloves, glasses and safety shoes
- Coil Loading: Place raw material coils on de-coiler mandrel
- Threading: Feed strip end through guiding rollers into first stand
- Parameter Input: Enter profile dimensions in machine controller
- Speed Setting: Define optimal RPM and output rate
- Automatic Operation: Forming automatically progresses after initiation
- Monitoring: Observe forming quality and stack off-take
- Periodic Oiling: Oil moving components to minimize wear and tear
- Quality Checks: Confirm dimensions using gauges randomly
Good operating practices maximize production rates and end product quality.
Maintenance
Scheduled maintenance activities ensure high working efficiency:
- Cleaning: Remove metal dust/scales clinging to assemblies
- Inspection: Check roll damage or component wear periodically
- Lubrication: Oil/grease all moving joints at defined intervals
- Filter Cleaning: Clean air filter bowls to maintain air quality
- Roll Grinding: Refurbish forming rolls to original profiles
- Hydraulics: Inspect cylinders, valves and hoses
- Hardware: Tighten any loose nuts/bolts on stands
- Spare Parts: Stock
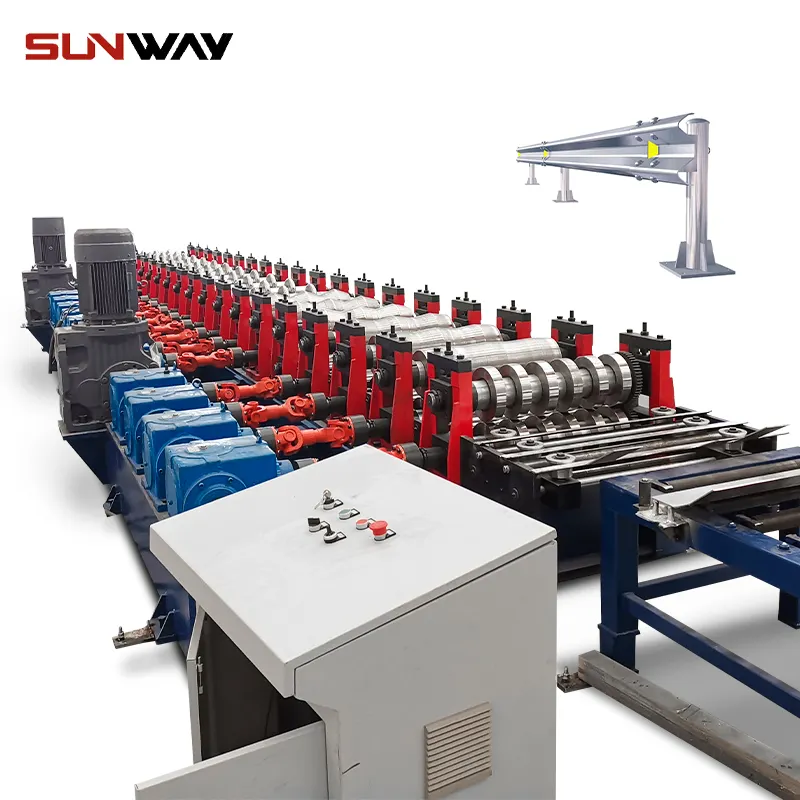
सामान्य प्रश्न
Q: What materials can be formed into studs and tracks using these machines?
A: Common materials include low carbon steel, stainless steel and galvanized iron coils. Other formable metals are aluminium and copper. Mild steel is the most widely used material.
Q: What construction standards do the profiles conform to?
A: Formed studs and tracks normally adhere to international specifications like AISI, EN, BS, AS/NZS etc. They meet designated strength and structural reliability standards.
Q: How to select the right stud and track sections for an application?
A: Consider load capacity, span, metal thickness, corrosion resistance needed. Heights range from 50mm to 300mm. Custom profiles are possible for special applications.
Q: What maintenance is vital for stud and track roll formers?
A: Regular roll grinding to restore forming accuracy, hydraulic system inspection and component lubrication are most critical. This optimizes quality and runtime.
Q: What safety aspects need monitoring during operation?
A: Key areas are machine guarding, emergency switches, safe coil handling, employee training and protective gear. Safety sensors help minimize risks.
Q: What are common defects in roll formed studs and tracks?
A: Typical defects are twist, bow, flaring, burrs and dimensional variations beyond tolerance limits. These get magnified over long production runs.
Q: How to troubleshoot problems in stud and track forming quality?
A: Check feed alignment, roll damage, hydraulic pressure, cutting accuracy as per quality manuals. Seek expert service support if unable to diagnose issues.
Q: What modern features are being incorporated into newer machines?
A: Some newer advances are customized roll design softwares, smart forming process controls, automated stackers and integrated package cutting/counting for end-to-end automation.