ए step beam making machine is an efficient automated solution for manufacturing step beams used in the construction industry. This guide provides a detailed overview of step beam maker machine technology, working principles, components, capabilities, suppliers, prices, and more.
What is a Step Beam?
A step beam is a type of load bearing structural beam that has ridges and channels resembling steps. Step beams are widely used to construct mezzanine floors, platforms, walkways, equipment foundations, and shelving units.
Compared to traditional I-beams, step beams offer significant advantages:
- Higher load capacity and strength due to composite structure
- Lighter weight by up to 30% for easy handling and installation
- Faster, simpler assembly without welding or bolting
- Flexibility to adjust beam height by cutting steps
- Low slip hazard surface for safe walking
Step beams are an optimal, cost-effective building material when high structural performance is required along with dimensional flexibility.
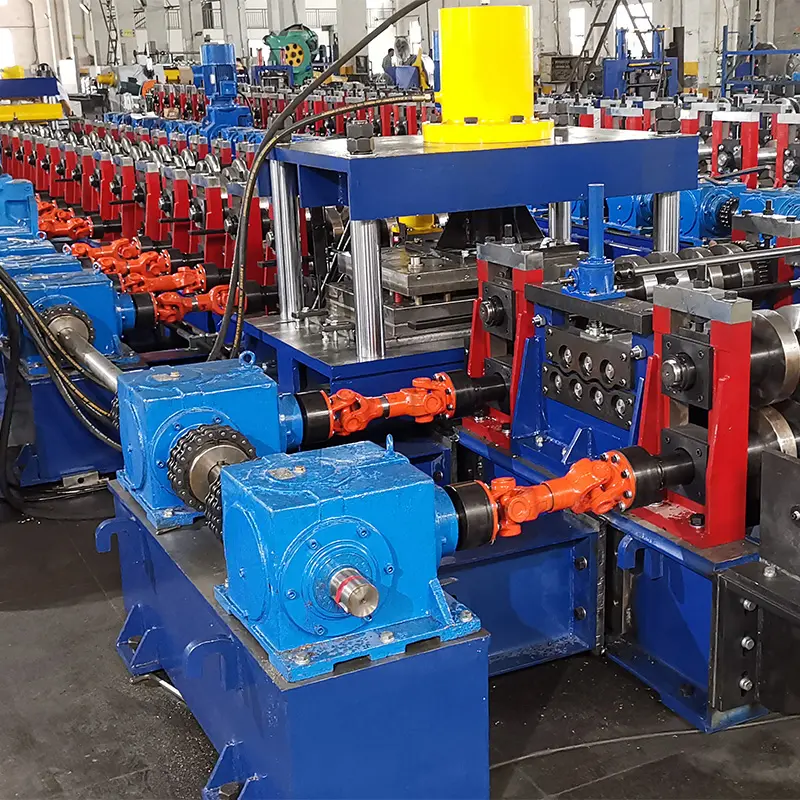
Key Features of Step Beam Making Machines
Step beam makers are automated roll forming systems with robust components for high speed production:
Forming Method
- Cold roll forming by progressive bending
Key Components
- Decoiler for sheet coil input
- Feeder and straightener
- Forming stations with guiding rollers
- Fly shear for step cutting
- Stacker for finished step beam output
Capabilities
- Beam height adjustment
- Step depth and beam thickness control
- Custom hole punching
- Support different structural designs and materials
Production Scale
- Up to 60 m/min forming speed
- 18-40 units per hour
- Small footprint
A properly equipped step beam making machine delivers rapid, high accuracy fabrication tailored to application needs.
Types of Step Beam Making Machines
Step beam manufacturers offer roll formers in manual, semi-automatic, and fully automatic configurations to suit different production requirements:
Machine Type | Description |
---|---|
Manual | Basic machine for small scale operations Manual controls for decoiler, forming, shearing Labour intensive with slower speeds |
Semi-automatic | Automated forming and shearing Manual decoiler and stacker Compact footprint, lower investment |
Fully-automatic | Fully motorized for all functions Pre-programmed control panel High output rates For large production volumes |
Key Factors Determining Machine Design
- Step beam dimensions – height, width, flange sizes
- Step configuration – number and spacing
- Material grade and thickness
- Production speed and volume
- Additional fabrication needs – hole punching, embossing
Reputable manufacturers can provide customized step beam roll forming solutions built specifically around a client’s product range and site requirements.
Working Process of a Step Beam Making Machine
A step beam production line utilizes synchronized mechanisms to transform input sheet metal into finished beams:
Stock Preparation
- Decoiler feeds metal coil stock into machine
- Sheet passes through feeder with pinch rollers
- Straightening rolls remove coil curvature
Beam Forming
- Sheet enters progressive bending stations
- Top and bottom rollers gradually bend metal into step shape
- Adjustable forming tools for varying profiles
Beam Cutting
- Formed sheet exits and passes under fly shear
- Shear trims sheet by height to cut finished beams
- Transport rollers below shear remove scrap
Product Finish
- Step beams stacked on exit conveyor by stacker
- Additional hole punching or marking stations can be integrated
- Stacked beams bundled for storage or just-in-time supply to construction floor
A step beam plant’s layout couples the roll former directly with a metal coil warehouse to minimize material handling. Modern machines also include safety shields and protocols.
Main Components of a Step Beam Making Machine
Step beam making machines are assembled from heavy-duty parts that work synergistically for high speed production:
Key Component | Description |
---|---|
डेकोइलर | Feeds sheet metal into system from loaded coil Capacity 15-25 tons Hydraulically expands mandrel to mount coils Adjustable brake for coil tension |
Guiding Rolls | Align sheet and remove camber Heavy-duty stands support straightening rolls Progressive straightening in multiple passes |
Forming Stations | Series of top and bottom precision rollers Gradually bend and shape sheet into steps Interlocked safety guards for roll housing |
Controls | Pre-programmed PLC logic controls Touchscreen for production monitoring Controls speed, step depth, shearing |
Fly Shear | Hydraulically operated trimming shear Hardened removable blades Precise cut-off control via servo motor |
Stacker | Belt-driven outfeed stacker Neatly stacks finished step beams Conveyor chain with adjustable guides |
Advanced 3D simulation aids component sizing for required beam specifications during the design phase.
-
रोलिंग शटर स्लेट रोल बनाने की मशीन
-
Highway Guardrail End Terminal Forming Machine
-
Highway U/C Post Roll Forming Machine
-
2 Waves Highway Guardrail Roll Forming Machine
-
3 Waves Highway Guardrail Roll Forming Machine
-
विद्युत कैबिनेट फ्रेम रोल बनाने की मशीन
-
दीन रेल रोल बनाने की मशीन
-
दो लहरें राजमार्ग रेलिंग मशीन
-
तीन लहरें राजमार्ग रेलिंग मशीन
Capabilities of Step Beam Making Machines
Modern step beam production lines offer extensive functionality for high accuracy automated fabrication:
Beam Size Flexibility
- Adjustable forming rollers – easy size changes
- Programmable beam step profile and lengths
- Fly shear for custom beam height
Fabrication Customization
- Hole punching units – tailor mounting points
- Embossing attachments – branding options
- Special roll dies – unique step patterns
Material and Strength Variants
- Mild steel coils up to 25 tons capacity
- Feed thickness 1-3 mm, yield strength 250-400 MPa
- Stainless steel forming for corrosive areas
Volume Production
- Up to 60 meter/minute line speed
- 18-40 pcs/hr rating based on size
- 97%+ forming accuracy
Quick Installation
- Modular components for easy shipping
- Leveling stands and bolt-down frame
- Plug-and-play electrical connections
With programmable controls and customization tools, step beam making equipment provides flexible, high speed beam manufacturing calibrated precisely to client needs.
Typical Structure and Dimension Range
Step beams are roll formed to provide optimal strength properties within tailored dimensional envelopes:
Typical Step Beam Structure
- Channel-shaped central web
- Perpendicular top and bottom flanges with steps
- Regularly spaced vertical ridges along flanges
- Beam height dictated by application loads
Dimension Range
- Height – 100mm to 400mm
- Width – 180 to 380 mm between flanges
- Flange thickness – 2mm to 4mm
- Metal grade – Q235, Q345, SS400 etc.
Advanced 3D CAD and FEA tools allow manufacturers to simulate the optimal step configuration, spacing, sheet thickness, and steel grade needed to withstand expected floor or platform loading conditions for a given beam section.
Main Design Factors
Equipment builders work closely with clients during design stage of the production line to understand key application parameters that drive step beam specifications:
Loading
- Uniform, pallet, moving, seismic
- Concentrated point or conduit loads
Span
- Simply supported or continuous spans
- Spacing between foundation points
Environment
- Indoor or outdoor installation
- Corrosive atmosphere – chemicals, moisture
Safety Factors
- Design codes and legal requirements
- Product certification needs
Cost Targets
- Budget limitations
- Balance performance with affordability
This joint analysis by engineers and fabricators ensures the automated step beam making system consistently manufactures economical and structurally optimized beams fully compliant for each project.
Material and Sheet Feed Options
A range of material and feeding configurations are supported on step beam lines:
Material Format
- Coiled steel sheet
- Decoiler capacity up to 25 tons
- Uncoil and straighten coils internally
Materials Handled
- Mild steel – SS400, Q235, ST37 etc. grades
- High strength low alloy steel
- Stainless steel coils
- Aluminum alloy sheets
Sheet Width
- Up to 1500mm coil strips
- Customized decoilers for narrow sheets
मोटाई
- 1mm to 4mm metal thickness
- Variable roll pass depth settings
Careful material selection allows fabricators to balance structural performance, weight, lifetime costs, and corrosion needs – from bare steel up to specialized alloys.
Typical Industrial Applications
The adaptable nature of step beams makes them ideal for diverse construction, storage, and material handling uses:
Mezzanine Flooring
- Custom floor levels within buildings
- Upper storage platforms in warehouses
Equipment Foundations
- Platforms for heavy machinery and vessels
- Conveyor bed framing with high load capacity
Walkways and Safety Railings
- Elevated or suspended access ways
- Crossovers between structures
- Guard rails around openings and heights
Shelving and Racking Systems
- Adjustable storage bay construction
- Catwalks and ladders integrated
Support Frames
- Multilevel staging for events
- Temporary building extensions
- Work platforms for maintenance access
Retail Shopfitting
- Display stands and gondolas
- Decorative brand structures
- Signage frames
From robust warehouse mezzanines to retail visual merchandising, step beams enable adaptable and cost-effective structures.
Step Beam Making Machine Suppliers
China is home to many specialized manufacturers of step beam production lines:
Supplier | Location | Equipment Scale |
---|---|---|
Zhangjiagang XinBei Machinery | Jiangsu province | Small to large automation levels |
Tianjin Hoffen Machinery | Tianjin | Customized lines |
Wuxi Hero Factory | Jiangsu | Affordable low capacity models |
Shijiazhuang Sanmei | Hebei | High speed + hole punching/embossing |
Botou Hongda Roll Forming | Hebei | Ultra large step beam fabricating |
Additional local Chinese fabricators are available. Importers also represent Taiwanese and European automated step beam equipment brands catering to regional demand.
When selecting a supplier, key considerations include machine capacity, production speed, customization abilities, local support structure, cost, and compliance with safety certifications. Site visits to existing facilities aid decision making.
Cost Analysis of Step Beam Making Equipment
A step beam production line represents significant upfront capital investment. However increased fabrication efficiency compared to manual methods usually enables fast payback:
Key Cost Components
- Type of machine – manual vs automated
- Production speed – beams per hour
- Additional tooling – hole puncher, laser marker
- Material coils – steel grade and thickness
- Site preparation needs
- Freight and installation
Price Range
- Manual $8,000 – $15,000
- Semi-automatic – $18,000 – $38,000
- Fully automatic – $45,000 – $120,000+
Cost Saving Opportunities
- Higher line speed and beam output
- Lower labor by automation
- Bulk purchase of coil feedstock
- Minimize customization
Detailed cost-benefit modeling during procurement stage helps fine tune equipment selection and operating targets for fastest ROI.
Installation, Operation and Maintenance
Step beam making machines are designed for quick installation and intuitive operation:
Installation
- Arrives fully factory tested
- Bolt down stands – minimal foundation needs
- Hydraulic, electric, and control connections
- Assisted debugging and trial runs
Operation
- Touchscreen HMI and manual control stations
- Easy coil loading and machine start/stop
- Parameter presets for each beam configuration
- Quality inspection systems
Maintenance
- Robust construction for 24 hour production
- Lubrication systems on wearing components
- Component access doors and handling points
- Visual service alerts and diagnostics
Proactive preventative maintenance is key to maximize equipment lifetime, output consistency, and safety. This includes regular lubrication, inspection, belt tensioning, alignments, and minor servicing as needed.
How to Choose A Reliable Step Beam Making Machine Supplier
Selecting the right step beam production line vendor is crucial for success:
Proven Experience
- Years manufacturing experience
- Case studies of previous similar projects
- Client reference calls and site visits
Customization Ability
- Range of machine sizes and production rates
- Tailor forming speeds, profiles, holes etc.
- Support future beam product iterations
Responsiveness
- Timely replies to RFQ technical queries
- Accommodate design change requests
- Commit to lead time promises
Local Support
- In-country sales engineer assistance
- Fast response for service calls
- Warehousing of spare parts
Certifications
- Quality management system
- Safety and compliance audits
- International standards: CE, UL etc.
Taking a systematic approach when shortlisting suppliers improves odds of securing productive step beam manufacturing equipment fine-tuned for years of volume production.
Pros and Cons of Automated Step Beam Fabrication
Automating production via roll forming yields advantages along with certain tradeoffs:
Pros
- High material yield and low waste
- Consistent end product quality
- Custom programming for variations
- Cost efficiency through speed
Cons
- Substantial initial capital expense
- Skilled labor still required
- Size limitations of forming heads
- Secondary finishing often needed
While automated solutions require more upfront investment, the long term savings from safer, rapid, precision fabrication typically outweigh the costs for manufacturers focusing on step beam products.
Comparison to Conventional Beam Manufacturing Methods
Traditional techniques for structural beam creation tend to consume more effort and resources versus modern step beam making:
Metric | Manual Fabrication | Automated Step Beam Line |
---|---|---|
Process | Cutting, drilling, welding and bolting I-beams | High speed roll forming from coil feedstock |
Skills Needed | Multiple skilled tradespeople | Machine operator and quality inspector |
Speed | Very slow and labor intensive | Up to 40 beams per hour automated |
Consistency | High variability in end product | Calibrated precision at every step |
Material Efficiency | High scrap loss from cutting sheets | Near net shape forming minimizes waste |
Safety | Dangerous equipment and lifting | Enclosed machinery with safety protocols |
अनुकूलन | Changes require fabrication modifications | Programmable machine settings for variations |
Expense | Higher labor and production costs | Reduced long term expense via automation |
While initial machinery procurement costs are high, optimizing the complete beam fabrication workflow through roll forming reduces expenses considerably.
Limitations of Step Beam Making Machines
Automating production via a dedicated step beam line maximizes efficiency but has restrictions around:
- Beam size range – Limited by decoiler capacity and forming head size
- Fabrication operations – Cannot complete complex assemblies requiring welding
- Material grades – Typically only structural and stainless steels
- Secondary finishing – Often needs manual deburring, drilling, galvanizing
- Prototype development – Manual methods faster for new product iterations
- Low volume batches – High mix production better suited for workshops
Working closely with equipment vendors aids selection of the ideal machine rating that balances automation capabilities against application requirements.
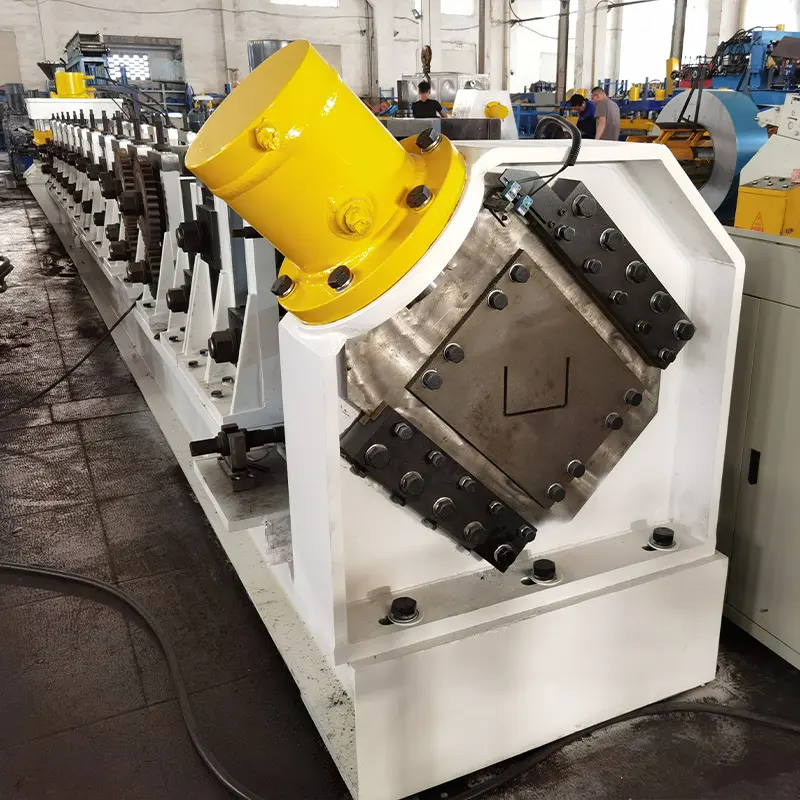
The Future of Step Beam Fabrication
As demand increases for structural step beams across industries, equipment builders continue innovating fabrication processes:
- Larger machines to economically produce deeper beams
- Expanded materials like aluminum alloys
- Improved precision through servomotors and quality monitoring
- Intelligent IoT controls to automate production flows
- Heavy-duty handling robots to manipulate beams
- Laser cutting and hole punching for finishing
- Inventory management software integration
These upgrades make step beam manufacturing lines even more versatile, efficient and simple to operate – further growing usage of step beams as a standard structural component worldwide.
सामान्य प्रश्न
Q: Are step beam making machines fully automated?
A: Modern step beam production lines utilize extensive automation for decoiling, straightening, roll forming, shearing and stacking functions. However an operator is still required for oversight along with occasional parts handling. Advanced lines also allow hole punching and embossing attachments for secondary fabrication steps.
Q: Can a step beam make holes and cutouts?
A: Yes, most leading step beam makers integrate automated hole punching units. These use hydraulic punches synchronized to the moving sheet to punch custom patterns of holes or notches at prescribed positions along the finished step beams. This allows simplified installation.
Q: Can I get custom roll forming dies?
A: Certainly – reputable step beam machine manufacturers can provide fully customized roll forming heads tailored to produce client-specified beam profiles including specialized step patterns. 3D CAD modeling confirms the custom tool geometry prior to precision production. Expect moderate charges for one-off tooling requirements.
Q: What safety devices are included?
A: Package step beam making equipment incorporates extensive safety protections for operator well-being. Light curtains, dual-hand controls, emergency stops, belt guards, interlocks, marked hazards, and lockouts are all standard. Safety certifications also confirm additional compliance to local regulations during shipment.