Steel silo forming machines are used to manufacture silos, hoppers, ducts, and other industrial storage vessels from steel coil material. This automated equipment forms the steel coil into the desired cylindrical or conical shape using a series of rollers while welding along the length to create large seamless tanks.
Steel silos provide excellent storage for bulk solids like grains, cement, minerals, etc. They are weather and corrosion resistant, easy to install, and require minimal maintenance. Steel forming machinery allows mass production of storage silos tailored to customer specifications.
Steel Silo Forming Machine Types
Machine Type | Description |
---|---|
रोल बनाना | Coil steel fed through series of roller dies to gradually shape into cylinder |
Press Brake Forming | Flat steel sheet pressed into shape between male and female ridges |
Spinning Lathe | Steel plate spun against rollers to form concave/convex shells |
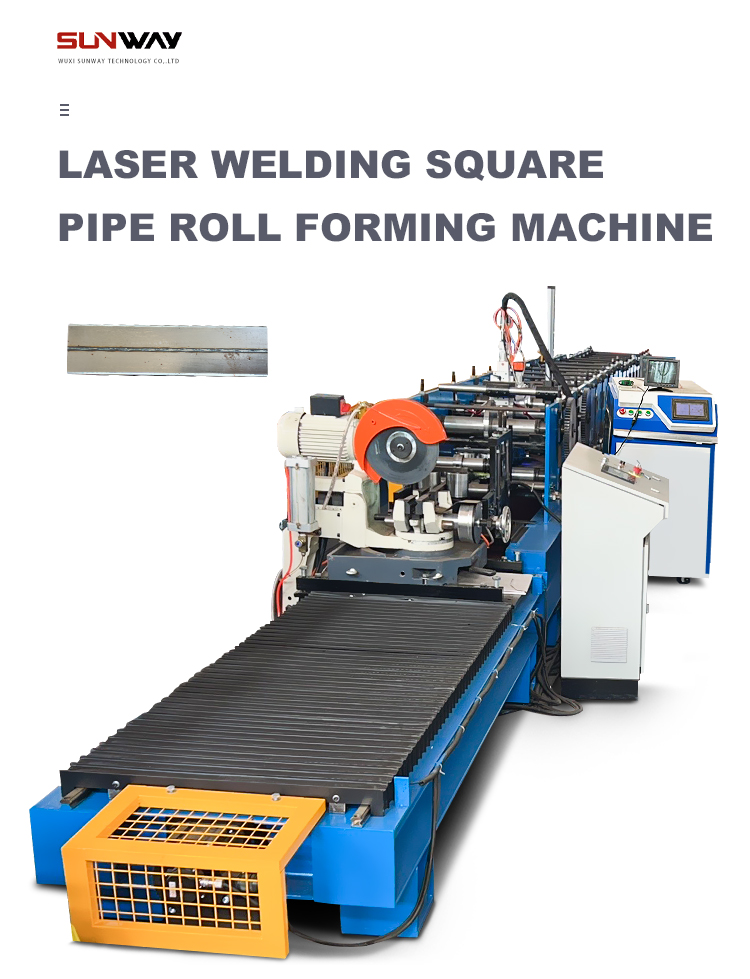
Working Process
The working process of a steel silo forming machine starts by loading a coil of thin steel sheet onto a de-coiler mechanism. The sheet is gradually fed through a series of roller dies engraves with the desired profile. As the sheet passes each roller station, it is bent into the cylindrical or conical form through a cold roll forming process without applying heat.
The edges of the formed sheet are then welded together along the length of the silo as it progresses through the machine. This creates a seamless, leakproof storage tank tailored to the exact size and capacity requirements. Modern steel silo machinery is fully automated with precision roller feeds and computerized controls to fabricate silos of various dimensions.
Operators can customize parameters like height, diameter, wall thickness, slope, number and size of outlets, surface finish, etc. The machine handles activities like de-coiling, feeding, pre-punching holes, forming, welding, cutting and deburring to output a ready-to-install steel silo in hours. Special features like corrugation, fins, ladder supports or surface coatings can also be integrated.
Material Feeding
- Coiled sheet steel loaded onto powered de-coiler and straightened automatically
- Roller feed pulls sheet through series of bending dies
- Feed speed synchronized with welding speed
- Various steel grades like stainless, galvanized, carbon steel used
- Sheet thickness from 0.5mm to 2mm for tanks up to 6m diameter
Profile Forming
- Cold roll forming process used without applying heat
- Sheet steel bent gradually by contour profiled roller dies
- Rollers engraves to required radius/angle of silo sides
- Forming stations setup to achieve steady curvature
- Conical sections created by precise roller positioning
Welding
- Formed steel sheet welded along length to create leakproof seam
- MIG, TIG, Spot, laser welding options for various materials
- Automatic oscillating or rotary welding torches used
- Continuous, high-speed welding upwards of 10m/min
- Welding done from inside and outside for smooth finish
Cutting and Deburring
- Formed, welded silo cut to desired height on exit
- Automatic oxy-fuel torches used for cutting
- Laser, plasma cutting available for neat edge
- Special deburring rolls or brushes used
- Smooth edge and weld seam ensures easy installation
Design and Customization
- Various loading/unloading outlets and covers designed
- Ladders, fins, platforms, etc integrated on sides
- Corrugations, stiffeners added for structural strength
- Surface coatings like epoxy, zinc applied
- Logos, graphics printed using inkjet technology
-
Highway Guardrail End Terminal Forming Machine
-
Highway U/C Post Roll Forming Machine
-
2 Waves Highway Guardrail Roll Forming Machine
-
3 Waves Highway Guardrail Roll Forming Machine
-
वाइनयार्ड पोस्ट रोल बनाने की मशीन
-
ऑटो आकार बदलने योग्य सिग्मा शहतीर रोल बनाने की मशीन
-
ऑटो आकार बदलने योग्य CZ शहतीर रोल बनाने की मशीन
-
ऑटो आकार बदलने योग्य Z शहतीर रोल बनाने की मशीन
-
ऑटो आकार बदलने योग्य घन शहतीर रोल बनाने की मशीन
Steel Silo Forming Machine Manufacturers
कंपनी | Location | Type |
---|---|---|
Spiroflow | USA | रोल बनाना |
Jorgensen Conveyors | USA | रोल बनाना |
Gough Econ | UK | Spinning Lathe |
Sesotec | भारत | रोल बनाना |
Price Range
- Small Roll Forming Machine – $50,000 to $250,000
- Large Automated Line – $500,000 to $5 million
Factors affecting price:
- Forming length and speed
- Level of automation
- Material thickness capacity
- Customization features
- Production output requirement
- Additional peripheral equipment
Installation Requirements
Parameter | विवरण |
---|---|
Location | Indoor factory site, stable flat floor |
शक्ति | 25 to 50kW connection, 480V 3-phase |
Compressed Air | 10 bar pressure for automation |
Material Handling | Lifting equipment to load coil stock |
Commissioning | 1 week by technician |
Operation
- Mostly automated operation after material loading
- HMI touchscreen to input job dimensions
- Controls for feed speed, weld settings, cut-off
- Sensors to detect coil runout, jamming
- Safety mechanisms like emergency stop button
Maintenance
Activity | Frequency |
---|---|
Visual Inspection | Daily |
Roller Lubrication | Weekly |
Belt Tension Check | Monthly |
Hydraulic Oil Change | 6 months |
Calibration | Annual |
How to Select Steel Silo Forming Machine Supplier
Consideration | विवरण |
---|---|
Product Quality | Consistent, smooth, defect-free output |
Reliability | Robust design for 24×7 operation |
अनुभव | Proven track record of installations |
अनुकूलन | Flexibility to tailor silo design |
Automation | Higher productivity and precision |
Service Support | Responsiveness for maintenance issues |
Compliance | ISO, CE, other safety/quality certificates |
Price | Capital cost, operating cost comparison |
Pros and Cons of Steel Silo Forming Machines
Pros
- High production rates up to 15m/min forming
- Lower labor cost due to automation
- Consistent quality and dimensions
- Custom profiles and features possible
- Suitability for food/chemical contact
- Low maintenance equipment
- Compact, safe design with sensors
Cons
- High initial capital investment
- Complex programming and setup
- Coil stock availability issues
- Limited forming capacity for thickness
- May still need manual welding finishing
- Requires constant operation to achieve ROI
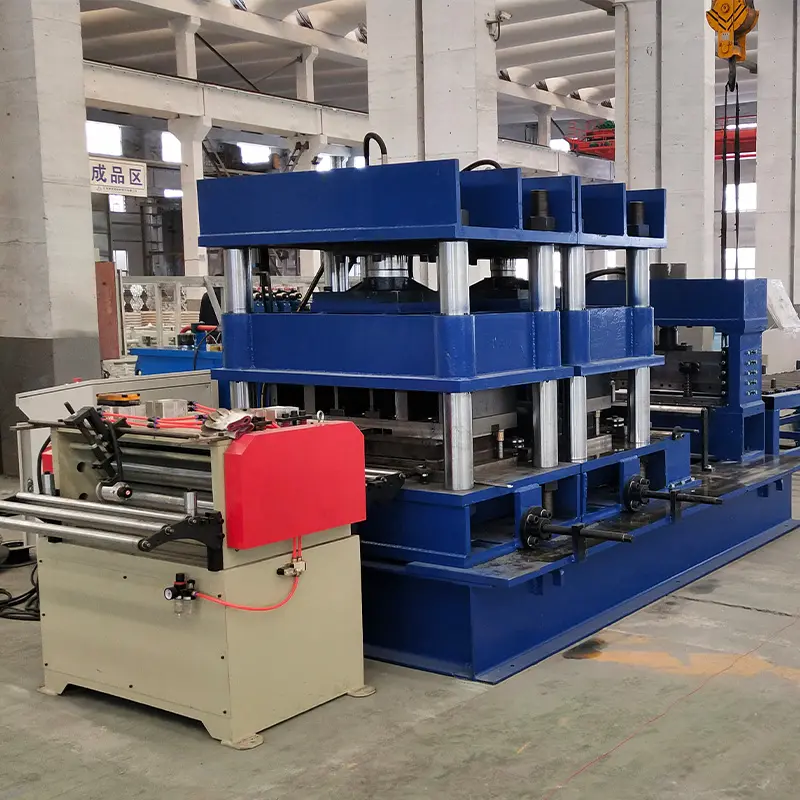
सामान्य प्रश्न
Q: What materials can be formed on a steel silo machine?
A: Most commonly low carbon steel, stainless steel or aluminum coils. Other metals like copper or titanium possible for custom applications.
Q: What industries use steel silos?
A: Agriculture, food processing, cement, mining, plastic manufacturing, scrap metal handling etc.
Q: What is the typical production rate?
A: Around 10 – 15 meters per minute of finished welded silo, depending on size.
Q: Can forming be done for conical shapes?
A: Yes, precise roller design allows both cylindrical and various conical profiles.
Q: How are custom graphics added to silos?
A: Using a digital inkjet printer to directly print logo or images on steel surface.
Q: What is the power consumption?
A: 30-50kW depending on if induction heating or other options selected.