Steel sheet panels are vital materials in construction, industrial, and architectural applications. Whether you’re building a durable roof, creating a long-lasting exterior, or even assembling industrial machinery, steel sheet panels offer unparalleled strength, versatility, and longevity. In this comprehensive guide, we’ll explore everything there is to know about steel sheet panels—from their types, manufacturing processes, key components, uses, and even how to choose the best suppliers. With a focus on ensuring you have a clear understanding of each aspect, this guide will dive deep into the details while remaining conversational and engaging.
Overview of Steel Sheet Panels
Steel sheet panels are flat or corrugated sheets made from different types of steel, used in various applications due to their strength, corrosion resistance, and formability. They come in different thicknesses and finishes depending on their intended use, including galvanized, painted, and plain steel sheets. Steel sheet panels are manufactured through a series of processes involving metal powders and rolling machines to create different profiles, such as corrugated iron sheets, standing seam panels, and flat sheets. The steel used can vary in composition, influencing the panel’s strength, flexibility, and longevity.
Key Details of Steel Sheet Panels:
- Durability: Steel panels last for decades, resisting weather conditions, corrosion, and mechanical wear.
- Versatility: Suitable for roofing, siding, construction, and even manufacturing processes.
- Ease of Customization: Available in various thicknesses, sizes, and finishes for different project needs.
- Low Maintenance: With minimal upkeep, steel sheet panels retain their appearance and structural integrity.
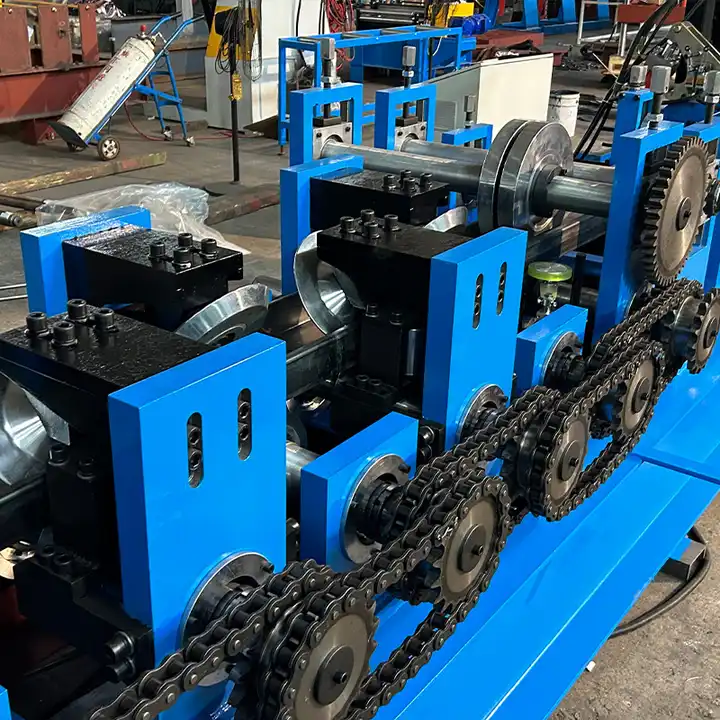
Types of Steel Sheet Panels
When choosing steel sheet panels, it’s essential to understand the different types available and what makes them unique. Below is a breakdown of the most common steel sheet panel types.
Common Steel Sheet Panel Types
Steel Sheet Type | Description | Key Features |
---|---|---|
Galvanized Steel Sheets | Coated with a layer of zinc to prevent rusting. Ideal for outdoor use where resistance to moisture is essential. | Corrosion-resistant, durable, and cost-effective |
Corrugated Steel Panels | Wavy-patterned sheets often used for roofing or siding. The design provides additional strength and rigidity. | Strong, lightweight, and easy to install |
Stainless Steel Sheets | Made from steel alloys containing chromium, these sheets offer enhanced corrosion resistance, especially in harsh environments. | High durability, corrosion-resistant, and aesthetically pleasing |
Aluminized Steel Panels | Steel sheets coated with aluminum-silicon alloy. These panels provide excellent heat resistance and are often used in automotive and industrial applications. | Heat-resistant, lightweight, and long-lasting |
Cold Rolled Steel Sheets | Cold-rolled for smooth finishes and precise dimensions, these sheets are used in high-end applications requiring accurate shaping and formability. | Smooth finish, precise shaping, and great for bending |
Hot Rolled Steel Panels | Created through heating and rolling, these sheets are more malleable and affordable. Used for structural applications where precise finishing isn’t crucial. | Affordable, malleable, and ideal for large-scale applications |
Electro-Galvanized Steel | These sheets undergo an electroplating process to ensure uniform zinc coating. They’re often used in appliances and automotive components. | Uniform coating, corrosion-resistant, and visually appealing |
Perforated Steel Sheets | Sheets with holes punched through them for ventilation, filtration, or decorative purposes. Widely used in architectural designs and industrial environments. | Airflow, customizable patterns, and versatile applications |
Color-Coated Steel Panels | Steel sheets painted or coated in various colors for aesthetic appeal. Often used in architectural projects where visual appeal is as important as functionality. | Aesthetic appeal, corrosion-resistant, and customizable |
Weathering Steel Sheets | Also known as Corten steel, these panels develop a rust-like patina over time, which protects them from further corrosion. Common in outdoor applications. | Self-healing rust patina, low maintenance, and weather-resistant |
Each of these steel sheet types offers distinct advantages and disadvantages, making it critical to choose the right one depending on your project’s specific needs, such as environment, budget, and design requirements.
Corrugated Steel Sheet Panels Guide
Corrugated steel sheet panels stand out due to their wavy shape, which adds strength and makes them ideal for roofing, siding, and even certain structural purposes. Their corrugated design improves rigidity while keeping the material lightweight and easy to install.
Advantages of Corrugated Steel Sheets
- Increased Strength: The corrugation process makes steel stronger by distributing weight more evenly across the panel.
- Weather Resistance: These sheets often come galvanized or painted, which helps them withstand harsh outdoor environments, including high winds and heavy rain.
- Cost Efficiency: Compared to other materials like tiles or asphalt shingles, corrugated steel is relatively affordable for large-scale applications.
- Simplicity of Installation: Due to their lightweight and flexibility, corrugated steel panels are easy to handle, cutting down on installation time and labor costs.
Working Process of Steel Sheet Panels
The production process of steel sheet panels involves several steps, starting from raw metal to the final product used in construction. The following steps outline the general process:
1. Raw Material Selection
Steel sheet panels typically begin with selecting the right steel alloy. These materials often include low-carbon steel for its workability or stainless steel for enhanced corrosion resistance. Various additives like chromium, zinc, or aluminum can be used depending on the desired properties.
2. Metal Powder Creation
Metal powders are often used for special coatings, such as galvanization. These powders are made by grinding metals into fine particles, which can be later applied to the surface of the steel sheet to improve corrosion resistance or provide heat resistance.
3. Rolling and Forming
The raw steel is heated to a high temperature and passed through rolling mills to achieve the desired thickness. This process can be done hot (for malleability) or cold (for precision).
4. Corrugation and Shaping
To create corrugated panels, the flat steel sheet is pressed into wavy patterns using specialized machines. This shaping adds strength and rigidity, making the sheet suitable for structural uses like roofing and siding.
5. Coating and Finishing
Once the panels are formed, additional finishes, such as galvanizing or painting, are applied. These coatings improve the steel’s resistance to corrosion, weather conditions, and wear over time.
6. Quality Inspection
Before shipping, the panels go through strict quality inspections to ensure they meet the required thickness, strength, and finish specifications. Panels that don’t pass quality checks are recycled or reworked.
Key Components of Steel Sheet Panels and Their Functions
Steel sheet panels consist of various key components that determine their performance in construction and manufacturing applications. Understanding the function of each component can help in choosing the right type of steel panel for your project.
Key Components and Their Functions
Component | Function |
---|---|
Steel Alloy | Provides the base material’s strength, flexibility, and durability. The alloy composition (carbon, chromium, etc.) influences these traits. |
Zinc/Aluminum Coating | Prevents rust and corrosion in galvanized or aluminized panels, extending the sheet’s lifespan in outdoor conditions. |
Chromium Additive | Used in stainless steel panels for corrosion resistance, especially in harsh environments. |
Corrugations | Add structural rigidity and strength without increasing the sheet’s weight, ideal for roofing and siding. |
Paint Coating | Provides both aesthetic appeal and additional protection against weather and wear. |
Perforations | In perforated sheets, holes are added for ventilation, filtration, or decorative use. |
-
कैरिज बोर्ड रोल बनाने की मशीन
-
Highway Guardrail End Terminal Forming Machine
-
Highway U/C Post Roll Forming Machine
-
2 Waves Highway Guardrail Roll Forming Machine
-
3 Waves Highway Guardrail Roll Forming Machine
-
सी सेक्शन ब्रेसिंग ओमेगा स्टोरेज रैक अपराइट पोस्ट रोल बनाने की मशीन
-
स्टील बॉक्स प्लेट रोल बनाने की मशीन बनाना
-
शेल्फ कॉलम के लिए बॉक्स बीम स्टील रोल बनाने की मशीन
-
पैलेट रैकिंग स्टेप बीम पी बीम रोल बनाने की मशीन
Machine Speed and Efficiency in Steel Sheet Panel Production
The production efficiency of steel sheet panels depends on the machinery used, including the speed and accuracy with which the material can be processed. Here’s a detailed table showing machine speeds and production efficiency.
Machine Speed and Efficiency
Machine Type | Speed (m/min) | Efficiency (Sheets per Hour) | Best Suited For |
---|---|---|---|
Corrugating Machine | 20-60 m/min | 1000 sheets/hour | Corrugated panel production |
Cold Rolling Mill | 10-30 m/min | 500-800 sheets/hour | High-precision cold-rolled steel sheets |
Hot Rolling Mill | 60-100 m/min | 1200 sheets/hour | High-speed production of malleable hot-rolled sheets |
Coating Machine (Galvanizing) | 5-15 m/min | 400-600 sheets/hour | Application of zinc/aluminum coating |
Perforation Machine | 15-40 m/min | 700-900 sheets/hour | Creating perforated steel sheets |
The type of machinery and its speed will influence production efficiency, cost, and the final quality of the steel sheet panels.
Customized Mechanical Parameters for Steel Sheet Panels
Customizing steel sheet panels requires adjusting specific mechanical parameters to suit the application. The following table outlines various customizable parameters and their importance.
Customized Mechanical Parameters
Parameter | Description |
---|---|
Thickness (mm) | Thicker sheets offer more strength and durability but are heavier and more challenging to install. |
Length (m) | Custom lengths allow for precision fitting in specific projects, reducing waste and installation time. |
Width (m) | Wider panels cover more area with fewer seams, reducing the risk of leaks in roofing applications. |
Coating Thickness (µm) | The thickness of the zinc, aluminum, or paint coating affects corrosion resistance and the panel’s longevity. |
Corrugation Depth (mm) | Deeper corrugations add strength but may affect the visual design and overall flexibility of the panel. |
Perforation Size (mm) | For perforated sheets, the size and pattern of the holes can be customized for ventilation or decorative purposes. |
Applications of Steel Sheet Panels
Steel sheet panels are used in a wide variety of industries, from construction to manufacturing. Below is a table that outlines some common applications.
Applications and Uses
आवेदन | Description |
---|---|
Roofing and Siding | Steel panels are often used for roofing and siding due to their strength, weather resistance, and low maintenance requirements. |
Automotive Industry | High-strength steel panels are used in automotive manufacturing for vehicle body panels, chassis parts, and other structural components. |
Industrial Equipment | Steel sheets are used to make parts for machinery, including enclosures, casings, and other components requiring strength and precision. |
Architectural Projects | Perforated and color-coated steel sheets are popular in architectural designs due to their aesthetic appeal and structural functionality. |
Agricultural Buildings | Corrugated steel panels are widely used in constructing barns, sheds, and storage buildings in agricultural settings. |
HVAC Systems | Perforated steel sheets are used in HVAC systems for air filtration, ducting, and ventilation purposes. |
Marine Environments | Weathering steel or stainless steel sheets are used in marine applications due to their ability to withstand harsh, salty environments. |
Appliances and Electronics | Electro-galvanized steel sheets are commonly used for making appliances such as refrigerators, washing machines, and electronic device casings. |
Installation, Operation, and Maintenance of Steel Sheet Panels
Steel sheet panels require proper installation, operation, and maintenance to ensure longevity and optimal performance. Below are guidelines for each aspect.
Installation, Operation, and Maintenance
Aspect | Guidelines |
---|---|
Installation | Ensure proper alignment, spacing, and secure fastening to prevent leaks and structural weaknesses. Use appropriate tools to cut and fit panels. |
Operation | Once installed, panels require little operational oversight, but regular inspections for signs of wear or damage are recommended. |
Maintenance | Clean the panels periodically to remove debris and dirt. Check for rust or corrosion in galvanized or coated panels and repair as necessary. |
Suppliers and Price Range of Steel Sheet Panels
Choosing the right supplier is critical for obtaining high-quality steel sheet panels at a reasonable price. Here’s a table showcasing a few suppliers and their price ranges.
Suppliers and Price Range
Supplier | Location | Price Range (per square meter) | Products Offered |
---|---|---|---|
BlueScope Steel | Australia | $5 – $15 | Galvanized, color-coated, and corrugated steel panels |
Tata Steel | भारत | $4 – $12 | Corrugated, aluminized, and cold-rolled steel sheets |
ArcelorMittal | Global | $6 – $18 | Stainless steel, weathering steel, and perforated steel sheets |
POSCO | South Korea | $7 – $20 | Hot-rolled, cold-rolled, and color-coated steel sheets |
Nippon Steel Corporation | Japan | $8 – $22 | High-strength steel, stainless steel, and electro-galvanized sheets |
How to Choose the Right Steel Sheet Panel Supplier
Selecting a supplier involves several factors, such as pricing, product quality, and the supplier’s reputation. Here’s a guide on what to look for when choosing a steel sheet panel supplier:
Choosing the Right Supplier
Criteria | Explanation |
---|---|
Product Quality | Check the quality of steel, coatings, and finishing options. Look for certificates like ISO 9001 that confirm the supplier’s adherence to quality standards. |
Pricing | Compare prices across multiple suppliers but ensure that lower prices do not compromise quality. Look for bulk discounts if purchasing in large quantities. |
Lead Time and Availability | Ensure the supplier can meet your project timelines and has adequate stock levels. Delays in delivery can derail projects. |
ग्राहक सहेयता | A reliable supplier offers good customer service, technical support, and after-sales assistance, helping you with installation, customization, and maintenance. |
Sustainability Practices | If environmental responsibility matters to your project, opt for suppliers who practice sustainable production, including recycling and minimizing emissions. |
Advantages and Limitations of Steel Sheet Panels
While steel sheet panels offer numerous benefits, they also come with certain limitations. Here’s a comparison table highlighting the advantages and drawbacks.
Advantages and Limitations of Steel Sheet Panels
Advantages | Limitations |
---|---|
Durability | Prone to denting under extreme conditions like hail or heavy impacts |
Corrosion Resistance (with coatings) | Can corrode if coatings are scratched or damaged |
Lightweight and Strong | Can be noisy during heavy rain or hail if not properly insulated |
Versatility in Design and Customization | Requires professional installation to avoid damage during handling or improper fastening |
Fire Resistance | Heat conductivity may be an issue in high-temperature environments, necessitating proper insulation |
Low Maintenance | Higher initial cost compared to traditional materials like asphalt shingles |
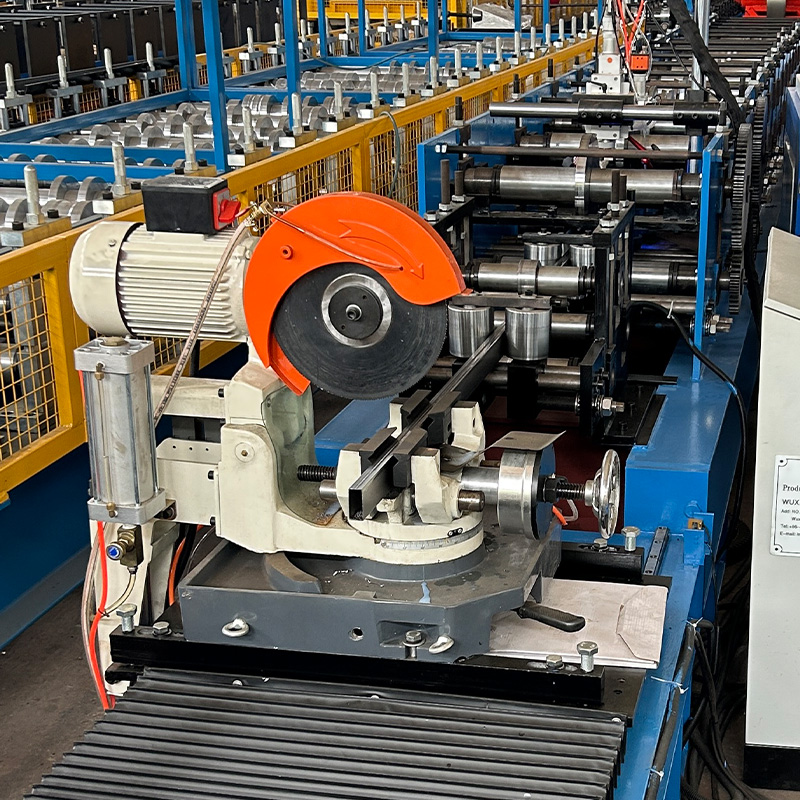
सामान्य प्रश्न
Question | Answer |
---|---|
What is the lifespan of steel sheet panels? | Steel sheet panels can last between 40 to 70 years, depending on the type of coating, environmental factors, and proper maintenance. |
Are steel sheet panels environmentally friendly? | Yes, steel panels are recyclable, and many manufacturers use eco-friendly practices, including the use of recycled steel in production. |
Can steel sheet panels be painted? | Yes, steel panels can be color-coated during production, or painted later on to match aesthetic preferences. |
How do I prevent rust on steel sheet panels? | Using galvanized or coated panels and ensuring proper maintenance, such as cleaning and repairing scratches, can help prevent rust. |
Are steel sheet panels good for insulation? | Steel is not a good insulator by itself, but adding proper insulation underneath the panels can improve thermal and sound insulation properties. |
How much do steel sheet panels cost? | Prices vary, but typically range from $4 to $22 per square meter, depending on the type of steel, thickness, and any additional coatings or treatments. |
Can steel sheet panels be used in coastal areas? | Yes, but it’s recommended to use stainless steel or specially coated panels, like weathering steel, to resist the salty, corrosive marine environment. |
निष्कर्ष
Steel sheet panels are an incredibly versatile and durable solution for a wide range of applications, from construction to industrial uses. With various types, coatings, and customization options available, they offer both functionality and aesthetic appeal. Whether you’re looking for cost-effective roofing materials or high-end architectural solutions, understanding the types, production processes, and performance characteristics of steel sheet panels will help you make an informed decision for your project.