As the world races toward cleaner energy solutions, solar power has emerged as a key driver of renewable energy adoption. Behind every solar panel lies a crucial component that ensures its stability and efficiency—the PV (Photovoltaic) mounting bracket. These brackets are the backbone of solar panel support systems, providing strength, durability, and adaptability across various installation scenarios. But how are they manufactured at scale with precision and efficiency? Enter the PV Mounting Bracket Roll Forming Machine.
In this definitive guide, we’ll explore everything you need to know about PV Mounting Bracket Roll Forming Machines in 2025. From their applications and types to pricing, automation trends, and why Wuxi Sunway Machinery stands out as a global leader, this guide is your one-stop resource for mastering this essential manufacturing technology.
Overview of PV Mounting Bracket Roll Forming Machines
ए PV Mounting Bracket Roll Forming Machine is a specialized piece of equipment designed to produce high-precision solar mounting bracket profiles from metal coils. These brackets are integral to solar panel installation systems, ensuring that panels remain securely mounted on rooftops, ground installations, or other structures.
The roll-forming process involves feeding flat metal coils into the machine, where a series of rollers progressively shape the material into intricate profiles. This ensures uniformity, durability, and high structural integrity—qualities that are vital for solar panel performance in various environmental conditions.
With the global push toward renewable energy, the demand for PV mounting brackets has skyrocketed, making these machines an essential investment for manufacturers looking to capitalize on the solar boom.
Applications of PV Mounting Bracket Roll Forming Machines
PV mounting brackets are used across a wide range of solar installation projects. Let’s take a closer look at their applications:
1. Rooftop Solar Systems
PV mounting brackets are widely used in both residential and commercial rooftop installations. They provide secure support for solar panels on flat, sloped, or curved roofs.
2. Ground-Mounted Solar Farms
Large-scale solar farms rely on robust bracket systems to withstand wind loads, temperature variations, and other environmental factors. Ground-mounted brackets allow for optimum panel orientation to maximize energy generation.
3. Floating Solar Systems
In floating solar installations, such as those on reservoirs or lakes, PV mounting brackets are often made of lightweight and corrosion-resistant materials. These brackets are designed to hold panels securely while withstanding water exposure.
4. Solar Carports
PV mounting brackets are a critical element in solar carports, combining energy generation with parking facilities. These systems are increasingly popular in urban and commercial spaces.
5. Off-Grid Solar Solutions
For remote or off-grid locations, PV mounting brackets ensure the stability of solar panels used to power everything from homes to telecommunications towers.
By investing in a PV Mounting Bracket Roll Forming Machine, manufacturers can meet the growing demand for these versatile and critical components across industries.
Types of PV Mounting Bracket Roll Forming Machines
Not all PV mounting brackets are the same, and neither are the machines that produce them. Here’s a breakdown of the main types of PV Mounting Bracket Roll Forming Machines:
1. Standard Roll Forming Machines
These machines are designed to produce a single type of solar mounting bracket profile. They are ideal for manufacturers focused on high-volume production of a specific bracket design.
2. Multi-Profile Roll Forming Machines
For manufacturers serving diverse markets, multi-profile machines offer the flexibility to produce different bracket designs. Quick-change tooling systems make switching between profiles seamless.
3. Fully Automated Roll Forming Machines
Fully automated machines handle every aspect of production, from material feeding to punching, cutting, and stacking. These machines are ideal for large-scale operations looking to minimize labor costs and maximize efficiency.
4. Custom Roll Forming Machines
If you require unique or specialized bracket profiles, custom machines can be designed to meet your exact specifications. These machines are tailored to your specific material, profile, and production needs.
Comparison Table: Types of PV Mounting Bracket Roll Forming Machines
Machine Type | Primary Use | Profiles Produced | Production Speed | Price Range (USD) |
---|---|---|---|---|
Standard Machines | Single-profile production | 1 Profile | 10–20 meters/min | $50,000–$80,000 |
Multi-Profile Machines | Versatile profile production | Multiple Profiles | 10–25 meters/min | $80,000–$120,000+ |
Fully Automated Machines | High-volume, multi-profile production | Multiple Profiles | 20–30 meters/min | $100,000–$200,000+ |
Custom Machines | Specialized or unique profiles | Variable | Variable | Based on design specs |
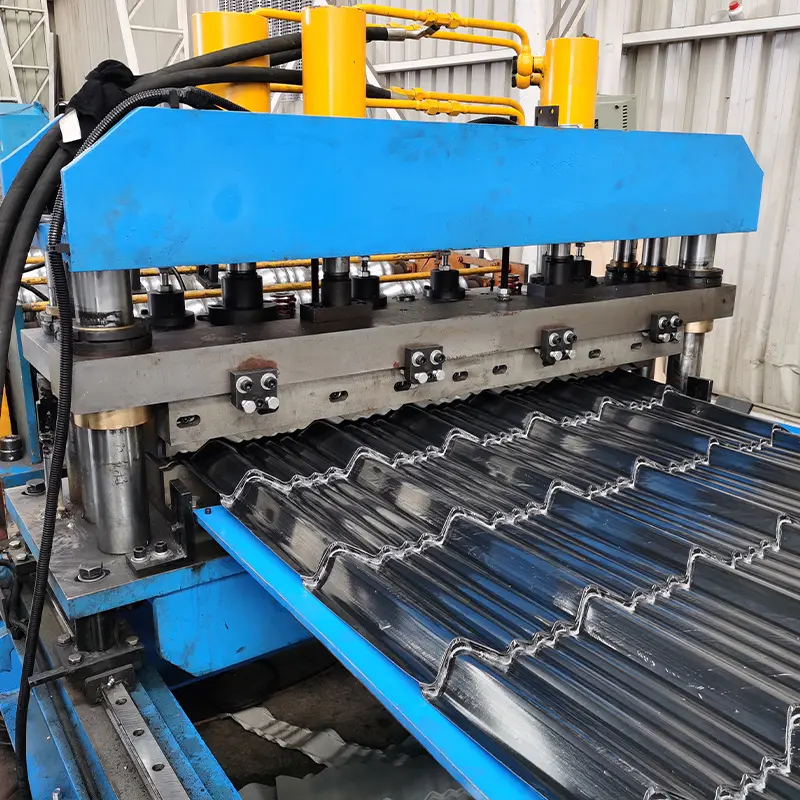
Key Features of PV Mounting Bracket Roll Forming Machines
When investing in a PV Mounting Bracket Roll Forming Machine, it’s essential to understand the features that ensure high-quality output and operational efficiency. Here’s what to look for:
1. High-Precision Rollers
The rollers are the heart of the machine. High-strength, chrome-coated steel rollers ensure precision and durability, producing consistent bracket profiles.
2. Integrated Punching Systems
Pre-punched holes are essential for assembling PV mounting brackets. Machines with integrated punching systems save time and ensure precision.
3. Servo-Driven Cutting Systems
Cutting systems powered by servo motors deliver clean, burr-free cuts, ensuring brackets meet exact length specifications.
4. PLC Control Systems
ए Programmable Logic Controller (PLC) system allows operators to automate production settings, monitor performance, and make real-time adjustments.
5. Material Compatibility
Ensure the machine can process a variety of materials, such as galvanized steel, stainless steel, and aluminum.
6. Quick-Change Tooling
For manufacturers producing multiple profiles, quick-change tooling systems minimize downtime when switching between designs.
Machines from Wuxi Sunway Machinery include these advanced features, ensuring top-tier performance and reliability.
Specifications of PV Mounting Bracket Roll Forming Machines
Here’s a quick overview of the technical specifications to expect:
Specification | विवरण |
---|---|
Material Thickness | 1.5mm–3.5mm |
Material Type | Galvanized steel, stainless steel, aluminum |
बनाने की गति | 10–30 meters per minute |
रोलर सामग्री | High-strength steel with chrome plating |
पंचिंग सिस्टम | Hydraulic or servo punching for pre-drilled holes |
कटिंग सिस्टम | Servo or hydraulic cutting for precision |
नियंत्रण प्रणाली | PLC with HMI (Human-Machine Interface) |
बिजली की आपूर्ति | Typically 380V/50Hz (customizable for regional standards) |
Pricing of PV Mounting Bracket Roll Forming Machines
The cost of a PV Mounting Bracket Roll Forming Machine depends on various factors, including its features, automation level, and customization. Here’s a general pricing guide:
Price Ranges
- Standard Machines: $50,000–$80,000
- Multi-Profile Machines: $80,000–$120,000+
- Fully Automated Machines: $100,000–$200,000+
- Custom Machines: Pricing depends on design and capabilities.
Factors Affecting Price
- Automation Level: Fully automated machines cost more but significantly reduce labor costs.
- Production Speed: Machines with higher speeds are generally more expensive.
- Customization: Tailored machines for unique profiles or materials come with a premium price tag.
- Brand Quality: Trusted manufacturers like Wuxi Sunway Machinery offer durable machines that deliver excellent ROI.
FAQs About PV Mounting Bracket Roll Forming Machines
Here are answers to some frequently asked questions:
Question | Answer |
---|---|
Can these machines produce custom profiles? | Yes, custom machines can be tailored to produce unique profiles for specialized applications. |
What’s the average production speed? | Depending on the machine, you can produce 5,000–10,000 meters of brackets per day. |
What materials can be processed? | Most machines handle galvanized steel, stainless steel, and aluminum within the specified thickness. |
Is training provided? | Absolutely! Manufacturers like Wuxi Sunway Machinery include training with every purchase. |
What’s the typical machine lifespan? | With proper maintenance, these machines can last 10–15 years or more. |
Automation Trends in PV Mounting Bracket Roll Forming Machines
As the solar industry scales up globally, automation in manufacturing is no longer optional—it’s the future. Modern PV Mounting Bracket Roll Forming Machines are integrating cutting-edge automation technologies to boost efficiency, reduce costs, and ensure consistent product quality. Here’s how automation is transforming the production of solar mounting brackets:
1. IoT Integration for Smart Monitoring
Imagine getting real-time data about your production line on your smartphone or tablet. IoT (Internet of Things) integration allows manufacturers to:
- Monitor machine performance remotely.
- Receive alerts about maintenance needs.
- Track production metrics like output rate, material usage, and energy consumption.
This not only reduces downtime but also gives you a granular understanding of your operations, helping you make data-driven decisions.
2. Fully Automated Production Lines
From feeding raw material to cutting, punching, and stacking the finished brackets, fully automated systems handle every step of the process. Operators only need to supervise the system, freeing up time and reducing labor costs.
3. Servo-Driven Components
Servo motors are now standard in advanced machines, offering unparalleled precision in cutting, punching, and forming. With servo-driven components, manufacturers can achieve:
- Accurate hole punching for assembly.
- Burr-free, clean cuts.
- Consistent profile dimensions, even at high speeds.
4. Adaptive Rollers for Material Flexibility
Modern machines feature adaptive rollers that automatically adjust to accommodate different material thicknesses and profile designs. This is particularly useful for manufacturers producing various types of brackets for diverse solar installation projects.
5. Predictive Maintenance Through AI
Predictive maintenance systems use artificial intelligence to analyze data from sensors embedded in the machine. These systems can:
- Predict when a component (like a roller or cutting blade) is likely to fail.
- Schedule maintenance proactively to avoid unexpected downtime.
- Extend the lifespan of the machine, reducing long-term costs.
At Wuxi Sunway Machinery, we incorporate these advanced automation features into our machines to ensure our customers stay competitive in the rapidly evolving solar energy market.
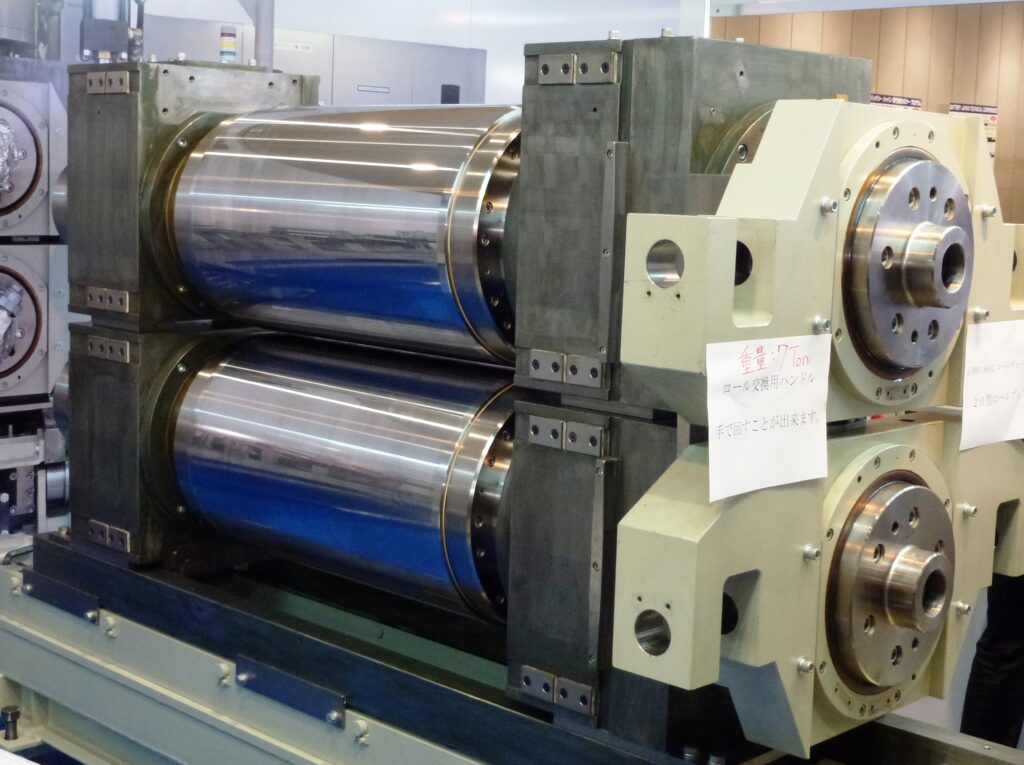
Workflow Optimization for PV Mounting Bracket Production
An optimized workflow is the key to maximizing efficiency, reducing waste, and meeting production deadlines. If you’re running a PV Mounting Bracket Roll Forming Machine, here’s how to streamline your manufacturing process for optimal results:
Step 1: Material Preparation
- Select High-Quality Coils: Use steel (galvanized or stainless steel) or aluminum coils with a thickness range of 1.5mm–3.5mm.
- Store Properly: Keep coils in a dry, clean environment to prevent corrosion or contamination before production.
- Automated Decoiling: Use a hydraulic decoiler to feed the material into the machine. This reduces manual handling and ensures consistent feeding.
Step 2: Feeding and Alignment
- Precision Material Feeding: Ensure the material is aligned perfectly as it enters the rollers. Misalignment can lead to defective profiles or machine jams.
- Tension Control: Maintain proper tension on the material to prevent slippage or wrinkling during the roll-forming process.
Step 3: Roll Forming
- Progressive Shaping: The material passes through a series of rollers that gradually form the desired bracket profile. This step ensures uniformity and structural integrity.
- Roller Inspection: Regularly inspect and clean the rollers to maintain their precision and prevent wear-related defects.
Step 4: Punching
- Integrated Hydraulic Punching: Machines with integrated punching systems create pre-drilled holes for bolts and fasteners, ensuring brackets are ready for assembly.
- Custom Patterns: Use the PLC system to program different punching patterns based on the bracket design.
Step 5: Cutting
- Servo-Driven Cutting Systems: These ensure the brackets are cut to the exact required length with clean, burr-free edges.
- Adjustable Lengths: Easily modify cutting lengths via the machine’s HMI (Human-Machine Interface) for different orders.
Step 6: Stacking and Packaging
- Automated Stacking: Finished brackets are automatically stacked for easy transport and storage.
- Protective Packaging: Wrap brackets in moisture-resistant materials to protect them during shipping or extended storage.
Real-Time Monitoring
Machines equipped with advanced PLC systems and HMI panels allow operators to monitor production metrics, adjust parameters, and troubleshoot issues instantly.
By following these steps, manufacturers can achieve high production efficiency while maintaining the quality standards required in the solar energy industry.
Troubleshooting Common Issues in PV Mounting Bracket Roll Forming Machines
Even the most advanced machines can encounter operational challenges. Here’s a quick troubleshooting guide for common issues in PV Mounting Bracket Roll Forming Machines:
1. Material Slippage
- Cause: Improper tension settings or worn feeding rollers.
- Solution: Adjust the tension and inspect the feeding rollers for wear. Replace rollers if necessary.
2. Misaligned Profiles
- Cause: Incorrect material alignment or roller calibration.
- Solution: Realign the material feeding system and recalibrate the rollers. Check the roller stations for debris that could cause misalignment.
3. Uneven Cutting
- Cause: Dull cutting blades or a misaligned cutting system.
- Solution: Replace or sharpen the blades. Ensure the cutting system is properly aligned to deliver clean cuts.
4. Punching Inaccuracy
- Cause: Worn punching dies or incorrect PLC programming.
- Solution: Inspect the punching dies for wear and replace them if needed. Verify that the punching pattern programmed in the PLC matches the desired design.
5. Machine Downtime
- Cause: Lack of regular maintenance or undetected wear on critical components.
- Solution: Follow a regular maintenance schedule, including lubrication, cleaning, and inspections. Use predictive maintenance features to identify potential issues early.
For expert assistance, contact Wuxi Sunway Machinery, which provides comprehensive support and spare parts for all their machines.
Environmental Impact of PV Mounting Bracket Roll Forming Machines
Sustainability is at the heart of renewable energy, and the machinery that supports it should align with eco-friendly practices. Here’s how PV Mounting Bracket Roll Forming Machines contribute to sustainability:
1. Minimal Material Waste
The roll-forming process is highly efficient, utilizing nearly all of the raw material. Scrap is minimal and can often be recycled, reducing environmental impact.
2. Energy Efficiency
Modern machines are designed to consume less energy while maintaining high production speeds. Features like servo motors and optimized hydraulics ensure lower power consumption.
3. Recyclable Materials
PV mounting brackets are often made from galvanized steel or aluminum, both of which are 100% recyclable. This aligns with global sustainability goals.
4. Long Product Lifespan
The brackets produced by these machines are durable and resistant to corrosion, reducing the need for replacements. This extends the lifecycle of solar installations and minimizes resource usage.
By investing in energy-efficient machinery, manufacturers can align with environmental standards while also reducing operational costs. At Wuxi Sunway Machinery, we prioritize sustainability in our machine designs.
FAQs About PV Mounting Bracket Roll Forming Machines
Here are additional frequently asked questions to address any lingering doubts:
Question | Answer |
---|---|
What is the typical lifespan of these machines? | With proper maintenance, these machines can last 10–15 years or longer. |
Can I produce custom profiles? | Yes, custom machines can be designed to produce unique profiles for specialized applications. |
What’s the average production speed? | Machines typically produce 10–30 meters of brackets per minute, depending on the model. |
Do these machines require skilled operators? | No, advanced PLC systems and automation make these machines user-friendly and easy to operate. |
What materials can be processed? | Most machines handle galvanized steel, stainless steel, and aluminum within a thickness range of 1.5mm–3.5mm. |
Is training provided with the purchase? | Yes, manufacturers like Wuxi Sunway Machinery provide on-site installation and operator training. |
Why Choose Wuxi Sunway Machinery for PV Mounting Bracket Machines?
When it comes to roll-forming machines, Wuxi Sunway Machinery is a trusted name globally. Here’s why:
- Decades of Expertise: Years of experience in designing and manufacturing roll-forming machines for diverse industries.
- Custom Solutions: Fully tailored machines to meet your unique production requirements.
- Global Reputation: Trusted by manufacturers across Asia, Europe, Africa, and beyond.
- Unmatched Quality: Machines built to international standards, ensuring durability and exceptional performance.
- Comprehensive Support: From installation to spare parts and troubleshooting, we’re with you every step of the way.
Conclusion: Is a PV Mounting Bracket Roll Forming Machine Right for You?
With the global solar energy market booming, the demand for PV mounting brackets is higher than ever. A PV Mounting Bracket Roll Forming Machine is an investment in efficiency, scalability, and sustainability, positioning your business to meet this growing demand.
When it comes to choosing a supplier, Wuxi Sunway Machinery stands out for its innovation, reliability, and customer-centric approach. Ready to elevate your production capabilities? Let’s roll into a sustainable and profitable future—together!