Sigma purlin forming machine is an equipment used to produce cold roll forming machine formed C and Z profile purlins for industrial and agricultural applications. Here is a detailed guide on everything related to this equipment.
What is Sigma Purlin Forming Machine?
A sigma purlin forming machine is a type of roll forming machine designed specifically for continuous production of purlins with a C or Z cross-sectional shape.
Purlins are structural beams running horizontally across roofs and walls providing support for roofing material. They are used extensively in industrial, commercial and agricultural building construction applications.
Sigma purlin forming machines allow fast, efficient and cost-effective manufacturing of high quality custom purlins on-demand to meet a facility’s exact specifications.
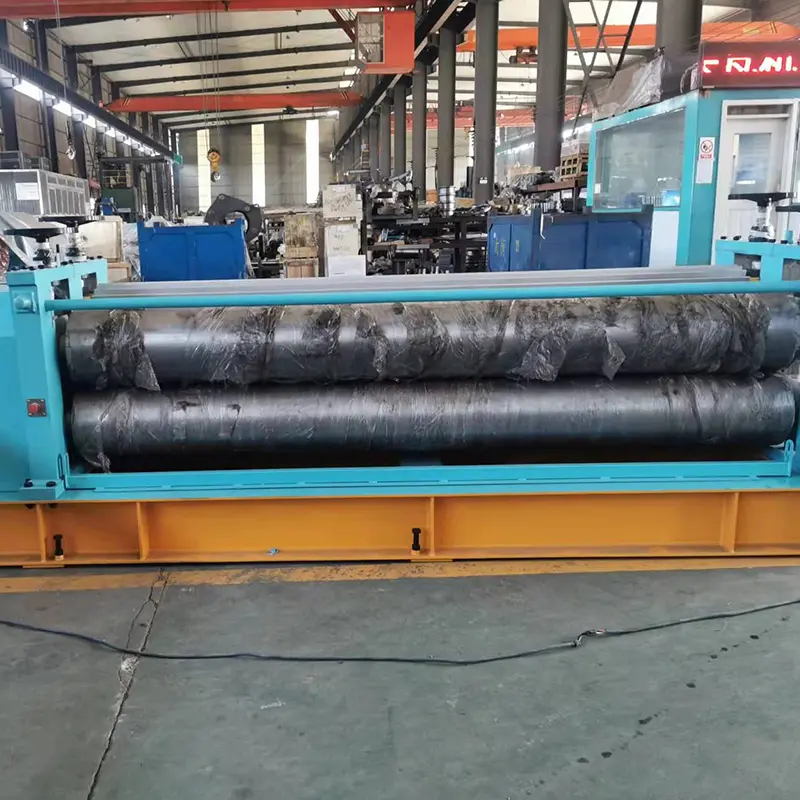
Key Details
Parameter | विवरण |
---|---|
Production Process | Cold roll forming |
End-product | Purlins with C, Z and custom profiles |
Key Components | Uncoiler, roll forming stations, cutoff, stacking/bundling system |
Drives Used | Hydraulic, Servo Electric, Geared AC motors |
नियंत्रण प्रणाली | PLC + HMI touchscreen |
Line Speed | 10-25 m/min based on thickness |
Metal Thickness | 0.3mm – 2mm |
Final Product Length | Customized as per application |
Working Process of Sigma Purlin Forming Machine
The working methodology of sigma purlin forming machine involves uncoiling of metal coil, feeding into a series series of roller stations to form the profile, cutting and finally stacking.
The step-by-step working process is outlined below:
- The input raw material is galvanized steel coil or sheet of the desired thickness and width
- It first passes through the decoiler/uncoiler unit which straightens the coil
- The metal sheet then passes through a series of roller dies stations that gradually bend it into the final C or Z purlin shape through a cold roll forming process
- Each roller station incrementally forms the profile with great precision
- The last station is the cutoff station with rotating shear blades to cut the formed purlins to customized or preset length
- The cut purlins are finally collected on a conveyor or stacking system for packaging and transport
Components of Sigma Purlin Forming Machine
The main components of sigma purlin forming machine are:
- Uncoiler/Decoiler – Feeds metal sheet from coil
- Guiding Rollers – Guides sheet in correct path
- Roll Forming Stations – Gradual profile forming
- Punching Unit – Optional holes punching
- Cutoff Shear – Cuts purlins to length
- Stacker – Collects cut pieces
- Control Panel – Controls line speed, cut length etc.
Additionally, there are mechanisms for part evacuation, safety covers, motors, hydraulics, and sensors to ensure smooth automated production.
-
Highway Guardrail End Terminal Forming Machine
-
Highway U/C Post Roll Forming Machine
-
2 Waves Highway Guardrail Roll Forming Machine
-
3 Waves Highway Guardrail Roll Forming Machine
-
वाइनयार्ड पोस्ट रोल बनाने की मशीन
-
ऑटो आकार बदलने योग्य सिग्मा शहतीर रोल बनाने की मशीन
-
ऑटो आकार बदलने योग्य CZ शहतीर रोल बनाने की मशीन
-
ऑटो आकार बदलने योग्य Z शहतीर रोल बनाने की मशीन
-
ऑटो आकार बदलने योग्य घन शहतीर रोल बनाने की मशीन
Parameters for Specifying Sigma Purlin Forming Machine
While purchasing a sigma purlin forming machine, parameters like production speed, metal thickness, product sizes and features need careful consideration:
Parameter | Typical Range |
---|---|
Metal Thickness | 0.3mm to 2mm |
Sheet Width | Up to 1250mm |
Final Product Length | 1500mm to 15000mm |
Production Speed | 10 to 25 m/min |
Purlin Profile | C, Z and custom |
Hole Punching | Yes/No |
offline/online stacking | Manual or automatic |
Line Automation Level | Semi to fully automatic |
Production Accuracy | +/- 1mm |
Motor Power | 5.5 kW to 22 kW |
Carefully evaluate the application requirements before finalizing the forming line specifications. Reputed manufacturers can also customize the machine configuration to suit unique needs.
Industrial Applications of Sigma Purlin Forming Machines
Sigma purlin forming lines find application across industrial domains:
- Metal Buildings
- Warehouses
- Manufacturing Facilities
- Aircraft Hangars
- Agricultural Sheds
- Commercial Complexes
- Metro Stations
- Shopping Complexes
- Tunnels
- Steel Plants
- Power Plants
- Chemical Plants
Essentially any structure with large exposed roofing area needing strong purlin supports employs these lightweight but very sturdy cold formed sections in huge quantities.
Choosing Reliable Sigma Purlin Forming Machine Manufacturers
Choosing a dependable purlin roll forming machine OEM involves checking:
- Proven experience – Number of years manufacturing
- Production facilities – In-house equipment manufacturing
- Domain expertise – Specialists in designing such lines
- Line capabilities – Offer wide operating ranges
- Customization skills – Offer flexible configurations
- Automation competencies – Ensure fast, reliable production
- Installation support – On-site support for setup
- प्रशिक्षण – Operator training services
- After-sales service – Timely maintenance and parts supply
- Cost economics – Reasonable investment costs
- Quality standards – Strict QA protocols
Reputed companies with abundant technical expertise offer customized, heavy-duty sigma purlin forming equipment built to exceed expectations while maximizing profitability through improved energy efficiency.
Cost Economics of Sigma Purlin Forming Machine
Sigma purlin forming line is a major investment decision with payback period directly related to:
- Production volumes – higher volumes better justify costs
- Energy/labor savings – automated lines cut production expenses
- Product consistency – uniform quality increases customer confidence
- Customization ability – unique profiles fetch premium value
- After-sales support – smooth running with timely service
Typical price range is $100,000 to $300,000 depending on parameters below:
Machine Rating | Price Range |
---|---|
Small | $<150,000 |
Medium | $150,000 – $250,000 |
Large | >$250,000 |
Labor and energy costs form a significant chunk of operating expenses. Investing in automated sigma purlin forming equipment leads to rapid savings through:
- Faster production – increased hourly output
- Fewer rejects – consistent quality
- Lower manpower – reduced labor costs
- Energy conservation – efficient forming technology
20-30% savings can be achieved on production costs with the right machine specification.
Pros and Cons of Sigma Purlin Forming Machine
Pros | Cons |
---|---|
Fast production of high-quality purlins | High initial capital investment |
Exact customized specifications | Complex design needs engineering expertise |
Lightweight but very strong end-products | Regular maintenance requirement |
Consistent and uniform profile | Occupies moderate production floor space |
Automated process saves labor and energy | Limited flexibility compared to manual methods |
Superior finish and durability | Production capacity fixed by machine rating |
Easy scalability by adding lines | After-sales service dependence on supplier |
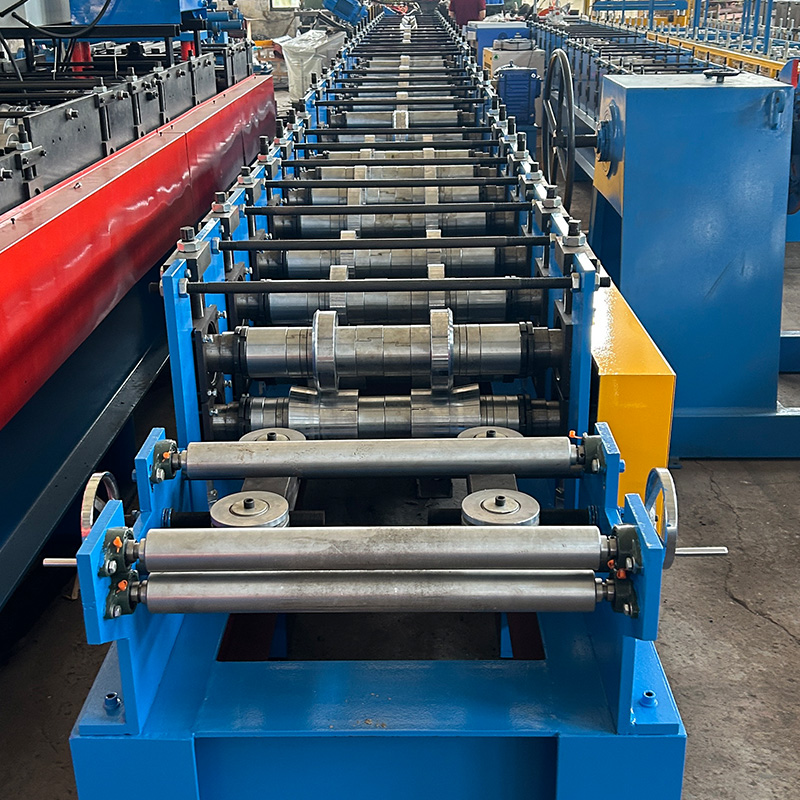
FAQs
Q: What materials can be formed on sigma purlin forming machine?
A: These machines are designed for roll forming steel coils and sheets. Galvanized steel is most common but some lines can also process stainless steel, aluminum and other metal coils.
Q: Can one machine make different sized purlins?
A: Yes, by adjusting the cutoff shear and line speed different purlin lengths can be produced from the same machine. However width is fixed as per tooling limit.
Q: What automation types are available?
A: Options range from semi-automatic needing manual offloading to fully automatic lines with inline stacking, bundling and even packaging. Level of automation depends on production volumes and budget.
Q: What regular maintenance is required?
A: Requirements involve lubrication, tension checks, calibrating shear cut length, wear check on forming rollers, sensor cleaning and overhaul of hydraulic/electrical components. Annual servicing contracts are highly recommended.
Q: What is the typical delivery time?
A: For standard designs delivery takes 8-12 weeks. For customized lines with engineering it may take 12-16 weeks. Reputed large manufacturers have capability to deliver multiple lines simultaneously.