From suburban homes to commercial complexes, siding panels play a pivotal role in enhancing the aesthetics and functionality of modern structures. The seamless integration of these panels owes much of its success to the innovation of siding panel roll forming machines. In this article, we delve into the world of these machines, their benefits, operational insights, and their impact on the construction industry.
परिचय
In the realm of construction, efficiency, precision, and quality are paramount. The introduction of siding panel roll forming machines has significantly transformed the way siding panels are manufactured and installed. These machines automate the process of creating intricate panel designs from raw materials, ensuring consistent quality while reducing manual labor.
Understanding Siding Panels
Siding panels, typically made from materials like metal, vinyl, or fiber cement, serve both functional and decorative purposes. They provide insulation, weather resistance, and act as a protective barrier against external elements. Siding panel roll forming machines enable manufacturers to create panels with precise dimensions and customizable designs, catering to the diverse needs of architects and homeowners.
Types of Siding Panels
- Metal Siding Panels
- Vinyl Siding Panels
- Fiber Cement Siding Panels
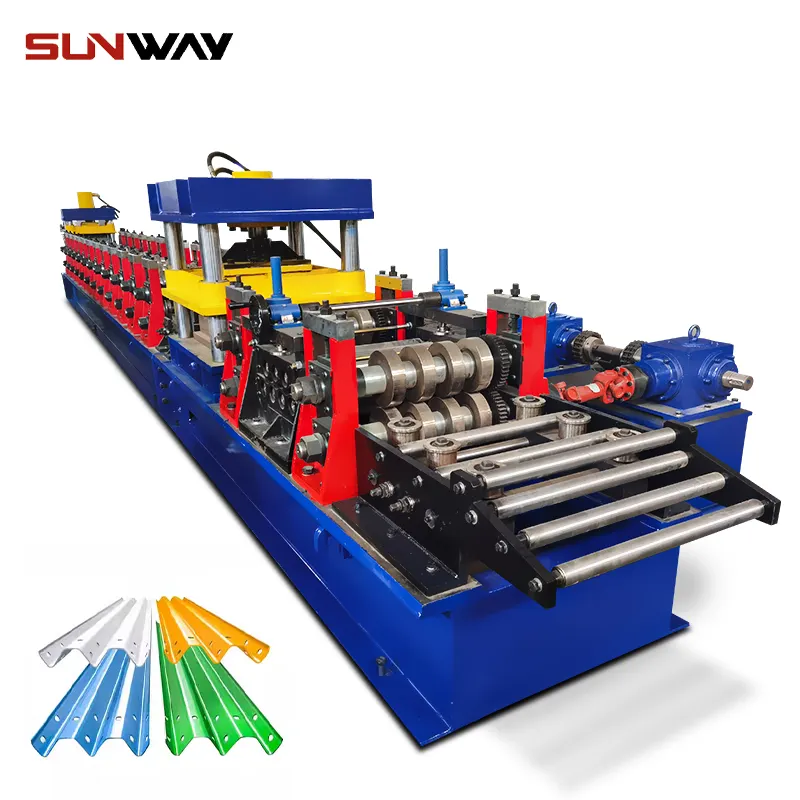
The Role of Roll Forming Machines
Roll forming machines are the backbone of the siding panel manufacturing process. These machines take flat strips of material and pass them through a series of rollers, gradually forming them into the desired shape. The process is continuous, allowing for high-volume production with minimal wastage.
Advantages of Roll Forming
- Consistent Quality
- High Efficiency
- Design Flexibility
Advantages of Siding Panel Roll Forming Machines
Siding panel roll forming machines offer a plethora of benefits to manufacturers and end-users alike. These advantages have contributed to their widespread adoption in the construction industry.
Precise Panel Dimensions
The roll forming process ensures that each panel is manufactured with precise dimensions, eliminating variations that can arise from manual fabrication.
गति और दक्षता
Roll forming machines can produce a large volume of panels in a relatively short time, enhancing overall project efficiency.
Design Customization
Architects and homeowners can explore intricate panel designs, and roll forming machines can replicate these designs accurately and consistently.
Reduced Labor Dependency
The automation of the manufacturing process significantly reduces the need for manual labor, leading to cost savings and minimized human error.
Key Features to Look for in a Roll Forming Machine
When considering the purchase of a siding panel roll forming machine, several key features should be taken into account.
Material Compatibility
Different roll forming machines cater to various materials. Choosing the right machine for the intended material is crucial for optimal results.
Customization Options
The machine’s ability to accommodate custom designs and adjustments is vital for meeting specific project requirements.
Production Speed
The production speed of the machine impacts the project timeline and delivery commitments.
Durability and Maintenance
Investing in a durable machine with easy maintenance ensures longevity and reduces downtime.
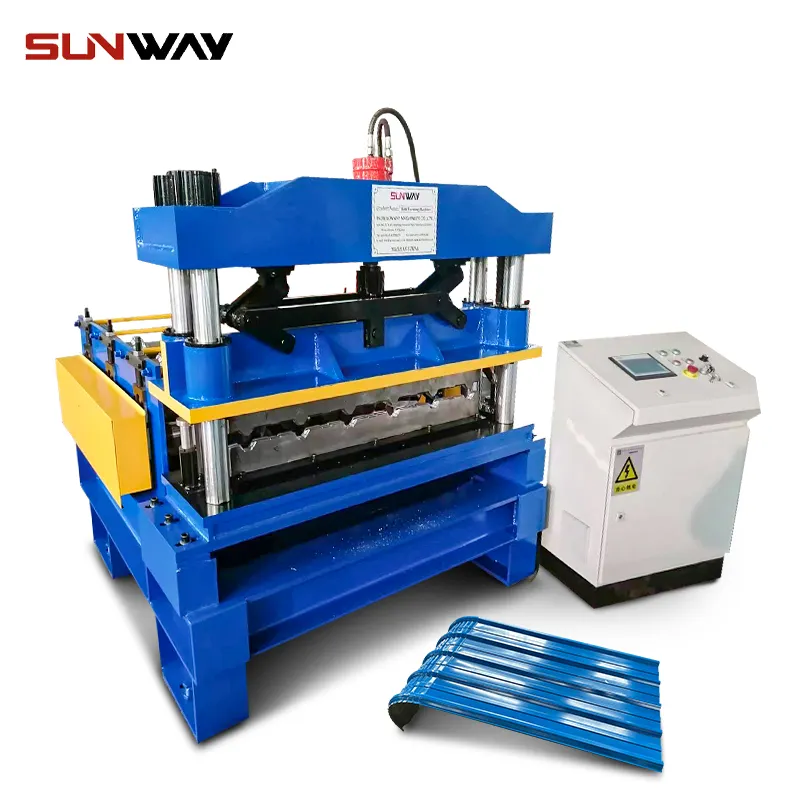
Choosing the Right Siding Panel Roll Forming Machine
The selection process involves a thorough assessment of the project’s needs, production volume, and customization requirements.
Project Requirements Assessment
Understanding the scope of the project, material preferences, and design specifications is the first step in making an informed choice.
Consultation with Manufacturers
Collaborating with roll forming machine manufacturers can provide insights into the best-fit solution for the project’s needs.
Cost-Effectiveness Evaluation
Balancing the initial investment with long-term benefits and ROI is essential for financial feasibility.
Step-by-Step Guide to Operating the Machine
Operating a siding panel roll forming machine requires proper training and adherence to safety guidelines. Here’s a step-by-step guide:
Material Loading
Place the raw material onto the machine’s feeding system, ensuring it is properly aligned.
Machine Setup
Adjust the machine’s settings according to the material type, design, and dimensions required.
Start the Machine
Initiate the machine, and observe the forming process to ensure it’s proceeding correctly.
Quality Checks
Regularly inspect the formed panels for any defects or deviations from the desired specifications.
Unloading Finished Panels
As the panels are formed, carefully remove them from the machine and prepare them for further processing or installation.
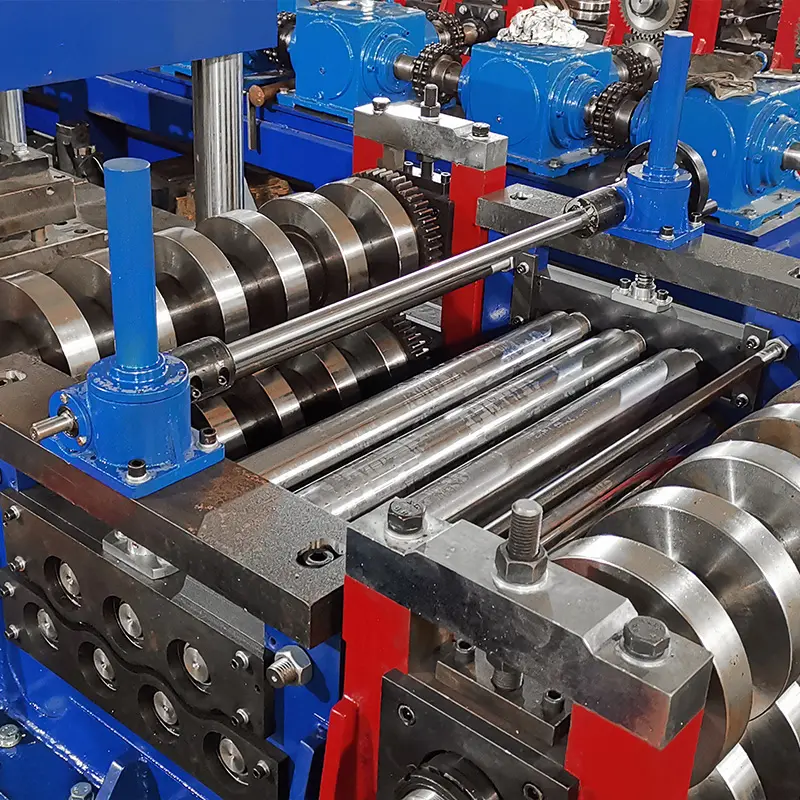
Maintenance and Care of Roll Forming Machines
Proper maintenance ensures the longevity and consistent performance of the roll forming machine.
Regular Lubrication
Keep the machine’s moving parts well-lubricated to prevent friction-related issues.
Cleaning and Inspection
Regularly clean the machine and inspect for any signs of wear or damage that might affect performance.
Component Replacement
Replace worn-out or damaged components promptly to prevent production interruptions.
Common Challenges and Troubleshooting
While roll forming machines offer remarkable benefits, they can encounter challenges that need troubleshooting.
Material Jamming
Improper material feeding can lead to jamming. Clearing the jam and adjusting the feeding mechanism can resolve this.
Forming Inaccuracies
Deviation from the desired panel shape might occur due to misaligned rollers or incorrect machine settings.
Maintenance Neglect
Neglecting maintenance can result in decreased efficiency and quality. Regular upkeep is key.
Innovations in Siding Panel Manufacturing
The roll forming technology continues to evolve, bringing forth innovations that enhance efficiency and design possibilities.
Computer-Aided Design (CAD)
CAD software allows for intricate and detailed panel designs that can be translated accurately by roll forming machines.
Smart Automation
Integration of automation and data-driven systems optimizes production and reduces errors.
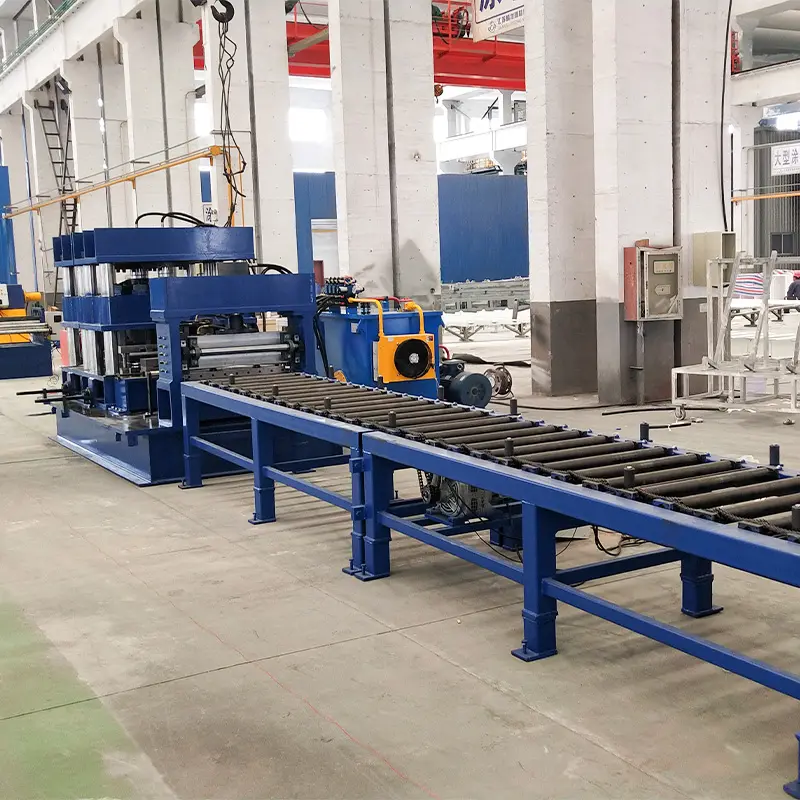
The Future of Roll Forming Technology
The roll forming industry is poised for further growth with advancements in automation, materials, and sustainability.
Sustainability Integration
Efforts to make roll forming more eco-friendly include material recycling and energy-efficient processes.
Enhanced Design Capabilities
Future roll forming machines may offer even more intricate designs, catering to architectural trends.
Cost Considerations and Return on Investment
Investing in a siding panel roll forming machine involves an initial financial outlay, but it’s essential to consider the long-term benefits and return on investment.
Initial Investment
The cost of a roll forming machine varies based on factors such as size, features, and brand reputation. While the upfront expense might seem significant, it’s crucial to analyze the potential cost savings and efficiency gains over time.
Reduced Labor Costs
One of the primary advantages of roll forming machines is the reduction in labor dependency. With fewer manual processes, labor costs are minimized, and the machine’s efficiency increases productivity.
Consistent Quality
The precision offered by roll forming machines ensures that the produced panels are of consistent quality. This can lead to fewer defects and reduced waste, contributing to overall cost savings.
Increased Production Speed
The high-speed production capabilities of roll forming machines result in quicker project completion, allowing manufacturers to take on more projects and increase revenue.
Long-Term Savings
The durability and minimal maintenance requirements of quality roll forming machines translate to long-term cost savings, as there’s reduced need for frequent repairs or replacements.
Case Studies: Successful Implementation
Real-world examples showcase the impact of siding panel roll forming machines in various industries.
Residential Construction
A residential construction company implemented a roll forming machine for its metal siding panels. The efficiency boost allowed them to complete projects ahead of schedule, leading to higher customer satisfaction and increased referrals.
Commercial Development
In a commercial development project, a fiber cement siding manufacturer adopted a roll forming machine with advanced customization capabilities. This enabled them to cater to intricate architectural designs, securing contracts for high-profile projects.
Environmental Impact and Sustainability
As the construction industry places greater emphasis on sustainability, roll forming technology contributes to environmental conservation.
Material Efficiency
Roll forming machines optimize material usage, minimizing waste and reducing the overall environmental impact.
Energy Efficiency
Many modern roll forming machines incorporate energy-efficient features, aligning with eco-friendly practices.
Recyclability
Materials used in siding panel manufacturing, such as metal and certain plastics, can often be recycled, further reducing the industry’s carbon footprint.
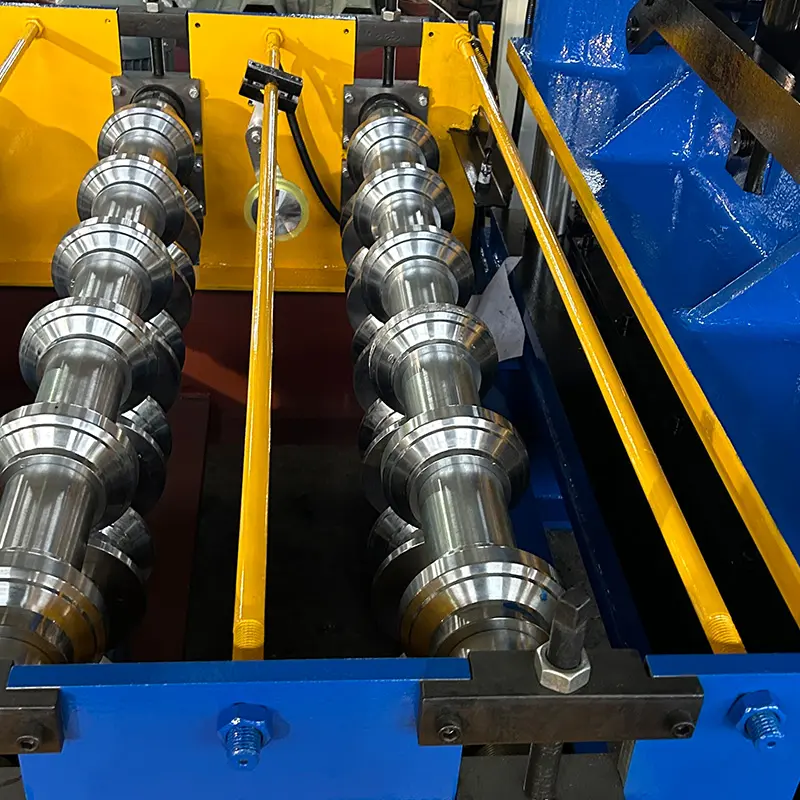
निष्कर्ष
Siding panel roll forming machines have revolutionized the construction industry by offering precise, efficient, and customizable manufacturing processes. From their advantages in quality control and design flexibility to their role in shaping sustainable construction practices, these machines are an indispensable asset to modern construction projects. As technology continues to evolve, we can anticipate even more innovative advancements in roll forming that will shape the future of construction.
Frequently Asked Questions
Q1: What materials are commonly used for siding panels? A1: Siding panels are often made from materials like metal, vinyl, and fiber cement.
Q2: How do roll forming machines improve efficiency in siding panel production? A2: Roll forming machines automate the manufacturing process, reducing manual labor and increasing production speed.
Q3: Can roll forming machines create intricate panel designs? A3: Yes, roll forming machines can replicate intricate designs accurately and consistently.
Q4: Are roll forming machines eco-friendly? A4: Yes, roll forming machines contribute to sustainability by optimizing material usage and incorporating energy-efficient features.
Q5: What’s the future of roll forming technology in construction? A5: The future holds advancements in automation, sustainability, and enhanced design capabilities, shaping the construction industry’s landscape.