Shutter door roll forming machines are essential equipment in the manufacturing process of various types of shutter doors, providing efficient and precise shaping of metal sheets. In this comprehensive guide, we’ll address the most common questions about these machines, from their functionality to maintenance.
Most Asked Questions about Shutter Door Roll Forming Machines
Question | Answer |
---|---|
What is a shutter door roll forming machine? | A shutter door roll forming machine is an industrial equipment used to shape metal sheets into shutter doors. |
What are the key components of these machines? | These machines consist of decoilers, feeding systems, roll forming sections, hydraulic systems, and cutters. |
What types of materials can be used with these machines? | Shutter door roll forming machines primarily work with galvanized steel, stainless steel, and aluminum. |
How does the roll forming process work? | The process involves feeding the metal sheet into the machine, passing it through rollers to shape it. |
What are the main applications of shutter doors? | Shutter doors find usage in commercial, industrial, and residential spaces for security and insulation. |
Are custom designs possible with these machines? | Yes, these machines can be adjusted to create various sizes and designs of shutter doors as needed. |
What safety measures should be considered? | Operators should receive proper training, and safety guards and emergency stop buttons must be in place. |
How do you maintain a shutter door roll forming machine? | Regular inspection, lubrication, and alignment checks are necessary to ensure optimal machine performance. |
What sets apart a high-quality machine from the rest? | High-quality machines offer precision, durability, ease of operation, and good customer support. |
How can I choose the right machine for my business? | Consider factors like production volume, material type, budget, and the machine’s versatility and speed. |
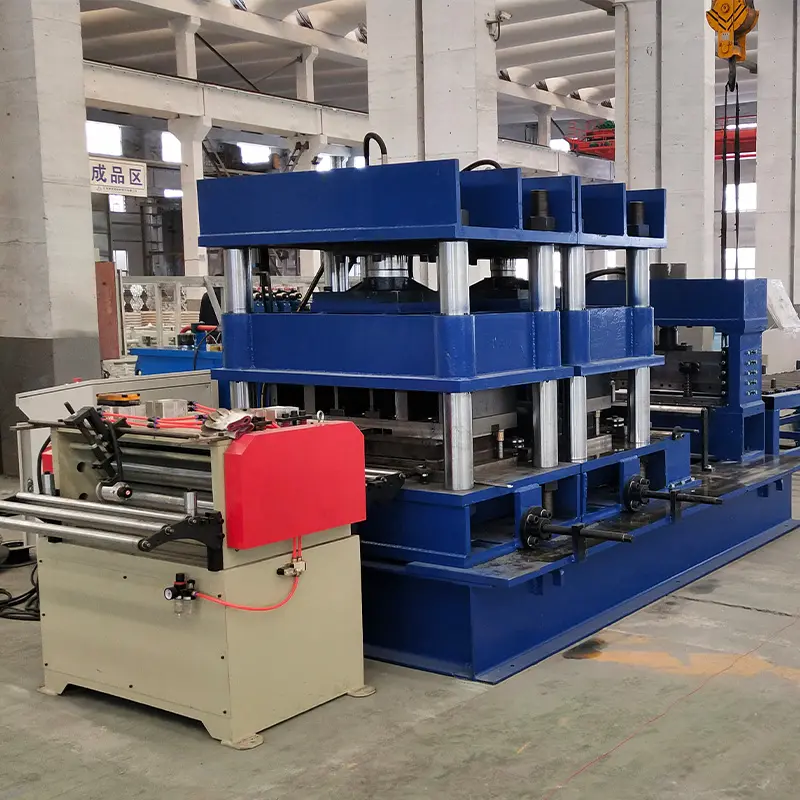
What is a Shutter Door Roll Forming Machine?
ए shutter door roll forming machine is a specialized piece of industrial equipment designed to transform metal sheets into shutter doors commonly used in various applications, including commercial, industrial, and residential spaces. These machines play a pivotal role in the manufacturing process by precisely shaping metal sheets according to specific designs and dimensions.
Key Components of Shutter Door Roll Forming Machines
A typical shutter door roll forming machine consists of several essential components:
- Decoilers: These are used to hold and feed the raw metal coils into the machine.
- Feeding System: The feeding system guides the metal sheet into the roll forming sections.
- Roll Forming Sections: These sections consist of sets of rollers that gradually shape the metal into the desired profile.
- Hydraulic Systems: Hydraulics are responsible for controlling various movements of the machine, such as cutting and bending.
- Cutting Mechanism: This component cuts the shaped metal sheet to the required length.
- Control Panel: The control panel allows operators to set parameters and monitor the machine’s performance.
The Roll Forming Process
The roll forming process is the heart of a shutter door roll forming machine. Here’s a simplified breakdown of how it works:
- Material Feeding: The process begins with feeding a metal sheet coil into the machine’s decoiler.
- रोल बनाना: The metal sheet moves through a series of rollers, each set gradually bending and shaping the material.
- Guiding and Cutting: As the metal sheet takes shape, guide rollers ensure proper alignment, and the cutting mechanism trims the sheet to the desired length.
- Final Product: Once the sheet passes through all the roll forming sections, it emerges as a fully shaped shutter door profile ready for assembly.
The versatility of these machines allows for customization, enabling the creation of various shutter door designs and sizes.
Advantages of Shutter Doors
Shutter doors produced using roll forming machines offer several advantages:
- Security: Shutter doors enhance security for commercial and industrial spaces, safeguarding against unauthorized access.
- Insulation: These doors provide insulation, helping regulate indoor temperatures and reduce energy consumption.
- Durability: Metal construction ensures longevity and resistance to weather conditions and wear.
In conclusion, shutter door roll forming machines are pivotal in producing high-quality shutter doors with precision and efficiency. Their ability to shape different metals and accommodate custom designs makes them indispensable in various industries.
Types of Materials for Shutter Door Roll Forming Machines
Shutter door roll forming machines are versatile tools that can work with a range of materials. The type of material used affects the door’s appearance, strength, and durability. Here are the main materials commonly used in the roll forming process:
- Galvanized Steel: This is the most popular material due to its excellent corrosion resistance. It’s often used in outdoor settings where exposure to weather elements is a concern.
- Stainless Steel: Stainless steel offers enhanced durability and rust resistance. It’s a preferred choice for environments with high humidity or chemical exposure.
- Aluminum: Aluminum is lightweight and corrosion-resistant, making it suitable for applications where weight is a concern, such as in residential areas.
- Color-Coated Steel: This type of steel is pre-painted, providing aesthetic appeal and additional protection against the elements.
- Cold-Rolled Steel: Cold-rolled steel is processed at lower temperatures, resulting in a smoother finish and tighter tolerances.
When selecting a material, consider factors such as the door’s intended use, the environment it will be installed in, and the desired aesthetics.
The Roll Forming Process Demystified
The roll forming process is the heart of a shutter door roll forming machine, enabling the transformation of flat metal sheets into complex shutter door profiles. Here’s a step-by-step breakdown of the roll forming process:
- Material Loading: A metal coil is loaded onto the decoiler, and the feeding system guides the material into the roll forming sections.
- Roll Forming Stations: The roll forming sections consist of multiple stations, each with a set of rollers. These rollers gradually shape the metal by bending it incrementally.
- Guiding and Alignment: Guide rollers ensure that the metal follows the correct path through the forming stations, maintaining alignment for accurate shaping.
- Profile Creation: As the metal passes through each station, it takes on the desired profile. The number of stations depends on the complexity of the design.
- Cutting Mechanism: Once the metal sheet reaches the end of the forming process, a cutting mechanism trims it to the required length. This can involve flying shears, hydraulic cutters, or other methods.
- Finished Product: The shaped and cut metal sheet is now a fully formed shutter door profile, ready for further assembly and installation.
The roll forming process offers several benefits, including high efficiency, precision, and the ability to produce consistent shapes in large quantities.
Exploring Shutter Door Applications
Shutter doors are versatile products with a wide range of applications in various industries. Their design and functionality make them suitable for different purposes, primarily revolving around security, insulation, and convenience. Here are some common applications of shutter doors:
- Commercial Spaces: Shutter doors are commonly used in shops, warehouses, and garages to provide security during non-business hours.
- Industrial Facilities: Industries utilize shutter doors for securing entrances to factories, warehouses, and manufacturing plants.
- Residential Use: Shutter doors offer homeowners security, privacy, and insulation benefits, making them suitable for garages, storage spaces, and even windows.
- Emergency Exits: In larger buildings, shutter doors can serve as emergency exits, allowing quick evacuation during emergencies.
- Loading Docks: Shutter doors are often installed in loading docks to secure cargo areas and provide efficient loading and unloading.
- Climate Control: Shutter doors can help regulate temperature and control airflow, making them valuable in spaces where environmental control is crucial.
These applications demonstrate the versatility and importance of shutter doors in modern construction and security practices.
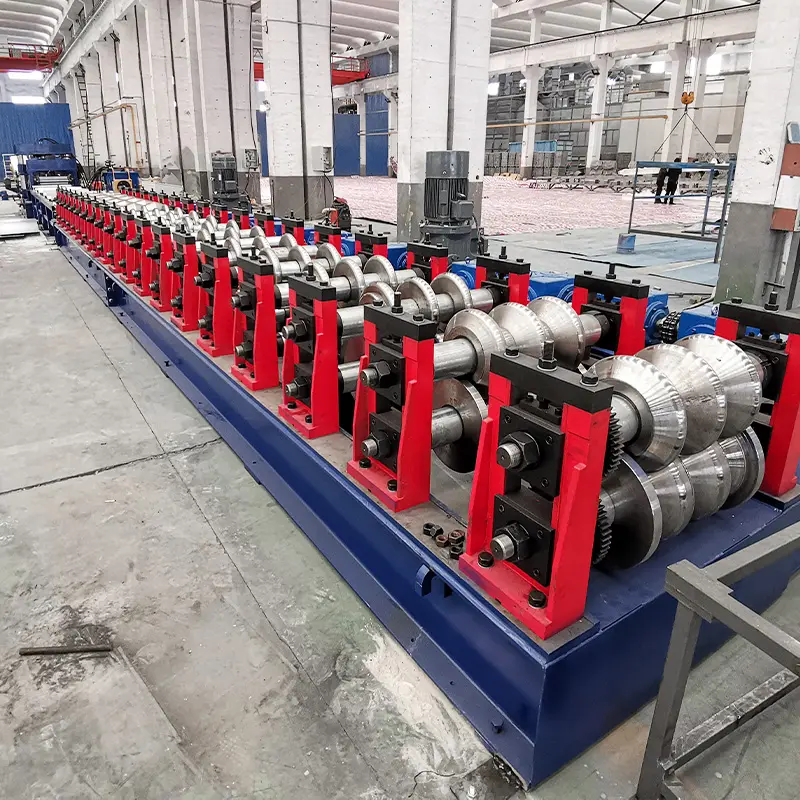
Customization Possibilities with Shutter Door Roll Forming Machines
One of the significant advantages of using shutter door roll forming machines is the ability to create customized designs to meet specific requirements. Whether you’re producing doors for residential, commercial, or industrial use, these machines offer flexibility in design and dimensions.
Tailored Sizes
Shutter door roll forming machines can be adjusted to produce doors of various sizes. This adaptability ensures that doors fit precisely in their intended spaces, whether it’s a small window or a large warehouse entrance.
Unique Profiles
The roll forming process allows for the creation of unique door profiles. This means you can design doors with specific patterns, textures, and features that align with your project’s aesthetics and functionality.
Material Choice
Customization also extends to the choice of materials. Depending on the application and environment, you can select the most suitable material—be it galvanized steel for robust security or aluminum for lightweight convenience.
Additional Features
Shutter doors can be enhanced with additional features like insulation materials, vision panels, or ventilation options. These features can be incorporated during the roll forming process, ensuring seamless integration.
In essence, the customization possibilities offered by shutter door roll forming machines empower businesses and individuals to create doors that perfectly fit their needs, enhancing both functionality and visual appeal.
Ensuring Safety When Operating Shutter Door Roll Forming Machines
Safety is paramount when working with any industrial equipment, including shutter door roll forming machines. Operating these machines requires careful adherence to safety protocols to prevent accidents and ensure the well-being of operators. Here are some essential safety measures to consider:
- Operator Training: Ensure that operators are properly trained in using the machine, including its controls, emergency stop procedures, and potential hazards.
- Safety Guards: Install safety guards around moving parts to prevent accidental contact and provide a barrier between operators and the machine’s mechanisms.
- Emergency Stop Button: Equip the machine with easily accessible emergency stop buttons that immediately halt all machine movements in case of a safety concern.
- Lockout/Tagout: Implement lockout/tagout procedures to secure the machine during maintenance or repair, preventing unexpected startups.
- Personal Protective Equipment (PPE): Operators should wear appropriate PPE, such as gloves, safety glasses, and ear protection, to minimize the risk of injury.
- Proper Lighting: Ensure the work area is well-lit to help operators see clearly and avoid potential hazards.
- Regular Maintenance: Regularly inspect and maintain the machine to address any issues that could compromise safety.
- Clear Workspace: Keep the work area free from clutter and obstacles that could impede safe operation.
By prioritizing safety and providing proper training and equipment, you can create a secure working environment for those operating shutter door roll forming machines.
Maintenance Tips for Long-Lasting Shutter Door Roll Forming Machines
Proper maintenance is crucial to ensure the longevity and consistent performance of your shutter door roll forming machine. Regular upkeep helps prevent breakdowns and costly repairs. Here are some maintenance tips to follow:
- Scheduled Inspections: Regularly inspect all components, including rollers, belts, and hydraulic systems, for signs of wear, damage, or misalignment.
- Lubrication: Keep moving parts well-lubricated according to the manufacturer’s guidelines to reduce friction and extend the machine’s lifespan.
- Alignment Checks: Ensure that all components are properly aligned to prevent uneven wear and to maintain the accuracy of the roll forming process.
- Cleaning: Keep the machine clean by removing debris, dust, and metal shavings. Cleanliness prevents interference with moving parts and maintains precision.
- Electrical Systems: Inspect electrical connections for loose wires or corrosion. Ensure that all electrical components are in good condition.
- Hydraulic System: Regularly check hydraulic fluid levels and replace or top up fluids as needed. Look for leaks or signs of degradation in hoses.
- Software Updates: If your machine has a control panel, keep its software updated to ensure it functions optimally and efficiently.
- Record Keeping: Maintain a maintenance log that tracks inspections, repairs, and any servicing performed on the machine.
By following these maintenance practices, you can ensure that your shutter door roll forming machine remains in excellent working condition, providing consistent and reliable performance over the long term.
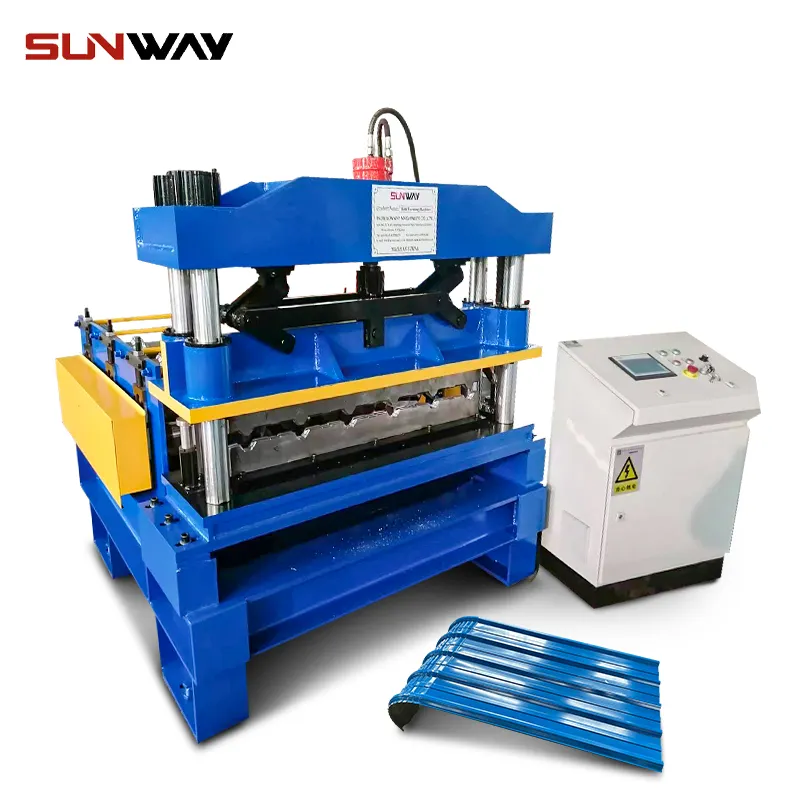
Distinguishing High-Quality Shutter Door Roll Forming Machines
Investing in a high-quality shutter door roll forming machine is essential for achieving consistent results and minimizing downtime. Here are some factors to consider when identifying a top-tier machine:
- Build Quality: High-quality machines are constructed using durable materials, ensuring stability and longevity.
- Precision: Look for machines that offer precise shaping and cutting capabilities, resulting in accurate and uniform shutter door profiles.
- Durability: A reliable machine should be able to withstand continuous use without frequent breakdowns or maintenance.
- Ease of Operation: User-friendly controls and an intuitive interface contribute to a smoother workflow and reduced operator errors.
- Support and Training: Manufacturers that provide comprehensive training and reliable customer support can help operators maximize machine efficiency.
- Customization Options: A high-quality machine should be adaptable, allowing for easy adjustments to accommodate various shutter door designs and sizes.
- Safety Features: Advanced safety features, such as emergency stop buttons and safety interlocks, ensure operator well-being.
- Feedback and Reviews: Research customer feedback and reviews to gain insights into the real-world performance of the machine.
Investing in a high-quality machine might require a larger initial investment, but it pays off in terms of productivity, longevity, and consistent output.
Choosing the Right Shutter Door Roll Forming Machine for Your Needs
Selecting the appropriate shutter door roll forming machine for your business is a critical decision that requires careful consideration. Here are some steps to help you make the right choice:
- Production Volume: Determine your expected production volume. This will influence the machine’s speed and capacity you need.
- Material Compatibility: Consider the types of materials you plan to work with and ensure the machine can handle them effectively.
- Design Flexibility: Assess whether the machine allows for easy customization and adjustments to suit different designs.
- Space and Layout: Evaluate the available workspace and ensure the machine’s dimensions fit comfortably.
- Budget: Set a realistic budget and find a machine that offers the best value for your investment.
- Manufacturer Reputation: Research the reputation of the manufacturer. Choose a reputable company with a history of producing reliable machines.
- Technical Support: Ensure that the manufacturer provides training, technical support, and readily available replacement parts.
- Warranty: Check the warranty terms to understand the coverage and support provided by the manufacturer.
By considering these factors, you can make an informed decision and choose a shutter door roll forming machine that aligns with your business requirements and goals.
सामान्य प्रश्न
Q1: Can these machines handle different thicknesses of metal sheets?
Yes, shutter door roll forming machines are designed to work with various thicknesses of metal sheets. They can be adjusted to accommodate different gauge sizes, ensuring flexibility in production.
Q2: Are there safety measures to prevent material jams during the roll forming process?
Yes, modern shutter door roll forming machines are equipped with sensors and mechanisms that detect material jams or irregularities. These safety features prompt the machine to stop or reverse the process, preventing damage and ensuring operator safety.
Q3: Can I integrate automation with these machines?
Yes, many shutter door roll forming machines can be integrated with automation systems, allowing for more streamlined and efficient production. Automation can include material feeding, profile cutting, and stacking of finished products.
Q4: What maintenance tasks can I perform myself?
Operators can typically perform tasks such as regular cleaning, lubrication, and visual inspections. However, more complex maintenance tasks, such as adjusting the alignment of rollers, may require the expertise of a technician or engineer.
Q5: How do I troubleshoot common issues during operation?
Shutter door roll forming machines often come with detailed user manuals that include troubleshooting guides for common issues. Following these guides can help operators address minor problems and maintain smooth operation.