ए shelf rack roll forming machine is an essential equipment for factories and warehouses that produce storage rack systems. This guide provides a comprehensive overview of shelf rack roll forming technology, including working principles, types of machines, major components, production processes, application areas, selection factors when choosing a supplier, installation and maintenance procedures, advantages and limitations compared to other methods, and frequently asked questions.
Introduction to Shelf Rack Roll Forming
Roll forming is a continuous bending operation in which sheet or strip metal is gradually shaped as it passes through consecutive rolls until the desired cross-section profile is obtained. Roll forming machinery is used for efficient, high-volume production of rack components with accurate tolerances and low operational costs.
Compared to other fabrication techniques like laser cutting, punching, pressing or welding, roll forming is ideal for creating long shelf beams, uprights, braces and connectors in rack structures from coiled steel. Custom profiles are also possible based on application requirements.
The formed parts have consistent quality and dimensional precision along the length from in-line automated cutting. Material waste is minimal due to nesting software. Quick die changeovers facilitate flexibility in production schedules. Overall, roll forming enables rack manufacturers to meet increasing demand rapidly and economically.
Working Principle
In a shelf rack roll forming machine, the raw input sheet or coil material passes through a series of consecutive rolling stands. Each rolling stand incrementally forms the material to the desired shape as it progresses down the line.
The rolling stands consist of an upper and lower set of rollers designed specifically for creating rack profiles. The rollers apply pressure to bend the strip as it feeds through continuously. Automated feeding mechanisms with pinch rollers ensure precise material guidance into the roll tooling.
As the material exits the final roll station, it has achieved the fully formed cross-section of the rack component like a beam, column, brace etc. The continuously formed parts can then move to additional integrated machines for processing steps like punching holes, slicing to length before automatic stacking.
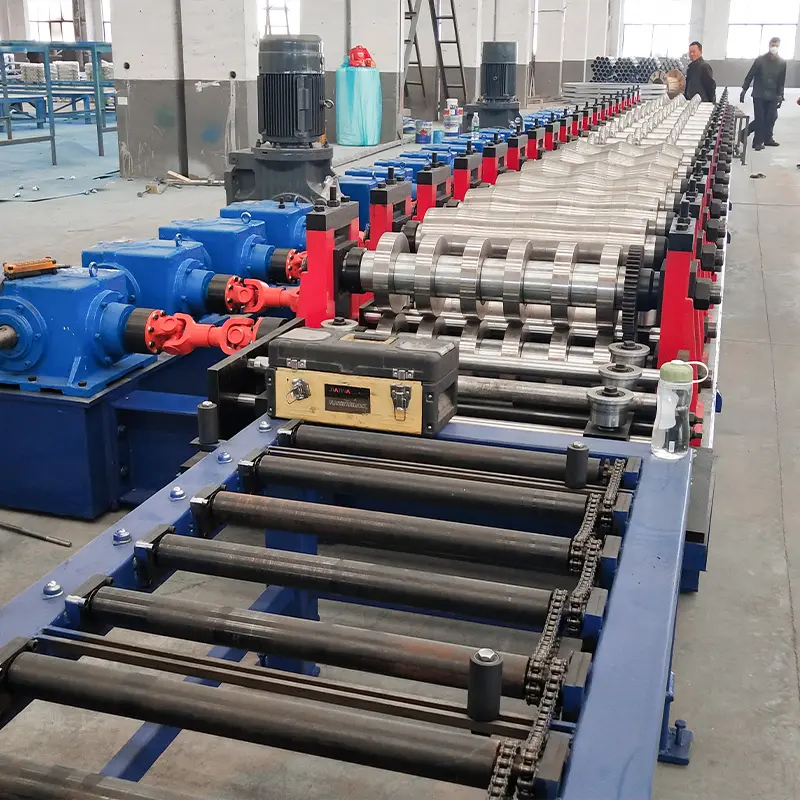
Types of Roll Formed Rack Products
Shelf racks are structural frameworks made of cold-formed steel sections that act as storage systems to support material loads on horizontal levels. They provide adjustable, modular platforms for factories, warehouses, retail stores, etc. Some commonly roll formed components include:
Rack Beams – Horizontal load bearing members with tabs, holes for connections
Uprights / Columns – Vertical members with holes to adjust beam positions
Braces and Gussets – Diagonal braces for stability and joint rigidity
Connectors – Special rivets, bolts to fasten members at intersections
Shelf Rack Roll Forming Machine Guide
This section explains the key aspects to consider when selecting and using a shelf rack roll forming line for in-house rack fabrication or working with roll forming equipment suppliers.
1. Material Feeding
The input material for roll forming can be supplied either as sheets of fixed width or coils of narrower widths. Coil lines are more common as they avoid scrap loss from shearing sheets and support high volume production with automated unwinding.
| Sheet Lines | Suitable for low to medium production volumes where frequent size changes occur. Manual loading of cut sheets. | | Coil Lines | Higher output rates possible with automatic coil unwinding and smooth workflow. |
2. Forming Capacity
The size range and speed determine overall capacity:
- मोटाई – 0.5 mm to 2 mm cold rolled steel
- Width – Up to 1200 mm
- Length – 1 m to 9 m (or higher)
- Speed – Up to 30 m/min (varying based on complexity)
Higher the number of roller heads, larger the cross-sections that can be formed. Advanced 3D forming is possible with up to 10 rolling steps in one machine.
3. Profile Design
The roll tooling consists of upper and lower rollers machined to gradually create the cross-sectional shape across the width. New profiles require design, machining and assembly of custom roll sets specific to each geometry.
Standard profiles are available but for specialty applications unique shapes may need engineering – example perforations for reduced weight and cost.
4. Automated Cutting
As the continuously formed profile exits the final station, computer controlled saws slice the longitudinal beam/column to desired lengths for shelving bays, upright frames etc., thereby maximizing material yield.
Additional cutting units create notches, holes or complex contours along the length if needed. Precision servo electric saws allow narrower pitches for dense storage racks.
5. Part Handling Systems
For large volumes, exit conveyors with automated stackers efficiently move finished cut components for anti-rust treatment, packaging and dispatch. Inline robotic pick-and-place systems directly feed other machines like drilling lines if secondary processing is needed.
6. Production Monitoring
Modern lines have touchscreen HMI, industrial PCs for monitoring current status, registering orders, reporting defects, maintenance tracking and analyzing historical performance. SCADA software can remotely access data for optimizing overall equipment effectiveness.
7. Customization Options
- Logo marking by embossing rollers
- Print registration for serialized labels, barcodes
- Hole punching for modular adjustment
- Profile wrapping for safety, aesthetics
- Special surface coatings
Top Shelf Rack Roll Forming Machine Manufacturers
कंपनी | Location | Typical Price Range |
---|---|---|
ECC Co., Ltd | Taiwan | $100k – $250k |
फॉर्मटेक ग्रुप | China | $50k – $500k |
DIMECO Group | इटली | $250k – $750k |
Finn-Power | Finland | $200k – $800k |
Kingsland | United Kingdom | $150k – $800k |
-
Standing Seam Roof Panel Curving Machine
-
बैरल नालीदार रोल बनाने की मशीन
-
Stand Seaming Roof Panel Roll Forming Machine
-
डाउनस्पॉट पाइप रोल बनाने की मशीन
-
गटर रोल बनाने की मशीन
-
Trapezoidal Panel Roll Forming Machine
-
रिज कैप रोल बनाने की मशीन
-
डबल परत पैनल रोल बनाने की मशीन
-
रूफ टाइल पैनल रोल बनाने की मशीन
How to Select a Shelf Rack Roll Forming Machine
Choosing the optimal roll forming equipment for rack production depends on business-specific factors. This section covers the key considerations.
Installation Requirements
- Floor space
- Power – up to 75 kW connected load
- Compressed air – 10 bar pressure
- Material handling space for coils, stacker
- Ambient operating temperatures
Proper grounding, ventilation and safety mechanisms must be provisioned. Field commissioning by technician is included.
Output Considerations
- Yearly volume in linear meters
- Cycle times for profiles based on length, thickness and complexity
- Material types – mild steel, stainless steel, aluminum
- Secondary processes needed – hole punching, notching, wrapping etc
Flexibility Needs
- Frequency of profile changes
- Range of sizes – thickness, width and lengths
- Types of sections – beams, columns, braces etc
Tooling modularity to accommodate variety of parts vs dedicated roll sets for high volume commodity profiles
Cost Factors
- Machine price – base model starts ~$100k, heavily customized lines ~$500k+
- Profile design charges – $5k upwards per profile
- Tooling cost – $20k to $60k for full tool sets
- Freight, taxes, installation extras
- Production rebates from suppliers likely on orders above 500 tons/yr
Software Capabilities
- 3D modeling of shapes
- Virtual simulation of rolling process
- Programming interface flexibility
- Communication protocols to other equipment
- Diagnostics modes, data logging and analytics
Advanced controls and interoperability reduce manual efforts in operation or maintenance.
Service Support
- Responsiveness to technical queries
- Maintenance visits per year by technician
- Inhouse team v/s local agents for parts, repairs
- Operator training provision
- Software upgrades over lifetime
Evaluate complete ownership costs over 10-15 years lifespan along with supplier relationship factors.
Roll Forming Machine Installation, Operation and Maintenance
Proper installation, daily operation and preventive maintenance are vital for trouble-free functioning, safety and longevity of roll forming equipment. Workers should follow the protocols given in equipment manuals. Key aspects are highlighted:
Set-up Requirements
- Position on flat leveled surface
- Anchor bolts to withstand vibrations
- Electrical connections to control panel
- Pneumatic hookups, air treatment unit
- Coil handling setup, exit conveyors
- Safety fences, light curtains
Operation Methods
- Parameter settings – width, thickness, feeds
- Speed and temperature monitoring
- Registration calibration
- Visual inspection at exits
- Quality checks per specs
- Automated stacking of finished goods
Maintenance Schedule
- Cleaning roll toolingweekly
- Lubricating bearings monthly
- Replacing worn components as needed
- Inspecting chains, belts every 6 months
- Hydraulic system checks
Pros and Cons of Roll Forming Machines
Roll forming provides benefits in rack production but also has limitations depending on context. Comparing the pros and cons allows appropriate selection for different manufacturers.
Advantages
High Productivity
- Output up to 10x higher than alternate methods
- 24/7 operation possible with minimum supervision
- Automated coil handling enhances throughput
Dimensional Accuracy
- Precision tolerance along full length
- Formed angles with ± 0.5° consistency
- Registration suited for secondary processes
Flexibility
- Multiple profiles on same line
- Faster design and changeover of tooling
- Modular expandability for capacity
Lower Operating Costs
- Prefabrication reduces labor, welding
- Lower power consumption than press brakes
- Scrap loss minimized by nesting software
Scalability
- Handle wide range of sizes
- Suit high-mix, low-volume or mass production
- Grow by integrating robotic automation
Safety
- Lower noise compared to fabrication floors
- Light curtains, safeguards for operator protection
- Closed loop monitoring for anomalies
Limitations
High Initial Capital
- Roll sets need profile-specific machining
- Specialized single-purpose machinery
- Payback over years of high utilization
Shape Constraints
- Limited bending radius per pass
- Challenge for closed narrow sections
- 3D forms may need multi-stage machines
Thicker Materials
- Over 2 mm requires large motor capacity
- Maintaining tolerances more difficult
Length Limits
- Support stands needed for long parts
- Issues with thinner foils buckling
Secondary Processing
- Additional steps likely required
- Needs good part handling interface
Process Expertise
- Specialized skill sets needed
- Defect modes not easily detectable
Large Footprint
- Heavy structures occupy extensive space
- Material movement areas also required
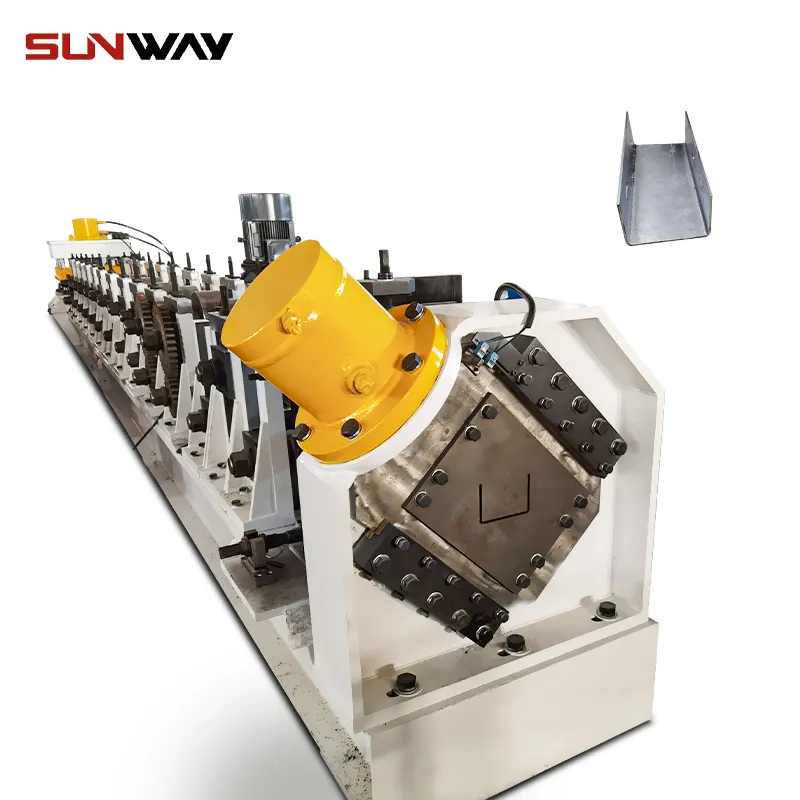
Applications of Roll Formed Rack Profiles
The versatile continuous forming process can create rack product geometries for widespread usage cases:
Warehouse Racking Systems
Adjustable pallet racking, mobile shelving racks and long span racks for distribution centers, warehouses relying on dense storage and material handling optimization.
Retail Store Racks
Retail shelving systems, display racks and check out stands customized for merchandising needs while meeting aesthetic codes.
Library Racks
Specialized racks with reinforced frameworks for books and archive storage with mobile access using rails or wheeled bases.
Industrial Workstations
Custom racks with integrated tables, tool boards, hangars as modular workbenches for assembly operations, quality checks etc.
Data Center Racks
IT server equipment racks designed for mounting networking devices, switches and panels for cord management while allowing heat dissipation.
सामान्य प्रश्न
Q: What sizes of rack components can be roll formed?
A: Common capabilities are 0.5 mm – 2 mm thickness, up to 1200 mm width and 1-12 m lengths. Multi-stand independent 18 m long lines exist for special applications.
Q: What tolerances are possible in roll forming process?
A: Standard tolerance is ± 0.5 mm but precision machines with additional guides and gauges can achieve ± 0.2 mm accuracy along full length.
Q: What degree of automation is possible in material handling?
A: Range of simple exit conveyors to highly automated stacking robots with integrated bundling, palletizing based on volumes and layout constraints.
Q: How often are tooling changes needed for new profiles?
A: For high volume lines dedicated to standard profiles, design life over 5 years. Where mix changes monthly, modular tooling allows faster changeovers.
Q: What secondary processes can be integrated with roll forming?
A: Common inline machines added are – hole punching, notching, tapping, swaging, marking, wrapping, robotic pick-and-place systems.
Q: How to calculate linear meter production rates per day?
A: Multiply machine speed (m/min) x 60 min x runtime (% of 24 hours) x efficiency ratio. Example – 20 m/min x 60 x 0.9 x 0.8 = 8,640 meters per day.
Q: What can be the defects in roll formed rack parts?
A: Twisted profiles, dimensional errors, wrinkles, flare, bow and camber out of standard range, burrs and foreign particle pickup requiring refinishing.
Q: How many bends per pass is common in roll forming machines?
A: Standard roll tooling creates 1-3 incremental bends per rolling station pair. Advanced 3D forming allows upto 6 bends in one pass leading to faster production.
Q: How long do roll forming machine service lifespans tend to be?
A: Approximately 12-15 years on average with proper scheduled maintenance before major overhaul costs occur as outdated systems face challenges.
Q: What factors affect selection between coil lines vs sheet lines?
A: Key considerations are volume, width, material yield, secondary processing needs and associated handling costs specific to production environment.