ए roof tile panel forming machine is an industrial roll forming equipment used to produce shaped roofing sheet metal panels for various structures. These machines create panels through a continuous bending and cutting process applied onto metal strips fed through a series of roll formers. Roof tile panel forming lines enable efficient, high-volume production of standardized sheets as per design requirements.
Overview
Roof tile panel forming machines enable long, customized metal sheets to be reliably mass-produced for roof cladding. They roll metal coils into panels with ribs, flutes or other special profiles using a series of roller dies. These corrugated metal panels interlock to create waterproof, durable roofs ideal for factories, warehouses, garages and homes.
Benefits: Consistent quality, cost efficiency for large volumes, versatile profiles, customized lengths
Drawbacks: High initial capital cost, fixed tooling restricts profile changes
Output: 500-1000 meters of formed metal sheet per hour
Applications: Roofing, wall cladding, architectural facades
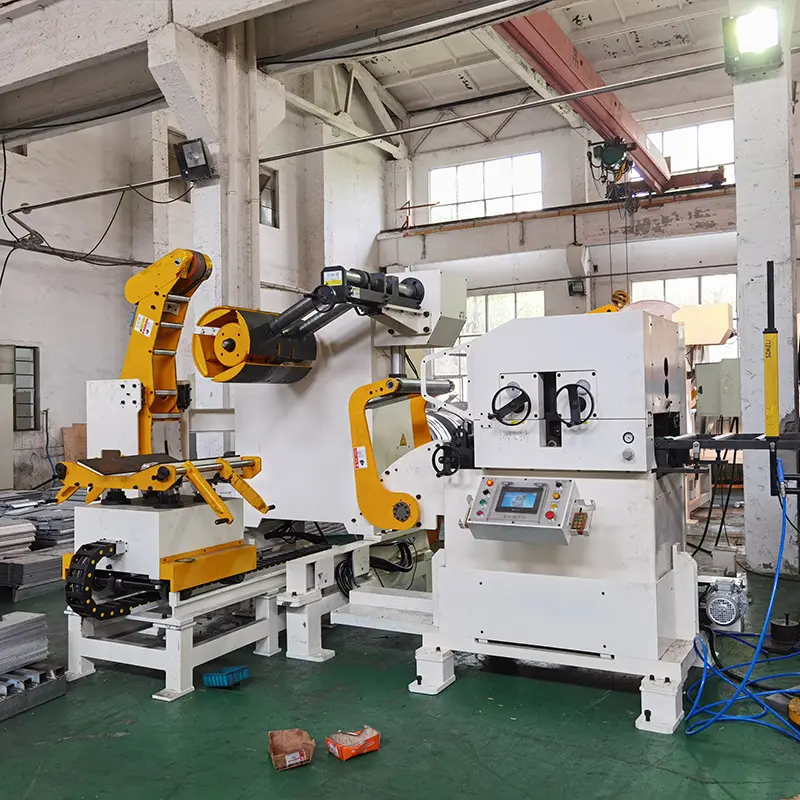
Working Process
Imagine a vast roof stretching across a building, its surface a captivating tapestry of interlocking tiles. But have you ever wondered how these individual tiles, the guardians against the elements, come to be? The answer lies in a remarkable machine – the roof tile panel forming machine, a tireless sculptor that transforms flat sheets of metal into the protective shields adorning our roofs.
The journey begins with a colossal coil of metal, often steel or aluminum, patiently waiting to be unraveled. A hydraulic uncoiler awakens it, unwinding the sheet like a metallic ribbon onto a conveyor. This ribbon then enters the heart of the machine – the forming stations.
Think of these stations as a series of intricately designed molds, each with a distinct purpose. The sheet glides through them, squeezed and shaped by precisely machined rollers. Each roller, with its unique grooves and profiles, imparts a specific bend or fold, gradually transforming the flat sheet into the desired tile profile. Imagine gentle waves forming, or sharp angles emerging, depending on the tile design.
But the process doesn’t stop at mere shaping. The machine can be equipped with additional stations that perform crucial tasks. Punching stations create holes for fastening the tiles, while cutting units slice the formed sheet into individual panels, ready for installation. Some machines even boast embossing stations that add intricate patterns or logos to the tiles, enhancing their aesthetic appeal.
The entire operation is a symphony of coordinated movement. The sheet moves smoothly through the stations, guided by precise feeding and leveling mechanisms that ensure perfect alignment. Hydraulics provide the necessary force to bend the metal without compromising its integrity. And finally, the finished panels emerge, ready to be coated or painted, adding a layer of protection and visual appeal.
The true beauty of the roof tile panel forming machine lies in its versatility. By adjusting the thickness of the sheet, the type of metal used, and the profiles of the rollers, the machine can produce a wide range of tile designs. From classic corrugated profiles to modern standing seam styles, the possibilities are endless. This adaptability makes it a valuable tool for architects and builders, allowing them to choose tiles that perfectly complement their design vision and withstand diverse weather conditions.
Types of Roof Tile Panel Forming Equipment
Type | Description |
---|---|
Standard Machines | Economic option for high volume commodity profiles like trapezoidal, corrugated sheets |
Customized or Specialty Lines | For unique patented or architectural panel designs |
Component/Accessory Machines | Produce small metal parts like flashing, ridges rather than full sheets |
-
रोलिंग शटर स्लेट रोल बनाने की मशीन
-
Highway Guardrail End Terminal Forming Machine
-
Highway U/C Post Roll Forming Machine
-
2 Waves Highway Guardrail Roll Forming Machine
-
3 Waves Highway Guardrail Roll Forming Machine
-
विद्युत कैबिनेट फ्रेम रोल बनाने की मशीन
-
दीन रेल रोल बनाने की मशीन
-
दो लहरें राजमार्ग रेलिंग मशीन
-
तीन लहरें राजमार्ग रेलिंग मशीन
Material, Feeding and Design Considerations
Parameter | Options |
---|---|
Material | Hot-dipped steel, aluminum, zinc alloys, stainless steel, pre-painted coils |
Strip Width | Up to 1250 mm for larger machines |
मोटाई | 0.4mm to 2mm |
Coil Weight | Max 30 MT, powered unwind mandrels |
Feeding | Friction, Accumulator, Servo Motor |
Sheet Length | 0.5m-15m, set by operator/automation |
Profiles | Trapezoidal, sinusoidal, box rib, corrugated, custom |
Tooling | Quick change dies to alter profiles |
Manufacturing and Customization Capabilities
Roof tile forming lines offer:
- Versatile outputs: Different widths, thicknesses, materials
- Profile options: Ribs, flutes and other geometric patterns
- Custom lengths: Set by operator or system automation
- Accessory making: Flashings, trims molded from same strip
- Secondary operations: Cutting, punching holes, edge bending on inline stations
- Surface treatments: Pre-painting, PVDF coatings through tower support
- Embossing and inspection: Logos, codes, prints added; defects detected
- Precision: Tight tolerances maintained on each sheet
These ensure optimal sheets suited for any roofing need.
Suppliers and Pricing
ब्रैंड | Location | Price Range |
---|---|---|
ECC Corp | Taiwan | $150,000 to $800,000 |
FD Machinery | China | $100,000 to $500,000 |
Olympic Machinery | Greece | $250,000 to $1 Million+ |
Metform | Turkey | $180,000 to $900,000 |
Flexospan | South Africa | $120,000 to $600,000 |
Pricing varies by speed, automation features, accuracy grades, sheet dimensions and customization needs.
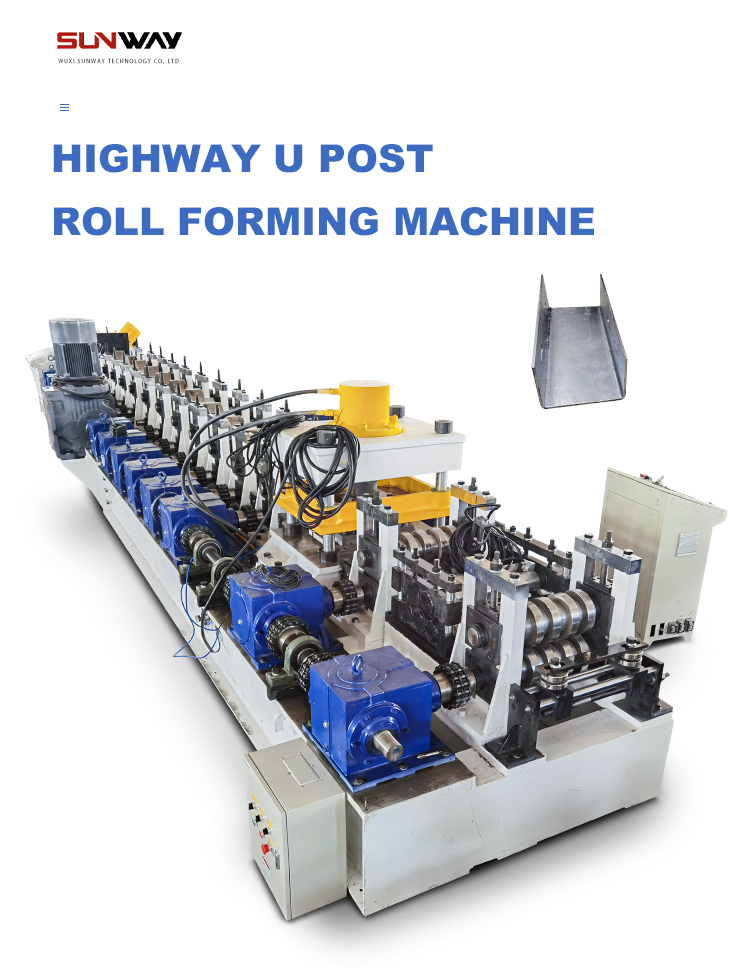
Installation, Operation and Maintenance
Standing tall and proud, a roof tile panel forming machine is more than just a piece of industrial equipment; it’s the key to crafting the protective armor for countless homes and structures. But before this metallic marvel can unleash its tile-shaping prowess, a crucial journey awaits – installation, operation, and meticulous maintenance. Let’s delve into the intricacies of each stage, ensuring your machine operates smoothly and delivers flawless tiles for years to come.
Installation: Laying the Foundation for Success
The installation process is like setting the stage for a symphony. A qualified team first meticulously prepares the foundation, ensuring level ground and proper anchor points for the machine’s weight. Next, comes the careful assembly, guided by the manufacturer’s instructions. From connecting electrical components to aligning rollers and testing hydraulics, each step demands precision and expertise. Once assembled, calibration becomes paramount, fine-tuning the rollers and adjusting settings to achieve the desired tile profile with unwavering accuracy.
Operation: Orchestrating the Metal Symphony
With the machine humming to life, the operator takes center stage. Their role is akin to that of a conductor, overseeing the smooth flow of metal and ensuring consistent quality. Understanding the control panel and its various functions is crucial. From adjusting sheet feeding speed to monitoring hydraulic pressure, each action impacts the final product. Regularly monitoring the machine for potential issues, such as worn rollers or faulty sensors, is equally important. Proactive maintenance prevents downtime and ensures optimal performance.
Maintenance: The Secret to Longevity
Just like any fine instrument, your roof tile panel forming machine requires regular maintenance to preserve its performance and lifespan. This involves a meticulous schedule of cleaning, lubrication, and inspections. Keeping the machine free of debris and metal shavings prevents jams and ensures smooth operation. Lubricating moving parts minimizes friction and wear, while regular inspections allow for early detection and repair of potential issues. Additionally, adhering to the manufacturer’s recommended maintenance schedule, including replacing worn parts, is essential for long-term trouble-free operation.
Stage | Activities |
---|---|
Installation | Civil, electrical, mechanical setup; calibration, trial runs |
Operation | feed coils, set profiles, speed; monitor strip flow; collect panels |
Maintenance | Regular lubrication, inspection, part replacement |
Train staff thoroughly since precision equipment. Employ qualified technicians for setup and repairs.
Choosing the Right Roof Tile Panel Forming Machine Supplier
Parameter | Preferred Criteria |
---|---|
Production Requirements | Speed, profiles, material specs, volumes |
Budget Constraints | Available capital expenditure |
Customization Range | Profile variants required now/future |
Safety Standards | CE, etc. to minimize workplace hazards |
Service Support | Installation, training, maintenance response times |
Brand Reputation | Experience, clientele, case studies |
Get quotes from multiple builders matching needs. Prioritize safety, service support.
Pros, Cons and Limitations
श्रेणी | विवरण |
---|---|
Advantages | Uniform high quality sheets, very high productivity, cost economies at scale, versatile |
Disadvantages | Inflexible once tooling is set, high machine cost |
Limitations | Fixed forming stations restrict profile changes, maximum strip width/gauge capacity constraints |
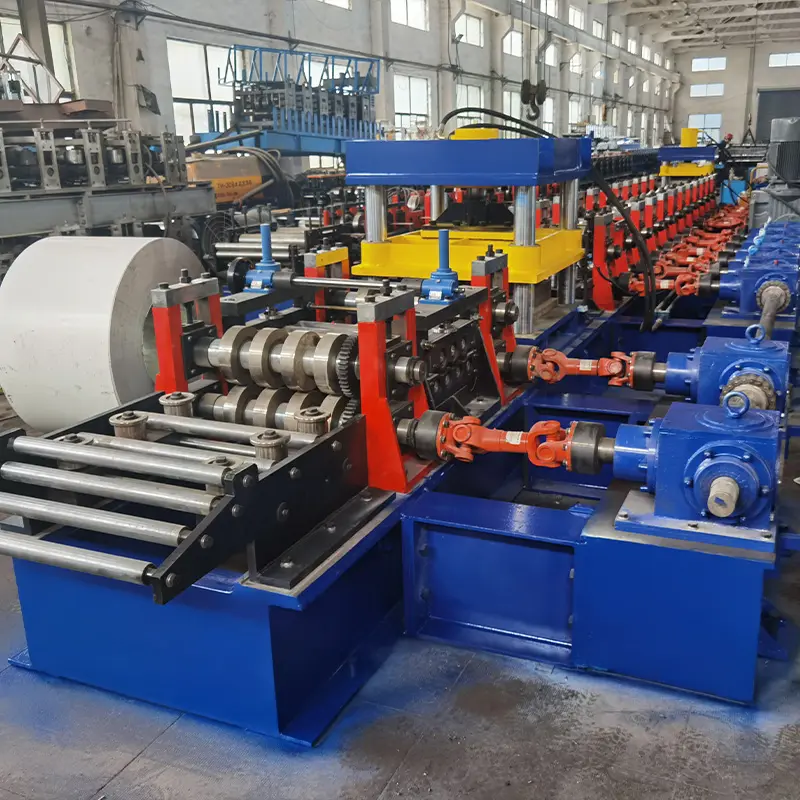
Applications of Roof Tile Panel Forming Machines
Roof tile panel forming machines, with their tireless metal-shaping abilities, are often associated with crafting the protective shields for our homes and buildings. But did you know these versatile machines extend their reach far beyond the realm of traditional roofing? Let’s embark on a journey to explore the diverse applications where their ingenuity shines.
From Homes to Hangars: Shelter in Diverse Forms
While residential roofing remains a key application, these machines cater to a wide range of structures beyond houses. They shape metal panels for industrial warehouses, agricultural sheds, and even aircraft hangars, providing durable and weather-resistant coverings that withstand demanding environments. The ability to customize panel profiles and thickness allows for tailoring solutions to specific needs, ensuring both functionality and aesthetic appeal.
Beyond Metal: Embracing New Materials
The innovation doesn’t stop at shaping metal. Modern machines are increasingly adapting to handle alternative materials like stone-coated steel and even clay, offering a wider range of options for architects and builders seeking unique and sustainable roofing solutions. This versatility expands the machine’s reach, contributing to the construction of eco-friendly structures with a distinctive aesthetic.
Walls Come Alive: Beyond Roofing Applications
The ability to shape metal panels extends beyond roofing applications. These machines can be adapted to create wall cladding for industrial buildings, commercial spaces, and even prefabricated housing units. The panels provide a durable, weather-resistant, and easily customizable alternative to traditional construction methods, accelerating construction timelines and offering design flexibility.
Creative Freedom: Shaping the Future of Design
The ability to create intricate profiles and patterns opens doors to a world of creative possibilities. These machines are now used to produce metal panels with unique finishes and textures, catering to the growing demand for architecturally distinct structures. From mimicking the look of traditional materials like wood or stone to creating contemporary geometric patterns, the possibilities are endless, pushing the boundaries of design and aesthetics.
FAQs
Q: What is the delivery time for roof tile panel forming lines?
A: Delivery takes 8-16 weeks including manufacturing, shipping and installation. Customized machines may take longer.
Q: Can I get a trial or sample sheet before purchasing the machine?
A: Yes, reputed suppliers provide sample profile sheets from the forming machine to approve before procurement.
Q: How often is maintenance required for these machines?
A: General lubrication and inspection every few months. Major overhauls needed annually handled by mechanic teams.
Q: What is the estimated lifespan of a roof tile panel forming equipment?
A: Approximately 15-20 years with proper maintenance and part replacements as needed.
Q: Can I automate the sheet cutting and stacking process for unmanned running?
A: Yes, automated cut-to-length lines and robotic stacking arms can be integrated to minimize manual intervention.