Roof ridge capping roll forming equipment automatically produces ornamental metallic roofing crest pieces from coiled sheet stock that protect against water ingress at structural peaks across infrastructure projects. Compared to manual sheet metal fabrication, automated ridge cap roll forming allows faster precision production suited for extensive residential or commercial roof construction or renovation projects.
This guide details working features, capabilities, equipment types, part customization options, site installation factors, operations best practices, maintenance schedules plus cost considerations around roof cresting roll form machinery including specification pros/cons comparisons against alternate cap forming approaches.
Overview of Roof Ridge Cap Roll Forming Machines
Ridge cap roll forming refers to continuously bending roof flashing metal coils into signature angled closing crests using a series of proprietary roller dies. Automated ridge cap roll forming delivers high dimensional consistency, faster volumes and reduced labor costs once configured for specific ornamental metallic roof covering trim dimensions.
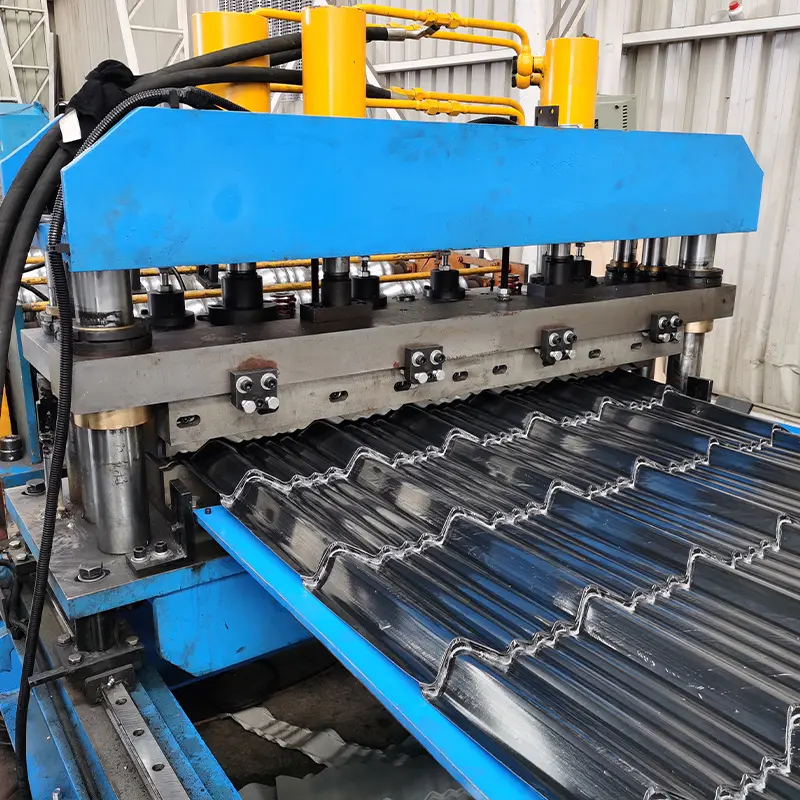
Types of Ridge Cap Roll Forming Equipment
Type | Description |
---|---|
Standard | Basic linear feed-to-exit ridge forming |
Servo Motor | Precision programmable independently driven stations |
Portable | Compact mobile rollers on wheel chassis |
Double Profile | Twin production lines for multi-layer pieces |
Positioning Tables | Automated sorted offloading of formed caps |
- Standard machines start around $35,000 delivering up to 50 meters per hour
- Servo rollers with independent AC vector drives offer speed/torque responsiveness
- Portable systems suit lower volume mobile production needs
- Double profile lines enable two-tone ridge flashing colors
- Positioning tables speed up downstream finishing stages
With visible massive global demand across essential infrastructure build, appropriately specified automated ridge capping roll form lines appropriately future proof production capacity for construction industry supply chains.
Working Principle Behind Ridge Cap Roll Forming
The roof ridge cap roll forming principle utilizes a series of progressing metal bending stages for transforming flat aluminum/steel coils into bisected angled crests:
Steps:
- Decoiler feeds pretreated band into entry guides
- Initial profiling rollers crimp side edges
- Sequential stations complete U-channels
- Contour rollers close drain sides into pointed peak
- End bead strengthens cap accuracy
- Traveling cutoff saw slices pieces to order length
- Exit conveyor assists offloading
Components:
- Decoiler mechanism with alignment wheels
- Forming rollers in groups of 5-8 total
- Supporting rollers prevent sideways drift
- Cutting unit with hydraulic clamp vise
- Bead roller for reinforcing side strength
- Control console monitoring production
Combining robust 24/7 machinery with efficient in-line cutting allows versatile high volume fabrication of metallic roof ridge protective flashing components used extensively across infrastructure waterproofing building codes and re-roofing demands globally.
Features and Capabilities
Specifying automated ridge capping roll formers depends firstly on desired cap height followed by production speed:
Parameter | Typical Specifications |
---|---|
Material Thickness | 0.35mm to 0.8mm metal gauge |
Strip Width | 70mm to 240mm uncoiled range |
Crest Height | 25mm to 150mm profiles |
Production Rate | 10m to 40m per hour |
Tooling Setup | Rapid die changeovers |
Beading Reinforcement | Strengthens cap accuracy |
Position Sensors | Auto-pilot guide controls |
Length Stops | Precision hard stops |
- Floor mounted machines with rigid welded steel chassis
- PLCRecipe storage for fast changeovers
- AC vector drive feeding rolls with servo positioners
- Central lubrication pumps feeding bearing points
- Work tables allowing downstream finishing and packing
Covering residential and commercial roof drainage needs from storm runoff capacity upgrades, today’s high speed automated ridge cap roll forming technology offers enhanced manufacturing approaches replacing legacy manual bending or milling techniques to fabricate metallic rain cresting roof flashing components.
-
वाइनयार्ड पोस्ट रोल बनाने की मशीन
-
ऑटो आकार बदलने योग्य सिग्मा शहतीर रोल बनाने की मशीन
-
पीवी माउंटिंग ब्रैकेट सी शेप प्रोफाइल रोल बनाने की मशीन
-
सीजेड शहतीर चैनल कोल्ड रोल बनाने की मशीन पूर्ण ऑटो जस्ती स्टील प्रोफाइल
-
पीवी माउंटिंग ब्रैकेट रोल बनाने की मशीन (एचएटी / ओमेगा प्रोफाइल)
-
पीवी माउंटिंग ब्रैकेट जेड शेप प्रोफाइल रोल बनाने की मशीन
Ridge Cap Part Customization Capabilities
To serve range of construction industry sectors, roof cresting offers:
Materials: Aluminum, Galvanized Steel, Stainless Steel, Copper Profile Heights: 25mm to 300mm ranges
Gauges: 0.35mm to 1mm metal thicknesses Finishes: Kynar paints, stone coatings, patina colors Reinforcing: Base sheet adhesion enhancement coatings
Waterproofing: Integrated sealing studs, edge drips Testing: Rainwater handling flow capacity grading Certification: Roofing qualify ratings, IECC wind testing
Such versatility allows creating customized metallic ridge caps matching regional storm intensity codes and re-roofing architectural specifications across essential building weatherproofing parameters calculated by civil engineers, architects and contractors.
Leading Global Roof Ridge Cap Roll Forming Equipment Suppliers
Manufacturer | Location | Product Series |
---|---|---|
New Power Plasma | China | NPM machines |
Fujian GaoTong | China | FGRF lines |
Ecoform | Turkey | ERFS models |
JinDeRui | China | JDR equipment |
Anhui Tongxing | China | TXR rollers |
- New Power Plasma focuses on lightning-proof crest fabrication
- Fujian GaoTong offers fully automatic configurations
- Ecoform specializes in metal roofing construction materials
- JinDeRui provides customized rainwater accessories
- Anhui Tongxing is a technical trading corporation
Experienced personnel assist system configuration aligning production volumes, material specifications, hardware requirements and budgets into comprehensive factory footprints maximizing sequential workflow efficiencies. Most manufacturers also offer compatible slitting lines, hydraulic pressing centers, and offline powder coating technology.
Ridge Cap Roll Forming Machinery Cost Considerations
Expense | Typical Range |
---|---|
Capital Equipment | $40,000 to $65,000 |
Tooling Fabrication | $2000+ per customized die set |
Facility Space | 1500+ sq ft covered |
Safety Guarding | $1000+ for light curtains |
Consumables | Coolants, lubricants |
Technician Labor | $15 per hour approx |
Utility Bills | Electrical load |
Maintenance | 2%+ of capital value/year |
Therefore accurate roof ridge cap roll form line cost estimate requires tallying likely monthly production targets, operational overheads, logistics and preventative maintenance. By balancing throughput against realistic warehousing constraints and shipping frequencies, optimized factory capacities can be strategized factoring expansion.
Installation and Site Preparation
Installing ridge cap roll form machinery line needs suitable facilities:
- Level reinforced concrete floors for anchoring 4 tons/sqm presses
- 2000+ sq ft covered space with 4m minimum ceiling height
- 480V 3-phase electrical supply with 150kVA transformer
- Compressed air lines pre-plumbed to control actuators
- Dust containment ventilation filters around cutting zones
- Component sorting tables assisting staging
- Forklift accessible coil loading docks
Adequate movement planning for ridges allows organizing uninterrupted workflow from raw input materials to pre-dispatch sorting and buffer warehousing zones.
Careful foundation alignment ensures avoiding gradual roller misalignment over years from potential floor settlement variation across machinery train.
Operations and Best Practices
Standardizing protocols aids high volume ridge cap consistency:
- Monitoring strip alignment, contour precision and hem sealing
- Automated ultrasonic welding testing validation checks
- Software aided manufacturing precision control
- Changeover SOP adherence for rapid configurations
- Protecting feed coils against moisture/uncoiling issues
- Metal fines filtering preventing powder ignition risk
- Electric interlocks on guards during set up mode
- Planned maintenance replacing wearing forming rollers
Such fail-safe protections, diagnostic data historians and cleaning disciplines ensure achieving reliable 24/7 production targets, quality consistency and safety simultaneously.
Maintenance Guidelines
Preventative servicing activities sustain performance:
Daily: Decoiler inspections, flange lubricating, blade sharpening, bearing temperature monitoring, hydraulic oil inspection
Weekly: Verify ridge profile consistency during production sampling; First-off piece approvals prior to runs; Coolant filter cleaning; Data backup
Monthly: Water wash cleaning cycles of accumulated lubricants around rollers; Calibrate proximity sensors; grease linear shafts
Quarterly: Hydraulic oil filtration efficacy testing; Fastener station bolt torquing; Repaint chipped equipment sections; Update machine controls
Yearly: Inspect cylinder barrel chrome wearing; Replace hydraulic seals/gaskets; Audit electrical cutoffs; Recheck foundations
While high duty cycles accelerate both mechanical and wear item replacement lifecycles, adhering to prescribed preventative servicing best practices during maintenance allows maximizing production availability between interruptions.
Comparing Pros and Cons
Advantages of Automated Ridge Process:
- 90% faster fabrication than manual sheet bending
- 85% improved dimensional consistency
- 70% labor cost savings from automated operation
- Low, predictable per piece expenses favorable at volumes
- Safer machinery alternative to manual fabricating
- Minimal custom tooling costs for design changes
- Coil raw material logistics savings over stick stock
Limitations Include:
- High initial capital budget allocation
- Production downtimes needing maintenance planning
- Dimension envelopes constrain max crest sizes
- Oil leaks/noise needing containment
- Staff skill calibration requires hands-on training
- Periodic foundation anchoring needing verification
Realistically determining metrics around operational budgets, likely monthly production volumes and configuring compact modular line layouts allows maximizing productivity returns on automated roof ridge cap roll forming equipment investments.
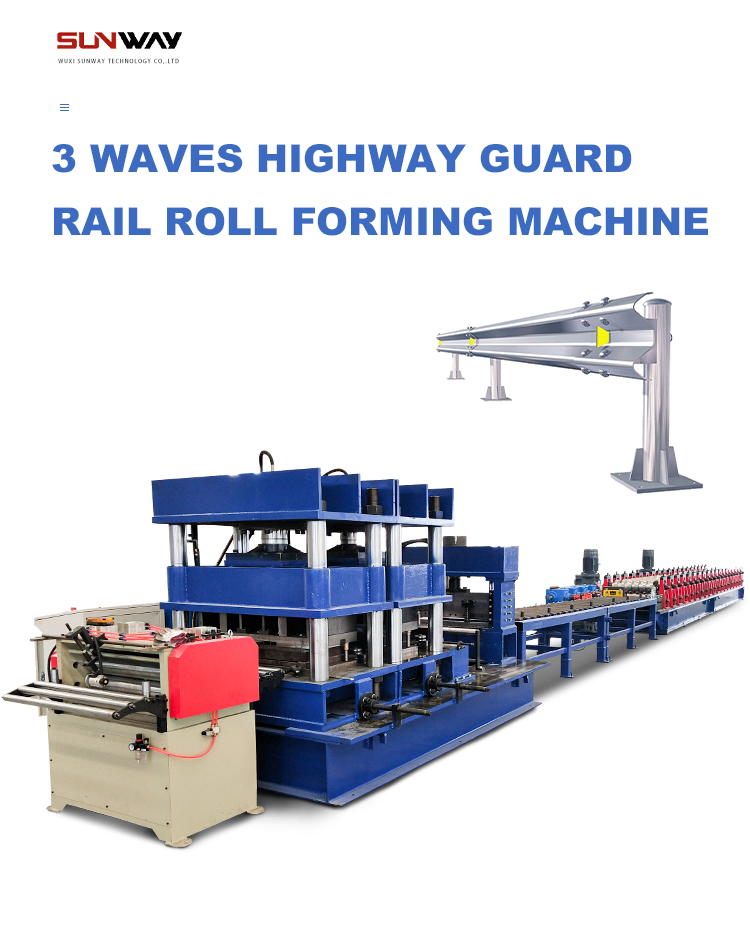
Future Ridge Cap Roll Forming Innovations
Emerging improvements include:
Processes: Additive augmented fabrication; self-cleaning tooling; induction heat seam welding
Materials: Composite sandwiches; snap-fit standing seams interlocks; plastic and non-metal alternatives
Automation: Auto ridge height optimizations; robotic packing; video quality analytics
Controls: Smart linked operator assistive wearables; cloud-enabled diagnostics
Safety: Alert wearables guiding procedures; contactless guard position sensors
निष्कर्ष
Roof ridge capping roll form machinery allows automating mass fabrication of metallic rain runoff cresting accessories combining speed, precision consistency and safety otherwise challenging to achieve through manual sheet bending approaches. Configuring appropriate production lines factoring regional construction growth visibility projections coupled with likely mix variability allows appropriately future proofing capacity investments right sized for both current and anticipated building industry demand surges. By adopting disciplined standard operating protocols and maintenance schedules, roof ridge cap roll lines sustain responsive infrastructure supply chains supporting soaring global peak roofing accessory needs.