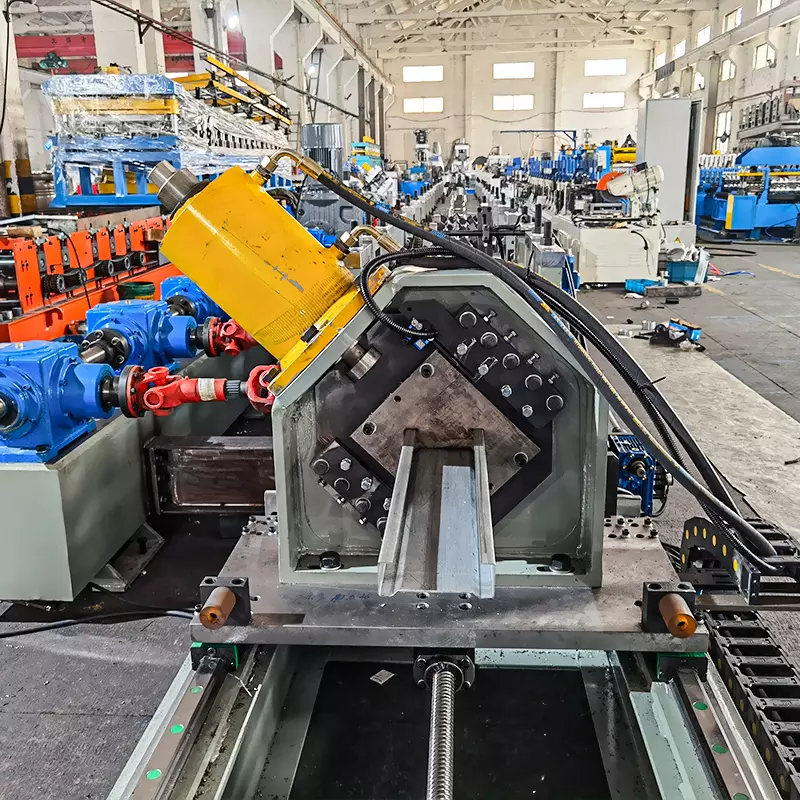
Introduction to Roll Forming
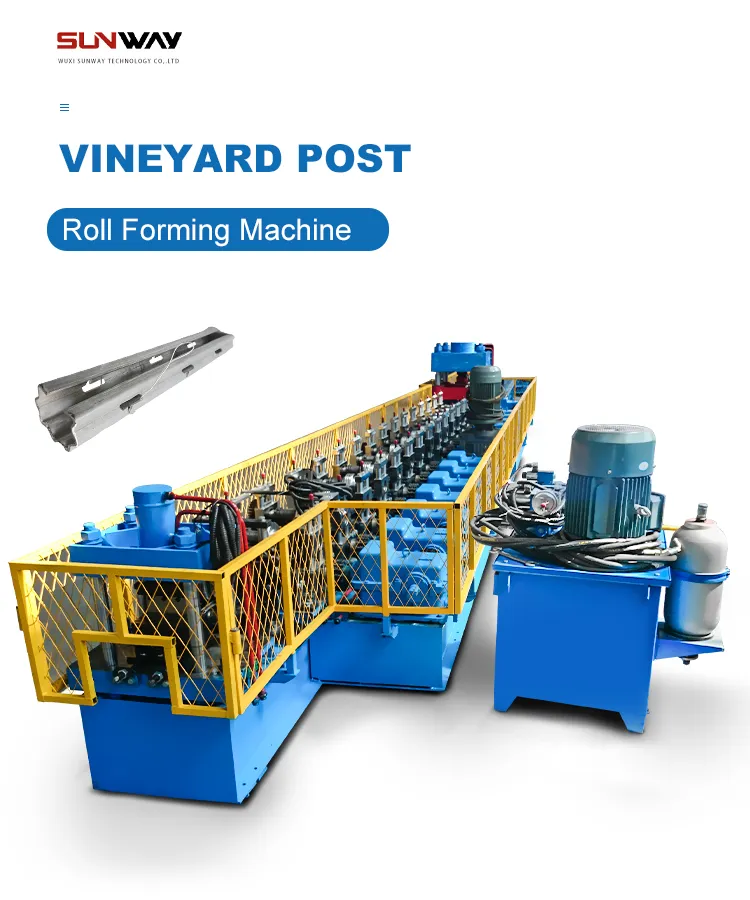
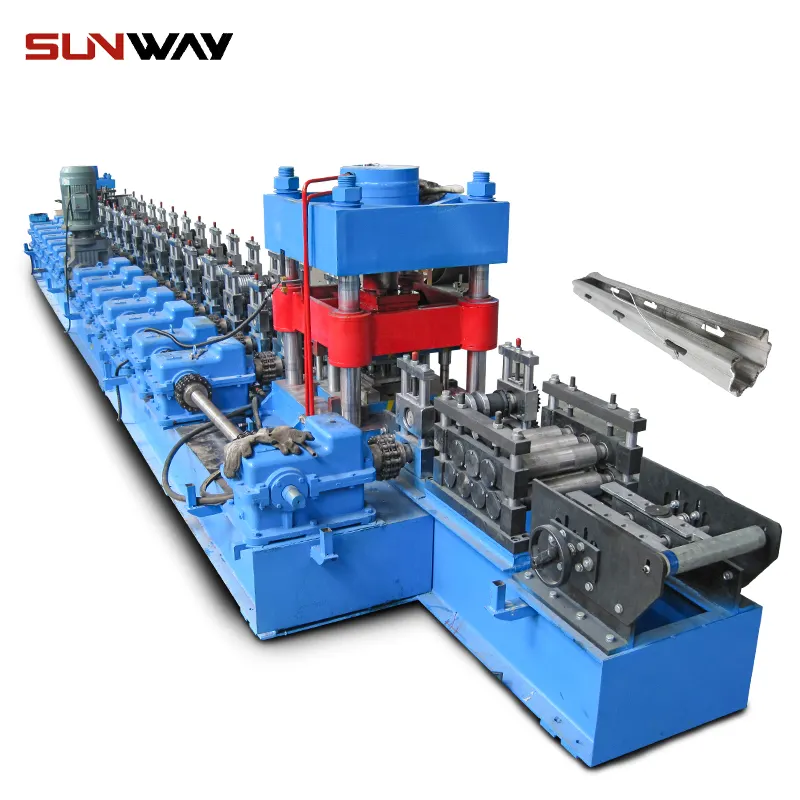
Roll forming is a manufacturing process that involves shaping metal into a specific profile or shape. The process begins with a long strip of metal, which is fed into a series of rollers in a roll forming machine. As the metal passes through the rollers, it is gradually formed into the desired shape or profile.
The basic components of a roll forming machine include the entry section, the forming section, the cut-off section, and the exit section. In the entry section, the metal strip is fed into the machine, where it is guided through a series of rollers to ensure a consistent width and thickness. In the forming section, the metal strip is gradually shaped into the desired profile as it passes through a series of rollers that apply pressure and bend the metal.
Once the metal has been formed into the desired shape, it moves to the cut-off section, where it is cut to the appropriate length. Finally, the formed and cut metal piece moves to the exit section, where it is collected and packaged for shipping or further processing.
The rollers in a roll forming machine are custom designed to produce a specific shape or profile. The rollers work in pairs, with the top roller applying pressure to the metal strip while the bottom roller supports it. The shape of the rollers determines the final shape of the metal profile.
Overall, roll forming is a highly versatile manufacturing process that can produce a wide range of metal shapes and profiles. By using precision tools and processes, roll forming machines can produce parts with consistent quality and accuracy, making them a valuable investment for businesses in a range of industries.
रोल बनाने की मशीन के प्रकार
-
विद्युत कैबिनेट फ्रेम रोल बनाने की मशीन
-
दीन रेल रोल बनाने की मशीन
-
केबल सीढ़ी रोल बनाने की मशीन
-
पीवी माउंटिंग ब्रैकेट सी शेप प्रोफाइल रोल बनाने की मशीन
-
केबल ट्रे रोल बनाने की मशीन
-
पीवी माउंटिंग ब्रैकेट रोल बनाने की मशीन (एचएटी / ओमेगा प्रोफाइल)
-
पीवी माउंटिंग ब्रैकेट जेड शेप प्रोफाइल रोल बनाने की मशीन
-
सौर बढ़ते अकड़ चैनल रोल बनाने की मशीन
-
स्ट्रट चैनल रोल बनाने की मशीन
रोल बनाने की मशीनें come in various types, each designed to meet specific production needs. Here are the main types of roll forming machines:
Single-Level Roll Forming Machines: As the name suggests, single-level roll forming machines have a single level of tooling and can produce one profile at a time. These machines are ideal for producing simple shapes or low-volume production runs.
Duplex Roll Forming Machines: Duplex machines have two levels of tooling and can produce two profiles simultaneously. This feature makes them more efficient than single-level machines, but they are still limited in terms of the number of profiles they can produce.
Triplex Roll Forming Machines: Triplex machines have three levels of tooling and can produce three profiles simultaneously. These machines are more efficient than duplex machines and can produce a wider range of profiles.
Multi-Level Roll Forming Machines: Multi-level machines have four or more levels of tooling and can produce multiple profiles simultaneously. These machines are highly efficient and versatile, making them suitable for high-volume production runs and complex profiles.
The main difference between these types of roll forming machines is the number of levels of tooling they have and the number of profiles they can produce at once. Single-level machines are the simplest and least expensive, but they are limited in terms of their capabilities. Duplex, triplex, and multi-level machines are more expensive but can produce more profiles simultaneously, which increases efficiency and reduces production time.
When choosing a roll forming machine, it’s important to consider the type of material being formed, the complexity of the part, and the desired output volume. The type of machine that is best for your business will depend on these factors, as well as your budget and production needs.
Roll Forming Machine Components
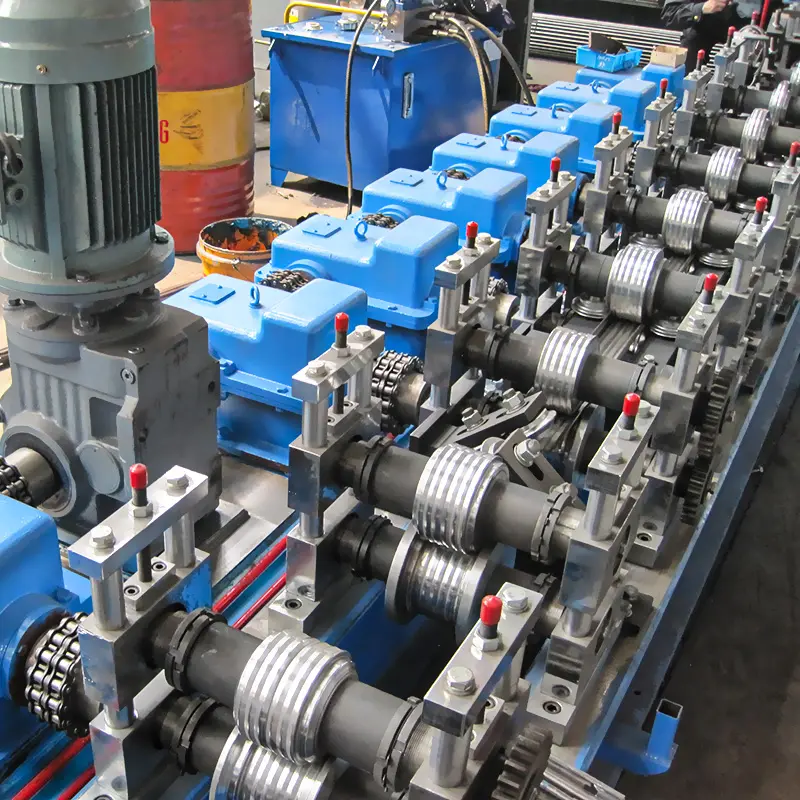

The four main components of a roll forming machine are the entry section, the forming section, the cut-off section, and the exit section. Here’s an overview of each section and how they work together to form parts:
Entry Section: The entry section is where the metal strip is fed into the roll forming machine. The metal strip is guided through a series of rollers to ensure a consistent width and thickness. The entry section also includes an uncoiler to feed the metal strip into the machine and a leveler to straighten the strip.
Forming Section: The forming section is where the metal strip is gradually shaped into the desired profile as it passes through a series of rollers. Each set of rollers in the forming section applies pressure and bends the metal in a specific way to form the profile. The shape and position of each roller are critical to producing the desired shape accurately.
Cut-Off Section: Once the metal has been formed into the desired shape, it moves to the cut-off section, where it is cut to the appropriate length. The cut-off section can include a shear, saw, or other cutting tool to cut the metal strip.
Exit Section: The exit section is where the formed and cut metal piece moves out of the machine and is collected. The exit section may include a conveyor belt or other handling equipment to move the finished part to the packaging or assembly area.
All of these sections work together to form parts by using precision tools and processes. The metal strip is gradually formed into the desired shape as it passes through the forming section, with each set of rollers contributing to the final shape. The cut-off section ensures that the parts are cut to the appropriate length, and the exit section collects the finished parts for packaging or further processing.
Applications of Roll Forming Machines
Roll forming machines have a wide range of applications across various industries. Here are some examples of specific parts that are commonly produced using roll forming machines in the automotive industry, construction industry, and HVAC industry:
Automotive Industry: Roll forming machines are commonly used in the automotive industry to produce parts such as bumpers, roof rails, door beams, and chassis components. These parts are typically made from high-strength steel and require precision forming to meet strict safety standards.
Construction Industry: Roll forming machines are used in the construction industry to produce parts such as metal roof and wall panels, steel framing, and gutter systems. These parts are often made from galvanized steel or aluminum and require precise forming to ensure they fit together properly and provide a weather-resistant barrier.
HVAC Industry: Roll forming machines are used in the HVAC industry to produce parts such as ductwork, vents, and air conditioning unit components. These parts are typically made from galvanized or stainless steel and require precise forming to ensure they meet strict airflow and efficiency standards.
In each industry, roll forming machines are valued for their ability to produce parts with consistent quality and accuracy. By using precision tools and processes, roll forming machines can produce parts that meet or exceed industry standards, making them a valuable investment for businesses in these industries.
In addition to these industries, roll forming machines are also used in a range of other applications, including the production of furniture, lighting fixtures, and various consumer goods. Overall, the versatility of roll forming machines makes them a valuable investment for any business looking to improve its manufacturing capabilities and produce high-quality parts efficiently.
In conclusion, roll forming machines come in various types and have numerous applications across industries, including automotive, construction, and HVAC. With their ability to produce parts with consistent quality and accuracy, roll forming machines are highly valued for their efficiency and versatility. By understanding the different types of roll forming machines and their respective capabilities, businesses can make informed decisions when selecting the right machine for their needs. With the right machine in place, businesses can improve their manufacturing capabilities and produce high-quality parts that meet or exceed industry standards.