Ridge cap tile roll forming machines continuously produce roofing ridge caps, hip caps, and edge flashing from metal coils. This guide provides detailed information on ridge cap roll former types, workings, specifications, applications, selection, operation, maintenance, and comparisons.
Introduction to Ridge Cap Tile Roll Forming Machines
Ridge cap roll forming machines cold form metal coils into curved ridge cap tile profiles used for roofing. Key features:
- High production speeds up to 25 meters/minute
- Capability to produce different ridge cap sizes and designs
- Quick and easy size changeover
- Compact and flexible setup
- Consistent quality and close tolerances
- Low operational costs
Roll formed ridge caps offer benefits over manual fabrication for high volume roofing production.
Types of Ridge Cap Tile Roll Forming Machines
Major Types of Ridge Cap Roll Formers
- Motorized Ridge Cap Roll Former
- Manual Ridge Cap Tile Roll Former
- Automatic Cutting Ridge Cap Roll Former
- Double Layer Ridge Cap Roll Former
- Semi-Automatic Ridge Cap Roll Former
- Custom Ridge Cap Roll Former
Dedicated automatic machines produce high volumes. Manual and semi-auto ridge cap roll formers provide flexibility for smaller batches.
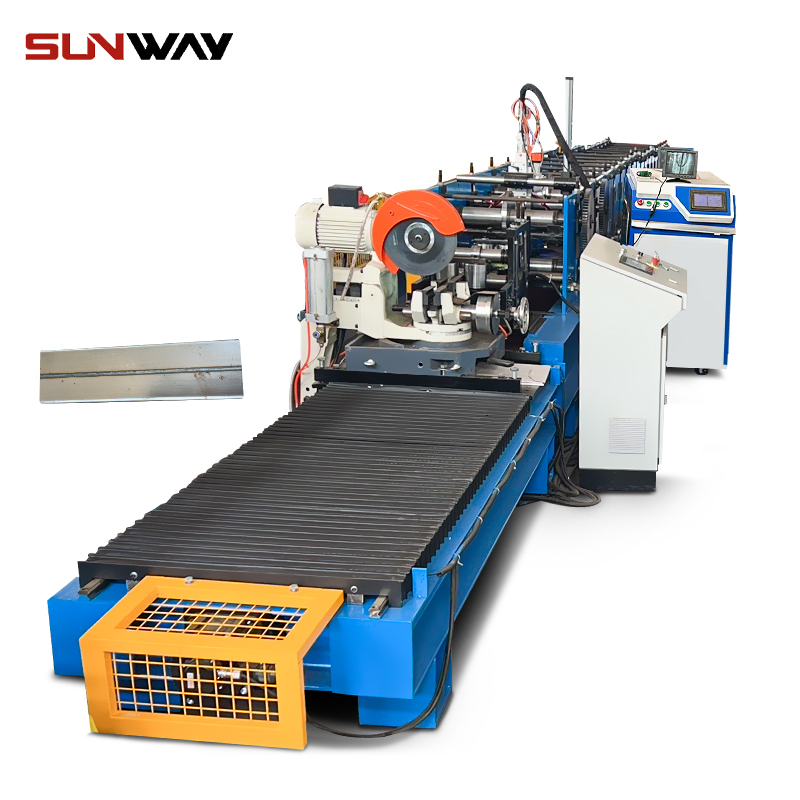
Working Principle of Ridge Cap Tile Roll Forming Machines
Ridge Cap Roll Forming Process Steps:
- Coil feeding into the roll former
- Sheet passed through progressive roller stations
- Formed into curved ridge cap profile gradually
- Cutting to required length by built-in shear
- Formed ridge caps discharged for collection
It continuously forms metal coil into finished roofing ridge caps.
Key Specifications of Ridge Cap Roll Formers
Technical Specifications:
- Production Speed: 10 – 25 meters/minute
- Forming Width: 300 – 750 mm
- Material Thickness: 0.3 – 1 mm
- Main Drive Power: 1.5 – 4 kW
- Voltage: 220 – 440 V, 3 phase
- Machine Length: 4000 – 8000 mm
- Machine Weight: 800 – 2500 kg
- Number of Stations: 8 – 16
Specifications depend on required output, material type, and product dimensions.
Design and Components
Machine Design:
- Robust welded steel frame construction
- Coil holding uncoiler and feeder section
- Initial sheet guidance system
- Roller stations for bending into ridge profile
- Hydraulic shearing system
- Formed tile discharge system
- Electrical controls with automation
Main Components:
- Coil loading and feeding unit
- Roll forming stations with guides
- Cutting unit with shear
- Outfeeding tables for finished tiles
- PLC based controller
- Safety guarding system
Sturdy construction and quality components ensure reliable high-speed production.
Working Principle
Sequence of Ridge Cap Roll Forming:
- Coil loaded and fed into the machine
- Sheet pre-bent and passed through successive stations
- Formed into curved ridge cap profile gradually
- Hydraulic shear cuts tiles to length
- Formed ridge caps slide down outfeed tables
- Touchscreen HMI automates production
- Sensors monitor operation and stop machine on faults
The cold forming action transforms flat metal coil into curved ridge tiles.
Raw Material Suitability
Suitable Coil Material:
- Hot rolled steel
- Cold rolled galvanized steel
- Stainless steel
- Aluminum
Key Material Parameters:
- Thickness – 0.3 to 1 mm
- Width – 800 to 1250 mm
- Tensile Strength – 250 to 550 MPa
- Coil Weight – Up to 5 tons
Properly specified coil material avoids cracking or warping issues.
Customization Options
Customization of Ridge Cap Roll Lines:
- Profile dimensions and tolerances
- Interlocking designs and patterns
- Quick changeover between sizes
- Hole punching and notching
- Special coatings like zinc, colors, prints
- Touchscreen HMI and data logging
- Safety guarding and lighting
Modular components enable reconfiguration for different profiles, metals and features.
Applications and End Products
Typical Uses of Roll Formed Ridge Caps:
- Metal roofing for commercial buildings
- Roofing for sheds, lean-tos, and canopies
- Capping rake walls and gable ends
- Covering vent pipes, chimneys, and skylights
- Edge flashing along slopes
- Decorative false chimneys
- Covering beam ends in open ceilings
Roll formed ridge caps provide curved profiles that interlock for waterproof and attractive roofing.
Leading Ridge Cap Roll Forming Machine Manufacturers
Notable Ridge Cap Roll Former Brands:
- Union Tool (Taiwan)
- Shandong Shengjia (China)
- Ruian Jinxing (China)
- Metform (Turkey)
- Hangzhou Roll Forming (China)
- Botou Xianfa (China)
- Dahua Machinery (China)
- Jouanel Industrie (France)
These established brands offer proven and robust ridge cap roll forming machines combining high speed, changeover flexibility, and ease of operation.
Cost Analysis and Pricing Information
Ridge Cap Roll Former Price Range:
- Basic manual machine – $3,000 to $5,000
- Automatic line – $15,000 to $40,000
- Large double layer line – above $60,000
Pricing depends on production speed, automation level, and width capacity. Installation, training and support add to costs.
How to Select a Suitable Ridge Cap Roll Former
Key Selection Criteria:
- Production speed and daily output targets
- Metal thickness and coil width capacity
- Level of automation required
- Variety of profiles and sizes to be run
- Available installation space and layout
- Power supply requirements and availability
- Budget constraints and ROI goals
- Reputation and experience of machinery supplier
- Availability of local service and support
The production targets and space constraints must align with the roll former specifications for smooth functioning.
Pros and Cons of Ridge Cap Roll Forming Machines
Advantages of Ridge Cap Roll Formers
- High production speeds and volumes
- Consistent and uniform product quality
- Lower scrap rates compared to fabrication
- Flexibility to quickly changeover profiles
- Compact footprint requiring less factory space
- Lower labor costs due to automation
- Safer enclosed roll forming process
Limitations of Ridge Cap Roll Formers
- High initial capital expenditure
- Require pre-treatment and flattening of coils
- Skilled personnel needed for operation
- Significant downtime for major size changeovers
- Limited to standard ridge cap shapes
- Risk of stoppage if cutting fails
- Noisy process requiring sound enclosures
When high volume ridge cap production is needed, the fast output rate and consistency merits investment in roll forming.
Comparison of Roll Forming With Alternatives
Roll Forming vs Other Ridge Cap Production Methods
Factor | रोल बनाना | Manual Fabrication |
---|---|---|
Setup time | Medium | Very High |
Running costs | Low | High |
Labor requirements | Low | High |
Production rate | High | Low |
Product consistency | Excellent | Poor |
Shape complexity | Medium | High |
Tooling cost | Medium | Minimal |
For rapid production of uniform ridge caps, roll forming is vastly superior on productivity, consistency and costs compared to manual metal fabrication techniques.
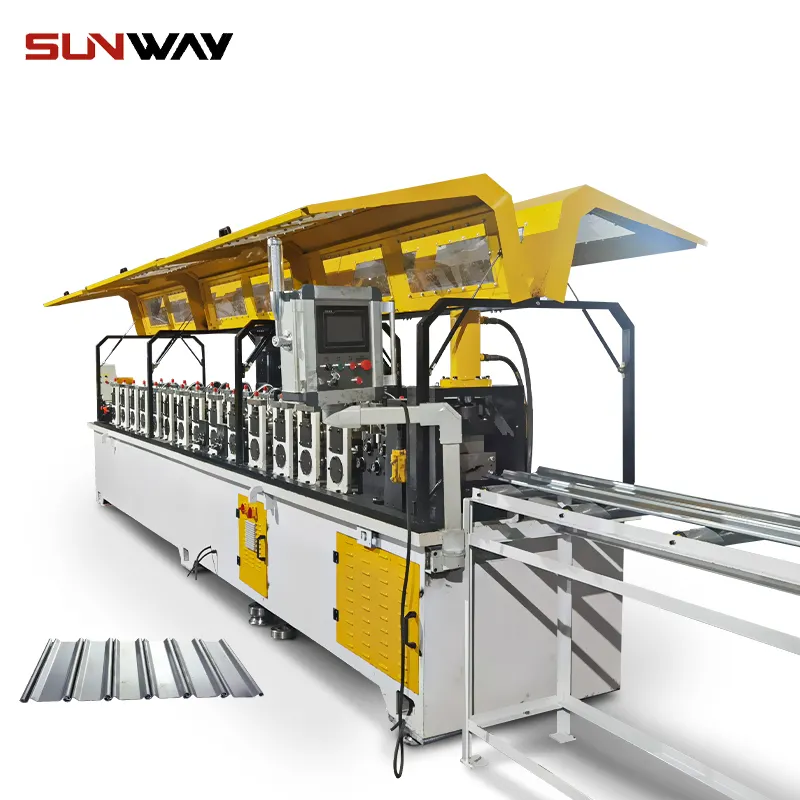
Frequently Asked Questions
Q: What sheet metal thickness is used for ridge caps?
A: Standard metal thickness from 0.3 to 1 mm is used. Thicker coils require more powerful roll formers.
Q: What type of steel is optimal for ridge caps?
A: Hot dip galvanized steel and AZ/Zincalume coated steel offer good corrosion resistance for roofing applications.
Q: What maintenance is required for ridge cap roll formers?
A: Mainly cleaning, lubrication, inspection for component wear, and replacement of damaged rollers, cutting blades, etc. as needed.
Q: What are common defects in roll formed ridge caps?
A: Twisted profiles, flange distortions, thickness variations, waviness, end flaring, deformation, and poor interlock are potential issues.
Q: How long does it take to changeover to a new profile size?
A: On quick changeover machines, size changeover can be accomplished in under 15 minutes in most cases.
Q: What safety precautions are mandatory for these machines?
A: Proper guarding, emergency stops, maintenance during downtime only, and operation by trained personnel wearing protective gear.