Width corrugated sheet roll forming machines are an essential tool in modern manufacturing, used to produce corrugated sheets of different widths, lengths, and thicknesses for a wide range of applications. These machines use a unique manufacturing process that involves feeding the material through a series of rollers and dies to form the desired corrugated shape. Understanding the process of width corrugated sheet roll forming machines is crucial for businesses looking to improve their production efficiency and profitability. In this post, we will discuss the roll forming process, the different types of corrugated sheets, the factors that affect the process, the advantages of using width corrugated sheet roll forming machines, and the safety considerations businesses need to take into account when using these machines. By understanding the process of width corrugated sheet roll forming machines, businesses can optimize their manufacturing operations and produce high-quality corrugated sheets that meet their specific needs and requirements.
Types of corrugated sheets that can be produced using width corrugated sheet roll forming machines
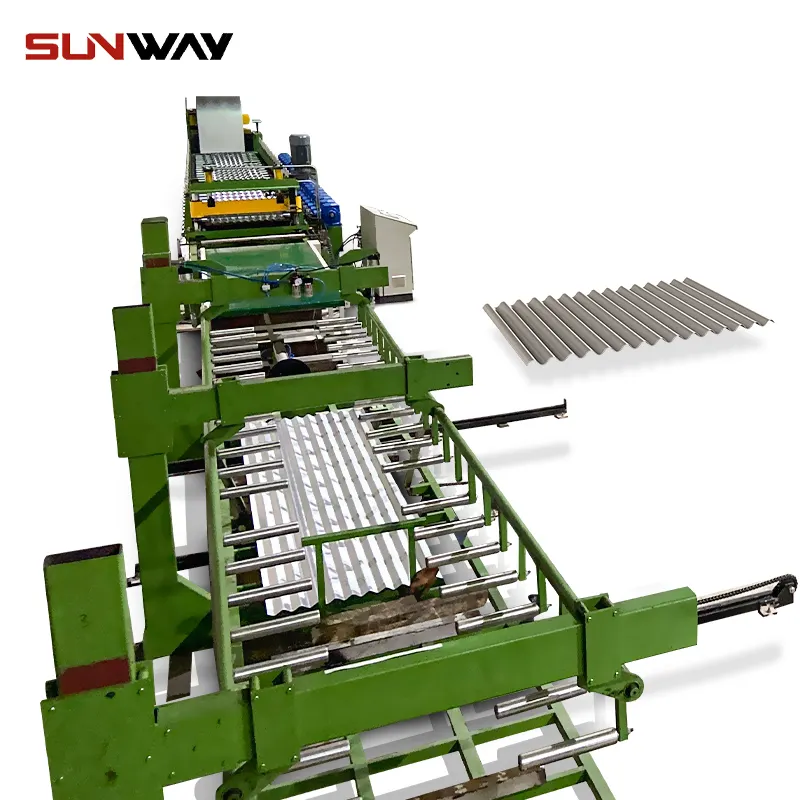
Width corrugated sheet roll forming machines can produce different types of corrugated sheets with various profiles and shapes. Here are some common types of corrugated sheets that can be produced using these machines:
- Sinusoidal profile: This is the most common type of corrugated sheet and is characterized by its curved shape. Sinusoidal profile sheets are commonly used in roofing and cladding applications, as well as in the automotive industry for body panels.
- Trapezoidal profile: Trapezoidal profile sheets have a straighter profile than sinusoidal profile sheets, with parallel sides and flat tops. These sheets are commonly used in roofing and cladding applications and are popular in the construction industry due to their excellent load-bearing capacity.
- Box profile: Box profile sheets have a similar profile to trapezoidal profile sheets but with a flatter base and a more pronounced crown. These sheets are often used in roofing and cladding applications and can be used in buildings with low roof pitches.
- Tile profile: Tile profile sheets have a profile that resembles traditional roof tiles. These sheets are commonly used in roofing applications and are popular in residential and commercial buildings due to their aesthetic appeal.
The type of corrugated sheet produced by a width corrugated sheet roll forming machine depends on the roller and die design used. The shape and profile of the corrugated sheet can be customized according to the specific needs and requirements of the customer. By producing different types of corrugated sheets, businesses can offer a variety of solutions to different industries and applications, improving their competitiveness in the market.
The roll forming process of width corrugated sheet roll forming machines
The roll forming process used in width corrugated sheet roll forming machines involves feeding a flat metal sheet through a series of rollers and dies to gradually shape it into a corrugated profile. Here’s a breakdown of the different stages of the process:
- Entry section: The process begins with the entry section, where the flat metal sheet is fed into the machine. The sheet is usually fed using a motorized or hydraulic decoiler, which unwinds the sheet and feeds it into the machine.
- Forming section: Once the sheet enters the machine, it passes through a series of rollers and dies that gradually shape it into the desired corrugated profile. The rollers and dies are designed to bend and shape the metal sheet as it moves through the machine. As the sheet progresses through the forming section, it takes on the desired corrugated shape.
- Cutoff section: Once the sheet has been fully formed, it passes through the cutoff section, where it is cut to the desired length. The cutoff section is usually equipped with a flying cutoff or a stationary cutoff, depending on the specific machine design.
Throughout the process, the rollers and dies are carefully calibrated to ensure the material is shaped accurately and consistently. The rollers and dies can be adjusted to produce different profiles and shapes, depending on the specific needs of the application.
In addition to the rollers and dies, other machine components, such as the entry and exit guides, the gearbox, and the electric motor, work together to ensure a smooth and efficient operation.
Factors that affect the process of width corrugated sheet roll forming machines
Several factors can affect the width corrugated sheet roll forming machine process, and it’s essential to consider these factors to ensure a smooth and efficient manufacturing process. Here are some of the key factors that can impact the process:
- Material properties: The properties of the material being used can significantly affect the roll forming process. Factors such as the material’s thickness, strength, ductility, and hardness can impact the final product’s quality. If the material is too thick or hard, it can put a strain on the rollers and dies, leading to increased wear and tear and potentially affecting the machine’s overall performance. Therefore, it’s essential to choose the right material for the specific application and ensure it meets the required quality standards.
- Roller and die design: The design of the rollers and dies can impact the final product’s quality, as well as the machine’s overall performance. Factors such as the roller diameter, the number of forming stations, and the material used to make the rollers and dies can all affect the process. A well-designed roller and die set can ensure a consistent and accurate shaping process, producing high-quality corrugated sheets.
- Machine settings: The machine settings, such as the forming speed, the tension level, and the pressure settings, can also impact the process. Adjusting these settings can help optimize the manufacturing process and ensure that the corrugated sheets are produced to the desired specifications.
By considering these factors, businesses can optimize their width corrugated sheet roll forming machine process and improve the final product’s quality. Adjusting the machine settings, using the right material, and ensuring a well-designed roller and die set can all contribute to an efficient and high-quality manufacturing process. It’s essential to regularly monitor the process and make necessary adjustments to ensure consistent performance and optimal results.
Advantages of width corrugated sheet roll forming machines
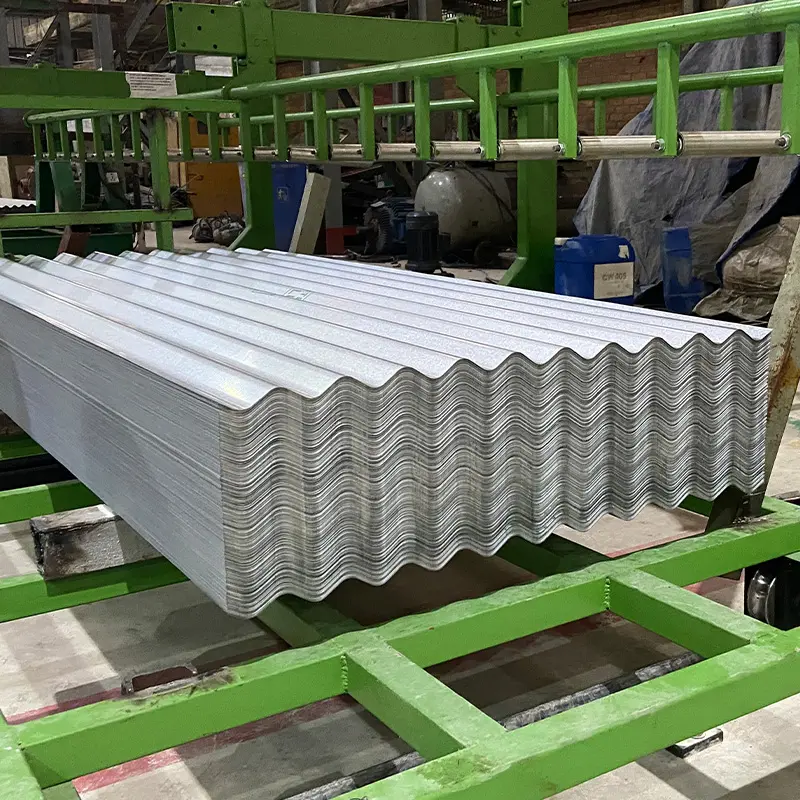
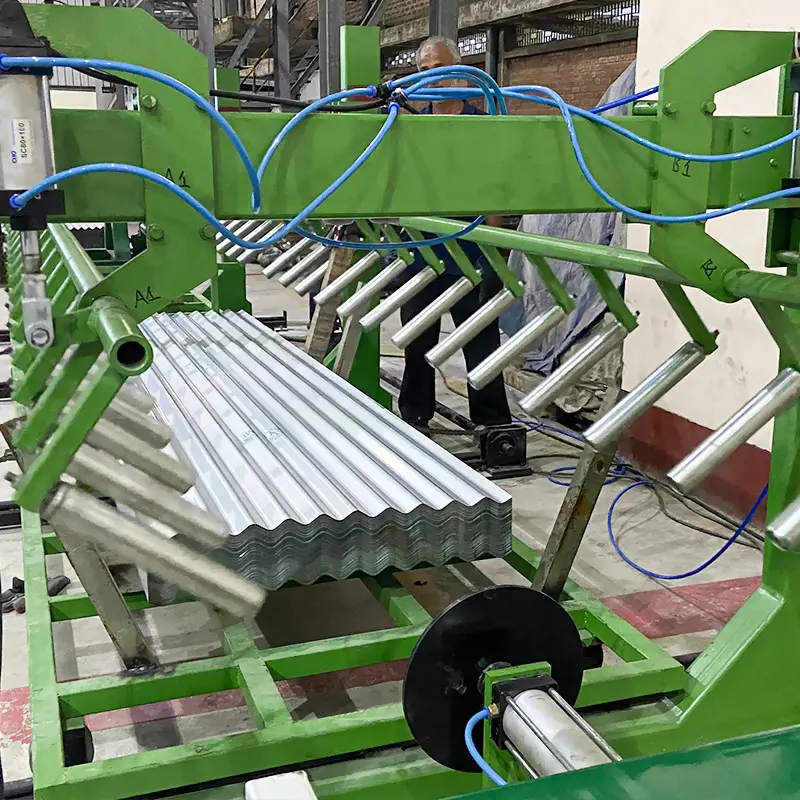

There are several advantages to using width corrugated sheet roll forming machines in manufacturing. Here are some of the key benefits:
- High production speed: Width corrugated sheet roll forming machines can produce corrugated sheets at a high speed, making them an efficient option for businesses that need to produce large quantities of corrugated sheets. This can help businesses increase their overall production efficiency and output.
- Precision and accuracy: These machines can produce corrugated sheets with high precision and accuracy, ensuring that each sheet is of the same high quality. This helps to maintain the integrity of the final product and improve customer satisfaction.
- Customization and flexibility: Width corrugated sheet roll forming machines can be customized to produce corrugated sheets of different widths, lengths, and thicknesses, with customizable profiles and shapes. This flexibility allows businesses to meet the specific needs and requirements of their customers, improving their competitiveness in the market.
- Cost-effectiveness: Roll forming is a cost-effective manufacturing process that can produce high-quality corrugated sheets at a lower cost than other manufacturing methods. The high production speed and accuracy of these machines can also reduce labor costs and improve production efficiency, leading to increased profitability.
By using width corrugated sheet roll forming machines, businesses can improve their production efficiency and profitability while also delivering high-quality products to their customers. The advantages of these machines can help businesses stay competitive in the market, meet customer demand, and grow their business.
In summary, width corrugated sheet roll forming machines are a crucial tool in modern manufacturing, used to produce corrugated sheets of different widths, lengths, and thicknesses for a wide range of applications. Understanding the roll forming process, the different types of corrugated sheets, the factors that affect the process, and the advantages of using width corrugated sheet roll forming machines can help businesses optimize their manufacturing operations and produce high-quality corrugated sheets that meet their specific needs and requirements. By choosing the right machine and adjusting the process to optimize production efficiency and quality, businesses can improve their profitability, competitiveness, and customer satisfaction.