pallet rack roll forming machine systems enable efficient, continuous production of storage rack structural components used extensively in warehouses and industrial facilities. This article covers working principles, capabilities, suppliers, comparisons, and more.
परिचय of pallet rack roll forming machine
Roll formed pallet racks utilize sequential roller dies to cold form metal coils into long structural members comprising the vertical columns, horizontal beams, braces etc. They provide an optimal balance of storage density, selectivity, and operational efficiency.
Benefits:
- High strength-to-weight designs
- Faster installation compared to stick-built methods
- Lower transportation cost
- Minimal production waste
- Consistent quality and dimensional accuracy
- Applicable for manual, automated storage/retrieval
This guide covers key aspects from specification and procurement to installation and utilization of roll formed selective pallet racks.
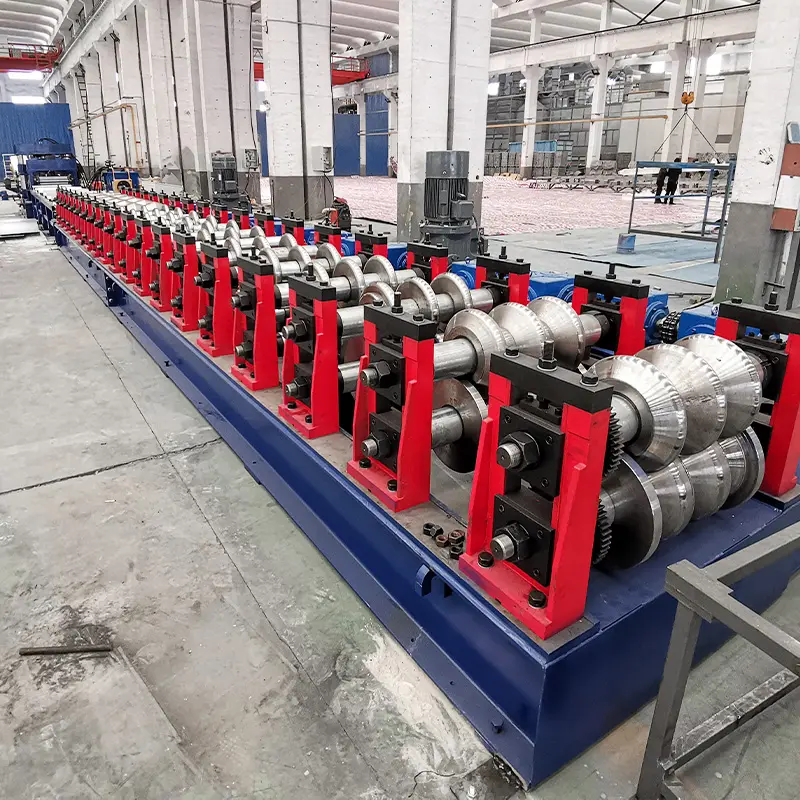
Working Principle of pallet rack roll forming machine
A typical heavy-duty roll forming production line involves:
1. Stock Feeding
Metal coils are loaded on a precise de-coiler feeder with an initial sheet guidance section. Galvanized steel is commonly used.
2. Roll Forming
The strip engages a series of roller dies mounted in a mill duty housing frame. Each die induces a series of small bends which gradually form the custom pallet rack profiles. Common components include columns, beams, braces, accessories.
3. Support and Guiding
Additional supporting and guiding rollers stabilize the precut blank as it progresses through the sequential stands finally achieving the completed cross-section profile.
4. Cutoff and Collection
Formed sections are automatically sheared to specified lengths, typically ranging from 3 ft to 12 ft. Conveyors collect and stack the finished parts for bundling and shipment.
Design Aspects:
- Number of dies and forming stations
- Vertical intermesh clearances
- Horizontal adjustment ranges
- Frame rigidity and stability
- Precision servo feeds
3D modelling optimizes these parameters for each new pallet rack component profile ensuring quality output.
Key Capabilities
Advanced pallet rack roll formers provide:
1. Components Produced
- Pallet rack columns – Uprights supporting horizontal beams
- Rack beams with connectors– Horizontal decks
- Diagonal and horizontal row spacers
- Reinforcing frames, sway braces
- Ancillary accessories, supports
2. Material Compatibility
- Hot-dip galvanized low carbon steel
- High strength steels up to 1000 MPa grade
- Prepainted, powder coated aesthetic finish options
- Stainless steel grades available
3. Size Ranges
- Column heights up to 40 ft produced continuously
- Lengths up to 65 ft feasible
- Thickness range from 1.0 mm to ~3 mm
- Formed widths adjustable per profile
4. Secondary Processing
- Hole punching for connectors and accessories
- Slotting, louvre patterns for visibility
- Chili toppings for structural engagement
- Embossing and corner detailing
- Sheared cut to length pieces per design
5. Key Quality and Output Rates
पैरामीटर | Typical Values |
---|---|
Forming speed | 16 – 23 m/min |
Punching/slotting speed | 18 – 25 strokes/min |
Shearing speed | 15 – 20 cuts/min |
Positioning accuracy | ± 0.5 mm |
Contour tolerance | ± 1.0 mm |
Higher precision achievable with appropriate upgrades.
Typical Pallet Racking Systems
Roll formed components cater to a wide range of storage requirements:
- Low rise shelving – up to 15 ft
- Medium rise – 20 to 30 ft
- High rise – Beyond 35 ft
- Narrow aisle adjustable racks
- Double deep storage structures
- Pushback cart systems
- AS/RS automation compatible
- Drive-in/drive-through adjustable lanes
Global Equipment Suppliers
कंपनी | Location | Models |
---|---|---|
FONNTAI | China | RFQ Series |
UNICO | Taiwan | IBR Series |
FORMETCO | Turkey | Max. 3mm thickness |
ILABLE | Spain | UL Certified |
Tips on Choosing Vendors:
- Get proposals from multiple suppliers
- Prioritize trust and responsiveness
- Ensure demonstrated pallet rack experience
- Request referrals and case studies
- Clearly specify key requirements
Involve suppliers early for optimal equipment design and delivery.
-
विद्युत कैबिनेट फ्रेम रोल बनाने की मशीन
-
दीन रेल रोल बनाने की मशीन
-
केबल सीढ़ी रोल बनाने की मशीन
-
पीवी माउंटिंग ब्रैकेट सी शेप प्रोफाइल रोल बनाने की मशीन
-
केबल ट्रे रोल बनाने की मशीन
-
पीवी माउंटिंग ब्रैकेट रोल बनाने की मशीन (एचएटी / ओमेगा प्रोफाइल)
-
पीवी माउंटिंग ब्रैकेट जेड शेप प्रोफाइल रोल बनाने की मशीन
-
सौर बढ़ते अकड़ चैनल रोल बनाने की मशीन
-
स्ट्रट चैनल रोल बनाने की मशीन
Pricing Estimates
Machine Price Range:
- $150,000 to $350,000
- Profile complexity impacts price tags
- Automation and secondary processing increase price
- Precision requirements affect price
Operating Cost Considerations:
- Material coil cost dominates
- Utility bills for power consumption
- Maintenance and consumables
- Labor, facility overheads
Opportunities to Reduce Costs:
- Standardize on profile designs
- Qualify local fabricators if feasible
- Compare upgrades vs. new machine
- Negotiate bulk purchase discounts
- Explore financing options
Carefully balance functionality, efficiency, and price for an optimal value equipment.
Installation & Operation
Best Practices for Installation
- Carefully site and anchor the heavy equipment
- Precision alignments and level checking
- Ensure clearances to coil payoff
- Confirm guides settings
- Test initial sample production thoroughly
Tips for Productive Operation
- Certified electricians handle wiring
- Monitor strip tension and guides wear
- Watch for coil defects during unspooling
- Utilize recommended mists and lubricants
- Inspect critical formed lengths
Preventive Maintenance
- Periodically resurface forming rollers
- Check bearing seals, hydraulics, electrics
- Tighten any loosened bolts
- Backup automation data and parameters
Proactive preventive maintenance minimizes unplanned outages.
Selecting the Right Roll Former
Key Selection Considerations
Parameter | Evaluation Aspects |
---|---|
Product Quality | Case studies, test certifications |
Reliability | MTBF history, safety features |
Lead Time | Order to delivery, after-sales support |
अनुकूलन | Flexibility to match specifications |
Value | Pricing relative to features offered |
Develop specific requirements and assess proposals weighing both technical and commercial aspects before finalizing equipment selection.
Roll Forming Pros & Cons
Advantages
- Continuous, efficient production
- High quality consistent parts
- Applicable for high strength steels
- Lower operational skill needs
Limitations
- Initial roll tooling setup time
- Can induce some residual stresses
- Thickness and width changes require roll change
For majority of pallet rack designs with production volume exceeding 250,000 linear feet per year, roll forming offers clear productivity and economic advantages over other fabrication approaches.
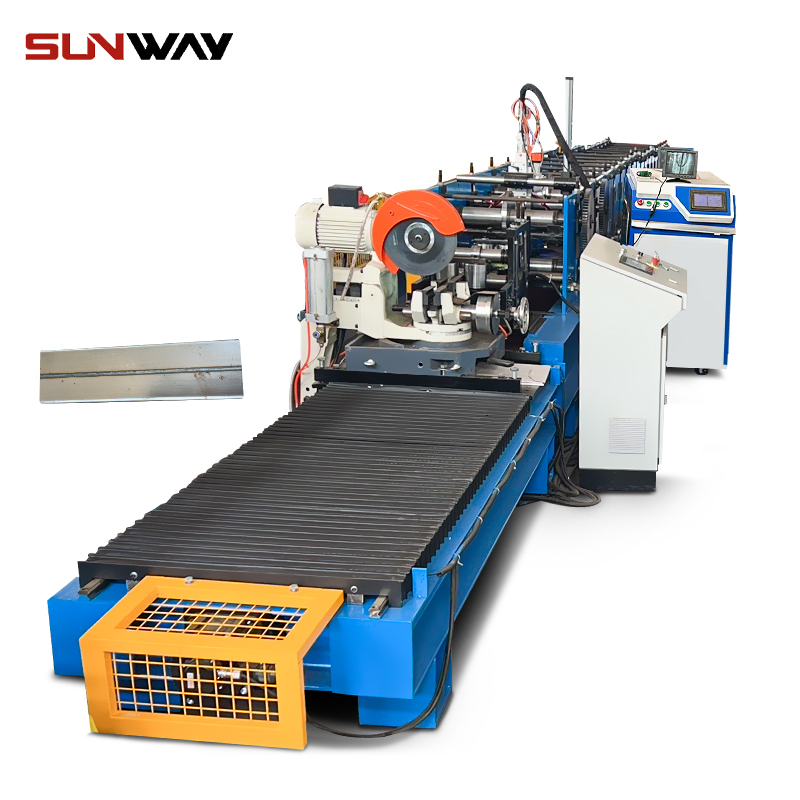
FAQs
Q: What information is required during design phase?
A: Complete 2D CAD and preferably 3D models with key dimensions defined for each pallet rack component are needed for equipment engineering.
Q: Can racking systems for cold storage be produced?
A: Yes, specialized grades with insulation layers or stainless-steel finishes suitable for cold and freezer environments can be formed.
Q: What automation options are typically available?
A: Servo feed upgrades, production data monitoring, automated stacking and order sorting conveyors etc. minimize manual handling needs.
Q: What testing is performed on roll formed racks?
A: Rigorous load testing per ANSI MH16.1 guidelines evaluating strength, durability, impacts, vibrations, and other structural parameters ensures storage system integrity.