oem gutter roll forming machine systems enable efficient production of long continuous eavestrough sections used extensively for roof drainage management in buildings. This article provides detailed technical guidance on oem gutter roll forming machine working, selection, installation, comparisons, and more.
परिचय of oem gutter roll forming machine
Gutter roll formers utilize a series of roller dies to gradually shape metal coil feedstock into various rain gutter profile geometries. Precision in-line punching and cutting stations provide finished ready-to-install components.
Benefits
- High production rates with low waste
- Dimensional consistency and quality control
- Applicable for various metals like steel, aluminium
- Versatile size adjustments
- Lower operational skill requirement
- Just-in-time inventory production
This guide covers key technical parameters for optimal gutter roll former selection, operation, and maintenance.
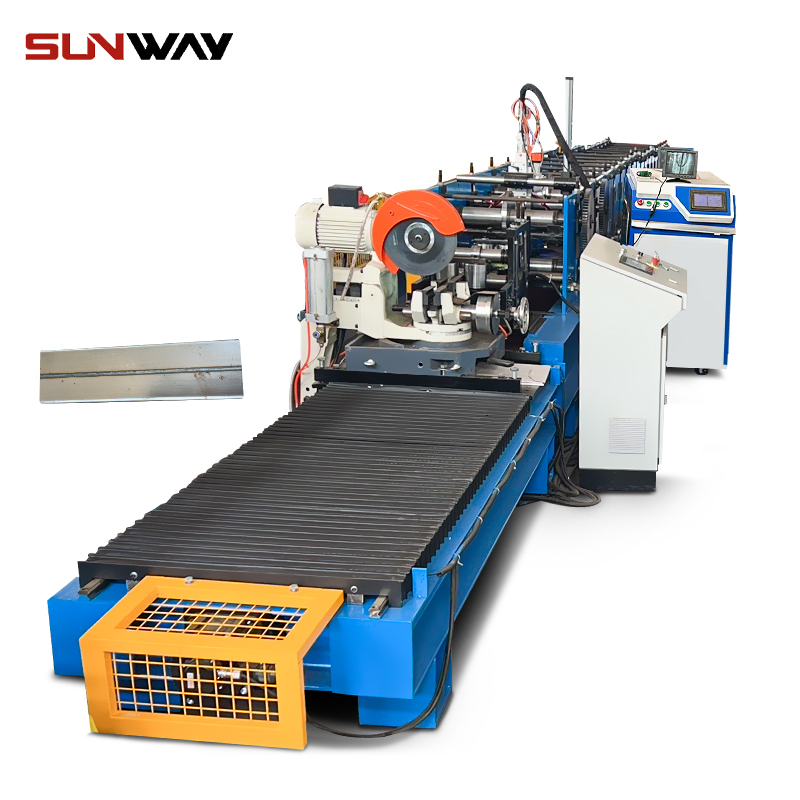
Working Principle
The working steps involve:
1. Metal Coil Loading
Prefab metal coils of materials like galvanized steel, zinc alloy coated steel, or aluminium alloys are loaded on a precision programmable de-coiler.
2. Size Reducing
An initial roller stand accurately sizes the strip width while maintaining tension. This feeds into the pre-cutter module.
3. Roll Forming
The metal strip engages precisely engineered top and bottom roller dies mounted sequentially. Each stand incrementally forms the strip into the desired rain gutter profile – half round, K style, box etc. Modern 3D modelling optimizes the number of stands and die geometries.
4. Punching and Cutoff
In-line punching stations create the required slot patterns for brackets attachment. A final shear then cuts the continuously formed gutters to specified lengths as per order requirements.
5. Stacked Output
Formed and sheared eavestrough pieces are automatically stacked on powered out-feed tables for packaging and transport.
Key Capabilities of oem gutter roll forming machine
1. Profile Options
- Half round gutters – Most common
- ‘K’ style with flat bottom
- Square box styles
- Custom profiles to match applications
2. Size Capacity
- Formed widths from 150 mm to 300 mm in incremental steps
- Strip coil thickness from 0.4 mm to 1.2 mm
- Adjustable length pieces up to 7 meters
- Larger sizes may need custom designs
3. Materials Suitability
- Hot-dip galvanized steel with zinc coating
- Pre-finished painted steel for aesthetics
- Aluminium alloy grades 5xxx, 6xxx
4. Added Features
- In-line punching for brackets
- Mitering attachments for corners
- Scroll bending for decorative ends
- Logo embossing capability
5. Key Quality & Rates
Parameter | Values |
---|---|
Maximum Forming Speed | 40 meters per minute |
Punching Speed | 25 cycles per minute |
Length Tolerance | ± 3.0 mm |
Contour Accuracy | ± 1.0 mm |
Typical Applications
- Residential roof drainage systems
- Low slope commercial roofs
- Rainwater harvesting lines
- Agricultural and greenhouse structures
And many more! Engage OEMs to customize for special application requirements.
-
वाइनयार्ड पोस्ट रोल बनाने की मशीन
-
ऑटो आकार बदलने योग्य सिग्मा शहतीर रोल बनाने की मशीन
-
पीवी माउंटिंग ब्रैकेट सी शेप प्रोफाइल रोल बनाने की मशीन
-
सीजेड शहतीर चैनल कोल्ड रोल बनाने की मशीन पूर्ण ऑटो जस्ती स्टील प्रोफाइल
-
स्टील का तार लंबाई लाइन मशीन में कटौती
-
स्टील का तार लंबाई लाइन मशीन में कटौती
-
स्टील का तार लंबाई लाइन मशीन में कटौती
-
पीवी माउंटिंग ब्रैकेट रोल बनाने की मशीन (एचएटी / ओमेगा प्रोफाइल)
-
पीवी माउंटिंग ब्रैकेट जेड शेप प्रोफाइल रोल बनाने की मशीन
Global Supplier Snapshot
Manufacturer | Location | Production Rates |
---|---|---|
FONNTAI | China | Up to 35 mpm |
UNICO | Taiwan | Up to 25 mpm |
ILDEX | Turkey | Up to 20 mpm |
BEHRANG | Iran | Up to 15 mpm |
Involve suppliers early in design development to customize equipment for specific production needs.
Pricing Estimates
Machine Investment
- $65,000 to $180,000
- Profile complexity impacts prices
- Secondary processing capabilities add cost
- Precision requirements affect price
- Level of automation influences price
Operating Costs
- Material coils dominate recurring spend
- Electricity and utilities
- Maintenance spares and labor
Cost Saving Opportunities
- Standardize few profile configurations
- Employ local fabricators where possible
- Carefully evaluate upgrade vs. new buy
- Compare lease vs. buy analysis
- Study total cost of ownership
Balancing production volume, quality, cost and delivery times is key.
Installation & Operation
Best Practices for Installation
- Carefully site and level equipment
- Check engagement and alignment of tooling
- Confirm coil loading and feeding path
- Test initial production thoroughly
- Inspect critical formed lengths and punching
Tips for Productive Operation
- Monitor line speed, strip tension
- Watch for coil defects during payout
- Use proper mists, lubricants on forming dies
- Ensure stacker smoothness
- Conduct preventive maintenance during breaks
Reliability Focus
- Inspect rollers and guides wear
- Check hydraulics, electrics, pneumatics
- Monitor overall rigidity and vibration
- Backup automation data and parameters
Well planned maintenance improves uptime.
Selecting Equipment
Key Selection Parameters
Parameter | Evaluation Aspects |
---|---|
Product Quality | Case studies, testimonials |
Technical Expertise | Proven gutter profile experience |
अनुकूलन | Flexibility to match specifications |
Responsiveness | Quote turnaround, after-sales support |
Reliability | ISO certifications, safety features |
Value Added | Commissioning support, Training services |
Get detailed proposals from multiple vendors on cost, quality and lead time considerations before ordering equipment.
-
Multi Profiles Roll Forming Machine
-
कैरिज बोर्ड रोल बनाने की मशीन
-
Auto Changeable C Z Purline Machine
-
Standing Seam Roof Panel Curving Machine
-
Semi Auto Size Changeable CZ Purlin Roll Forming Machine
-
Laser Welding Square Pipe Roll Forming Machine
-
बैरल नालीदार रोल बनाने की मशीन
-
रोलिंग शटर स्लेट रोल बनाने की मशीन
-
Highway Guardrail End Terminal Forming Machine
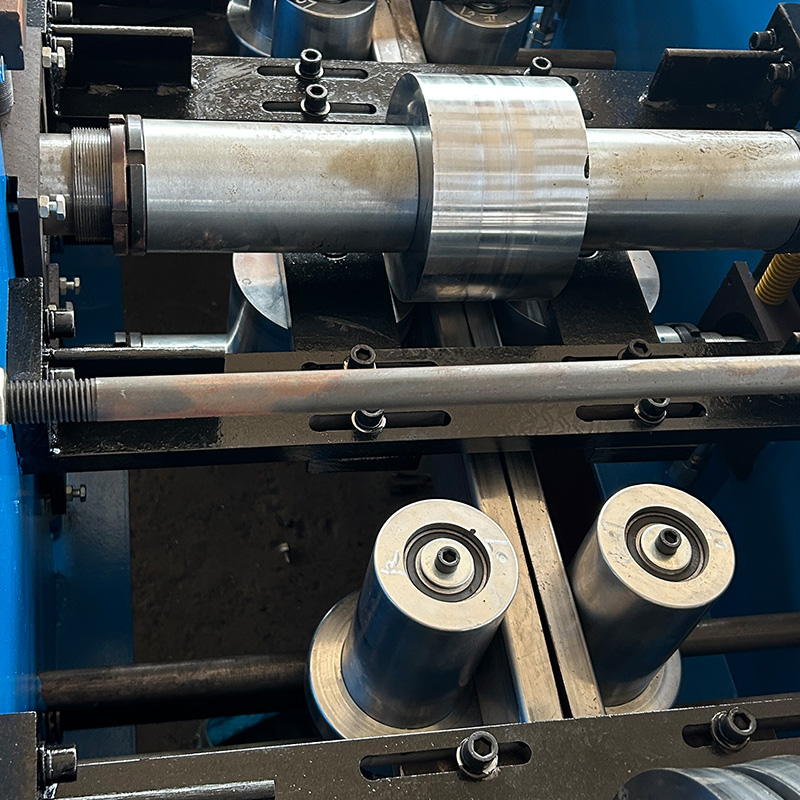
SWOT Analysis
Strengths
- Continuous, efficient production
- Dimensional consistency
- Low operational skill needs
Weaknesses
- Initial die engineering timelines
- Thickness range limitations
Opportunities
- New materials compatibility
- Building code acceptance
Threats
- Low labor cost competition
- Commoditization unless unique
Gutter roll forming offers optimal productivity for production volumes over 200,000 linear feet annually provided equipment selection and operation is professionally managed.
FAQs
Q: What thickness range can be formed?
A: Up to 1.5 mm thickness for steel and 2.5 mm for softer aluminium is possible directly. Thicker metals require separate rolling first.
Q: What automation options are available?
A: Servo feed upgrades for consistency, monitoring systems to reduce human errors, stacking robots etc. minimize manual intervention.
Q: What testing standards apply for rain gutters?
A: Various durability tests for load capacity confirm designs meet codes like AS/NZS 2904 and EN 1462. Leakage testing ensures water tightness.