Roll forming allows continuous, efficient and economical shaping of metal coils into customized sections using roller dies. OEM door frame roll forming machines produce door frame profiles rapidly to consistent specifications.
This guide covers all key aspects of procuring and deploying oem door frame roll formers for optimum productivity.
Overview of OEM Door Frame Roll Forming Machines
OEM stands for original equipment manufacturer. OEM door frame roll forming machines are customized as per design requirements to mass produce door frame profiles.
Available in manual, semi-automatic and fully automatic variants, key advantages are:
- High production speed
- Consistent quality output
- Cost effective for volume production
- Customization to suit profile needs
- Quick changeovers between sizes
- Scalability for increasing demand
Additional enhancements like holes punching, notching, hole patterns etc. can also be integrated in line with profile requirements.
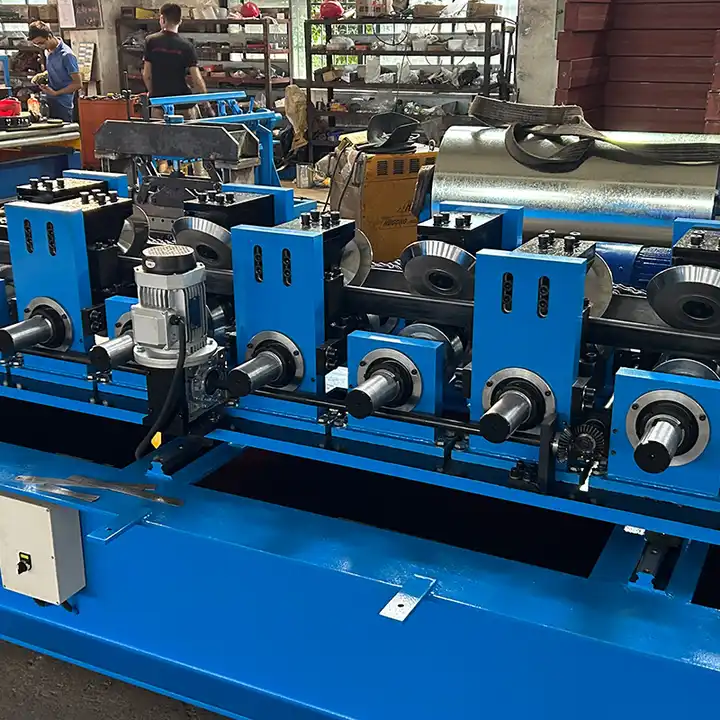
Types of OEM Door Frame Roll Formers
Table 1: Major Types of OEM Door Frame Roll Forming Machines
Machine Type | Description |
---|---|
Manual | Basic model with manual material handling |
Semi-Automatic | Automated forming but manual feed/cutoff/exit |
Fully Automatic | Fully automated material flow and post-forming operations |
Single Profile | Designed for one profile shape |
Double Profile | Creates two profiles simultaneously |
Fixed | Stationary design with fixed layout |
Movable | Portable design with flexible layout |
Light Duty | For thinner gauges and smaller widths |
Heavy Duty | For thicker gauges and wider coils |
Working Principle of Roll Forming
Gradually bending metal strip through a series of stands containing roller dies to shape it into desired cross-section.
Key Stages:
- Uncoiling – Sheet coil loaded onto a decoiler
- Feeding – Strip fed into the roll former
- Pre-bending – Initial shaping
- Forming – Final shaping by roller dies
- Post-forming – Additional features if needed
- Cutting – Cut to length by built-in cutter
- Exit conveyor – Formed cut lengths exits machine
Material Handling Considerations
- Coils – Sheet metal in rolled continuous strips
- डेकोइलर – Feeds strip from uncoiling coils
- Accumulator – Allows continuous running
- Coil Joiner – Joins new coil to end of old one
- Straightener – Removes coil curvature
Profile Shaping Capabilities
Modern OEM door frame roll forming machines can produce:
- Square and rectangular door frames
- Doors with single/double rebate
- Special edge bending styles
- Insulated double skin foam filled
- Knock down and half cut frames
- PVC coated profiles
Forming Limits
- Metal thickness up to 3 mm
- Strip width up to 1250 mm
- Profile height up to 300 mm
Additional Features
- Punching – Holes for hinges etc.
- Notching – Special cutouts if required
- Embossing – Brand name, logo imprinting
- Special cuts – Custom edge shapes
- Special bends – Scrolls, hems etc.
- Coatings – Powder coating, galvanizing
-
Standing Seam Roof Panel Curving Machine
-
बैरल नालीदार रोल बनाने की मशीन
-
Stand Seaming Roof Panel Roll Forming Machine
-
डाउनस्पॉट पाइप रोल बनाने की मशीन
-
गटर रोल बनाने की मशीन
-
Trapezoidal Panel Roll Forming Machine
-
रिज कैप रोल बनाने की मशीन
-
डबल परत पैनल रोल बनाने की मशीन
-
रूफ टाइल पैनल रोल बनाने की मशीन
Key Specification Parameters
Table 2: Main Parameters for OEM Door Frame Roll Forming Machines
Parameter | Typical Values |
---|---|
Speed | 10-100 m/min |
मोटाई | 0.3-3 mm |
Strip Width | 50-1250 mm |
Profile Height | 50-300 mm |
Roller Size | >100 mm diameter |
Number of Stands | 8-24 |
Motor Power | 5.5-132 kW |
Voltage | 220-480 V, 50/60 Hz, 3 phase |
How to Select an OEM Door Frame Roll Former Machine Manufacturer
Key factors in selecting OEM door frame roll forming machine partner:
Table 3: OEM Door Frame Roll Former Machine Manufacturer Selection Criteria
Consideration | विवरण |
---|---|
अनुभव | Years in business, clientele served |
Design Expertise | Custom profile engineering capability |
Manufacturing Facility | Usage of advanced machinery and processes |
Product Range | Portfolio of standard and custom machine models |
Quality | Certified standards compliance, performance guarantee |
Commissioning Support | Installation guidance, operator training |
After-sales Service | Maintenance contracts, prompt spare parts supply |
Delivery Time | Production and shipment schedule |
Pricing | Reasonable transparent quotes |
Global Presence | Sales and service support coverage |
As technology progresses, partnering with established roll forming specialists like [company name] ensures leveraging of the latest domain expertise for door frame profile manufacturing.
Price Range of OEM Door Frame Roll Forming Machines
Pricing varies based on:
- Level of automation
- Production speed rating
- Drive system specifications
- Machine size and coil width capacity
- Material thickness handling
- Additional integrated features
- Quality and precision criteria followed
- Manufacturer’s reputation and volumes
Table 4: Indicative Pricing for OEM Door Frame Roll Forming Machines
Production Speed | Price Range |
---|---|
Low (<20 m/min) | $18,000 – $75,000 |
Medium (20-60 m/min) | $58,000 – $185,000 |
High (>60 m/min) | $95,000 – $270,000 |
Leading OEM suppliers like [company name] offer significant value advantage stemming from process expertise and higher manufacturing volumes while delivering high precision equipment.
Installing an OEM Door Frame Roll Former
Correct installation ensures smooth functioning. Checklist covers:
Table 5: OEM Door Frame Roll Forming Machine Installation Guidelines
Activity | Instructions |
---|---|
Site Readiness | Level floor, power supply access, adequate lighting |
Unpacking | Careful removal without damage |
Positioning | Ensure proper clearances to walls, other equipment |
Levelling | Use spirit level for perfectly horizontal base |
Anchoring | Tighten all anchor bolts to prevent vibrations |
Electrical Connections | Link to suitable power source |
Pneumatic Connections | Connect to compressed air line if required |
Trial Runs | Test machine functions as per operating manual |
Commissioning | Start real production after all checks done |
Seeking machine supplier’s specialists’ assistance is recommended during installation to avoid issues later.
How to Operate an OEM Door Frame Roll Former
Efficient operation maximizes productivity and formed product quality:
Table 6: OEM Door Frame Roll Forming Machine Operating Guidelines
Activity | Procedure |
---|---|
Safety | Wear protective accessories, enable safeguards |
Material Loading | Use appropriate trolleys/cranes, prevent damage |
Machine Settings | Input correct parameters like speed, thickness etc |
Startup Sequence | Follow sequence given in operating manual |
Steady Operation | Monitor strip flow, lubrication, sensors etc |
First Piece Check | Verify cut length dimensions and finish |
Shutdown Sequence | Follow shutdown sequence given in manual |
Data Recording | Note production counts, observations etc |
Proper training to operators on ideal machine handling, troubleshooting and maintenance is vital.
Maintenance Guidelines for OEM Door Frame Roll Formers
Scheduled maintenance activities are crucial for consistent high performance:
Table 7: OEM Door Frame Roll Forming Machine Maintenance Schedule
Frequency | Tasks |
---|---|
Daily | Clean dirt/dust, top up lubricants, check settings |
Weekly | Lubricate all points, inspect electricals and pneumatics |
Monthly | Check roller condition, drive transmission, safety devices |
Quarterly | Oil change, inspect hoses/pipes, production quality audit |
Yearly | Complete inspection and overhaul, replace worn parts |
Additional best practices:
- Maintain updated records of all machine parameters
- Analyze trends to prevent sudden failures
- Plan replacement of wear components
Proactive maintenance enhances machine availability and lowers costs.
Advantages and Limitations of OEM Door Frame Roll Formers
Table 8: Pros and Cons of OEM Door Frame Roll Forming Machines
Advantages | Limitations |
---|---|
Excellent part consistency and accuracy | Higher initial purchase cost |
High production speed with automation | Require more space than other methods |
Low operating costs thanks to electric drives | Size limits in a given model |
Minimal supervision needed | Roll design expertise needed for new profiles |
Safer than press brakes or shears | Not ideal for very low quantities |
Wide range of profiles can be shaped |
For current and future production volumes, OEM door frame roll forming lines provide efficient fabrication solutions.
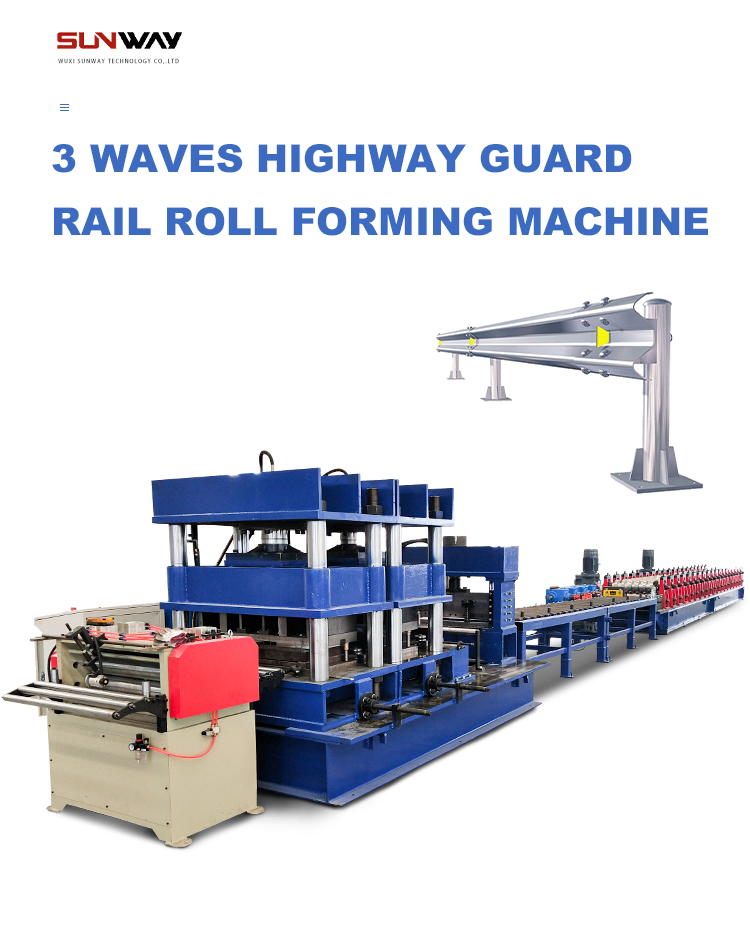
सामान्य प्रश्न
Q: What sheet metal materials can you use?
A: Most thin, ductile metal coils like low carbon steel, stainless steel, aluminium etc. under 3 mm thickness.
Q: What profile dimensions are possible?
A: Around 300 mm maximum profile height and 1250 mm max strip widths are possible in standard models. Custom built variants can go bigger.
Q: How easy is it to switch between profiles?
A: Manual machines allow profile changeovers in 1-2 hours. For automatic lines, expect around 4-6 hours since mechanical & controls adjustments are needed.
Q: What automation features are offered?
A: Robotic part handling, punching holes/notches, embossing, specialized downstream operations can be integrated.
Q: What support do OEM suppliers provide?
A: Reputed manufacturers offer complete support for machine shipping, installation, operator training as well as prompt after-sales service.
Q: What are typical warranty terms?
A: Most OEM suppliers offer 12-18 month standard warranties on door frame roll forming machines covering materials and workmanship defects.