oem c purlin roll forming machines are used to continuously bend and form metal coils into C-shaped purlin beams for the construction industry. As an original equipment manufacturer (OEM), these machines can be customized to produce purlins of different sizes and specifications per client requirements.
Introduction to oem c purlin roll forming machine
Roll forming is a continuous bending process that forms long metal sheets or coils into customized profiles using a series of successive rolling stands. OEM purlin roll formers transform plain metal coils into finished C or Z-shaped purlins through the following steps:
Material Feeding
Uncoiling and feeding metal coils into roll forming line
Alignment and edge preparation before forming
Controlling feed speed in sync with rollers
Profile Forming
Progressively bending sheet through consecutive roller stages
Each stand incrementally forms desired ribbing and shape
Connects to shape cutter for final custom purlin length
Design and Customization
Machines can form C or Z purlins of different sizes
Specialized tooling for custom purlin dimensions
Operators program and adjust forming parameters
OEM purlin forming lines offer:
- Higher outputs up to 18-25 meters per minute
- Quick roll and die changeovers
- Option for inline punching and shearing
- Automated control systems for efficient operations
- Customization for specialized purlin specifications
Compared to manual bending methods, purlin roll formers provide consistent, superior quality beams at higher production volumes necessary for large construction projects.
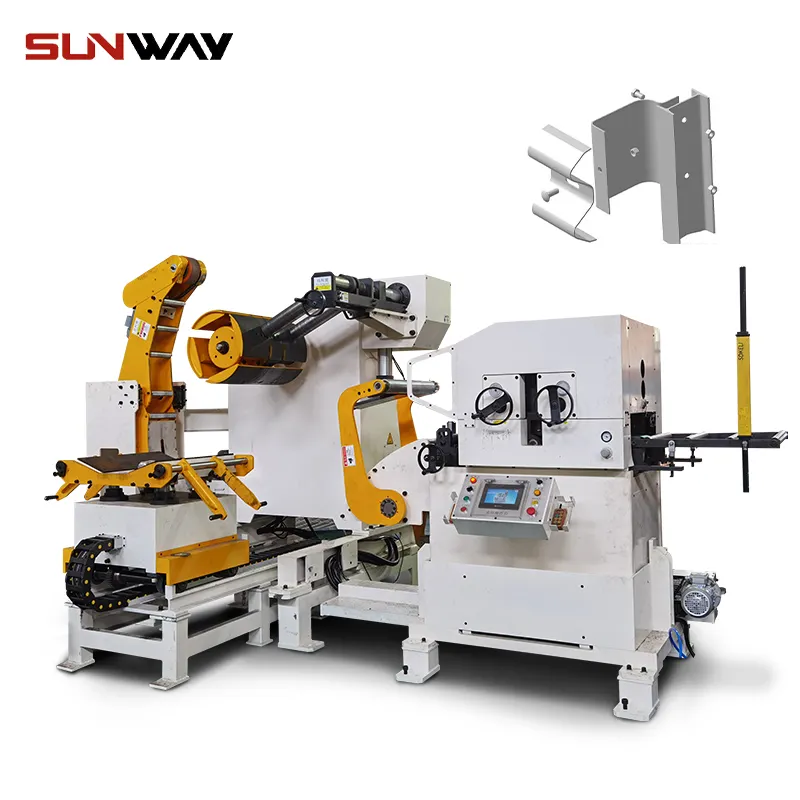
Major Components of oem c purlin roll forming machine
Component | Function |
---|---|
Uncoiler | Feeds raw coil stock into machine |
Feed table | Controls material speed into forming stands |
Roll forming stands | Each set of rollers progressively forms C shape |
Hydraulic system | Provides power for bending process |
डेकोइलर | Recoils formed purlins for safe exit |
Cutter | Shears purlins to length after roll forming |
Control panel | HMI and PLC automates production |
Working Process of OEM C Purlin Forming Machines
The working principle behind purlin roll forming involves continuously shaping flat metal stock into final C or Z ribs by passing it through a series of rolling dies in a sequential bend-form-bend process:
Step 1) The uncoiled raw material from a metal coil is fed into the feed table which straightens and aligns the strip before the first forming stands.
Step 2) The metal sheet then passes through a series of rolling stations, each with a set of top and bottom rollers.
Step 3) At every stand, the sheet is incrementally bent into the shape of a C rib with specific dimensions based on client requirements.
Step 4) Specialized tooling is used to create different purlin sizes – the rollers have machined contours that impart desired bending during each rolling phase.
Step 5) Finally, the formed C profile sheets goes to the cutter which shears it to customizable lengths as per order specifications.
Step 6) Formed purlins exit the line through a set of decoiler rolls for safe offloading.
OEM purlin lines are equipped with programmable automation to control this forming process and produce beams efficiently in large volumes. Operators can set the tandem rolling stations to create the exact purlin size and cut lengths as needed in each client order using the HMI panel.
Main Technical Parameters
Specifications | विवरण |
---|---|
Production Speed | 18-25 meters per minute |
Material Thickness | 0.7 – 2.5 mm steel coils |
Finished Size | 75 to 300 mm purlin depths |
Machine Power | 11 kw main motor |
Line Voltage | 380V, 50 Hz AC 3-phase |
Structure | Welded steel frame |
रोलर सामग्री | 45# high-carbon steel |
Roll Stands | 10 minimum; 16 stands typical |
Length Accuracy | ± 1.5 mm tolerance |
Oil Tank Capacity | ≥250 liters |
Operation Mode | Automatic PLC control |
-
नालीदार पैनल रोल बनाने की मशीन
-
लाइट गेज स्टील रोल बनाने की मशीन
-
ऑटो आकार बदलने योग्य सिग्मा शहतीर रोल बनाने की मशीन
-
ऑटो आकार बदलने योग्य CZ शहतीर रोल बनाने की मशीन
-
ऑटो आकार बदलने योग्य Z शहतीर रोल बनाने की मशीन
-
ऑटो आकार बदलने योग्य घन शहतीर रोल बनाने की मशीन
-
स्टील बॉक्स प्लेट रोल बनाने की मशीन बनाना
-
दीन रेल रोल बनाने की मशीन
-
ओमेगा शहतीर रोल बनाने की मशीन
Choosing oem c purlin roll forming machine
Construction contractors looking to set up purlin manufacturing plants should evaluate suppliers on:
Product Quality
- Material grade and thickness capacity
- Profile dimensional accuracy
- Surface finish of formed purlins
- Cut length precision
- Bending quality consistency
Production Output
- Line speed and hourly output
- Quick changeover between sizes
- Easy adjustment of parameters
- Reliable uncoiling and recoiling
Customization Ability
- Range of purlin sizes produced
- Special profiles beyond C and Z
- Custom roll pass design
- Integration of auxiliary equipment
Automation Features
- User-friendly HMI for production monitoring
- Auto calculation of length compensation
- Preset recipes for fast size changes
- Real-time monitoring of line malfunctions
Service Support
- Operator training provided
- Maintenance staff assistance
- Quick response for breakdowns
- Local suppliers preferred
Evaluating multiple manufacturers on these criteria increases chances of selecting an ideal OEM C purlin roll former tailored to construction needs.
oem c purlin roll forming machine Suppliers
कंपनी | Location | संपर्क करना | Price Range |
---|---|---|---|
Rollex Group | भारत | +91 98 restless329 | $100,000 – $250,000 |
posture Machines | China | +86 15502965002 | $80,000 – $150, 000 |
Installing OEM Purlin Roll Forming Equipment
Proper installation is key for peak performance of purlin roll lines. Here are key steps:
Site Preparation
- Level concrete or steel foundation
- Sufficient working area for safe operation
- Proper shed or enclosure for weather protection
- Adequate power supply near equipment
Transportation & Unloading
- Use cranes, forklifts to unload components
- Take care not to damage parts during shifting
Positioning & Alignment
- Assemble stands, tables as per drawings
- Precision alignment of rolling stations
- Proper anchoring and machine stability
Trial Runs & Testing
- Check uncoiler, hydraulic power, controls
- Run without material to verify functioning
- Parameter tweaking to validate forming
- Inspect if system meets specifications
Taking appropriate measures during installation prevents potential issues that can disrupt functioning after commissioning.
Operation and Maintenance Best Practices
Activity | Frequency | Purpose |
---|---|---|
Visual Inspection | Daily | Check for leaks, wear, loose parts |
Roller Maintenance | Monthly | Grease bearings, calibrate gaps |
Hydraulic Oil Change | 6 months | Replace oil to avoid overflow, leaks |
Machine Lubrication | Weekly | Apply lubricants to prevent rusting |
PLC Backup | Monthly | Save updated parameters, recipes |
Safety Audits | Quarterly | Ensure no potential hazards for workers |
Advantages of oem c purlin roll forming machine
- Higher production volumes save time and costs
- Superior uniformity versus manual bending
- Quality consistency batch after batch
- Programmable automation increases efficiency
- Swift size changes with adjustable tooling
- Safer process compared to site fabrication
- Scalability to match growing order volumes
- Limited manpower needed for operation
- Low maintenance without molds or dies
- Compact, continuous production saves space
Limitations of C Purlin Roll Forming Process
- High initial capital investment
- Complex electromechanical parts prone to issues
- Trained staff needed for maintenance
- Limited flexibility versus custom fabrication
- Fine tuning of processes needs expertise
- Auxiliary tools required for complexity
- Lengthy production times for special alloys
- Space constraints can limit line length
Proper precautions and preventive strategies during selection, commissioning and operations can overcome these limitations and derive maximum ROI from roll formers over years of working.
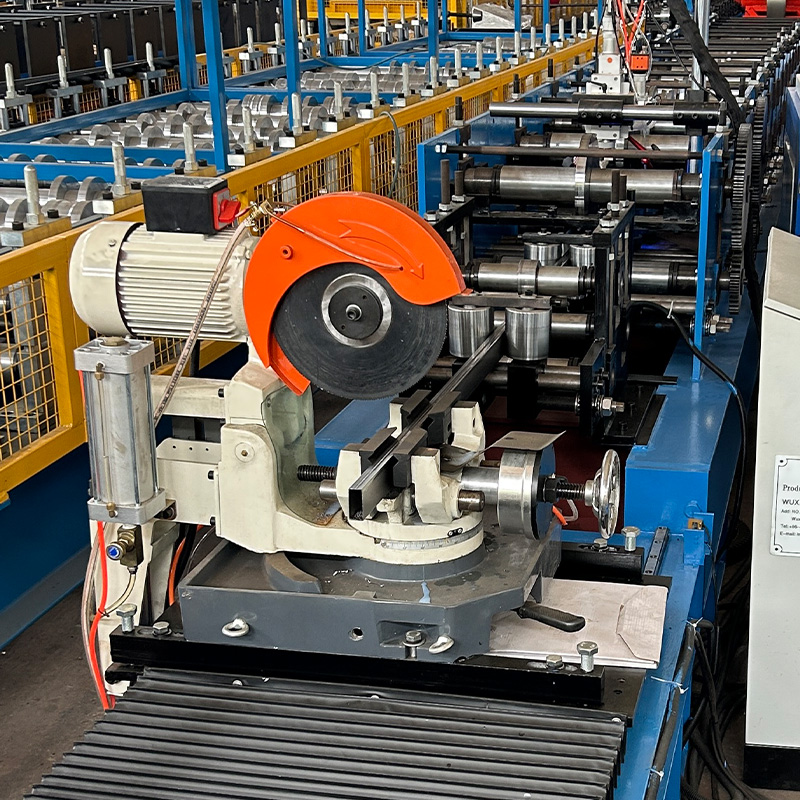
सामान्य प्रश्न
Q: What sizes of C purlins can be formed on OEM roll lines?
A: Standard machines can produce 75 to 250 mm depth symmetric C profiles. Customized roll pass design allows purlins up to 300 mm depth if required.
Q: How to determine correct line speed for quality purlins?
A: Typical speeds are 18-25 m/min based on material grade. Heavier gauges may require slower forming for proper profile development without defects.
Q: What processes are needed to join formed purlin sections?
A: Self-tapping screws can connect purlin beams on site. For very long spans, specialized presses join sections through crimping or embossing to get required overlap strength.
Q: How to ensure dimensional accuracy of finished purlins?
A: Precision ground steel rollers, accurate feed measurement systems, tension controls, and depth stops on cutter are some ways purlin quality consistency is achieved.
Q: What auxiliary equipment can be added to purlin roll lines?
A: Decoilers, stackers, straighteners, hole punching, specialized cutting and bending machines can be integrated for secondary processing as per client needs.
निष्कर्ष
OEM C purlin roll forming equipment represent efficient, high-quality solutions for companies venturing into purlin manufacturing. Appropriate due diligence of technical parameters and after-sales support while selecting suppliers goes a long way in determining outcomes. Proactive maintenance combined with good operating practices ensure maximum working life with minimal disruptions. When configured optimally for construction demands, these machines deliver substantial productivity benefits versus alternate purlin fabrication approaches.