mobile roll forming machine delivers lightweight fabrication capabilities onsite converting sheet coils or blanks into various structural framing, roofing, fencing, architectural panel profiles facilitating rapid enclosures ideal for temporary venues, staged construction needs or hard reach locales where transporting in heavy preformed sections poses challenges like public parks, alley access or offshore platforms. Portable electric and manual brake lever powered mobile roll forming outlines ideal for producing simple open box beam, square/circular hollow and single grooved channel section geometries.
Overview of Mobile Roll Forming Machines
Portable roll forming equipment aims for simplified compact designs focused on easy site maneuverability rather than high speed mass production lines which traditionally anchor fixed factory settings.
Table 1: Background on Mobile Roll Forming Machines
Attribute | Description |
---|---|
Working Concept | Transportable simplified roll forming lines |
Key Components | Decoiler, forming rollers, sheet support table, electric motor or manual brake lever drive |
Source Materials | Steel coil strips, sheet blank sections |
Section Profiles | Square, rectangular and circular hollows, I-beam, single open channels |
Output speed | Manual: 0.5 meter per minute. Electric: 1.5 to 6+ meters per minute |
Primary Mobile Applications | Temporary structural shelters, fencing, staged construction projects |
These transportable roll forming machines ranging from lightweight lever powered a frames up to trailered electric motor drive systems aim for flexibility delivering forming functionality direct onsite bypassing shipping formally profiled parts otherwise limited to highway transport widths and route access clearances. Applications well suited cover straightforward geometries like square structural framing uprights or fencing rails curved into box beam, cylindrical/tubular and single open back channel profiles commonly utilized for basic shelters and staged project enclosures where weather covering install rapidity temporarily remains vital before following with formal building shells.
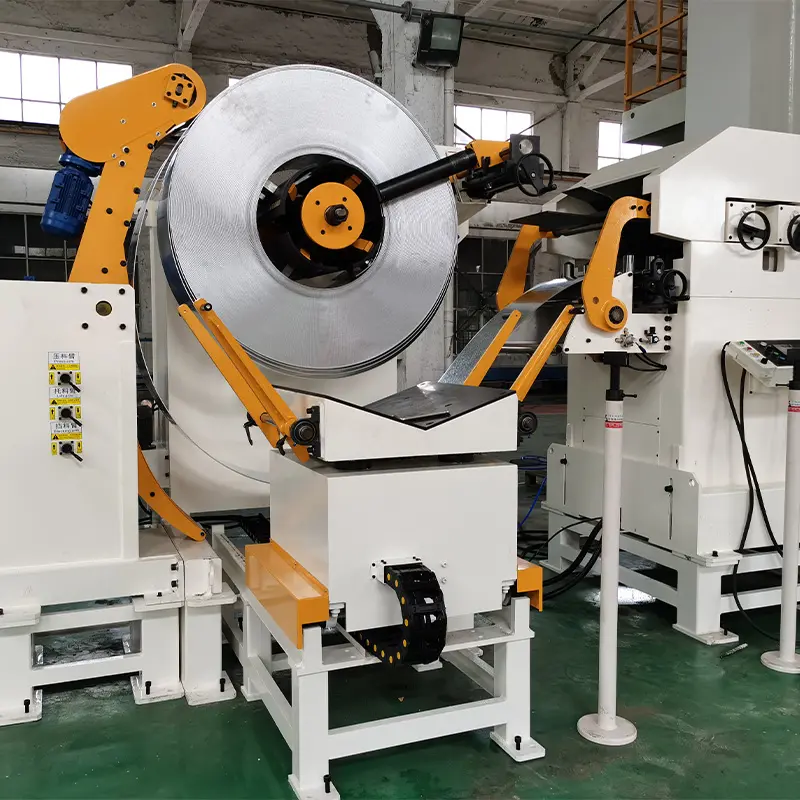
Working Principles of Mobile Roll Formers
Mobile roll forming machines transform metal strips or sheet cut blanks into structural sections by progressing stock through consecutive roller dies staged in an inline layout – with electric motor or manual lever arm mechanisms incrementally advancing material through the series of bending progressions to shape desired contour profiles.
Table 2: Core Components of Mobile Roll Forming Machines
Section | Purpose | Considerations |
---|---|---|
Material inlet guides | Stage strip/blanks into process | Table assists supporting stock |
Forming roll housings | Hold graduated bend roller shafts | Pillow block bearings provide flexibility plus friction minimizing rotational torque transfer across consecutive roller pairs |
Electric drive motor or manual lever pull handles | Apply motivation torque rotating drive roller advancing strip through machine | Powered options facilitate increased output speeds |
Adjustment controls | Facilitate situating movable top roller platens optimally contouring stock | Spring tensioning retains settings across production runs |
Outfeed support table | Safely back up strip maintaining infeed alignment entering machine while supporting exiting formed lengths | Roller tables aid transferring longer sections |
Thanks to a simplified subsystem layout focused on being compact when collapsed while fast deployment erection schemes aid setup relocating fabrication functionality job site adjacent. These lightweight versatile mobile roll formers provide previously unattainable section forming direct delivered where needed eliminating external part forming delays.
Types of Mobile Roll Forming Machines
While all portable roll formers share common goals around transportability, equipment distinctions emerge categorized by drive power mechanisms, number of forming roller heads enabling profile geometries and auxiliary support provisions determining appropriate selections aligned with frequency plus complexity of moving paired against necessary section dimensional accuracies and feature details.
Table 3: Common Mobile Roll Former Machine Configurations
Configuration | Characteristics | Example Uses |
---|---|---|
Manual drive braking lever | Floor jack erection aid. 3-5 roller heads for basic forms | Temporary fencing rented short duration sites |
Electric motor single phase | 4 direction lockable casters. Enclosure safety guarding | Staged construction projects with power available |
Electric motor three phase | Removable tow trailer. 6-10+ roller heads facilitate complex forms | Architectural detail elements unfeasible prefabricating |
Automated speed control | Portable generator power when pulses needed variable | Contour lighting housings around stages/arenas |
Digital readouts | Counts linear meterage or pieced quantities | Assists billing accurate formed amounts |
Supporting roller conveyors | Extend parts handling abilities | Sophisticated multi form manufacturing processes |
Light duty products focus budget affordability transporting fabrication functionality periodically relocating minimally equipped maximizing manual leveraging. Meanwhile purpose built workshop outfitted high roller count machines target maximizing output speeds, dimensional accuracies and section contour complexity tolerances rivaling traditional factories.
Careful consideration choosing electric, relocation frequency, automatically and accuracy necessities strike balances optimizing total operating cost tradeoffs.
Key Mobile Roll Former Technical Specifications
Optimizing portable roll former layouts involves appropriately weighing critical machine parameters balancing transportability and onsite maneuvering against production throughput targets plus part dimensional variability ranges and feature intricacy needs per architectural project designs flare types.
Table 4: Mobile Roll Former Machine Specification Considerations
Parameter | Typical Range | Key Factors |
---|---|---|
Drive type | Manual or electric motor | Power accessibility and speed goals |
Forming stations | 3 to 10+ roller heads | Part contour complexity |
Working widths | Up to 32 inch coil | Available stock strip widths |
Working thicknesses | 26 to 10 gauge | Strength necessities |
Working speeds | .5 to 6+ meter/minutes | Throughput targets |
Linear length capacities | 1.5 to 16+ meter sections | Supporting roller conveyors extend abilities |
Accuracy capabilities | ±1 to 3 mm | Project precision necessities |
Weight compacted | 150 to 1450+ kg | Vehicle carrying capacities |
Getting optimal sidewall piloted support bearing ratios between consecutive roller heads ensures smooth interlocks minus tearing adopting appropriate small incremental bend arc curvature radius per pass.
Establishing upfront compacted transportation size constraints plus extended operational fabrication width, thickness, speed parameters and permissible tolerance envelopes allows appropriately allocating capital investments confident specified architectural project variable section geometries become fulfilled as designed.
-
वाइनयार्ड पोस्ट रोल बनाने की मशीन
-
ऑटो आकार बदलने योग्य सिग्मा शहतीर रोल बनाने की मशीन
-
पीवी माउंटिंग ब्रैकेट सी शेप प्रोफाइल रोल बनाने की मशीन
-
सीजेड शहतीर चैनल कोल्ड रोल बनाने की मशीन पूर्ण ऑटो जस्ती स्टील प्रोफाइल
-
पीवी माउंटिंग ब्रैकेट रोल बनाने की मशीन (एचएटी / ओमेगा प्रोफाइल)
-
पीवी माउंटिंग ब्रैकेट जेड शेप प्रोफाइल रोल बनाने की मशीन
Top Mobile Roll Former Equipment Manufacturers
Leading China metalworking machinery factories provide versatile yet portable roll forming equipment selections spanning manual lever drive braking systems up to fully automated CNC adjustable motorized lines with touchscreen controls recipe storing hundreds of common structural framing parameters nesting within highway towable workstation enclosures for ultimate onsite production flexibility freedom.
Table 5: Leading Mobile Roll Former Producers
Manufacturer | Associations | Target Markets |
---|---|---|
Botou Jianteng | 15 years focusing portable designs | Developing economy builders needing flexibility |
Hebei New Prime | Featured enhanced support conveyors assist longer runs | Larger contractors supporting multi-site crews |
Henan BEIST | Affordable starter simplicity low technology barriers | Small independent operators managing sporadic demands |
Foshan YSD | High accuracy facial panel lines | Architectural metal applications |
Hangzhou Rollform | Container enclosed humidity/dust protection provisions | International equipment rentals |
These factory teams leverage extensive light gauge roll forming expertise through sister mass production lines nurturing precision high speed process understandings applied engineering purpose built transportability machines maximizing production potential delivered direct onsite. Sophisticated CNC programmability further adapts contouring abilities matching custom structural steel sections as architectural creativity requires right scheduled where needed.
And thanks greatly accelerate project timelines reduced involving awaiting custom brake press tooling combined high transportation costs associated heavyweight prefabricated sections. Portable rollers facilitate medium production batches dimensionally precise befitting artistic styles exactly staging framing erection sequence work progress desired.
China Mobile Roll Former Line Pricing Considerations
Delivering over 50% baseline machinery costs savings against comparative western built transportable systems while matching European quality benchmarks, China built mobile roll forming investments enable less than 2 year ROI timeframes for most small construction teams or specialty metal fabricators. Whether supplementing production between legacy shop presses refits or entering new sector opportunities, these mobile outfitted workstations provide affordable scaled entry expanding customer project variety potentials.
Table 6: China Mobile Roll Former Line Price Analysis
Type | Price Range | Key Scales |
---|---|---|
Manual and mechanical actuation gear | $3,500 – $15,000 | One person operated capabilities |
Electric motor driven lines | $8,500 – $65,000 | Crew production output capacities |
Towable trailer enclosed | $25,000 – $155,000 | Lockable shop capabilities delivered direct adjacent project sites |
Ancillary punching, counters and support conveyor accessories | $2,500 – $7,500 per station | Right sized integrated mechanics maximize material handling throughputs |
Significant capex savings over costly European built alternatives allows smaller contractors easier differentiated market entry at higher profit margins – or provides larger established builders and architectural metal providers sufficient cost room experiment innovating location oriented fabrication/assembly approaches faster enclosing temporary weather sensitive work staging phases.
Carefully weighing true existing crew capabilities against realistic throughputs attainable balances specifications suiting budget.
Best Mobile Roll Former Operational Practices
Properly siting compact portable lines followed by preventative monitoring facilitates rated repeatable output over 20+ years of extended China built machinery service lifecycles thanks accessible local servicing capabilities. Whether supplementing legacy pressing capacity refits between factory downtimes or entering new scale opportunities, outfitted versatile mobile metalworking workstations facilitate productivity potential.
Table 7: Smooth Mobile Roll Operation Recommendations
Practice | विवरण | Benefits |
---|---|---|
Compact footprint siting | Balance 6 sided clearances | Ensures safe clearances plus working clearances |
Maximum level platform | Eliminate twisting alignment concerns | Superior linear dimensional repeatability |
Locking mobility during operation | Prevent inadvertent dangerous movements | Isolates vibration resonance risks |
Periodic control calibrations | Verifies accuracy readings | Builds correctly as designed first time proper |
Program parametric cataloging | Documentation aids rapid changeover recalls | Reduces set up errors unexpected |
Upgrade budgeting | Plan additional stations fulfillment | Right sizes integration expansion investments later |
Inspecting factors influencing reliable extended duty cycles like:
- Monitoring frame weld integrity impacting alignments
- Scheduling specialist maintenance examining component wearing before failure shutdowns
- Budgeting annual preventative upkeep accommodating predictable maintenance planning
Provides ownership confidence consistently outputting rated design quality production over equipment lifetime.
Partner Selection Essentials for Smooth Operations
Discerning reputable mobile roll former machinery exporters against prudent benchmarks provides clarity ensuring chosen collaborators provide appropriately specified equipment solutions meeting current expectations while offering future add on stations scaling production capabilities matching anticipated manufacturers growth years forward.
Table 8: Ideal China Mobile Roll Former Partner Traits
Evaluation Aspect | Preferred Details | Risk Management Benefits |
---|---|---|
Niche focus | Years dedicated perfecting compact versatility first | Reduces unexpected shutdown business surprises |
Staff talent retention | Skilled welding, electrical and mechanical engineering staff continuity | Promotes incremental optimizations maximizing fatigue lifespans |
Sincere relationship importance | Avoiding merely transaction interactions | Built mutual commitments accelerate issue resolutions |
Precision capabilities | Advanced vision inspection calibration integration | Ensures standards conformance avoiding failures |
Support detail | Virtual troubleshooting tools options accessibility | Accelerates technicians issue resolution productivity over distances |
Requesting existing production line tours while scrutinizing after sales Southeast Asia support accessibility demonstrates responsive collaborative commitments better catering subsequent expertise augmentation needs as regional order demand patterns evolve.
Cultivating relationship rooted mutual trust paves technical prosperity even through unforeseen emergency circumstances thanks open visibility and timely issue resolution keeping enterprises progressing strong.
Future Outlooks Across Light Gauge Construction Industries
With resurgent global construction activity emerging across developing Asian and African regions on heels their industrialization plus improving infrastructure investments, lucrative volume tailwinds look favorable supporting continued growth around light gauge cold formed framing and small section structural component demand supporting both residential plus commercial building initiatives over the upcoming decade.
Table 9: Global Light Gauge Steel Construction Industry Projections
Region | 2026 Forecast Market Scale | Notable Macro Trends |
---|---|---|
East Asia | $185+ billion | Strongly growing consumer economy and discretionary expenditures with swelling middle class and urbanization |
South Asia | $125+ billion | Expanding middle class and manufacturing spurring real estate builds |
Middle East & North Africa | $95+ billion | Strong populations desiring modernization will drive continued growth |
Central Asia | $68+ billion | Youthful demographics support adoption as stabilization improves |
And thanks rising ESG pressures and policies emphasizing deconstruction favoring reuse recycling, there looks strong impetus shifting construction specifications selecting thinner cold form building techniques maximizing recycled contents and end life reclamation streamlining waste reductions over other heavier footprint material legacies.
So admirably suited facilitating remote delivery difficult access locales plus rapid deployments when timing remains essential light gauge component demands look strengthening well into future decades as developing regions advance plus environmental protections progress. These bright global market outlooks look quite favorable supporting continued equipment investment shifts as organizations substitute outdated heavier lines better economizing shipments adopting the newest lightweight Chinese designed mobile transportability metal fabrication production innovations offering leapfrog per piece savings achieving tasks previously believed impossible.
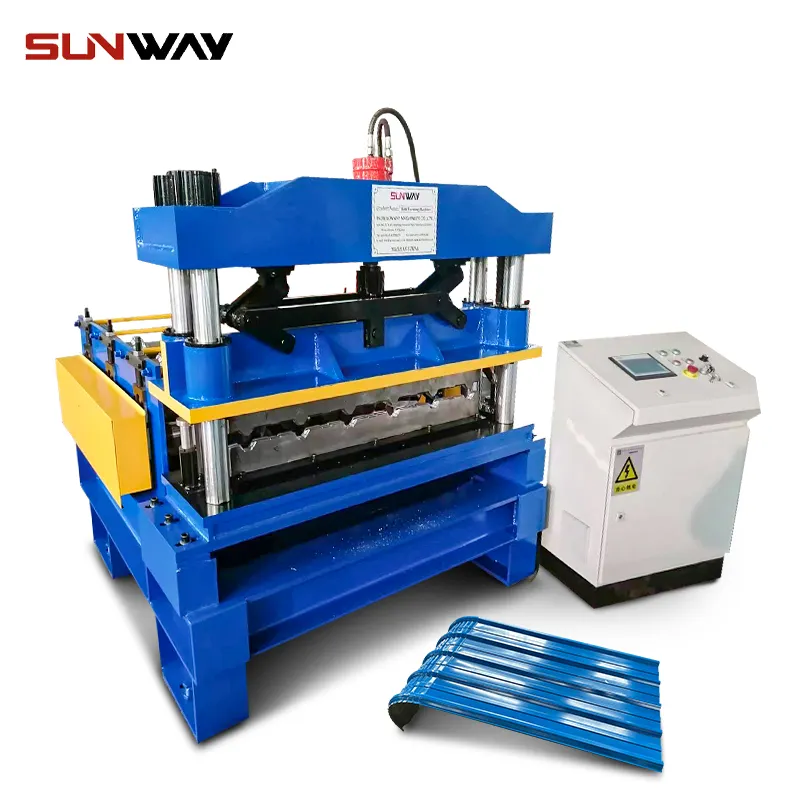
Frequently Asked Questions
Q: What risks around mobile roll lines need addressing?
A: Pinch hazards from rotating draw rollers, exposed electrical busbars and hazards falling onto unsupported sheet strip mandate proper operator training, isolation barriers and control safety integration most importantly before field transports begin.
Q: What metal thickness ranges cost effectively form?
A: 0.5mm to 1.2mm finished strip gauges well accommodate roll forming structural channels and tubing without subsequent flattening deformation concerns under static loading floor/roof spans while keeping prices affordable using common coil stock sourcing. Architectural projects allow heavier platings when adding bracing.
Q: What ancillary stations provide additional production benefits?
A: Common complementary equipment like hole punching, dimpling, header crimping and even miter saw cutoff saws often get mounted flanking lines helping completion onsite finished framing elements installations.
Q: What lifecycle timeline assumptions justify capex budgets?
A: With adequate preventative maintenance expectations following recommended product manuals – 15-20 year machine services with occasional upgrades makes reasonable lifecycle assumptions if no excessive damage/abuses occur expediting replacements.
Q: When should in-house lines become considered over outsourcing?
A: Below ~250 meters monthly roll forming demands generally makes outsourcing fabrication advisable before ownership gains cost warrants transition. Above that threshold direct metalworking control accelerations reacting against fluctuating market demands normally better suits most manufacturers objectives.