Metal stud and track roll forming lines efficiently transform coiled steel into C-shaped channel profile framing studs paired with U-shaped track elements used extensively constructing interior walls and structural builds thanks to economical light gauge cold-formed structural capabilities modernizing construction techniques accelerating schedules. This guide offers builders, contractors and architects extensive details about China roll former types, technical specifications, top machinery manufacturers, pricing insights, installation guidance plus total cost of ownership comparisons.
Overview of Metal Stud and Track Roll Forming Machines
Roll forming machinery incrementally converts metal coil feedstock into structural light gauge steel framing studs and tracks by progressing stock through consecutive contouring roller die stations with automated feeding, punching and cutting steps integrated preparing finished components pulled continuously off the line.
Table 1: Background on Metal Stud and Track Roll Forming Machines
Attribute | Description |
---|---|
Working Principle | Continuous cold formed steel roller die bending |
Key Components | Decoiler, guides, punching & cutoff |
Source Materials | Hot-dip galvanized coils |
Profile Types | C studs, U tracks, plus custom forms |
Output Speed | 16 – 45 meters per minute |
Primary Uses | Interior walls, structural buildings |
Unlike fixed die stamping approaches requiring separate sets per profile, flexible roll forming methods facilitate efficient short, medium or mass production runs once initial profiling tooling gets developed – ideal for the repetitive structural members comprising walls, floors and roofs where modular standardization validates economies at scale.
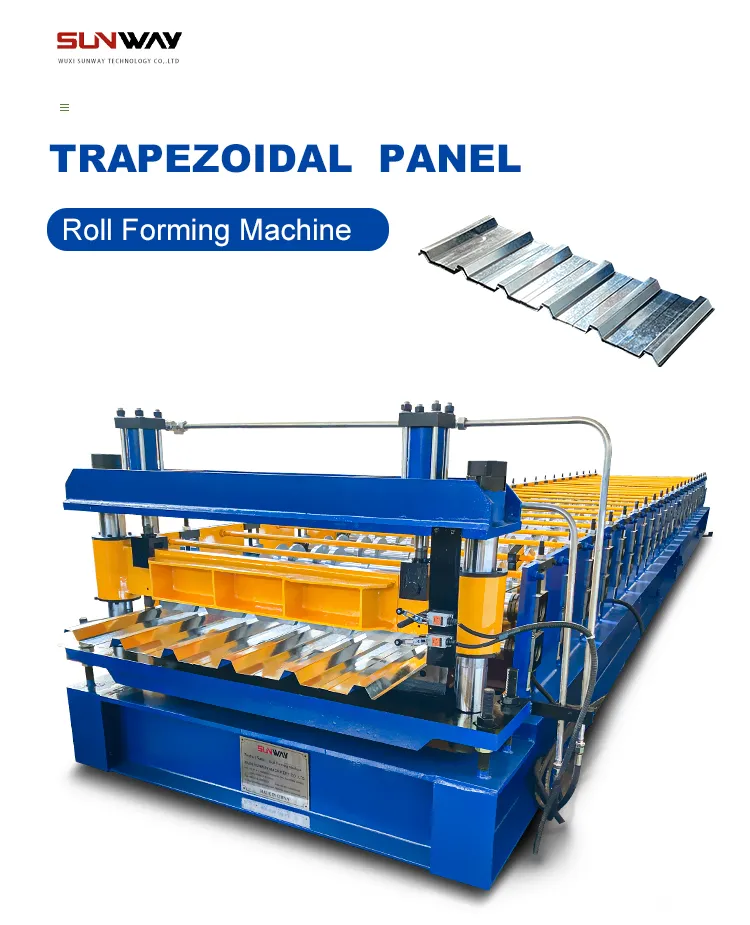
Working Principles of Metal Stud and Track Roll Lines
Metal stud and track roll forming machinery transforms ribbons of galvanized steel coils into structural C and U channels featuring centralized intermittent hole punching facilitating easy vertical mating securement onsite by operators when framing interior walls thanks to compatibility matings with horizontal pressure tracks capturing vertical stud ends while offering opportunities adjusting stories high alignments.
Table 2: Overview of Metal Stud and Track Roll Former Subsystems
Section | Purpose | Considerations |
---|---|---|
Decoiler mechanism | Feeds rolled coil stock | Tension regulation |
Sheet guides | Stage strip into first forming rollers | Centering calibration assurance |
Contouring stations | Shape into channel profiles via roller dies | Changes require forming roller replacements |
Hole punching | Pierce holes along centerline | Optional CNC programmability |
Shearing cutoff | Chop at regular durations | Avoiding burrs delaying installations |
Exit table with stacker | Aligns elements for bundling | Optional but speeds staging framing crews |
Thanks competitive light gauge steel construction techniques displacing heavier gauge built-ups composite framing throwing manpower intensive established methods, efficient automated stud and track roll forming promises remain strong as global urbanization trends stimulate new builds plus renovations remodeling aging housing stocks.
Types of Metal Stud and Track Profile Roll Forming Machines
While all stud and track roll form lines share fundamental coiled metal feeding principles, optional configurations suited for particular throughput environments prioritize between quick width size changeover easements, hole punching and hardware insertion requirements, or roller head duplication extension capabilities determination driving appropriate machinery outfitting selections.
Table 3: Common Metal Stud and Track Profile Roll Former Machine Configurations
Configuration Class | Description | Example Uses |
---|---|---|
Mechanically actuated | Fixed speed cranks alter forming box widths | Small contractors managing limited inventory breadth |
Servo electric control | Touchscreen recipe storage for channel size changes | Large regional builders balancing demand variability |
Modularly expandable | Bolted on same frame extensions | National big box brands centralizing framing production efficiency |
Automated speed control | Variable mill speeds for specialty high-strength channels | Custom residential developers fluctuating ornamental styles |
Inline hole punching | Fixed center or CNC programmable | Reduces downstream prefabrication handling steps |
Supporting conveyors/stackers | Manages finished production logistics | Enables staging optimized workflows maximizing installations |
Purpose built flexibility accommodating interchangeable tooling retrofits adds future abilities adopting late model innovations unforeseen during early investments like servo feed actuation or vision assurances guaranteeing hole punch registry precision frame fitting field assemblies first tries every sequential member without productivity robbing modifications reworking site.
Technical Specifications
Matching appropriately specified metal stud and track roll form lines against design envelope performance constraints permits flexibility configuring optimized machinery investments confident satisfying projected annual demand volumes spanning residential new builds along with stochastic commercial renovation remodeling activities keeping crews continuously supplied.
Table 4: Key Metal Stud and Track Roll Former Specifications
Parameter | Common Ranges | Key Factors |
---|---|---|
Drive types | Geared AC motors | Production volume throughput rates |
Linear mill speeds | 16 – 45+ meters per minute | Channel complexity and architectural gauge metals |
Channel widths | 50mm to 300mm+ | Regional construction conventions |
Metal thicknesses | 0.55mm to 2.0mm | Strength and thermal insulation needs |
Quick size changeovers | Mechanical actuators to servo indexing | Inventory breadth vs model mix flexibility |
Punching centers | Fixed or CNC programmable | Construction compatibility needs |
Interpreting local labor availability composition against incoming project backlog mixes guides proper specifications budgeting covering current and future fabrication requirements minimizing obsoleting risks from market demand cyclic shifts.
China Metal Stud and Track Roll Forming Manufacturers
Top Chinese metalworking machinery factories provide versatile yet very affordable stud and track roll forming machinery selections spanning configurable manual insertion through fully automated high speed CNC programmable lines with touchscreen controls recipe storing hundreds of common structural framing parameters – all nesting within intermodal container enclosures for ultimate logistics conveniences delivering production capabilities globally.
Table 5: Leading China Metal Stud and Track Roll Former Manufacturers
Manufacturer | Profile Catalog Capacities | Target Markets |
---|---|---|
Foshan YSD | 6000+ adjustable parameters | High-end decorative residential developers |
Botou Xianfa | 1000+ structural channel variants | Mid-tier regional contractors balancing model flexibility |
Hebei Yaomei | 800+ common profiles | Cost competitiveness remains vital |
Bluesky Steel Tech | 600+ standard residential construction compatible | International exports maximizing shipping densities |
Hangzhou Rollform | 400+ typical commercial Reno channels | Economic market entry minimizing inventories |
These factory teams leverage accumulated precision high speed cold structural roll forming insights applied engineering versatile framework process lines maximizing efficiency output rates attainable – thanks offset by very reasonable baseline equipment plus operational costs leveraging extensive local skilled labor pools. Sophisticated quick sizing change capabilities enabled by precision programmability plus light framing production commonality promises remain strong as developing regions expand needing construction improvements in increasingly compressed timelines.
And thanks to economical containerized shipping392 densities competiting exports against domestic incumbent western buildingapproaches, global partners specializing global light gauge steel fabrication enjoy new opportunities as accelarating schedule priorites make inregion heavyweight alternatives unfeasible. Whether moderizing housing stocks interpolating new wall placements or staging multi-story commercial builds minimizing concrete drying forms removal delays, metal stud channel integrations promise strong continued growth trajectories well into future decades.
China Metal Stud and Track Line Price Analysis
Delivering over 40% baseline machinery costs savings against comparative western built systems while matching European quality and reliability benchmarks, China built metal stud and track roll forming investments enable 2-3 year ROI timeframes for most purchasers after factoring projected regional operational expenses modeled from existing global customer installation feedback polls. Whether supplementing legacy pressing capacity limits constrained by acute skilled labor shortages or entering new residential/commercial market sector opportunities outright, outfitted containerized workstations provide reasonable upfront capital risk ventures setup adjacent fabrication sites.
Table 6: China Structural Channel Roll Former Line Price Considerations
Configuration Class | Price Range | Production Scales |
---|---|---|
Manual and mechanical actuation gear | $45,000 – $120,000 | One shift outputs up to 20 residential units daily |
Servo electric control with +/- 1,000 recipe storage | $88,000 – $320,000 | Two shifts outputting 100 commercial rooms per day |
Large automatically reconfigurable high speed lines | $155,000 – $450,000 | 20 hour unattended production up to 500 housing unit lots |
Ancillary inline hole punch, stackers and bundling | $15,500 – $55,000 per station | Minimizes finishing steps reduced handling minimizing damage |
Significant capex savings over imported European or American systems allows smaller developing contractors easier differentiated market entry at higher profit margins – or provides larger established builders and architectural franchises sufficient pricing flexibility when experimenting production innovation factories adjacent projects. Estimated freight plus import logistics still keep startup machinery risks reasonable for cautious investors.
Carefully weighing true manpower capabilities against realistic site installation throughputs matching backlogs balances specifications suiting regional construction applicant needs.
Operational Recommendations
Appropriate installation paired with preventative monitoring facilitates rated metal stud and track production over 20 years of extended China built cold roll forming machinery service lifecycles thanks to accessible local servicing capabilities. Whether upgrading legacy rural constructions markets or entering high growth coastal region opportunities, outfitted versatile intermodal containerized workstations facilitate maximizing productivity potential adjacent fabrication sites.
Table 7: Smooth Metal Stud & Track Roll Operation Recommendations
Practice | विवरण | Benefits |
---|---|---|
Test calibration builds | Validate channel fits/+1mm/-0mm tolerances | Ensure framing builder compatibility |
Lockdown leveling | Eliminate twisting alignment concerns | Superior linear dimensional repeatability |
Schedule maintenance | Follow factory recommended PM guidance | Extends mechanical longevity through early diagnoses detecting wearing parts needing planned replacements |
Setup parametric cataloging standards | Group common settings by application minimizing changeover confusion risks | Reduces unexpected variance faults |
Upgrade budgeting | Plan additional stations like hole punching/conveyors | Right sizes ancillary equipment investments supporting scaled growth years forward |
In particular, monitoring factors influencing hitting targets like:
- Verifying mill section frame rigidity integrity without developing unintended calibration deviations from high speed cylinder sequencing billions of punch stroke cycles yearly
- Catching minor knockout die wearing before liberation sidewall burrs develop scattering debris into feed paths shutting lines down
- Forecasting three year major machine component maintenance accommodating predictable preventative repairs needing occasional specialist scheduling
Provides ownership confidence consistently outputting architectural compatibility and dimensional quality rates reliably over decades servicing regional construction industries.
Partner Selection Essentials
Vetting reputable stud and track roll former exporters against prudent benchmarks provides clarity ensuring chosen collaborators provide appropriately specified equipment solutions meeting current expectations while offering future add on stations matching manufacturers growth strategizing over upcoming years.
Table 8: Ideal China Metal Stud & Track Roll Former Partner Traits
Evaluation Aspect | Preferred Details | Risk Management Benefits |
---|---|---|
Niche focus commitment | Years dedicated perfecting cold rollforming versatility first | Reduces unexpected shutdown surprises from allocating sufficient engineering resources upfront |
Staff talent retaining abilities | Skilled welding, electrical and mechanical engineering staff continuity | Promotes incremental optimizations maximizing fatigue lifespans stretching capital investments |
Sincere customer prioritizing | Avoiding short term profit motivated transactional interactions | Built integrity and mutual commitments persevering through adversities |
Precision & flexibility capabilities | Advanced vision inspection and quick changeover innovations | Ensures standards conformance avoiding failures or rushed excessive field reworking |
Attentive sales supporting | Virtual troubleshooting tools option accessibility | Accelerates issue resolution response times building relationsships |
Touring existing factory production lines witnessing staff talent depth while scrutinizing after sales support Southeast Asia accessibility demonstrates responsive commitments better facilitating subsequent expertise augmentation needs as regional order demand patterns evolve over upcoming years.
Cultivating relationships rooted upon mutual trust and respect paves technical prosperity even through unforeseen emergency circumstances thanks open visibility and earnest timely issue resolution keeping enterprises progressing strong through intermittent adversity.
Future Construction Industry Market Outlooks
Bright global construction backlog visibility looks quite favorable supporting continued innovations around cold-formed light gauge steel stud and track framing components supply improving speedier scheduling plus handling conveniences aiding crews accelerating overall project completions over this decade. Thanks rising proportions middle class populations especially across Asia seeking modern housing upgrades as discretionary incomes swell plus commercial market builds supporting consumerism plus enterprise investments, metalforming structural fabrications promise strong continued growth trajectories well into future decades.
Table 9: Global Light Gauge Steel Construction Industry Volume Projections
Region | 2026 Forecast Market Scale | Notable Macro Trends |
---|---|---|
East Asia | $185+ billion | Strongly growing consumer economy expanding middle classes seeking modernization |
South Asia | $125+ billion | Expanding populations needing infrastructure improvements |
Middle East & North Africa | $95+ billion | Strong birth rates desiring updates will drive new builds and renovations |
Central Asia | $68+ billion | Youthful demographics graduating needing economic revitalization |
And thanks rising ecological pressures emphasizing reduced material usages, operational energy minimizations favoring renewable sources plus legislating waste reductions and recycling, there looks strong impetus shifting construction specifications selecting thinner cold form building techniques maximizing recyclable steel content ratios while optimizing shipping densities lowering embodied costs over other heavier footprint material legacy approaches less accommodating disassembly reuse.
So with developing regions advancing favoring metal constructions plus environmental protections progressing, stud and track components promise continued double digit growth trajectories well into future decades as outdated building techniques get modernized through swifter light gauge steel assembly methods. These bright global market outlooks look quite favorable supporting retooling investment shifts as prudent developers substitute outdated equipment for the newest automatic Chinese designed innovations offering leapfrog fabrication savings ratcheting consumer pricing down thanks previously unfeasible production cost control.
Careful budgeting early pilot testing running residual regional inventoried coils sampling product verifies satisfactory conformance and crews compatibility assurances before larger machinery commitments.
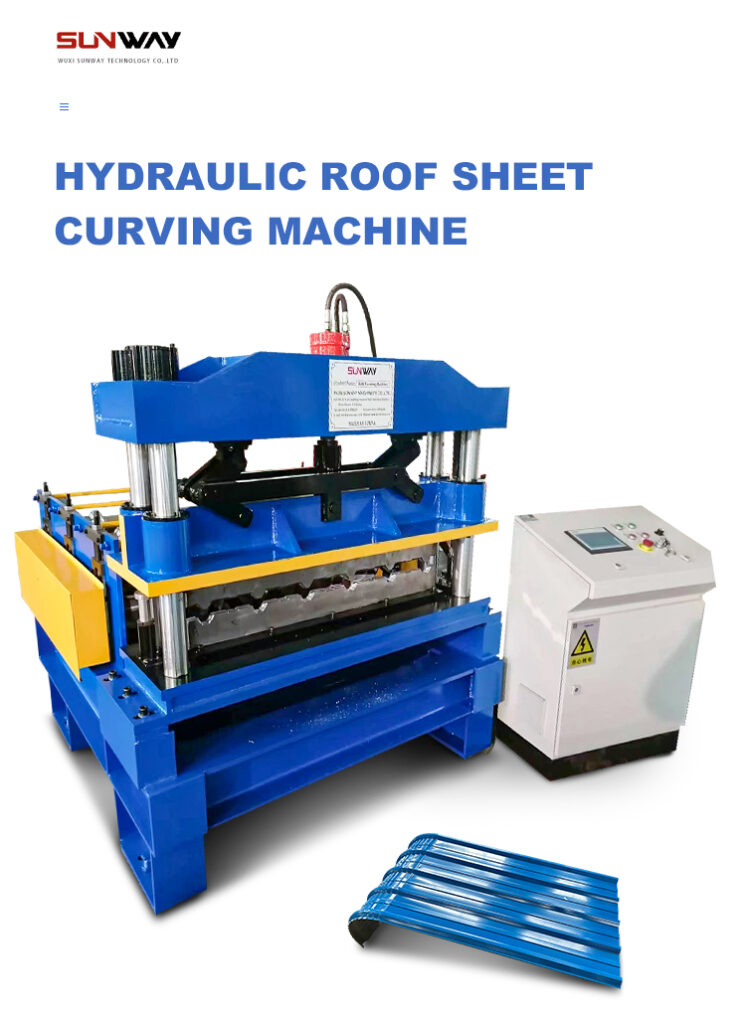
Frequently Asked Questions
Q: What risks around metal stud and track lines need addressing?
A: Rotating draw rollers and exposed electrical busbars pose safety hazards needing proper integration of emergency stop controls plus routine isolation and maintenance procedures.
Q: What metal thickness ranges cost effectively form?
A: 0.5mm to 1.5mm finished material gauges well accommodate roll forming and hole punching structural channels keeping material costs affordable from common coil stock sourcing. Limiting widths under 300mm allows upsizing gauges when adding bracings.
Q: What ancillary stations provide additional capabilities?
A: Inline hole punching, chop saw cutoff, bundling stackers plus even header crimping help completeness minimizing off-line fabrication finishing efforts before site installations.
Q: What typical machine lifespan assumptions justify capex budgeting?
A: With adequate preventative maintenance like scheduled key wearing components replacement between 5-7 years – 20-25 year machine services remain reasonable assumptions barring excessive damage or operator abuses necessitating earlier major refurbishments.
Q: When should in-house lines become considered over outsourcing?
A: Below ~500,000 meters annual roll forming demands generally makes outsourcing fabrication advisable before ownership cost warrants transition. Above that threshold direct metalworking control reactions against fluctuating market demands normally better suits most manufacturers objectives once reliably forecast.