metal roof ridge cap roll forming machine provide decorative finishing touches protecting critical roofing joints. This guide covers various metal ridge cap profile types, working principles of roll forming lines producing them, key machmetal roof ridge cap roll forming machineine components, installation guidelines, maintenance factors, leading global manufacturers, and typical end-use case comparisons.
Common Ridge Cap Profiles Produced by Roll Formers
Profile Type | Key Attributes | Typical Materials |
---|---|---|
Angular ridge caps | Triangle cross-section | Painted steel, zinc |
Flatlock ridge caps | Overlapping flat pan | Aluminum |
Beaded ridge caps | Rounded ornamental bead | Copper |
Venting ridge caps | Perforations for ventilation | Galvanized steel |
Bullnose ridge caps | Convex curved shape | Stainless steel |
Roll formed ridge caps protect vulnerable roofing joints from weather stresses aesthetically. Fit with panels.
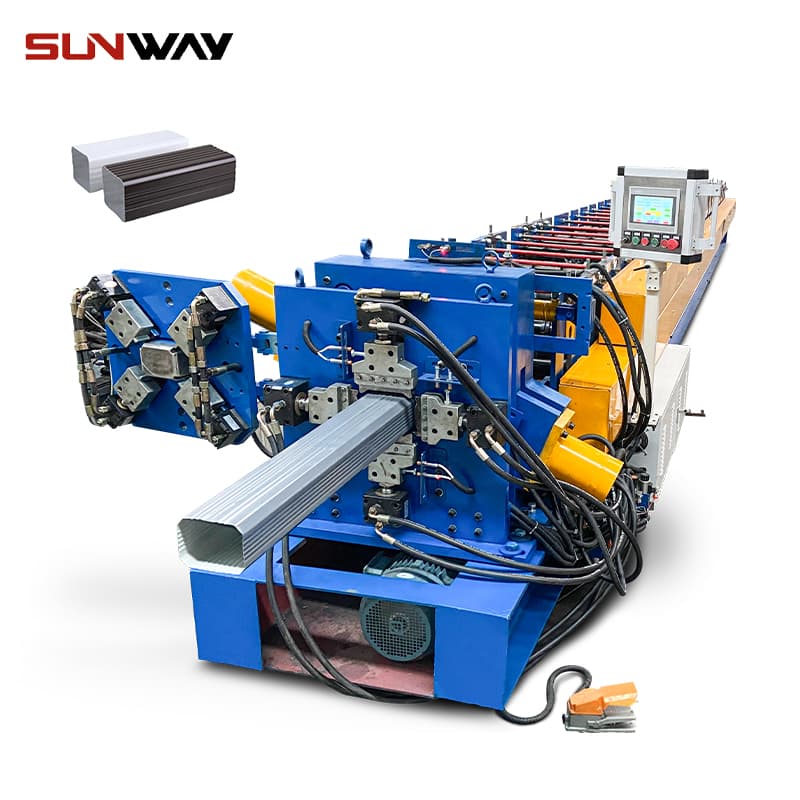
Working Principle of metal roof ridge cap roll forming machine
Continuous forming from coil stock into ridge cap profiles uses a series of bending and shaping roller dies operating in matched male-female pairs. Main aspects:
- Programmable tooling molds specific geometries
- Strategic positioning for metal grain flow
- Automatic edge guidance and gauging
- Supporting decoilers and straighteners
- Flying shear length cutoff control
- Exit tables, automated packing
Fully formed cap sections exit at the designed lengths continuously when feeds optimized.
Key Components of metal roof ridge cap roll forming machine
Component | Role |
---|---|
डेकोइलर | Feeds raw metal coil stock |
Entry guides | Aligns strip before dies |
Forming stations | Each imparts profile incrementally |
Control cabinet | Manages production logic |
Hydraulic unit | Powers die actuation |
Flying cutoff | Trims caps to length |
Exit conveyor | Transfers finished caps out |
Standardized modular designs allow changing machine widths easily.
-
Highway Guardrail End Terminal Forming Machine
-
Highway U/C Post Roll Forming Machine
-
2 Waves Highway Guardrail Roll Forming Machine
-
3 Waves Highway Guardrail Roll Forming Machine
-
दो लहरें राजमार्ग रेलिंग मशीन
-
तीन लहरें राजमार्ग रेलिंग मशीन
-
स्टील का तार लंबाई लाइन मशीन में कटौती
-
स्टील का तार लंबाई लाइन मशीन में कटौती
-
स्टील का तार लंबाई लाइन मशीन में कटौती
Installation Guidelines
Activity | Procedure |
---|---|
Positioning | Level concrete base |
Layout | Rear access considered |
Connections | Power drops, conduits |
Initial run | Confirm clearances, flows |
Programming | Template recipes for profiles |
Commissioning | Validate with test materials first |
Utilize factory technician support during initial configuration to streamline debugging and maximize runtime productivity faster.
Operation and Maintenance Factors
Schedule | Tasks |
---|---|
Daily | Verify roller lubrication |
Weekly | Inspect/tension drive chains |
Monthly | Check hydraulic leaks |
Quarterly | Inspect control wiring |
Yearly | Bearing replacement |
Keep records of length inspection data, downtime causes and electrical faults to prioritize improvements increasing overall equipment effectiveness.
Considerations When Purchasing Ridge Cap Roll Forming Machines
Factor | Evaluation Criteria |
---|---|
Production rate | Linear feet per hour rate |
Material types | Steel, aluminum etc |
Profile range | Variants required |
Accuracy | Twist, bow, length variation |
Automation level | Degree of manual operation |
Runtime guarantees | Mean time between failures |
Delivery terms | Install schedules |
प्रशिक्षण | Operator familiarization scope |
Request machine tolerance capabilities report from vendors during selection process.
Comparative Analysis of Major Ridge Cap Roll Former Manufacturers
कंपनी | Accuracy | Lead Time | Cost |
---|---|---|---|
Metform | Very good | 10 weeks | Medium |
EWMenn | Good | 12 weeks | Lower |
Rollmac | Excellent | 14 weeks | Higher |
Gasparini SpA | Very good | 16 weeks | Higher |
botou Xianfa | Good | 8 weeks | Lower |
Advantages and Limitations
Pros | Cons |
---|---|
Rapid mass production | High initial tooling cost |
Lower operating costs | Skilled technician requirment |
Consistent end quality | Heavier gauge capability limited |
Range of integration | Large production footprint |
Cost efficiency at utilization | Significant foundations needed |
Calculate total cost savings from accelerated roofing project timelines against higher equipment investment when planning capacity.
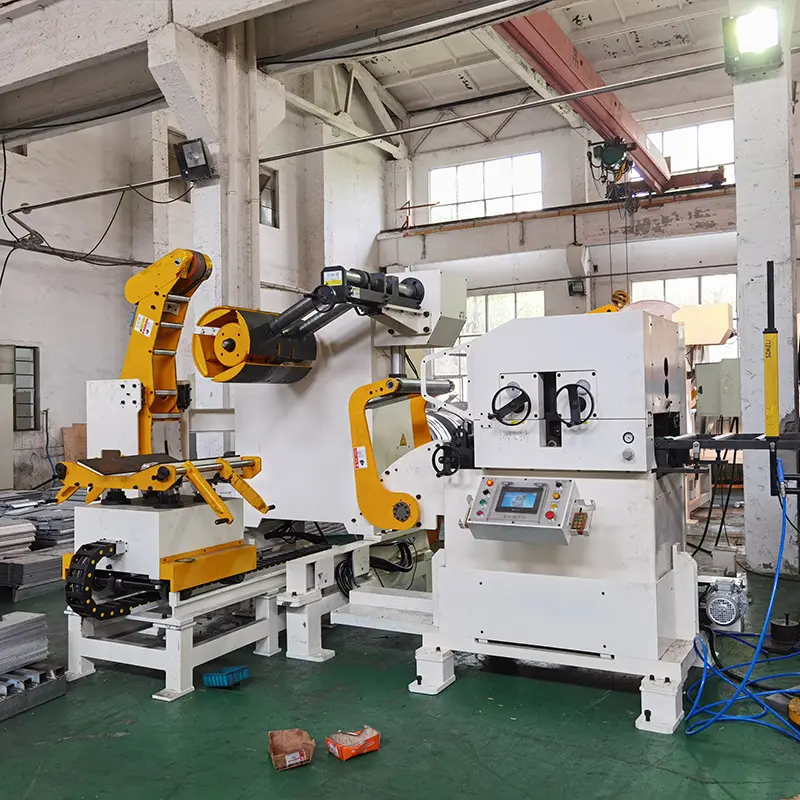
सामान्य प्रश्न
What thickness range can these machines handle?
Most standard lines efficiently process 0.4 mm to 0.7 mm metallic sheets for ridge caps. Thicker specialty materials require heavier presses and custom roller sets.
What determines maximum line speed?
Motor drive power ratings, press tonnage capabilities, decoiler payload and rates of downstream handling systems govern production tempo. Vendor proposal should provide speed calculations.
How quick are changeovers between profiles?
1-2 days is typical for experienced technicians to switch dedicated ridge profile roller sets handling similar substrate widths. Modular designs speed changeovers.
What degree of length precision held?
Precision servo powered cutoffs with rigid framing achieve under 2 mm length tolerance capability for quality lines even at peak speeds.
How to select suitable lubricants?
Consult lubricant vendor to match fluids, oils and greases to operating pressures, velocities, material specs, temperatures and ambient conditions to maximize machine lifespan while preventing contamination.
निष्कर्ष
In summary, specialized ridge cap roll formers deliver productive roofing accessory manufacturing combining operational cost efficiencies vital for regional building products supply security. Careful evaluation of purchase costs against revenue projections from resultant sales funnel ROI potentials assists strategic capacity investments.