Metal roll forming machines have revolutionized the manufacturing industry by enabling precise and efficient shaping of metal sheets into complex profiles. From construction to automotive applications, these machines play a pivotal role in creating a wide array of products with consistent quality and design. In this article, we delve into the intricate world of metal roll forming machines, exploring their workings, benefits, applications, and more.
Introduction to Metal Roll Forming Machines
Imagine a process that transforms flat metal sheets into intricate shapes with remarkable precision. This is the essence of metal roll forming, a technique that employs specialized machines to gradually bend and shape metal while it passes through a series of carefully designed rollers. This process is highly regarded for its ability to create uniform cross-sections over extended lengths, making it ideal for industries that demand both aesthetics and functionality.
How Metal Roll Forming Machines Work
At the heart of every metal roll forming machine lies a series of roll stations, each equipped with rollers designed to progressively shape the metal. As the metal sheet enters the machine, it undergoes a sequence of bending operations, with each station contributing to the final profile. The precision of this process is a result of meticulous engineering, ensuring that the material is gradually formed without compromising its integrity.
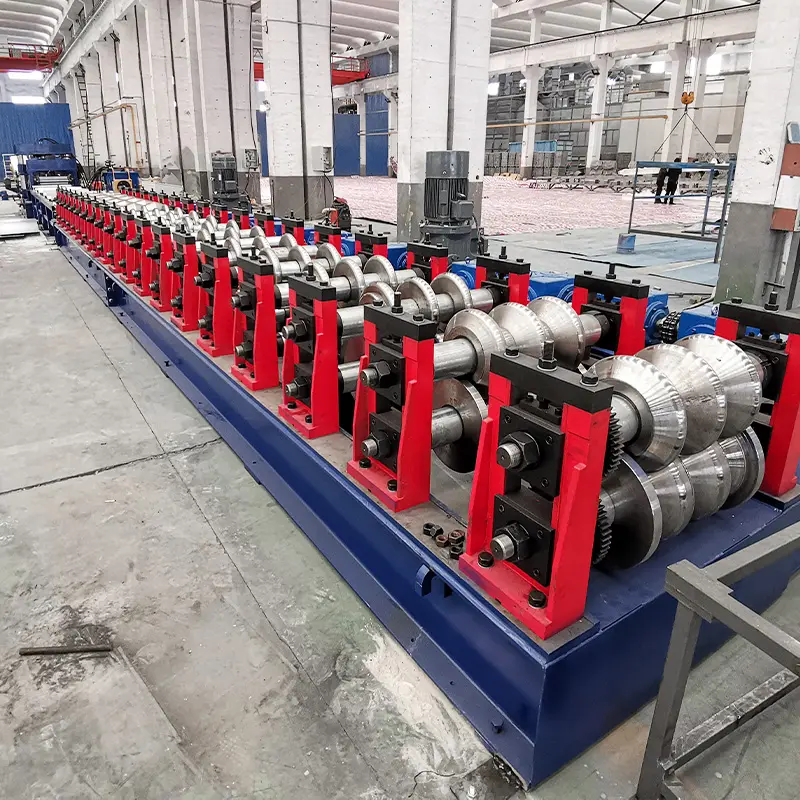
Advantages of Using Metal Roll Forming Machines
Precision and Consistency
Metal roll forming machines excel in producing uniform shapes with tight tolerances. The controlled nature of the process ensures that each piece is consistent, reducing the need for extensive post-production adjustments.
Material Savings
Traditional manufacturing techniques often lead to material wastage due to the need for extensive cutting and machining. Metal roll forming minimizes such wastage by shaping the metal directly into the required form, reducing scrap and optimizing material usage.
Versatility in Design
From simple angles to complex geometries, metal roll forming machines offer remarkable versatility in design. This flexibility allows manufacturers to create customized profiles that meet specific project requirements.
Common Applications of Metal Roll Forming
Automotive Industry
In the automotive sector, where safety and aesthetics are paramount, metal roll forming machines contribute to creating structural components with intricate designs. From chassis elements to bumper reinforcements, these machines help in crafting parts that balance form and function.
Construction Sector
Metal roll forming machines are extensively used in construction for manufacturing roofing panels, wall claddings, and structural components. The ability to produce long panels with consistent profiles streamlines the construction process and enhances the building’s durability.
HVAC Systems
Heating, ventilation, and air conditioning systems rely on precision components for efficient operation. Metal roll forming machines play a vital role in shaping ducts and other components that ensure optimal airflow within HVAC systems.
Types of Metal Roll Forming Machines
Single Stand Roll Formers
Single stand roll formers consist of a single set of rollers that progressively shape the metal. They are suitable for simpler profiles and are often used in applications where versatility is not the primary concern.
Double Stand Roll Formers
Double stand roll formers feature two sets of rollers placed one after the other. This design allows for more complex shaping and is often preferred for profiles that require intricate details.
Continuous Roll Forming
Continuous roll forming involves an ongoing process where the metal is fed continuously into the machine, allowing for uninterrupted production of long profiles. This method is highly efficient for high-volume manufacturing.
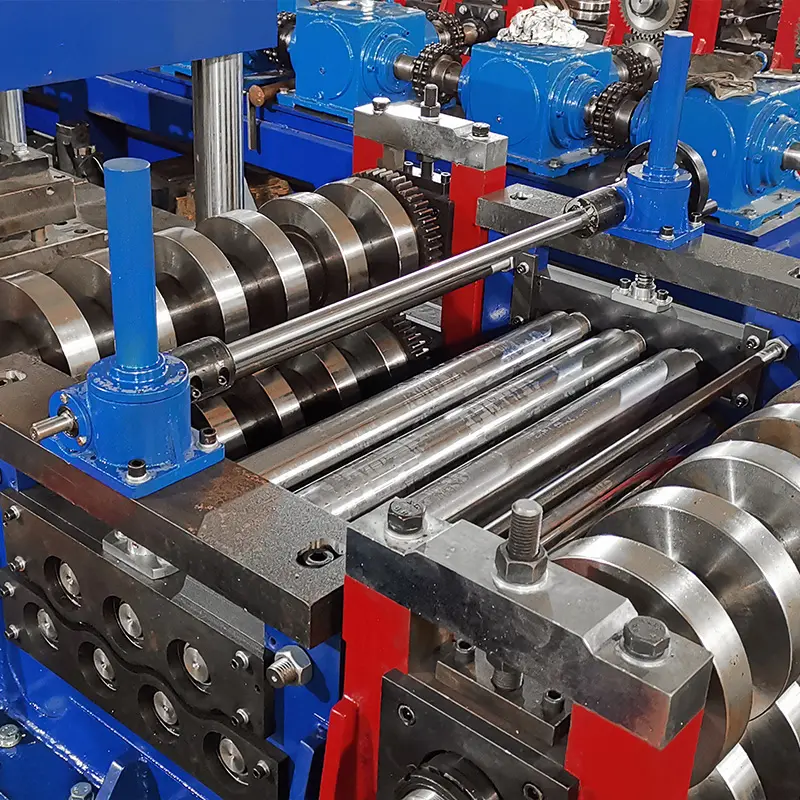
Key Components of a Metal Roll Forming Machine
Entry Section
The entry section serves as the starting point, where the raw metal sheet is fed into the machine. This section often includes straightening mechanisms to ensure the material enters the rollers uniformly.
Roll Stations
The heart of the machine, roll stations consist of a series of rollers that progressively shape the metal. Each station is responsible for specific bends or curves in the final profile.
Cutting Mechanism
After the metal has been formed, a cutting mechanism is employed to separate the shaped piece from the rest of the sheet. Various cutting methods, such as shear cutting or flying cutoff, can be used.
Exit Section
The exit section marks the end of the process, where the newly formed profile is ejected from the machine. This section may also include stacking or packaging mechanisms for efficient handling.
Factors to Consider When Choosing a Metal Roll Forming Machine
Material Compatibility
Different metals require different levels of force and precision during the forming process. Manufacturers must choose machines that are compatible with the specific type of metal they intend to work with.
Production Speed and Volume
The production speed of the machine should align with the required output volume. High-volume production might necessitate continuous roll forming machines, while lower volumes could be managed by single or double stand formers.
Customization Options
Not all projects require standardized profiles. Machines that offer customization options in terms of roll design and settings provide manufacturers with the flexibility to cater to diverse project needs.
Maintenance and Care of Metal Roll Forming Machines
To ensure the longevity and consistent performance of metal roll forming machines, regular maintenance is crucial. This includes routine inspections, lubrication of moving parts, and addressing any signs of wear or misalignment promptly.
Future Trends in Metal Roll Forming Technology
The evolution of technology continues to influence metal roll forming. Automation, advanced control systems, and predictive maintenance are some of the trends that are shaping the future of these machines, making them even more efficient and user-friendly.
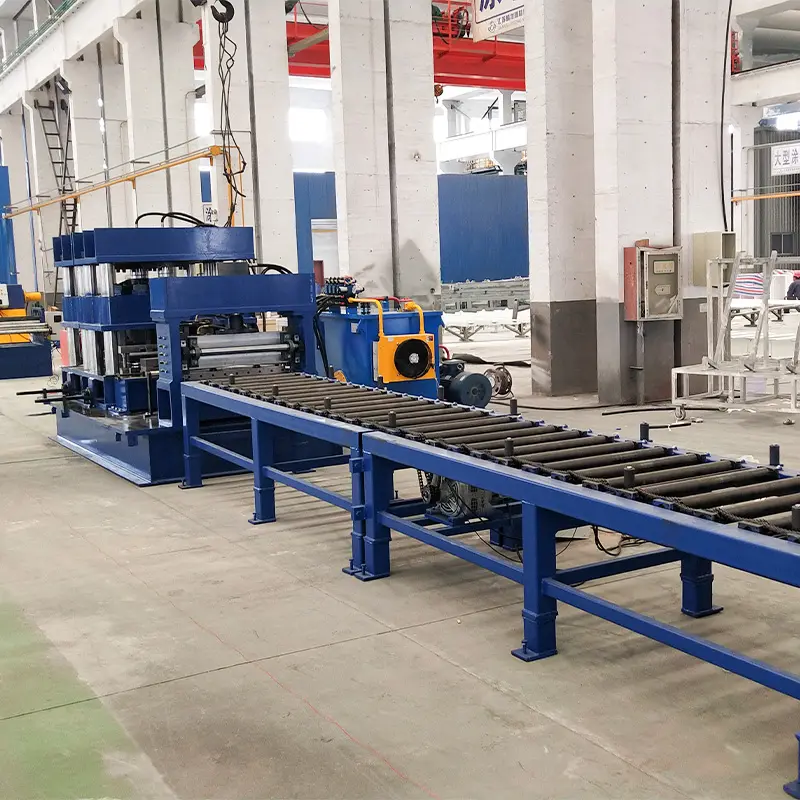
निष्कर्ष
Metal roll forming machines have undoubtedly transformed the manufacturing landscape. Their ability to shape metal with precision, reduce material wastage, and accommodate diverse design needs makes them indispensable in various industries. As technology progresses, these machines will likely continue to play a vital role in shaping the products that define our modern world.
FAQs
- What materials can be used with metal roll forming machines? Metal roll forming machines can work with a wide range of materials, including steel, aluminum, copper, and more.
- Can metal roll forming machines create complex shapes? Yes, metal roll forming machines can create complex and intricate shapes by carefully designing the sequence of roll stations.
- Are these machines suitable for small-scale production? Yes, there are options available, such as single stand roll formers, that are suitable for smaller production volumes.
- How often should maintenance be performed on these machines? Regular maintenance should be performed according to the manufacturer’s guidelines and the machine’s usage intensity.
- What role does automation play in metal roll forming technology? Automation enhances efficiency by reducing manual interventions, enabling faster production and consistent quality.