Metal panel sheets have gained significant popularity in the construction and manufacturing industries, providing durability, versatility, and aesthetic appeal. From roofing systems to wall cladding, these sheets offer a practical solution for various applications. If you’re looking to understand more about metal panel sheets—what they are, the types available, their benefits, and how they work—you’re in the right place. This guide breaks down everything you need to know, in an easy-to-follow yet detailed format.
Whether you’re a contractor, architect, or someone exploring metal panel sheets for a DIY project, this article will dive deep into the specifics, showcasing various models, materials, working processes, and maintenance tips. We’ll also compare the advantages and limitations of different products, helping you make informed decisions.
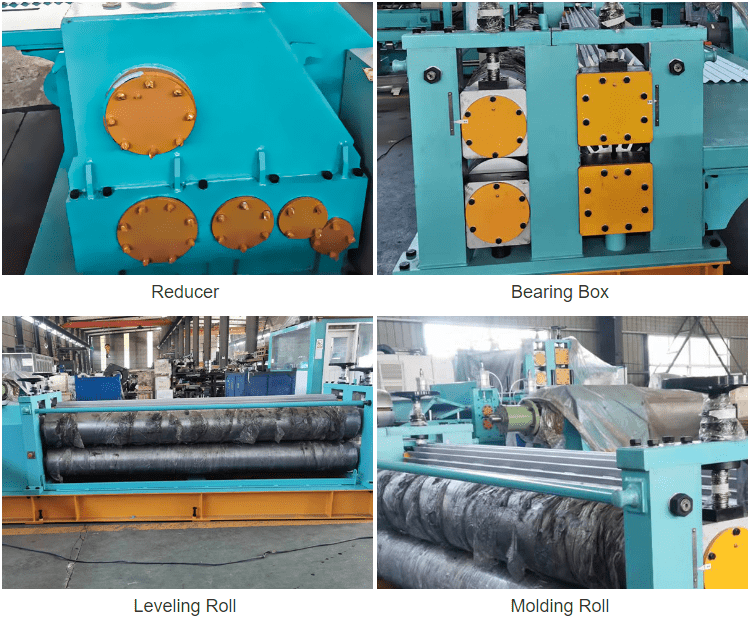
Overview of Metal Panel Sheets
Metal panel sheets are thin, flat pieces of metal designed for various construction applications. They are primarily used for roofing, siding, and wall cladding. Available in several metals like steel, aluminum, zinc, and copper, these sheets provide high strength, flexibility, and corrosion resistance. Metal panel sheets can be corrugated, smooth, or textured, and come in different finishes and coatings that enhance their longevity and aesthetic value.
Key Characteristics of Metal Panel Sheets:
- Durability: Withstanding harsh weather conditions like rain, snow, and strong winds.
- Versatility: Ideal for commercial, industrial, and residential projects.
- Sustainability: Often made from recyclable materials, reducing environmental impact.
- Aesthetics: Available in various styles and colors, enhancing building designs.
Types of Metal Panel Sheets
There are numerous types of metal panel sheets, each with its unique properties, and they are chosen based on their use case, material, and design. Below are ten prominent types with detailed descriptions:
Metal Panel Model | Description |
---|---|
Corrugated Steel Panels | Widely used for roofing and siding, these panels are known for their wavy structure, which adds strength and rigidity. Steel’s durability and low maintenance make it a preferred choice in industrial settings. |
Standing Seam Panels | Featuring raised seams that interlock, these panels offer superior water-tightness. They are ideal for sloped roofs and modern architectural designs. |
Ribbed Metal Panels | These sheets have broad, flat surfaces with raised ribs at intervals. They are designed for large-scale buildings like warehouses and offer a sleek, industrial look. |
Aluminum Metal Sheets | Lightweight, corrosion-resistant, and easy to install, aluminum panels are perfect for marine environments and places prone to high humidity. |
Copper Panels | Known for their unique patina and timeless appeal, copper panels are expensive but offer unmatched aesthetic value and longevity. They are often used in luxury homes and historic restorations. |
Galvanized Steel Sheets | Coated with zinc to prevent rusting, these panels are a popular option for outdoor structures. They are long-lasting and affordable. |
Perforated Metal Panels | These are sheets with a pattern of holes punched through, providing both functionality and decorative appeal. Used in facades, sunscreens, and acoustic ceilings, they offer a modern look. |
Zinc Panels | Highly corrosion-resistant and self-healing, zinc panels develop a patina that protects the metal from further damage. They are often used in eco-friendly and sustainable building projects. |
Composite Metal Panels | These are multi-layered panels that combine metal and insulation material. They are used for energy-efficient walls and offer good thermal insulation. |
Weathering Steel (Corten Steel) Panels | Designed to rust on the surface to create a protective layer, these panels are favored for their unique, rustic appearance. Commonly used in outdoor art installations and architectural features. |
Types of Metal Panel Sheets at a Glance
This table summarizes the different types of metal panel sheets and their common uses.
Type of Metal Sheet | Material | Primary Application | Key Advantage |
---|---|---|---|
Corrugated Steel Panels | Steel | Roofing and siding | High strength and durability |
Standing Seam Panels | Steel/Aluminum | Roofing | Superior water-tightness |
Ribbed Metal Panels | Steel | Large-scale structures | Modern industrial look |
Aluminum Metal Sheets | Aluminum | Coastal/marine applications | Lightweight and corrosion-resistant |
Copper Panels | Copper | Luxury and historic projects | Aesthetic appeal and patina |
Galvanized Steel Sheets | Steel + Zinc | Outdoor structures | Rust prevention |
Perforated Metal Panels | Various Metals | Facades, sunscreens, acoustics | Functional and decorative |
Zinc Panels | Zinc | Sustainable buildings | Self-healing and eco-friendly |
Composite Metal Panels | Multi-layered | Energy-efficient walls | Good thermal insulation |
Weathering Steel Panels | Corten Steel | Outdoor art/architectural | Unique rusted finish |
Corrugated Iron Sheets Guide
Corrugated iron sheets are the oldest and most recognizable form of metal roofing and siding. They are designed with a wave-like pattern, which increases their strength and load-bearing capacity. Typically made of galvanized steel or iron, these sheets are favored for their weather-resistance and affordability.
-
कैरिज बोर्ड रोल बनाने की मशीन
-
Highway Guardrail End Terminal Forming Machine
-
Highway U/C Post Roll Forming Machine
-
2 Waves Highway Guardrail Roll Forming Machine
-
3 Waves Highway Guardrail Roll Forming Machine
-
ऑटो आकार बदलने योग्य सिग्मा शहतीर रोल बनाने की मशीन
-
ऑटो आकार बदलने योग्य CZ शहतीर रोल बनाने की मशीन
-
ऑटो आकार बदलने योग्य Z शहतीर रोल बनाने की मशीन
-
ऑटो आकार बदलने योग्य घन शहतीर रोल बनाने की मशीन
Advantages of Corrugated Iron Sheets
- Durability: The corrugated structure allows the sheets to withstand high pressures and loads.
- Corrosion Resistance: Galvanized coatings provide excellent protection against rust.
- Affordability: These sheets are among the most budget-friendly metal panel options.
- Ease of Installation: They are lightweight and can be installed quickly by a small team.
However, corrugated iron sheets have some drawbacks, such as noise during rain and temperature fluctuations due to poor insulation properties.
Working Process of Metal Panel Sheets
The manufacturing of metal panel sheets involves several steps, from material selection to shaping and finishing. Here’s a detailed breakdown of the process:
- Material Selection: The process begins by selecting the appropriate metal, such as steel, aluminum, or copper, depending on the required properties like strength, flexibility, and corrosion resistance.
- Sheet Forming: The metal is rolled into thin sheets using a process called “cold rolling,” which enhances the strength of the material. These sheets are then passed through a series of rollers that shape them into their final form—corrugated, ribbed, standing seam, etc.
- Coating and Finishing: After the shaping, the sheets are coated with protective layers, such as zinc (galvanization) or paints, to improve durability and resistance to the elements.
- Cutting and Customization: The sheets are cut to the desired size and can be customized based on customer needs (e.g., color, texture, or perforations).
- Quality Inspection: The final step involves checking the sheets for any defects and ensuring they meet the required quality standards.
Key Components and Their Functions in Metal Panel Sheets
This table highlights the essential components involved in the construction of metal panel sheets and their roles.
Component | Function |
---|---|
Base Metal | Provides structural integrity and durability |
Protective Coating | Protects against corrosion and environmental wear |
Seams | Ensures water-tightness in roofing applications |
Ribs and Corrugations | Add strength and rigidity to the panels |
Insulation Layer | (For composite panels) Improves energy efficiency |
Fasteners | Secure the panels to structures |
Metal Panel Sheets Machine Speed and Efficiency
The machines used to produce metal panel sheets are designed for high-speed and efficient output. Depending on the type of metal and the panel design, these machines operate at various speeds. Here’s a table summarizing typical machine speeds and their efficiencies.
Metal Panel Type | Machine Speed (meters/minute) | Efficiency |
---|---|---|
Corrugated Steel Panels | 25-50 | High, due to simple design |
Standing Seam Panels | 15-25 | Medium, due to intricate seams |
Ribbed Metal Panels | 30-40 | High, large surface area covered |
Perforated Metal Panels | 10-20 | Medium, complex perforations |
Customized Mechanical Parameters for Metal Panels
Customization of metal panels allows manufacturers to tailor the product to specific needs. Various mechanical parameters, such as thickness, strength, and coatings, can be adjusted. Below is a table summarizing typical customizable parameters.
Parameter | Description | Customization Range |
---|---|---|
मोटाई | Refers to the thickness of the sheet | 0.4 mm to 3.0 mm |
Length | Total length of the panel | 1 m to 12 m |
Width | Varies depending on design | 600 mm to 1200 mm |
Coating | Protective layer (zinc, paint, etc.) | 20-275 g/m² (for zinc) |
रंग | Custom colors for aesthetic purposes | Any RAL color |
Applications and Uses of Metal Panel Sheets
Metal panel sheets are versatile and can be used in a wide variety of applications, from residential homes to large-scale industrial buildings. Here’s a look at the most common uses:
आवेदन | Commonly Used Metal Panel Type | Key Consideration |
Residential Roofing | Corrugated or Standing Seam Panels | Durability, aesthetic appeal |
Commercial Siding | Ribbed or Perforated Panels | Modern look, energy efficiency |
Industrial Buildings | Ribbed or Composite Panels | Strength, large coverage area |
Agricultural Barns | Corrugated Panels | Affordability, weather resistance |
Architectural Facades | Copper or Zinc Panels | | Acoustic Ceilings |
Aesthetic, sustainability | Perforated Metal Panels | Sound absorption, modern design |
Solar Panel Support Systems | Standing Seam Panels | Integration with solar technology |
Installation, Operation, and Maintenance of Metal Panel Sheets
Proper installation, operation, and maintenance are essential to ensure the longevity and performance of metal panel sheets. Below are the guidelines for each phase:
Phase | Description |
---|---|
Installation | Metal panels are attached to the structure using screws or clips. The process involves careful alignment, sealing of seams, and placing insulation (if needed). Professional installation is recommended for complex designs like standing seam panels. |
Operation | Once installed, metal panels require minimal maintenance. They perform well in various climates and conditions, including rain, snow, and high winds. However, sound insulation may be needed for areas prone to heavy rain. |
Maintenance | Metal panels should be inspected periodically for damage, corrosion, and fastener security. Repainting or re-coating may be necessary for maintaining appearance and protection over time. Zinc or galvanized panels may develop patina, which acts as a protective layer. |
Suppliers and Price Range for Metal Panel Sheets
The cost of metal panel sheets varies depending on the material, size, and customization. Here is a general overview of suppliers and price ranges for different types of metal panel sheets:
Supplier | Metal Panel Type | Price Range (per square foot) |
---|---|---|
ABC Metal Roofing | Corrugated Steel Panels | $2.50 – $4.00 |
Bridger Steel | Standing Seam Panels | $4.50 – $7.00 |
McElroy Metal | Ribbed Metal Panels | $3.00 – $5.50 |
Englert | Aluminum and Copper Panels | $8.00 – $12.00 |
Metal Sales Manufacturing | Galvanized Steel Sheets | $2.00 – $3.50 |
How to Choose the Right Metal Panel Sheet Supplier
Choosing the right supplier is crucial for the success of your project. Factors to consider include:
- Reputation: Look for reviews and customer feedback.
- Product Range: Ensure they offer the specific type of panel you need.
- Customization Options: Can they tailor the product to your specifications?
- Delivery Time: Confirm how long it takes for them to deliver.
- Pricing: Compare pricing, but remember that cheaper isn’t always better.
Criteria | Why It’s Important |
---|---|
Reputation | Ensures product quality and customer satisfaction |
अनुकूलन | Allows for specific project needs |
Delivery Time | Affects project timelines |
Price | Helps balance budget with quality |
Comparing Pros and Cons of Different Metal Panels
Each type of metal panel has its own set of advantages and disadvantages. Below is a comparison of the pros and cons of popular metal panel sheets:
Metal Panel Type | Advantages | Disadvantages |
---|---|---|
Corrugated Steel Panels | Affordable, durable, easy to install | Can be noisy during rain |
Standing Seam Panels | Sleek, modern, excellent waterproofing | Expensive, requires professional installation |
Aluminum Metal Sheets | Lightweight, corrosion-resistant | Higher cost compared to steel |
Copper Panels | Aesthetic appeal, long-lasting | Expensive, prone to theft |
Perforated Metal Panels | Decorative and functional | Not suitable for load-bearing uses |
Galvanized Steel Sheets | Rust-resistant, affordable | May require re-coating over time |
Composite Metal Panels | Good insulation, energy efficient | Higher cost due to multi-layer design |
Zinc Panels | Eco-friendly, self-healing patina | Expensive upfront cost |
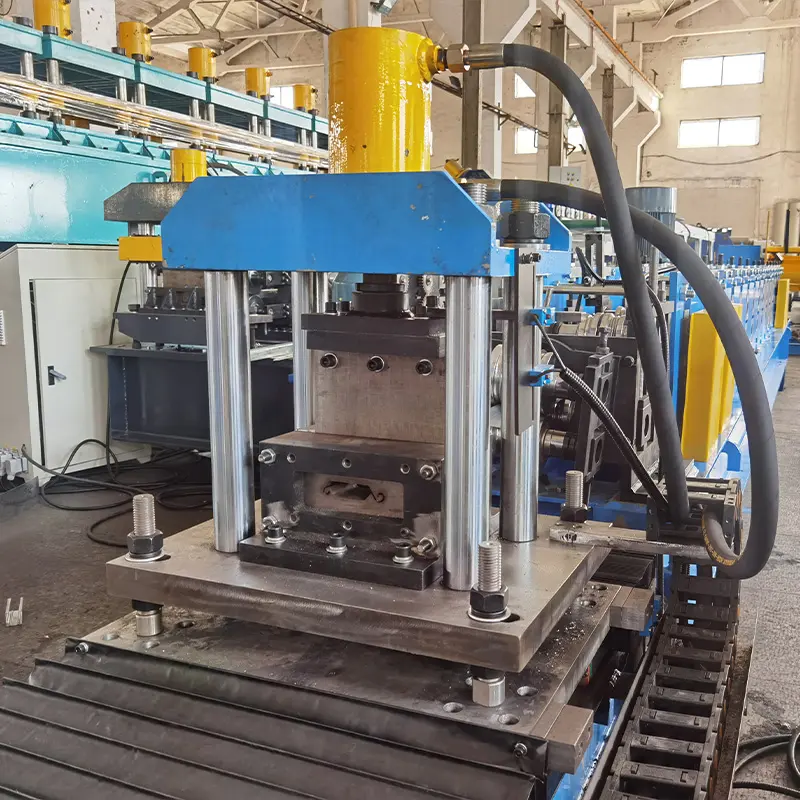
FAQs
Question | Answer |
---|---|
What are the most common uses of metal panel sheets? | Metal panel sheets are commonly used for roofing, siding, wall cladding, and facades in residential, commercial, and industrial projects. |
How long do metal panel sheets last? | Depending on the material, metal panel sheets can last anywhere from 40 to 70 years with proper maintenance. |
Are metal panel sheets eco-friendly? | Yes, many metal panel sheets are made from recyclable materials, making them an eco-friendly choice. |
Can I install metal panel sheets myself? | Simple metal panels like corrugated sheets can be DIY-friendly, but more complex systems like standing seam panels are best installed by professionals. |
How do I maintain metal panel sheets? | Maintenance involves inspecting for corrosion, cleaning dirt and debris, and re-coating if necessary. |
Do metal panels work in extreme climates? | Yes, metal panels are highly durable and perform well in extreme weather conditions, from heavy rain to snow and high winds. |
निष्कर्ष
Metal panel sheets offer a robust, versatile, and aesthetically pleasing option for various construction projects. Whether you’re selecting corrugated steel for a warehouse roof or copper panels for a luxury home, understanding the different types, applications, and pros and cons will help you make the best choice for your needs. Remember, choosing the right supplier and properly maintaining the sheets are critical to ensuring longevity and optimal performance.
By exploring the models, processes, and technical details in this guide, you’re now well-equipped to dive into your next project with confidence. Happy building!